- お役立ち記事
- How to Improve Mold Design Accuracy and Prevent Molding Defects
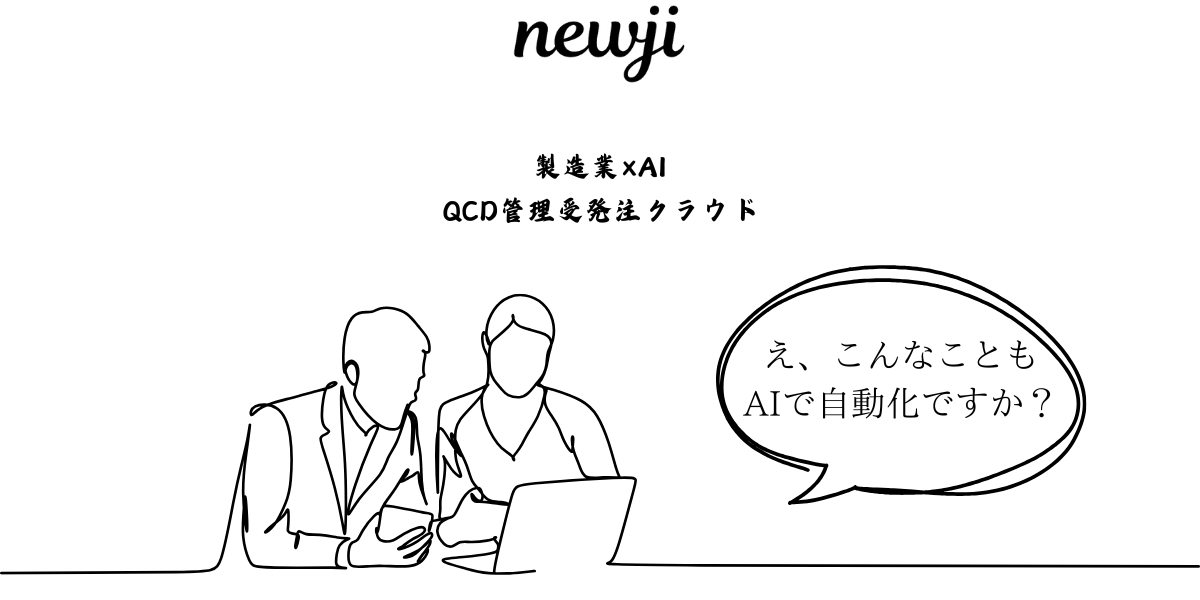
How to Improve Mold Design Accuracy and Prevent Molding Defects
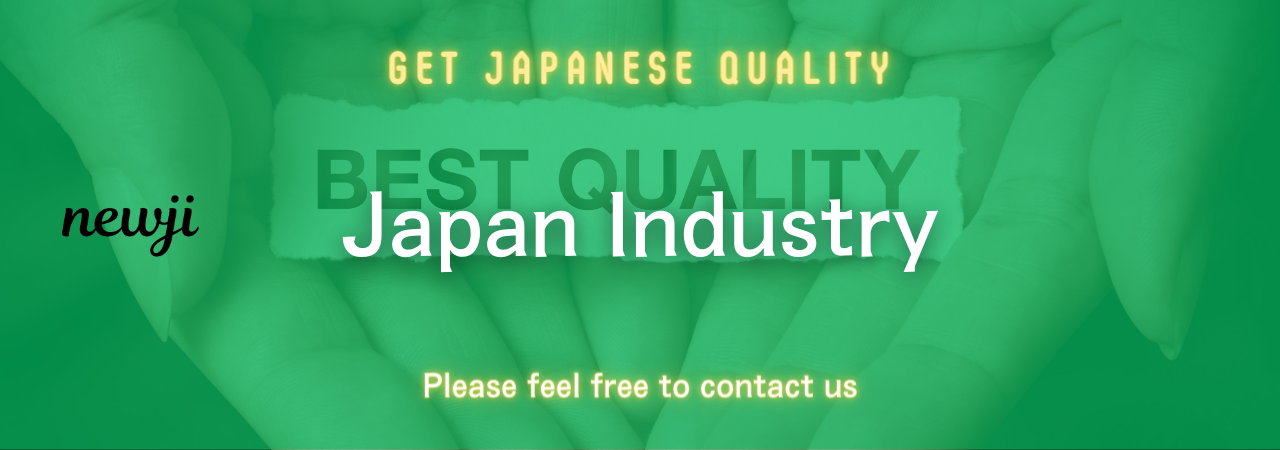
目次
Understanding Mold Design
Mold design is a critical process in manufacturing that involves creating a cavity where raw material is poured or injected to form specific shapes.
The design of the mold greatly influences the quality and precision of the final product.
Errors during this stage can lead to defects in the molded parts, causing delays and increased production costs.
Key Elements of Mold Design
The accuracy of mold design depends on several key elements.
First is the cavity size, which must match the dimensions of the desired product exactly.
Any deviation can result in excess material or under-filling, leading to defective items.
Another crucial element is the gating system, responsible for directing the flow of material into the mold.
An improperly designed gating system can cause turbulence, leading to air bubbles or uneven distribution of the material.
Cooling channels are also vital as they help regulate the mold’s temperature.
Uneven cooling can lead to warping or shrinking, impacting the product’s final shape and size.
Common Molding Defects
Understanding and recognizing common molding defects is the first step towards improving mold design accuracy.
Some prevalent defects include warping, where parts bend or twist due to uneven cooling or material shrinkage.
Sink marks, which are visible depressions on the surface, often occur when the cooling process is too slow or uneven.
Flash, a defect where excess material forms on the edges of a mold, results from gaps between the mold halves or insufficient clamp force during molding.
Additionally, voids or bubbles can appear if air gets trapped in the mold cavity during the injection process.
Strategies to Prevent Molding Defects
To improve mold design and prevent defects, one must employ several strategies.
Firstly, ensuring precise and accurate measurements during the design phase is crucial.
Using computer-aided design (CAD) software can enhance accuracy and simulate the molding process, allowing designers to identify potential issues before production begins.
Secondly, material selection plays a significant role in mold design.
Different materials have varied flow and cooling characteristics, which influence how they behave during molding.
Selecting the right material that matches the product’s production requirements is essential for achieving desired outcomes.
Regularly maintaining and calibrating mold equipment can also prevent defects.
Over time, molds can wear and develop imperfections.
Routine inspections and maintenance help detect such issues early, allowing for prompt corrections.
Furthermore, optimizing the cooling process can reduce defects like warping and shrinkage.
Setting up an efficient cooling system with properly designed channels ensures even temperature distribution across the mold, leading to uniform cooling.
Enhancing Technician Training
Skilled technicians play a pivotal role in maintaining mold accuracy and preventing defects.
Providing comprehensive training ensures technicians understand the nuances of mold design and operation.
They should be familiar with the machinery, materials, and design principles integral to the molding process.
Regular workshops and updated training programs can keep technicians abreast of the latest innovations in mold design.
This knowledge improves their ability to troubleshoot issues and maintain high levels of accuracy in production.
The Role of Technology in Mold Design
Technology innovations continuously reshape mold design, enhancing accuracy and reducing defects.
3D printing, for instance, has revolutionized prototyping in mold design.
It allows designers to create and test multiple iterations of a mold before final production, identifying potential issues early on.
Additionally, machine learning algorithms can optimize the molding process by analyzing vast amounts of data to predict and correct defects.
Such predictive analysis tools can point out areas in the design prone to errors, allowing designers to make necessary adjustments swiftly.
IoT (Internet of Things) has further enhanced mold design accuracy by connecting devices and systems for real-time monitoring.
Sensors embedded within molds can provide critical data on temperature, pressure, and more, helping technicians maintain optimal conditions during molding.
Conclusion
Improving mold design accuracy and preventing molding defects is an ongoing challenge that requires a multifaceted approach.
From understanding the key elements of design to preventing common defects and embracing technological advancements, manufacturers can significantly improve their processes.
By investing in precise measurements, regular maintenance, skilled technicians, and innovative technology, companies can enhance production quality, ensuring smooth operations and high-quality products.
This commitment to accuracy not only reduces waste and costs but also leads to greater customer satisfaction and trusted brand reputation.
資料ダウンロード
QCD調達購買管理クラウド「newji」は、調達購買部門で必要なQCD管理全てを備えた、現場特化型兼クラウド型の今世紀最高の購買管理システムとなります。
ユーザー登録
調達購買業務の効率化だけでなく、システムを導入することで、コスト削減や製品・資材のステータス可視化のほか、属人化していた購買情報の共有化による内部不正防止や統制にも役立ちます。
NEWJI DX
製造業に特化したデジタルトランスフォーメーション(DX)の実現を目指す請負開発型のコンサルティングサービスです。AI、iPaaS、および先端の技術を駆使して、製造プロセスの効率化、業務効率化、チームワーク強化、コスト削減、品質向上を実現します。このサービスは、製造業の課題を深く理解し、それに対する最適なデジタルソリューションを提供することで、企業が持続的な成長とイノベーションを達成できるようサポートします。
オンライン講座
製造業、主に購買・調達部門にお勤めの方々に向けた情報を配信しております。
新任の方やベテランの方、管理職を対象とした幅広いコンテンツをご用意しております。
お問い合わせ
コストダウンが利益に直結する術だと理解していても、なかなか前に進めることができない状況。そんな時は、newjiのコストダウン自動化機能で大きく利益貢献しよう!
(Β版非公開)