- お役立ち記事
- For SMEs: Tips for Improving Product Quality Through Clamping Force Management
For SMEs: Tips for Improving Product Quality Through Clamping Force Management
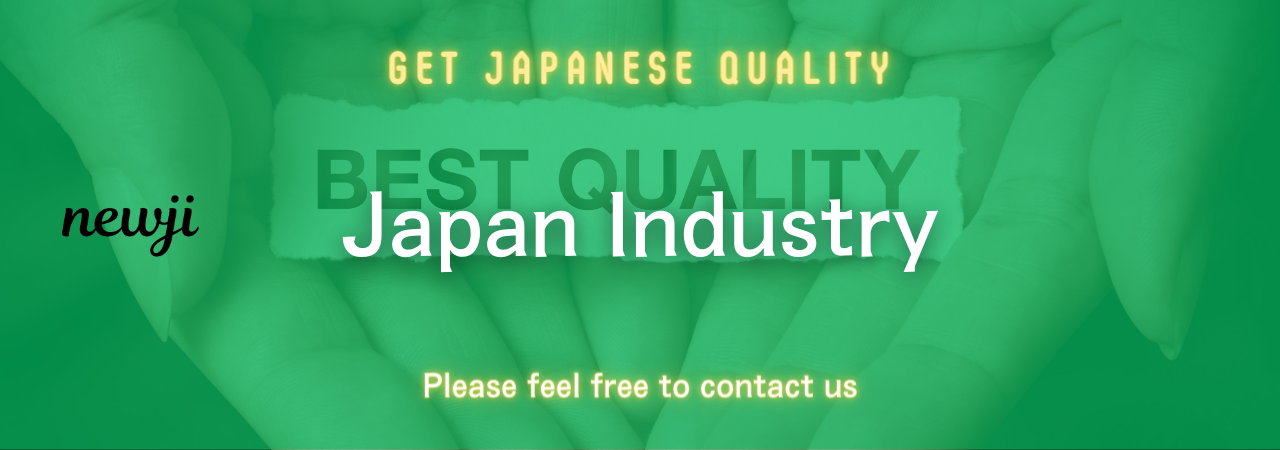
目次
Understanding Clamping Force Management
Clamping force management is an essential process in manufacturing, especially for small and medium-sized enterprises (SMEs) aiming to improve product quality.
At its core, clamping force refers to the pressure applied to secure parts or components during production.
This pressure ensures that parts remain in place without shifting during machining or assembly.
Effective clamping force management helps prevent defects, enhances precision, and contributes to the overall quality of the finished product.
The Importance of Clamping Force
For SMEs, maintaining the right clamping force is crucial for several reasons.
Firstly, too much clamping pressure can deform materials, leading to dimensional inaccuracies or surface defects.
Conversely, insufficient pressure may cause parts to move or vibrate, resulting in misalignment and potential product failure.
Proper clamping force management provides a balance, securing the workpiece effectively while preserving its structural integrity.
Additionally, by reducing errors caused by incorrect clamping, SMEs can significantly minimize waste and rework, leading to enhanced profitability.
How to Determine the Right Clamping Force
Determining the appropriate clamping force requires careful consideration of several factors.
These factors include the type of material being clamped, its thickness, and the tooling or machinery in use.
For SMEs, it’s often effective to start by consulting the manufacturer’s guidelines and specifications for clamping equipment.
These guidelines usually provide a recommended clamping force range.
Additionally, engineers and technicians should consider conducting tests or simulations.
These evaluations help to identify the optimal clamping pressure needed to avert deformation and ensure alignment.
Using Technological Tools
Many SMEs are now incorporating technological tools to enhance clamping force management.
Software and sensors specifically designed to monitor clamping force can provide real-time data and alerts.
These tools enable manufacturers to maintain the correct pressure throughout the production process.
With automated systems, it becomes easier to adjust clamping force dynamically in response to changes during production.
This adaptability limits human error and further ensures the quality of the final product.
Training and Skill Development
For SMEs to fully leverage clamping force management, employee training is paramount.
Training programs should focus on educating workers about the importance of correct clamping techniques and the impact of clamping force on product quality.
Skill development ensures that employees can effectively use the tools and technology available for monitoring and adjusting clamping pressure.
Furthermore, trained employees are more capable of identifying potential issues early on and executing preventative measures.
An investment in training usually translates to enhanced efficiency and reduced error rates across production lines.
Implementing Standard Operating Procedures (SOPs)
Another critical aspect of improving product quality through clamping force management is the development and implementation of Standard Operating Procedures (SOPs).
SOPs provide detailed, step-by-step instructions on how to set and monitor clamping forces for different products and materials.
For SMEs, SOPs ensure consistency and reliability in production processes.
By establishing procedures, companies can reduce variability and ensure every team member follows best practices.
Regular Maintenance and Calibration
Regular maintenance and calibration of clamping equipment are essential in maintaining optimal performance.
For SMEs, ensuring that equipment is in excellent working condition prevents inconsistencies in clamping force application.
Machines and tools that are well-maintained and regularly calibrated are less likely to experience breakdowns or deliver inadequate pressure.
This reliability translates to higher product quality and less production downtime.
Frequent checks and services also extend the lifespan of equipment, enabling SMEs to get the best return on their investment.
Documentation and Analysis
Documentation plays a significant role in the effective management of clamping force.
For SMEs, maintaining records of clamping settings, adjustments, and outcomes allows for detailed analysis.
This analysis helps in tracing any quality issues back to their source and facilitates continual improvement.
By tracking this data over time, SMEs can identify trends and areas for improvement, optimizing production processes further.
Such documentation is also beneficial for meeting regulatory and quality standards, demonstrating a commitment to maintaining product excellence.
Conclusion
For SMEs striving to improve product quality, effective clamping force management is a strategic tool.
By understanding the principles of clamping force and implementing methods to manage it, these enterprises can significantly reduce defects and enhance precision.
Incorporating technology, fostering employee expertise, and committing to regular maintenance are keys to success.
With these strategies in place, SMEs can ensure high-quality production, gaining a competitive edge in their market.
資料ダウンロード
QCD調達購買管理クラウド「newji」は、調達購買部門で必要なQCD管理全てを備えた、現場特化型兼クラウド型の今世紀最高の購買管理システムとなります。
ユーザー登録
調達購買業務の効率化だけでなく、システムを導入することで、コスト削減や製品・資材のステータス可視化のほか、属人化していた購買情報の共有化による内部不正防止や統制にも役立ちます。
NEWJI DX
製造業に特化したデジタルトランスフォーメーション(DX)の実現を目指す請負開発型のコンサルティングサービスです。AI、iPaaS、および先端の技術を駆使して、製造プロセスの効率化、業務効率化、チームワーク強化、コスト削減、品質向上を実現します。このサービスは、製造業の課題を深く理解し、それに対する最適なデジタルソリューションを提供することで、企業が持続的な成長とイノベーションを達成できるようサポートします。
オンライン講座
製造業、主に購買・調達部門にお勤めの方々に向けた情報を配信しております。
新任の方やベテランの方、管理職を対象とした幅広いコンテンツをご用意しております。
お問い合わせ
コストダウンが利益に直結する術だと理解していても、なかなか前に進めることができない状況。そんな時は、newjiのコストダウン自動化機能で大きく利益貢献しよう!
(Β版非公開)