- お役立ち記事
- How to Manufacture High-Quality Products Using Extrusion Molding
How to Manufacture High-Quality Products Using Extrusion Molding
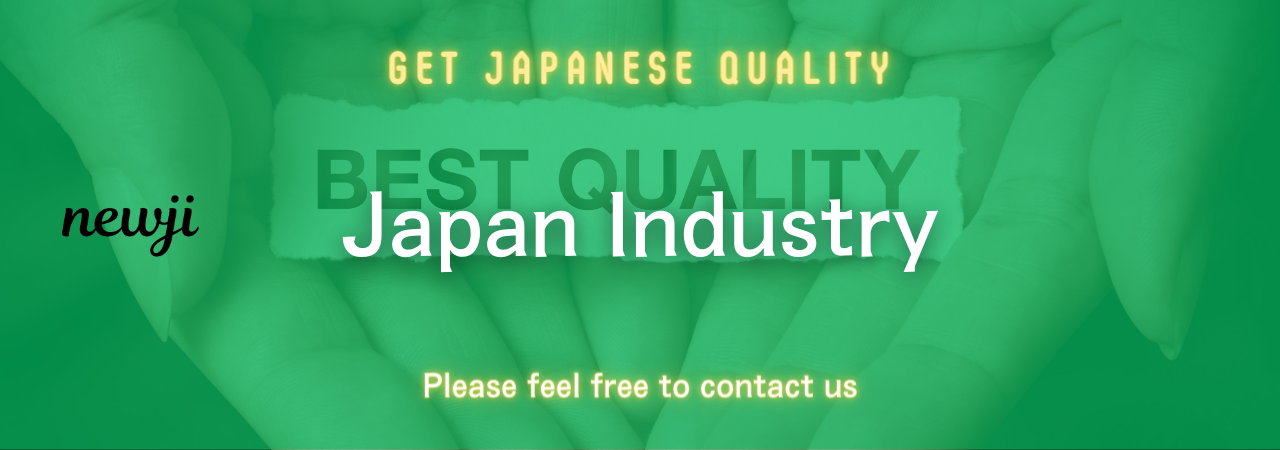
目次
Understanding Extrusion Molding
Extrusion molding is a popular manufacturing process used to create high-quality products by shaping material, typically plastic or metal, into a specific form through a die.
This method allows for the production of continuous shapes of fixed cross-sectional profiles, making it ideal for a variety of industries including automotive, construction, and consumer goods.
By leveraging the benefits of extrusion molding, manufacturers can produce durable, uniform, and efficient products.
The extrusion process involves feeding raw material into an extruder, which is a machine designed to apply heat and pressure to the material.
The extruder uses a screw mechanism to force the material through the die, ultimately shaping it into the desired form.
Once extruded, the product is cooled and cut or shaped into its final form, ready for use or further processing.
Benefits of Extrusion Molding
Extrusion molding offers several advantages over other manufacturing processes.
One of the primary benefits is its ability to produce complex shapes with uniform dimensions.
This precision is achieved due to the continuous nature of the process, allowing for consistency in output.
Another benefit is the efficiency of material usage.
Extrusion molding typically results in minimal waste as materials can be reused and recycled within the process.
This not only reduces costs but also contributes to sustainability efforts, making it an appealing option for environmentally-conscious manufacturers.
The process is also cost-effective due to its high production speeds and the ability to produce large quantities in a relatively short amount of time.
This allows manufacturers to meet high demand and fulfill orders quickly without compromising on quality.
Key Considerations for High-Quality Extrusion Molding
Producing high-quality products through extrusion molding involves several key considerations that manufacturers must keep in mind.
Attention to these factors ensures the end product meets the desired standards and specifications.
Material Selection
Selecting the appropriate material is a crucial step in ensuring product quality.
Different materials offer varying characteristics such as flexibility, strength, and thermal resistance.
Understanding the specific requirements of the product and the intended use will guide the material selection process.
Common materials used in extrusion molding include plastics like PVC, PET, and PE, as well as metals like aluminum.
Die Design
The design of the die plays a significant role in shaping the final product.
A well-designed die ensures precise dimensions and smooth finishes, contributing to the overall quality of the product.
Manufacturers should work closely with experienced die designers to address any challenges related to material flow, stress distribution, and potential defects.
Process Parameters
Optimizing process parameters is essential for achieving high-quality extrusion results.
Key parameters include temperature, pressure, and screw speed.
These variables must be carefully controlled and adjusted to suit the material properties and product specifications.
Consistent monitoring and fine-tuning of these parameters throughout the process will help maintain product uniformity and quality.
Challenges in Extrusion Molding
While extrusion molding offers numerous benefits, it also presents certain challenges that manufacturers must address to maintain product quality.
Handling Material Variability
Variability in raw materials can impact the extrusion process and the final product quality.
Slight changes in material composition or properties can lead to inconsistencies in product dimensions or surface finish.
Manufacturers need to establish strict quality control measures to monitor and manage material variability effectively.
Maintaining Equipment Performance
The performance of the extrusion equipment is vital in ensuring a consistent and reliable production process.
Regular maintenance and calibration of machines are necessary to avoid unexpected downtimes and quality issues.
Routine checks on screws, barrels, and dies can help identify and resolve potential problems before they affect production.
Addressing Environmental Factors
Changes in environmental conditions such as temperature and humidity can impact the extrusion process.
Manufacturers should establish controlled environments and adaptive procedures to mitigate the effects of these external factors.
This can involve regulating room conditions, implementing cooling systems, and maintaining optimal processing conditions.
Conclusion
Extrusion molding is an effective manufacturing process for producing high-quality products with precise dimensions and durable characteristics.
By selecting the right materials, designing efficient dies, and optimizing process parameters, manufacturers can overcome the challenges associated with extrusion molding.
It is essential for manufacturers to establish robust quality control systems and maintain their equipment to ensure a reliable and efficient production process.
By understanding and implementing best practices, extrusion molding can provide a competitive advantage in meeting customer demands and maintaining product excellence.
資料ダウンロード
QCD調達購買管理クラウド「newji」は、調達購買部門で必要なQCD管理全てを備えた、現場特化型兼クラウド型の今世紀最高の購買管理システムとなります。
ユーザー登録
調達購買業務の効率化だけでなく、システムを導入することで、コスト削減や製品・資材のステータス可視化のほか、属人化していた購買情報の共有化による内部不正防止や統制にも役立ちます。
NEWJI DX
製造業に特化したデジタルトランスフォーメーション(DX)の実現を目指す請負開発型のコンサルティングサービスです。AI、iPaaS、および先端の技術を駆使して、製造プロセスの効率化、業務効率化、チームワーク強化、コスト削減、品質向上を実現します。このサービスは、製造業の課題を深く理解し、それに対する最適なデジタルソリューションを提供することで、企業が持続的な成長とイノベーションを達成できるようサポートします。
オンライン講座
製造業、主に購買・調達部門にお勤めの方々に向けた情報を配信しております。
新任の方やベテランの方、管理職を対象とした幅広いコンテンツをご用意しております。
お問い合わせ
コストダウンが利益に直結する術だと理解していても、なかなか前に進めることができない状況。そんな時は、newjiのコストダウン自動化機能で大きく利益貢献しよう!
(Β版非公開)