- お役立ち記事
- Optimizing Molding Cycles and Hold Pressure to Prevent Burrs
Optimizing Molding Cycles and Hold Pressure to Prevent Burrs
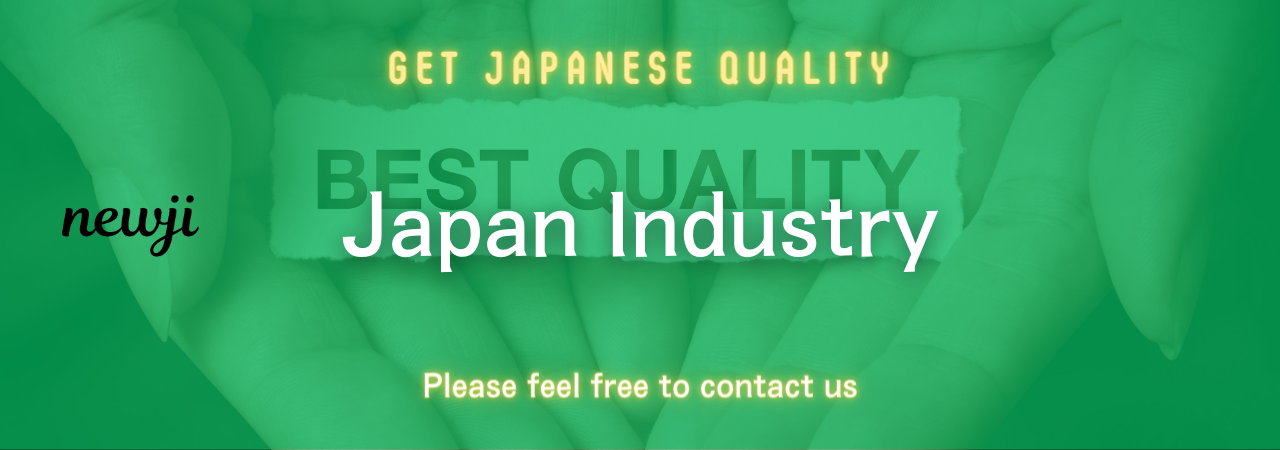
目次
Understanding Burrs in Injection Molding
Injection molding is a widely-used manufacturing process that produces parts by injecting molten material into a mold.
It’s a process highly revered for its efficiency and ability to produce complex parts to precise specifications.
However, one common defect that can occur during this process is the formation of burrs.
Burrs are thin, unwanted pieces of material that form on the edge of molded parts.
They not only detract from the aesthetic appeal of the part but can also affect its functionality and performance.
Preventing burrs is crucial in maintaining the quality of the molded parts, and optimizing molding cycles and hold pressure are two effective ways to do so.
The Role of Molding Cycles
The molding cycle in injection molding consists of several stages, including filling, packing, cooling, and ejection.
Optimizing these cycles is essential for reducing defects, like burrs, and enhancing the overall quality of the product.
Taking the time to understand and adjust each part of the cycle can lead to better outcomes.
Filling Phase
The filling phase is where the molten material is injected into the mold cavity.
The speed and pressure used during this phase can significantly impact the presence of burrs.
If the injection speed is too high, it may lead to material overflowing the mold cavity, resulting in burrs.
Therefore, adjusting the injection speed to ensure smooth and even filling can help prevent burr formation.
Packing and Holding Phase
This phase follows the initial filling and involves applying additional pressure to pack more material into the cavity.
This pressure is maintained to compensate for material shrinkage during cooling.
If the hold pressure is too high, it can cause the mold to open slightly, resulting in burrs.
Conversely, if the hold pressure is too low, parts may not fully form or may have sink marks.
Cooling Phase
During the cooling phase, the material solidifies and takes the shape of the mold cavity.
Insufficient cooling time or uneven cooling can lead to warping and burrs as the material can still flow until it’s fully hardened.
Ensuring even cooling across the mold is therefore critical to prevent any defects.
The Importance of Hold Pressure
Hold pressure plays a pivotal role in molding quality and significantly affects the occurrence of burrs.
It helps compensate for part shrinkage and supports the maintenance of part integrity.
The optimal hold pressure level ensures that the material does not escape into unwanted areas, causing burrs.
Balancing Hold Pressure
Finding the right balance for hold pressure is critical.
The optimal pressure depends on many factors, such as material properties, mold design, and product specifications.
Too much pressure can open the mold slightly, leading to burr formation or even mold damage.
On the other hand, inadequate hold pressure can result in incomplete parts.
Techniques for Optimizing Molding Cycles and Hold Pressure
Optimizing molding cycles and hold pressure involves a combination of fine-tuning machine settings and understanding material properties.
Here are some strategies to consider:
Material Selection
Different materials have different characteristics and responses to pressure and temperature.
Choosing a material that fits well with the design specifications and maintaining awareness of its behavior under specific conditions is vital.
Test different materials to see how they react to varying pressures and temperatures in your molding process.
Machine Calibration
Regularly calibrating injection molding machines ensures that they are operating correctly and at peak efficiency.
Make sure the machine parameters are set according to the material needs and production requirements.
Consider using process monitoring systems that provide real-time feedback on the injection process to ensure consistency and accuracy.
Mold Design and Maintenance
The design of the mold has a direct impact on the occurrence of burrs.
Ensure that mold fit and alignment are exact, as even a slight misalignment can lead to uneven pressure distribution.
Regular maintenance ensures that the mold remains in optimal condition, preventing leaks and issues that could cause burrs.
Conclusion
Preventing burrs in injection molding is fundamental to achieving high-quality parts.
By optimizing molding cycles and hold pressure, manufacturers can significantly reduce the occurrence of these defects.
It involves a thorough understanding of the material properties, meticulous machine settings, and regular maintenance of molds.
While the journey to the perfect injection molded part may require adjustments and frequent fine-tuning, the benefits of having a burr-free product are well worth the effort.
Not only will it enhance product aesthetics and functionality, but it will also meet the increasing demands for precision in today’s competitive market.
資料ダウンロード
QCD調達購買管理クラウド「newji」は、調達購買部門で必要なQCD管理全てを備えた、現場特化型兼クラウド型の今世紀最高の購買管理システムとなります。
ユーザー登録
調達購買業務の効率化だけでなく、システムを導入することで、コスト削減や製品・資材のステータス可視化のほか、属人化していた購買情報の共有化による内部不正防止や統制にも役立ちます。
NEWJI DX
製造業に特化したデジタルトランスフォーメーション(DX)の実現を目指す請負開発型のコンサルティングサービスです。AI、iPaaS、および先端の技術を駆使して、製造プロセスの効率化、業務効率化、チームワーク強化、コスト削減、品質向上を実現します。このサービスは、製造業の課題を深く理解し、それに対する最適なデジタルソリューションを提供することで、企業が持続的な成長とイノベーションを達成できるようサポートします。
オンライン講座
製造業、主に購買・調達部門にお勤めの方々に向けた情報を配信しております。
新任の方やベテランの方、管理職を対象とした幅広いコンテンツをご用意しております。
お問い合わせ
コストダウンが利益に直結する術だと理解していても、なかなか前に進めることができない状況。そんな時は、newjiのコストダウン自動化機能で大きく利益貢献しよう!
(Β版非公開)