- お役立ち記事
- Cost Reduction Methods Using the Latest Injection Molding Machines
月間76,176名の
製造業ご担当者様が閲覧しています*
*2025年3月31日現在のGoogle Analyticsのデータより
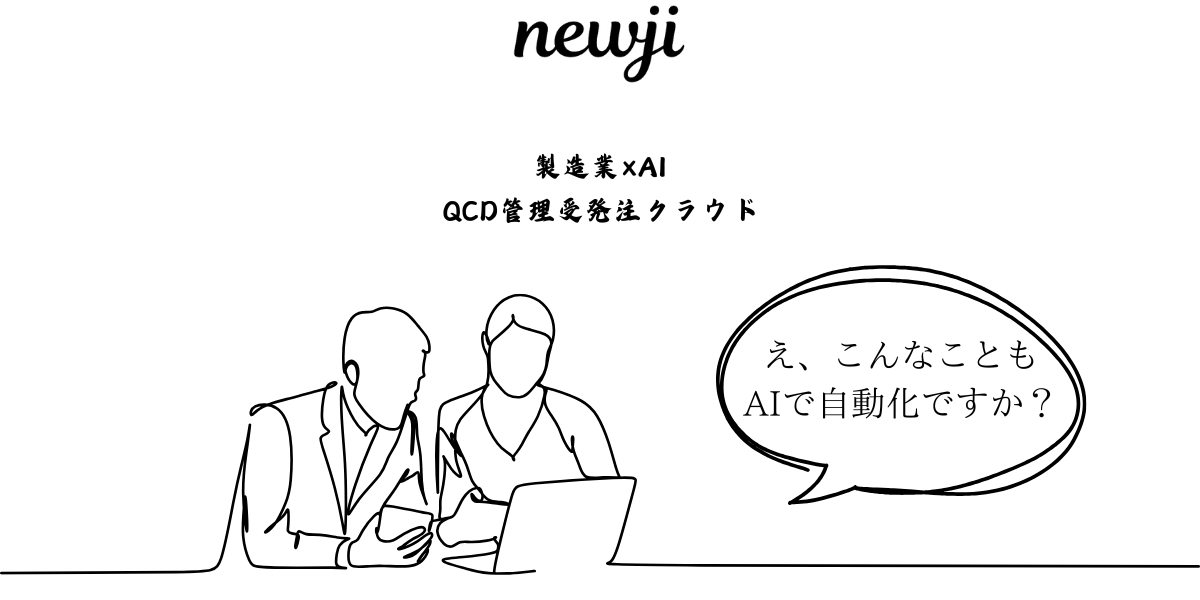
Cost Reduction Methods Using the Latest Injection Molding Machines
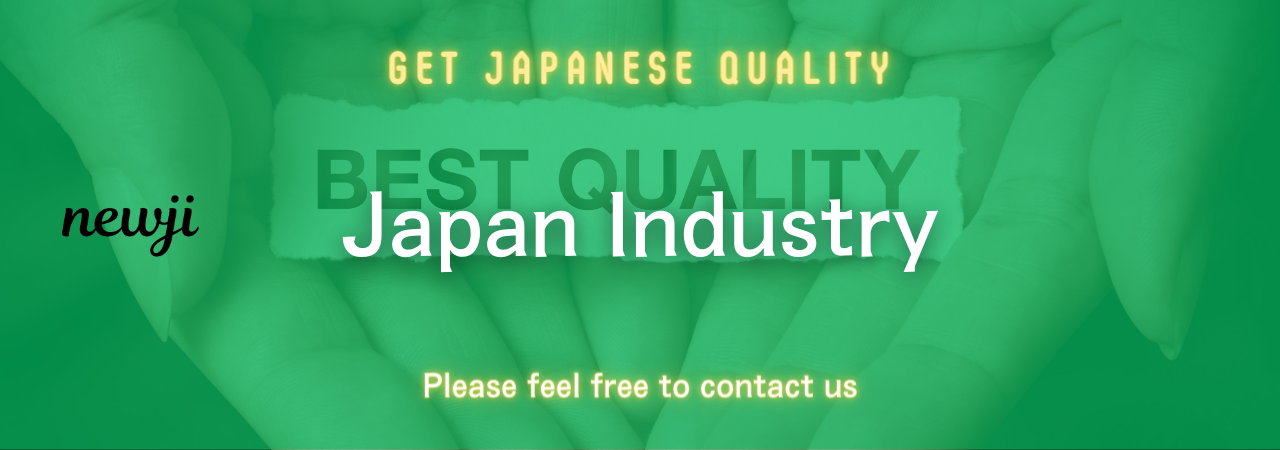
目次
Introduction to Injection Molding
Injection molding is a popular manufacturing process used to produce a wide variety of parts, from small components to large products.
It involves injecting molten material into a mold, where it cools and solidifies into the desired shape.
The process is widely used due to its ability to produce parts with high precision and repeatability.
In recent years, advancements in injection molding technology have focused on reducing costs while maintaining or improving product quality.
Understanding the Costs in Injection Molding
To effectively reduce costs, it’s essential to understand where expenses arise in the injection molding process.
Costs typically originate from several key areas: materials, machine operation, labor, and maintenance.
Material costs can be significant, particularly if using specialized materials or resins.
Machine operation involves energy consumption and wear and tear, which can lead to expensive repairs or replacements.
Labor costs include operators, technicians, and engineers necessary to oversee production.
Finally, maintenance costs include routine inspections, mold repairs, and cleaning to ensure the machinery runs smoothly.
Advancements in Injection Molding Technology
Recent technological advancements in injection molding have provided several methods for reducing costs.
These innovations focus on improving efficiency, reducing material waste, and enhancing equipment longevity.
Energy-Efficient Machines
One significant advancement is the development of energy-efficient injection molding machines.
Modern machines often feature variable-speed drives, which adjust the motor’s power consumption based on the process requirements, reducing energy usage.
Furthermore, all-electric machines, which use electric motors instead of hydraulic systems, are more energy-efficient and can reduce operational costs significantly.
Better Material Management
Innovations in material handling and recycling processes can lead to substantial cost savings.
Resin drying systems with closed-loop moisture monitoring ensure that materials are used efficiently, minimizing waste.
Advanced recycling techniques can reprocess scrap material and reintroduce it into production lines, reducing the need for raw materials.
Automation and Smart Manufacturing
Automation plays a crucial role in reducing labor costs and increasing production efficiency.
Robotic arms and automated systems can handle tasks such as part removal, assembly, and packaging, lowering the need for manual labor.
Smart manufacturing technologies, such as the Internet of Things (IoT), enable machines to communicate and optimize production processes automatically.
Predictive maintenance, supported by IoT, can reduce downtime by alerting operators to potential issues before they result in costly repairs.
Optimizing the Production Process
Streamlining the production process is another method to reduce costs, focusing on efficiency and product quality.
Cycle Time Reduction
Cycle time is the period required to produce a part, including the time taken for injection, cooling, and mold opening/closing.
Reducing cycle time is critical for increasing production efficiency.
Advancements in mold design, such as better cooling channel layouts and rapid cooling techniques, can significantly shorten cycle times.
Lean Manufacturing Principles
Implementing lean manufacturing principles can also help cut costs.
By identifying and eliminating waste at every production stage, companies can reduce unnecessary expenses.
This includes optimizing inventory levels, minimizing overproduction, and ensuring efficient transportation within the production facility.
Improving Equipment Longevity
Equipment failure can lead to production delays and increased costs, so it’s vital to ensure machines remain in optimal condition.
Regular Maintenance and Upgrades
A proactive maintenance schedule is essential for preventing unexpected breakdowns.
Regularly scheduled inspections and timely repairs can extend equipment life and reduce long-term expenses.
Additionally, staying updated with the latest machine upgrades can improve performance and reliability.
Employee Training and Skill Development
Investing in employee training ensures that operators, technicians, and engineers are adept at managing and maintaining advanced machinery.
Well-trained staff can identify and address potential issues before they escalate, maintaining efficient production and minimizing downtime.
Conclusion
By utilizing the latest injection molding machines and technologies, companies can achieve significant cost reductions.
Advancements such as energy-efficient machines, better material management, and automation play vital roles in optimizing the production process.
Through regular equipment maintenance and ongoing employee training, businesses can further enhance their operations.
These combined strategies not only reduce costs but also improve product quality and competitiveness in the marketplace.
資料ダウンロード
QCD管理受発注クラウド「newji」は、受発注部門で必要なQCD管理全てを備えた、現場特化型兼クラウド型の今世紀最高の受発注管理システムとなります。
ユーザー登録
受発注業務の効率化だけでなく、システムを導入することで、コスト削減や製品・資材のステータス可視化のほか、属人化していた受発注情報の共有化による内部不正防止や統制にも役立ちます。
NEWJI DX
製造業に特化したデジタルトランスフォーメーション(DX)の実現を目指す請負開発型のコンサルティングサービスです。AI、iPaaS、および先端の技術を駆使して、製造プロセスの効率化、業務効率化、チームワーク強化、コスト削減、品質向上を実現します。このサービスは、製造業の課題を深く理解し、それに対する最適なデジタルソリューションを提供することで、企業が持続的な成長とイノベーションを達成できるようサポートします。
製造業ニュース解説
製造業、主に購買・調達部門にお勤めの方々に向けた情報を配信しております。
新任の方やベテランの方、管理職を対象とした幅広いコンテンツをご用意しております。
お問い合わせ
コストダウンが利益に直結する術だと理解していても、なかなか前に進めることができない状況。そんな時は、newjiのコストダウン自動化機能で大きく利益貢献しよう!
(β版非公開)