- お役立ち記事
- Technologies for Optimizing Precision Injection Molding Cycles and Efficiency
Technologies for Optimizing Precision Injection Molding Cycles and Efficiency
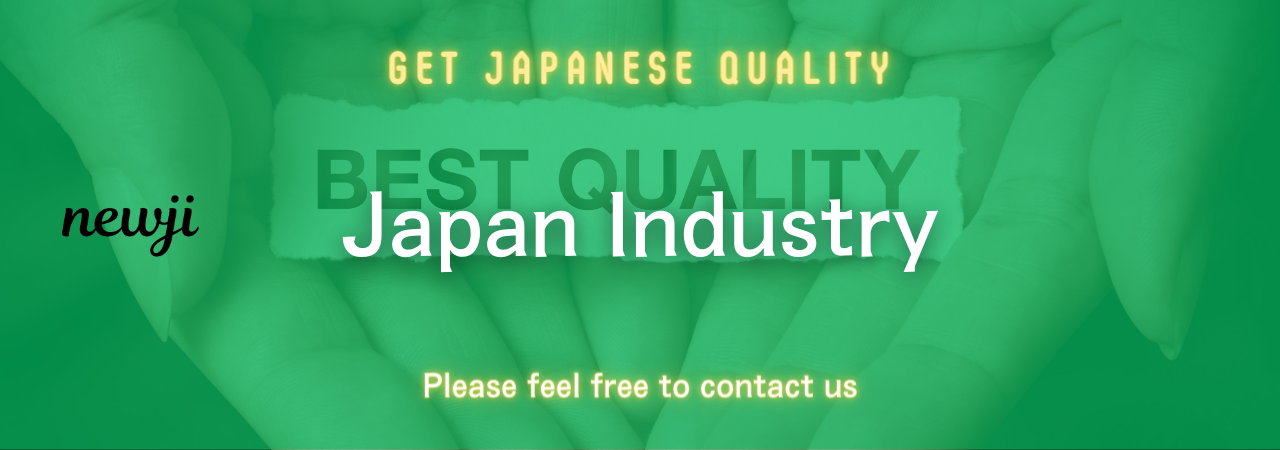
目次
Introduction to Precision Injection Molding
Precision injection molding has become a critical process in the manufacturing industry, especially for producing parts with intricate designs and tight tolerances.
This technique is used in various sectors, from automotive to healthcare, because it offers high efficiency, precision, and flexibility in creating complex plastic components.
To maintain competitiveness and meet the growing demands for product quality and minimized production costs, manufacturers continuously seek advancements in injection molding technologies.
Understanding Cycle Time in Injection Molding
One of the most significant factors influencing the efficiency of the injection molding process is the cycle time, which determines how quickly products can be manufactured.
Cycle time is the duration required to complete one molding cycle, including injection, cooling, and ejection phases.
Minimizing cycle time while ensuring the quality of the final product is paramount in optimizing production efficiency.
Several elements contribute to the overall cycle time.
These include material type, mold design, cooling rate, and machine performance.
Efforts to shorten cycle time aim to enhance these aspects without compromising the structural integrity or dimensional accuracy of the molded parts.
Technologies Enhancing Injection Molding Efficiency
The advancement of precision injection molding technologies has led to the emergence of innovative methods and tools that significantly optimize efficiency.
Among these technologies are:
Advanced Mold Materials and Design
The use of high-performance materials for mold manufacturing improves heat transfer and reduces the cooling time per cycle.
Design adjustments, such as conformal cooling channels, provide uniform cooling across the mold.
This enhancement effectively decreases cycle time and energy consumption.
Conformal cooling is designed using 3D printing technologies, which allows for complex geometries that improve heat dissipation.
Process Automation and Monitoring
The integration of automation in injection molding processes streamlines operations, reduces manual errors, and increases throughput.
Robots and automated systems handle tasks like part removal and quality inspection, delivering efficiency and consistency.
Additionally, real-time monitoring systems evaluate various parameters, such as temperature and injection pressure, to maintain optimal conditions throughout the cycle.
Data collected from these systems enable predictive maintenance and process improvement.
Precision Control Systems
Sophisticated control systems with advanced sensors and software manage precise parameters within the molding process.
These systems modify variables in real-time to ensure consistent quality and minimize waste.
By maintaining accurate control over injection speeds, pressures, and temperatures, manufacturers can achieve shorter cycle times without sacrificing precision.
Energy-Efficient Machinery
Modern injection molding machines are designed with energy efficiency in mind.
Energy-saving techniques, such as servo-driven hydraulic systems and optimized motor designs, help reduce power consumption.
These machines adjust energy usage to match the needs of each phase of the injection cycle, decreasing operating costs and environmental impact.
Advanced Material Compounds
The development of new material compounds with superior thermal properties facilitates faster cycle times.
By selecting materials that cool and set quickly without compromising on quality, manufacturers can increase the speed of production significantly.
Improving Quality while Reducing Cycle Time
While optimizing cycle time is essential, manufacturers must balance speed with quality.
New technologies ensure this balance by offering enhanced control over injection molding processes:
Simulation Software
Simulation tools help in designing processes that minimize defects such as warping and sink marks.
By previewing how materials are likely to behave under certain conditions, engineers can make adjustments before production begins, reducing the trial-and-error associated with traditional methods.
Material Characterization
Understanding the precise behavior of materials used in injection molding can improve cycle times.
By examining properties such as melting points and viscosity, manufacturers can adjust machines to handle specific materials more effectively, addressing potential quality issues upfront.
Precision Temperature Control
By managing mold temperature with accuracy, manufacturers can prevent problems such as unintentional crystallization or incomplete fills.
Precision temperature control also contributes to reducing cooling times and improving overall part quality.
The Future of Precision Injection Molding
As the demand for sophisticated plastic components grows, the evolution of injection molding technologies will continue.
Future advancements will likely focus on further reducing cycle times and enhancing the quality and sustainability of the process.
Emerging trends, such as the integration of machine learning and artificial intelligence, promise to bring about revolutionary improvements in productivity and part design.
Machine learning algorithms will improve material selection and process setup by analyzing large datasets.
With advancements in AI, predictive maintenance and the optimization of cycle parameters will become even more efficient, ensuring greater operational uptime and reducing waste.
Conclusion
Optimizing precision injection molding cycles and efficiency involves a combination of improved machine technologies, advanced materials, and enhanced process control.
By leveraging these innovations, manufacturers can reduce production time and costs while delivering high-quality products.
As technology advances, the injection molding industry will continue to evolve, driven by the need to meet the ever-increasing demands of various markets.
資料ダウンロード
QCD調達購買管理クラウド「newji」は、調達購買部門で必要なQCD管理全てを備えた、現場特化型兼クラウド型の今世紀最高の購買管理システムとなります。
ユーザー登録
調達購買業務の効率化だけでなく、システムを導入することで、コスト削減や製品・資材のステータス可視化のほか、属人化していた購買情報の共有化による内部不正防止や統制にも役立ちます。
NEWJI DX
製造業に特化したデジタルトランスフォーメーション(DX)の実現を目指す請負開発型のコンサルティングサービスです。AI、iPaaS、および先端の技術を駆使して、製造プロセスの効率化、業務効率化、チームワーク強化、コスト削減、品質向上を実現します。このサービスは、製造業の課題を深く理解し、それに対する最適なデジタルソリューションを提供することで、企業が持続的な成長とイノベーションを達成できるようサポートします。
オンライン講座
製造業、主に購買・調達部門にお勤めの方々に向けた情報を配信しております。
新任の方やベテランの方、管理職を対象とした幅広いコンテンツをご用意しております。
お問い合わせ
コストダウンが利益に直結する術だと理解していても、なかなか前に進めることができない状況。そんな時は、newjiのコストダウン自動化機能で大きく利益貢献しよう!
(Β版非公開)