- お役立ち記事
- Achieving an Efficient Molding Process Through Shot Size Adjustment
Achieving an Efficient Molding Process Through Shot Size Adjustment
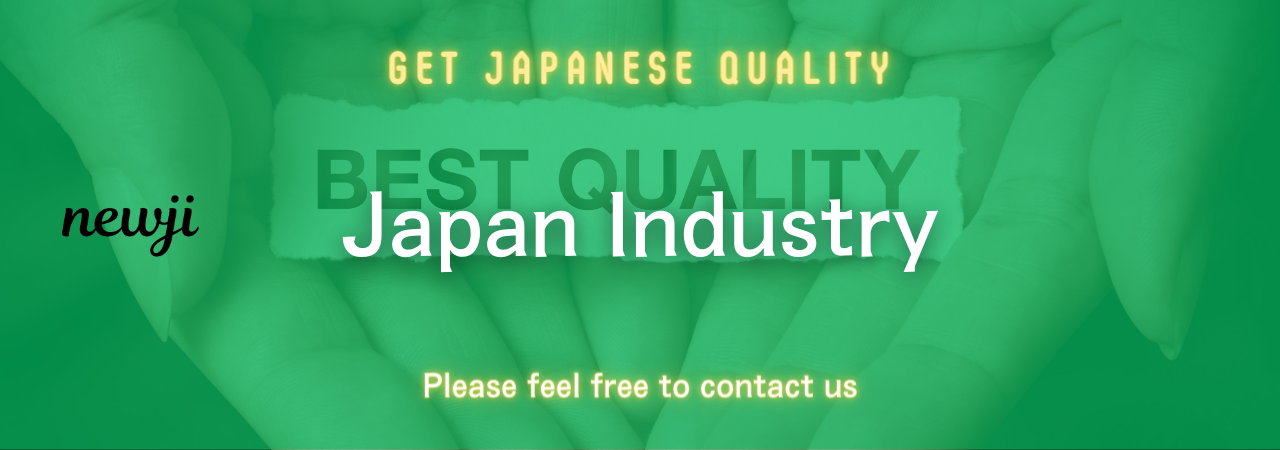
目次
Understanding the Importance of Shot Size in Molding
In the world of manufacturing, especially in molding processes, efficiency is the key to success.
When it comes to achieving efficiency, one of the critical factors is the adjustment of shot size.
Shot size refers to the amount of material injected into a mold during the molding process.
Proper management of shot size can lead to significant improvements in product quality, production speed, and cost-effectiveness.
Shot size adjustment is often overlooked, but it’s what ensures that products are consistently well-formed and free from defects.
An incorrect shot size can lead to problems such as incomplete filling, flash, or excessive wear and tear on molds.
Efficient management of shot size not only saves time but also reduces waste, ensuring businesses remain competitive in today’s market.
The Role of Shot Size in Molding Efficiency
The role of shot size in molding is substantial.
A correctly adjusted shot size means all the cavities in the mold are filled adequately without generating flash or excessive material use.
It ensures that each mold cycle produces parts that meet quality standards, saving time in quality control and finishing.
Additionally, optimally adjusted shot size can reduce material costs and extend the life of the mold.
Perfecting the shot size ensures the electronic components, automotive parts, or even simple plastic toys produced are of top-notch quality.
The challenge for manufacturers is to balance between too little or too much material.
Both extremes lead to inefficiencies either through the production of defective items or through wasted materials.
How to Adjust Shot Size for Better Results
Adjusting shot size correctly requires understanding the intricacies of the molding process.
Firstly, it’s crucial to analyze the material type since different materials have unique flow characteristics and behaviors when heated.
Conducting tests to determine the best shot size for the specific material in use is a practical approach.
Next, consider the mold design, complexity, and the number of cavities.
Complicated mold designs or designs with many cavities may demand a reevaluation of the shot size to achieve full cavity filling without spilling over.
Consistent monitoring and adjustment during production can also help maintain the right shot size.
Technological advancements like automated systems and sensors can continually check and adjust the shot size in real-time, ensuring a streamlined process.
Common Problems Due to Incorrect Shot Size
Incorrect shot size in molding processes often results in a range of problems, each capable of compromising product quality.
When the shot size is too small, the mold cavities may not fill completely, leading to defects known as short shots.
These incomplete parts cannot be used and result in wasted material and labor.
Conversely, if the shot size is too large, the material will overflow from the mold, creating flash.
Flash requires additional work to trim and affects the aesthetics and integrity of the finished product.
Excessive shot size can also place undue stress on the mold, causing premature wear or damage.
These problems highlight why it is essential to set and maintain the correct shot size, ensuring that neither the product quality nor the production efficiency suffers.
Benefits of Optimizing Shot Size
Optimizing shot size in the molding process offers numerous benefits that can enhance a company’s operational efficiency and product quality.
First and foremost, it ensures product consistency and quality across every production cycle.
Uniform shot size minimizes defects, allowing for fewer rejects and less waste.
Additionally, by optimizing shot size, manufacturers can significantly reduce material consumption.
This efficiency not only cuts costs associated with raw materials but also supports sustainable manufacturing practices by minimizing waste.
Moreover, correct shot size adjustment helps prolong the life of molds.
Reducing the mechanical stress and flash formed during the molding process means that molds will not wear out as quickly, postponing the need for costly replacements or repairs.
Implementing Shot Size Control in Your Facility
To implement effective shot size control in a manufacturing facility, companies must equip themselves with relevant technology and train their staff adequately.
Investing in modern machinery that provides precise shot size control is an excellent starting point.
Machines with built-in sensors and feedback systems can automatically adjust shot size, enhancing the reliability and quality of the process.
Training the workforce is equally important.
Staff should understand the significance of shot size adjustment and be able to identify and rectify any inconsistencies in production.
Regular workshops and continuous education in technological advancements can keep the team knowledgeable and adept in handling complex scenarios.
Furthermore, developing a comprehensive quality assurance program can support the process.
Such a program should include regular inspections and adjustments of shot sizes, ensuring adherence to quality standards.
Conclusion
In conclusion, adjusting shot size in the molding process is a crucial aspect of achieving higher efficiency.
By understanding the importance of shot size and making the necessary adjustments, manufacturers can significantly enhance product quality, reduce material costs, and extend mold life.
Implementing modern technologies and proper training programs further facilitates successful shot size control.
By prioritizing these strategies, businesses can optimize their production processes and maintain a competitive edge in the ever-evolving marketplace.
As the manufacturing industry continues to grow, those who adapt and refine their techniques will surely lead the charge in efficiency and quality.
資料ダウンロード
QCD調達購買管理クラウド「newji」は、調達購買部門で必要なQCD管理全てを備えた、現場特化型兼クラウド型の今世紀最高の購買管理システムとなります。
ユーザー登録
調達購買業務の効率化だけでなく、システムを導入することで、コスト削減や製品・資材のステータス可視化のほか、属人化していた購買情報の共有化による内部不正防止や統制にも役立ちます。
NEWJI DX
製造業に特化したデジタルトランスフォーメーション(DX)の実現を目指す請負開発型のコンサルティングサービスです。AI、iPaaS、および先端の技術を駆使して、製造プロセスの効率化、業務効率化、チームワーク強化、コスト削減、品質向上を実現します。このサービスは、製造業の課題を深く理解し、それに対する最適なデジタルソリューションを提供することで、企業が持続的な成長とイノベーションを達成できるようサポートします。
オンライン講座
製造業、主に購買・調達部門にお勤めの方々に向けた情報を配信しております。
新任の方やベテランの方、管理職を対象とした幅広いコンテンツをご用意しております。
お問い合わせ
コストダウンが利益に直結する術だと理解していても、なかなか前に進めることができない状況。そんな時は、newjiのコストダウン自動化機能で大きく利益貢献しよう!
(Β版非公開)