- お役立ち記事
- Achieving Cost Reduction and Productivity Improvement by Optimizing Clamping Force
Achieving Cost Reduction and Productivity Improvement by Optimizing Clamping Force
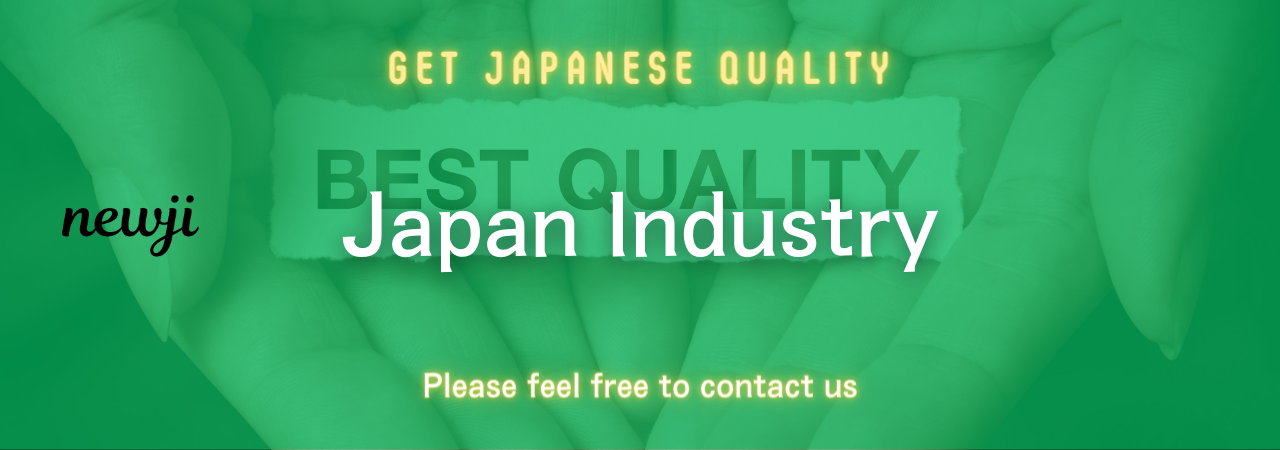
目次
Understanding Clamping Force in Manufacturing
In the world of manufacturing, clamping force plays a pivotal role in ensuring the efficient operation of machinery and the quality of the products produced.
Essentially, clamping force is the pressure applied by a clamp in holding an object in place during a manufacturing process.
This might seem simple, but the optimization of clamping force is crucial, as it impacts everything from the cost of production to the durability of the final product.
When manufacturing products, it is necessary to hold parts securely to prevent movement during operations such as machining, welding, or bonding.
The amount of force applied needs to be precise; too little force can result in poor alignment and defects, while too much force can damage materials and equipment.
Therefore, understanding and controlling clamping force is essential for any manufacturing setup.
Why Optimize Clamping Force?
The optimization of clamping force is not just a matter of maintaining product quality—it’s also about enhancing productivity and reducing operational costs.
One of the most significant benefits of optimizing clamping force is the potential for significant cost reductions.
By using the exact amount of force required, manufacturers can minimize material waste and reduce wear and tear on machinery, which in turn can lower repair and replacement costs.
Furthermore, optimizing clamping force can lead to productivity improvements.
When the clamping force is dialed in just right, the manufacturing process can operate at higher speeds with fewer interruptions.
Machines are less likely to jam or break down, which means less downtime and increased efficiency.
Finally, optimizing clamping force enhances product quality.
With the correct application of force, parts are held securely, reducing the likelihood of errors or defects that might necessitate costly rework or lead to customer dissatisfaction.
Methods to Measure and Optimize Clamping Force
There are several methods manufacturers use to measure and optimize clamping force.
One common method is the use of strain gauges, which measure the amount of deformation in a material when a force is applied.
These gauges provide real-time data, allowing for precise adjustments.
Another method is using load cells, sensors that convert the force into an electrical signal.
Load cells offer high accuracy and can be integrated into the machinery control systems for automatic adjustments.
Advancements in technology have also introduced the use of digital torque wrenches and other sophisticated tools that help in setting the desired clamping force accurately and consistently.
Step 1: Assessment
The first step in optimizing clamping force is to assess the current setup.
This involves measuring the existing force applied and analyzing any potential issues such as over-clamping or insufficient force.
Identifying these issues helps in setting the baseline for improvements.
Step 2: Calculation
Next is the calculation of the ideal clamping force.
This calculation must consider various factors, including the material properties, the nature of the operation, and the manufacturer’s specifications.
Performing these calculations ensures that the correct force is used for each application.
Step 3: Implementation
Once the ideal clamping force is determined, the next step is to implement changes.
This may involve recalibrating equipment or upgrading components to achieve precise force application.
Continuous monitoring ensures that the clamping force remains optimal over time.
The Importance of Regular Maintenance
Regular maintenance of the clamping system is necessary to ensure ongoing optimization.
Over time, factors such as equipment fatigue and material changes can alter the effectiveness of the clamping force.
Routine checks and calibrations help identify and address these issues before they impact production.
Additionally, training operators to understand the importance of clamping force and how to adjust it effectively can be beneficial.
Well-informed staff are better equipped to maintain optimal settings, further improving productivity and reducing costs.
Conclusion
Optimizing clamping force is a critical component of modern manufacturing that significantly impacts cost reduction and productivity enhancement.
By measuring, calculating, and continuously monitoring clamping force, manufacturers can improve the efficiency of their operations and the quality of their products.
A strategic approach to clamping force not only helps in minimizing expenses but also contributes to a smoother production process.
As technology advances, the ability to optimize clamping force with greater precision will only become more accessible, offering more avenues for efficiency and savings in manufacturing.
資料ダウンロード
QCD調達購買管理クラウド「newji」は、調達購買部門で必要なQCD管理全てを備えた、現場特化型兼クラウド型の今世紀最高の購買管理システムとなります。
ユーザー登録
調達購買業務の効率化だけでなく、システムを導入することで、コスト削減や製品・資材のステータス可視化のほか、属人化していた購買情報の共有化による内部不正防止や統制にも役立ちます。
NEWJI DX
製造業に特化したデジタルトランスフォーメーション(DX)の実現を目指す請負開発型のコンサルティングサービスです。AI、iPaaS、および先端の技術を駆使して、製造プロセスの効率化、業務効率化、チームワーク強化、コスト削減、品質向上を実現します。このサービスは、製造業の課題を深く理解し、それに対する最適なデジタルソリューションを提供することで、企業が持続的な成長とイノベーションを達成できるようサポートします。
オンライン講座
製造業、主に購買・調達部門にお勤めの方々に向けた情報を配信しております。
新任の方やベテランの方、管理職を対象とした幅広いコンテンツをご用意しております。
お問い合わせ
コストダウンが利益に直結する術だと理解していても、なかなか前に進めることができない状況。そんな時は、newjiのコストダウン自動化機能で大きく利益貢献しよう!
(Β版非公開)