- お役立ち記事
- Case Studies of High-Precision Product Manufacturing Using Micro Injection Molding
Case Studies of High-Precision Product Manufacturing Using Micro Injection Molding
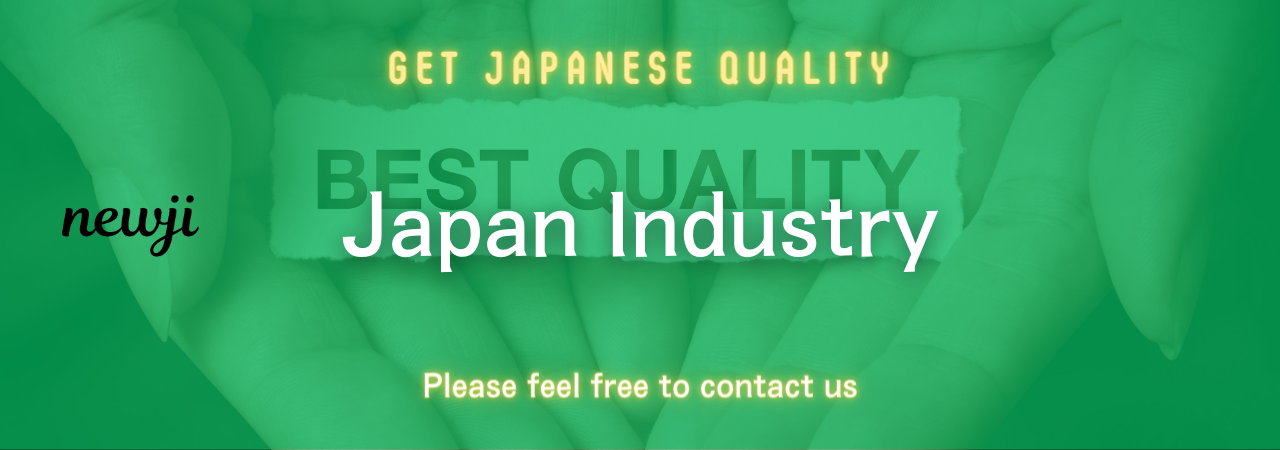
目次
Introduction to Micro Injection Molding
Micro injection molding is a sophisticated manufacturing technique that enables the production of high-precision, miniature plastic components.
This process is widely utilized in industries such as medical devices, electronics, automotive, and telecommunications, where intricate designs and exacting tolerances are paramount.
Micro injection molding involves injecting molten plastic into a precision-machined mold cavity at high pressure.
The material then cools and solidifies to form a precise replica of the mold surface.
This method is ideal for producing small parts with complex geometries, ensuring consistent quality and dimensional accuracy.
The Importance of High-Precision Manufacturing
High-precision manufacturing is crucial in today’s industrial landscape due to the increasing demand for miniaturized and highly detailed components.
With advancements in technology, products are becoming smaller while retaining, or even increasing, functionality.
This trend underscores the need for manufacturing processes that can achieve high levels of precision and repeatability.
Micro injection molding addresses this demand by offering superior dimensional control, excellent surface finishes, and the ability to replicate intricate details on a miniature scale, which are critical in sectors such as medical and electronics.
Micro Injection Molding Process Overview
The micro injection molding process begins with the selection of suitable thermoplastic materials, which are chosen based on factors such as mechanical properties, chemical resistance, and intended application.
Common materials include PEEK, LCP, and nylon, known for their durability and stability.
Next, the mold design plays a pivotal role in ensuring the success of the molding process.
The molds are manufactured with precision machining techniques, often using steel or aluminum alloys to withstand the pressure and wear during molding.
The cavities must be designed to account for the shrinkage and flow characteristics of the plastic material.
Once the mold is prepared, the molten plastic is injected into the mold cavity at high speed and pressure.
This step requires precise control to fill the cavity completely without air entrapment or material degradation.
The mold is then cooled rapidly, facilitating the solidification of the plastic and allowing for ejection from the mold.
Case Study 1: Micro Injection Molding in Medical Device Manufacturing
The medical device industry has greatly benefited from micro injection molding, particularly in the production of diagnostic and therapeutic devices.
One case study involves the manufacturing of microfluidic chips used for disease detection and monitoring.
These chips require intricate channels and features to manipulate fluids at the microscale.
Using micro injection molding, manufacturers can achieve the high precision necessary for proper fluid flow and interaction within the chip.
The consistency provided by this technique ensures that each batch of chips meets stringent regulatory standards, a critical factor in the healthcare sector.
Furthermore, micro injection molding allows for the use of biocompatible materials, essential for medical applications.
The adaptability of this process to produce complex parts rapidly and cost-effectively makes it invaluable in the med-tech industry.
Case Study 2: Micro Injection Molding in Consumer Electronics
In the consumer electronics industry, the demand for compact and lightweight devices necessitates components with exceptionally precise dimensions and performance.
A notable example is the production of connectors and gears within modern smartphones.
Micro injection molding facilitates the creation of these critical components, ensuring they fit perfectly within the limited space available in such devices.
Manufacturers can produce parts with fine details and tight tolerances, enabling the seamless integration of various electronic components.
The repeatability of the micro injection molding process also ensures that these parts function reliably over extended use, which is essential for maintaining consumer trust and satisfaction.
This consistency, combined with cost efficiency, supports the high-volume production typical in the electronics market.
Key Advantages of Micro Injection Molding
Micro injection molding offers several advantages that make it a preferred choice in high-precision manufacturing.
Firstly, it allows for the production of complex geometries that would be difficult or impossible with other techniques.
The fine detail achievable with this method can meet the most challenging design specifications.
Secondly, micro injection molding supports high-volume production with excellent repeatability, ensuring uniformity across thousands or even millions of parts.
This capability is crucial in industries where consistent quality is non-negotiable.
Additionally, the process is highly efficient, with short cycle times that reduce production costs while maintaining high output levels.
The ability to use a wide range of materials, including advanced engineering plastics, expands the potential applications of micro injection molding.
Future Trends in Micro Injection Molding
As technology continues to evolve, micro injection molding is poised to become even more significant in advanced manufacturing.
The integration of smart manufacturing technologies, such as real-time monitoring and data analytics, will enhance process control and further improve product quality.
Moreover, advancements in material science will introduce novel plastics with enhanced properties, opening new opportunities for innovation.
There is also a growing focus on sustainability, encouraging the development of recyclable materials and energy-efficient processes.
In conclusion, micro injection molding stands at the forefront of high-precision product manufacturing.
Its ability to produce complex, miniature components with extraordinary precision and efficiency makes it indispensable across various industries.
As new challenges and opportunities arise, micro injection molding will continue to adapt and excel, shaping the future of manufacturing.
資料ダウンロード
QCD調達購買管理クラウド「newji」は、調達購買部門で必要なQCD管理全てを備えた、現場特化型兼クラウド型の今世紀最高の購買管理システムとなります。
ユーザー登録
調達購買業務の効率化だけでなく、システムを導入することで、コスト削減や製品・資材のステータス可視化のほか、属人化していた購買情報の共有化による内部不正防止や統制にも役立ちます。
NEWJI DX
製造業に特化したデジタルトランスフォーメーション(DX)の実現を目指す請負開発型のコンサルティングサービスです。AI、iPaaS、および先端の技術を駆使して、製造プロセスの効率化、業務効率化、チームワーク強化、コスト削減、品質向上を実現します。このサービスは、製造業の課題を深く理解し、それに対する最適なデジタルソリューションを提供することで、企業が持続的な成長とイノベーションを達成できるようサポートします。
オンライン講座
製造業、主に購買・調達部門にお勤めの方々に向けた情報を配信しております。
新任の方やベテランの方、管理職を対象とした幅広いコンテンツをご用意しております。
お問い合わせ
コストダウンが利益に直結する術だと理解していても、なかなか前に進めることができない状況。そんな時は、newjiのコストダウン自動化機能で大きく利益貢献しよう!
(Β版非公開)