- お役立ち記事
- Troubleshooting Hold Pressure Processes and Stabilizing Product Quality
Troubleshooting Hold Pressure Processes and Stabilizing Product Quality
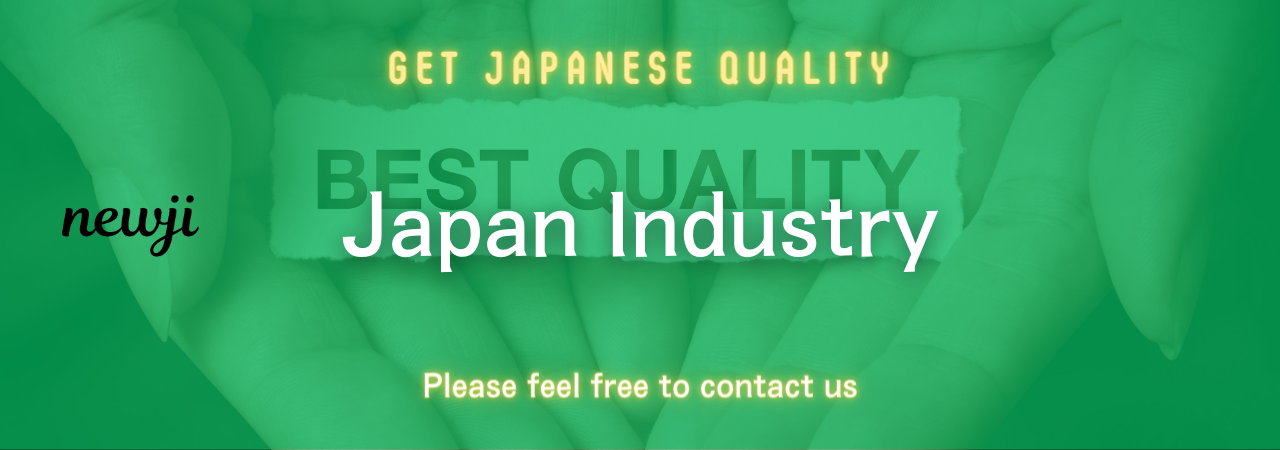
目次
Understanding the Hold Pressure Process
In the world of manufacturing, especially when dealing with injection molding, the hold pressure process plays a crucial role in ensuring product quality and consistency.
Hold pressure, also known as packing pressure, is a phase in the molding process that comes after the injection phase.
During this phase, a specific amount of pressure is applied to the molten material to pack it into the mold cavity effectively.
This helps to control the shrinkage of the material as it cools and solidifies, ensuring the final product maintains its desired dimensions and structural integrity.
Why Hold Pressure is Important
The hold pressure process is critical because it directly affects the quality of the final product.
If the hold pressure is too low, parts may end up being undersized, or they might have internal voids or sink marks.
Conversely, if the pressure is too high, it could lead to flash, where excess material seeps out from the mold cavity.
Balancing the correct hold pressure is essential for maintaining the quality, strength, and appearance of the product.
Common Problems in Hold Pressure Processes
Even with the best practices, issues in the hold pressure process can arise.
Understanding these problems can help in better troubleshooting and stabilizing the product quality.
Inconsistent Pressure
Inconsistency in applying pressure during the hold phase can result in parts with varying quality.
This might be due to fluctuations in the hydraulic system or improper setup of the molding machine.
Inadequate maintenance or calibration might also lead to irregular pressure application.
Incorrect Hold Time
The duration for which hold pressure is applied is just as crucial as the pressure itself.
Too short a hold time can lead to incomplete filling, while too long can cause residual stresses in the product.
Both scenarios adversely affect the product’s functionality and longevity.
Material Flow Issues
Sometimes, the molten material may not flow effectively into the mold cavity due to an obstruction or improper temperature settings.
This can result in short shots or incomplete filled parts.
Ensuring proper material flow is essential for consistent and high-quality output.
Steps to Troubleshoot Hold Pressure Issues
To stabilize the product quality, addressing hold pressure issues is necessary.
Here are some steps to help troubleshoot and resolve these problems.
Check Equipment Calibration
One of the first steps in troubleshooting is to ensure that your equipment is correctly calibrated.
Regular calibration of the molding machines can help prevent discrepancies in pressure application.
This involves checking sensors, gauges, and other input devices to ensure they’re working correctly.
Review Pressure and Hold Time Settings
It’s vital to verify that both pressure and hold time settings are according to the specifications needed for the particular material and mold design.
Adjusting these settings to align with optimal levels can help maintain product quality.
Make sure to record and monitor these settings regularly to detect any deviations.
Analyze and Adjust Material Temperature
The temperature of the molten material affects its flow and filling capacity.
Regular analysis of temperature settings and the material being used can help mitigate flow issues.
Adjusting temperature according to the material’s specific thermal characteristics can enhance the quality of the final product.
Perform Regular Maintenance
Preventative maintenance of injection molding machines is crucial.
Regular checks and servicing can help detect potential mechanical issues before they lead to significant problems, such as pressure inconsistency.
Ensure that all parts of the machine, including hydraulics, are in good working condition.
Stabilizing Product Quality
Once troubleshooting is complete, the next step is to stabilize and maintain the product quality over time.
Implementing the following practices can help achieve this goal.
Consistent Process Monitoring
Continually monitor the hold pressure process to ensure the parameters remain within acceptable ranges.
Utilizing advanced monitoring systems can provide real-time data and alert operators to any deviations.
Consistent monitoring helps maintain a high standard of quality.
Use Standard Operating Procedures (SOP)
Establishing and adhering to standard operating procedures can bring uniformity and consistency to the hold pressure process.
SOPs help ensure that all operators follow the same protocols, reducing variability in product quality.
Training and Development
Investing in training programs for machine operators and maintenance crews can substantially improve the hold pressure process.
A skilled workforce can identify and resolve issues more efficiently, leading to enhanced product quality and consistency.
Regular training helps keep the staff updated on the latest technologies and best practices.
Utilize Advanced Technologies
Employing cutting-edge technologies such as automation and machine learning can aid in optimizing the hold pressure process.
These technologies provide predictive insights and automation capabilities that help maintain consistent pressure and temperature, ultimately improving the final product quality.
Conclusion
Troubleshooting and stabilizing the hold pressure process is a vital aspect of ensuring high product quality in manufacturing.
By understanding the common issues, and employing strategic troubleshooting and maintenance practices, manufacturers can effectively manage and stabilize the quality of their products.
Continual monitoring, adherence to SOPs, and leveraging modern technologies play an indispensable role in maintaining consistent product quality.
With these practices in place, manufacturers can reduce defects, improve efficiency, and achieve greater customer satisfaction.
資料ダウンロード
QCD調達購買管理クラウド「newji」は、調達購買部門で必要なQCD管理全てを備えた、現場特化型兼クラウド型の今世紀最高の購買管理システムとなります。
ユーザー登録
調達購買業務の効率化だけでなく、システムを導入することで、コスト削減や製品・資材のステータス可視化のほか、属人化していた購買情報の共有化による内部不正防止や統制にも役立ちます。
NEWJI DX
製造業に特化したデジタルトランスフォーメーション(DX)の実現を目指す請負開発型のコンサルティングサービスです。AI、iPaaS、および先端の技術を駆使して、製造プロセスの効率化、業務効率化、チームワーク強化、コスト削減、品質向上を実現します。このサービスは、製造業の課題を深く理解し、それに対する最適なデジタルソリューションを提供することで、企業が持続的な成長とイノベーションを達成できるようサポートします。
オンライン講座
製造業、主に購買・調達部門にお勤めの方々に向けた情報を配信しております。
新任の方やベテランの方、管理職を対象とした幅広いコンテンツをご用意しております。
お問い合わせ
コストダウンが利益に直結する術だと理解していても、なかなか前に進めることができない状況。そんな時は、newjiのコストダウン自動化機能で大きく利益貢献しよう!
(Β版非公開)