- お役立ち記事
- Tips for Adjusting Filling Time to Prevent Molding Defects
Tips for Adjusting Filling Time to Prevent Molding Defects
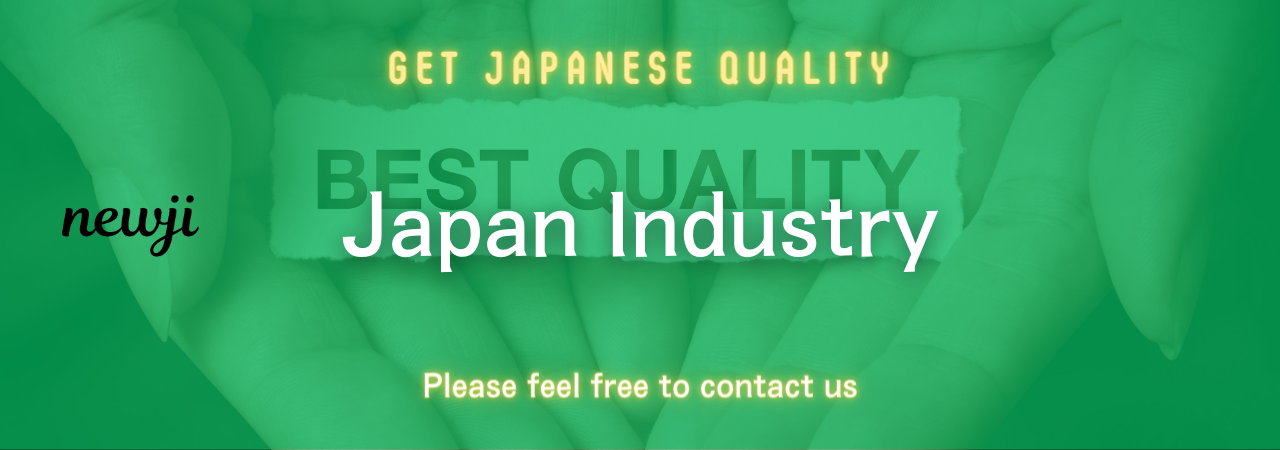
目次
Understanding Molding Defects
Before diving into tips for adjusting filling time, it’s important to understand what molding defects are and why they occur.
Molding defects refer to imperfections that arise during the injection molding process, resulting in flawed or unusable products.
These defects can manifest in various forms, such as warping, short shots, burn marks, and sink marks.
Understanding these defects can help us comprehend the significance of filling time in the molding process.
The Role of Filling Time
Filling time is a crucial factor in the injection molding process.
It refers to the duration taken to fill the mold cavity with molten material completely.
Achieving the correct filling time is essential to producing high-quality products with minimal defects.
If the filling time is too short, it may lead to incomplete filling, which results in short shots.
In contrast, prolonged filling time can cause issues like overpacking, warping, or burn marks.
Thus, controlling the filling time is pivotal towards preventing various molding defects.
Material Characteristics
Different materials have unique properties that can significantly influence the filling time.
For instance, materials with high viscosity might require more time to fill the mold, whereas those with lower viscosity may fill more quickly.
Understanding the characteristics of the material you are working with is crucial for accurate filling time adjustments.
It is also important to consider the melting temperature, flow rate, and cooling time of the material, as these can affect the filling performance in the mold cavity.
Mold Design Considerations
The design of the mold itself is another vital aspect affecting filling time.
Complex molds with intricate patterns or multiple cavities may require more precise adjustments to ensure uniform filling.
Attention must be paid to factors like gate location, runner systems, and venting.
Optimizing these aspects of mold design can assist in reducing potential defects related to filling time.
Gate Location and Size
The gate location and size play a significant role in controlling material flow into the mold.
A strategically placed gate allows for even distribution of the material, minimizing the chances of defects.
Additionally, appropriate gate sizes can prevent pressure loss and ensure efficient filling within the specified time.
It may be beneficial to experiment with different gate placements and sizes during the design stage to enhance the overall molding quality.
Runner Systems
Runner systems are channels through which molten material travels before entering the mold cavity.
An effectively designed runner system ensures that the material reaches the cavity smoothly and evenly.
It is essential to ensure the runners are of appropriate size and shape to facilitate consistent flow and reduce resistance.
Consider using balanced runner systems for molds with multiple cavities to ensure simultaneous filling and minimize defects.
Venting
Venting is crucial to allowing trapped air to escape from the mold cavity during the filling process.
Proper venting prevents air pockets from forming, which could lead to defects like burn marks or voids in the finished product.
Ensure that vents are placed strategically within the mold design to allow efficient air release without affecting the structural integrity of the product.
Adjusting Machine Parameters
Accurate adjustment of machine parameters is crucial in achieving the desired filling time.
Injection pressure, injection speed, and holding time are the primary parameters that influence filling time.
Each of these parameters must be optimized to ensure complete and even filling while avoiding defects.
Injection Pressure
Injection pressure directly affects the flow rate of the molten material into the mold cavity.
Adjusting the pressure can help control the filling speed, which is critical in preventing short shots or overpacking.
It is advisable to start with moderate pressure settings and gradually fine-tune them based on the results.
Injection Speed
The speed at which the injection process occurs plays a pivotal role in determining filling time.
Excessively high speeds may lead to defects such as warping or burn marks due to rapid material flow and friction.
Conversely, slow speeds might cause incomplete filling and short shots.
Finding the optimal injection speed requires careful experimentation and monitoring.
Holding Time
Holding time refers to the duration for which pressure is maintained after filling to ensure the material solidifies correctly.
Proper holding time allows for even cooling and solidification, reducing the risk of defects like sink marks or warping.
Adjust holding time in conjunction with cooling time to optimize overall product quality.
Trial and Error Approach
While many factors influencing filling time can be controlled theoretically, a trial and error approach is often necessary to achieve optimal results.
Conducting small sample runs can help identify any underlying issues and allow for further fine-tuning of parameters.
During this phase, closely monitoring outputs and assessing defects will provide valuable insights for making further adjustments.
Conclusion
Effectively adjusting filling time is paramount in preventing molding defects and ensuring high-quality product outcomes.
By understanding the role of material properties, mold design, and machine parameters, manufacturers can achieve optimal filling time and mitigate the risk of defects.
A combination of theoretical knowledge and practical experimentation will yield the best results, leading to efficient and precise molding processes.
資料ダウンロード
QCD調達購買管理クラウド「newji」は、調達購買部門で必要なQCD管理全てを備えた、現場特化型兼クラウド型の今世紀最高の購買管理システムとなります。
ユーザー登録
調達購買業務の効率化だけでなく、システムを導入することで、コスト削減や製品・資材のステータス可視化のほか、属人化していた購買情報の共有化による内部不正防止や統制にも役立ちます。
NEWJI DX
製造業に特化したデジタルトランスフォーメーション(DX)の実現を目指す請負開発型のコンサルティングサービスです。AI、iPaaS、および先端の技術を駆使して、製造プロセスの効率化、業務効率化、チームワーク強化、コスト削減、品質向上を実現します。このサービスは、製造業の課題を深く理解し、それに対する最適なデジタルソリューションを提供することで、企業が持続的な成長とイノベーションを達成できるようサポートします。
オンライン講座
製造業、主に購買・調達部門にお勤めの方々に向けた情報を配信しております。
新任の方やベテランの方、管理職を対象とした幅広いコンテンツをご用意しております。
お問い合わせ
コストダウンが利益に直結する術だと理解していても、なかなか前に進めることができない状況。そんな時は、newjiのコストダウン自動化機能で大きく利益貢献しよう!
(Β版非公開)