- お役立ち記事
- How to Create High-Value Products Using Multi-Injection Molding Technology
How to Create High-Value Products Using Multi-Injection Molding Technology
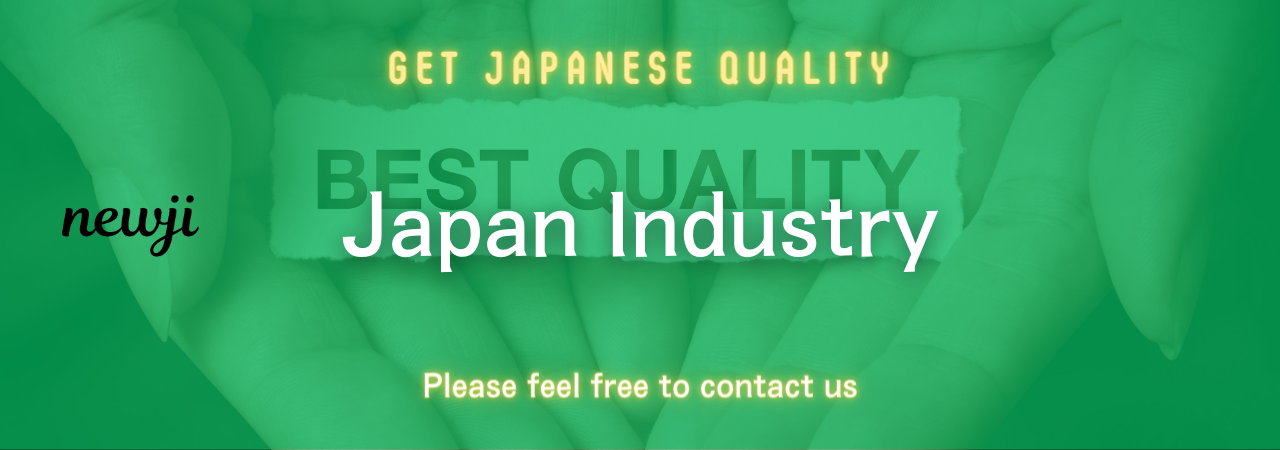
目次
Understanding Multi-Injection Molding Technology
Multi-injection molding technology is a state-of-the-art process used in manufacturing to create complex and high-value products.
It involves injecting two or more materials into a single mold during the manufacturing process.
This combination allows producers to achieve designs and functionalities that are difficult to accomplish with traditional single-shot molding techniques.
The primary benefit of multi-injection molding is its ability to combine different materials and colors in a single product without the need for assembly or adhesives.
This results in products that are more durable, aesthetically pleasing, and cost-effective to manufacture.
Types of Multi-Injection Molding
There are several types of multi-injection molding techniques, each serving unique manufacturing needs.
Understanding these can help businesses choose the best method for their specific application.
– **Co-injection Molding**: This process involves injecting two different materials into a mold, one after the other.
The first material (usually called the “skin”) forms the outer layer of the product, while the second material (the “core”) fills the interior.
Co-injection molding is used for products where the exterior requires a different material property than the core.
– **Overmolding**: Overmolding involves placing a pre-molded insert into the mold and then injecting a second material over it.
This technique is often used to combine soft-touch materials, like rubber grips, onto a firmer plastic product.
– **Sequential Injection Molding**: In this process, different materials are injected in succession into a mold that is divided into sections.
This allows the creation of multi-material products with complex designs without manual intervention.
– **Bi-injection Molding**: This technique involves injecting two different materials into separate yet connected cavities.
It is suitable for creating parts that need two distinct colors or materials.
Benefits of Multi-Injection Molding
Multi-injection molding technology offers various advantages that add value to the manufacturing process and final products:
– **Design Flexibility**: The ability to incorporate multiple materials and colors increases design possibilities.
Manufacturers can create intricate and visually appealing designs without additional painting or finishing processes.
– **Cost-Efficiency**: By eliminating the need for assembly, adhesives, or additional finishing processes, multi-injection molding can significantly reduce production costs.
This efficiency results in a faster time to market for products.
– **Improved Product Quality**: Products created through multi-injection molding are known for their enhanced strength and durability.
The bonding of materials during the molding process creates a robust connection that does not come apart easily.
– **Environmental Benefits**: Multi-injection molding reduces waste since there’s no need for additional gluing or painting processes that might involve harmful chemicals.
The technology also allows for material optimization, ensuring optimal use of resources.
Steps to Create High-Value Products with Multi-Injection Molding
To create high-value products using multi-injection molding technology, it is essential to follow a structured approach from the design phase to the final product delivery.
1. Product Design and Material Selection
The initial step is designing the product and selecting the appropriate materials for each component.
It’s crucial to consider the material properties required for each part of the product, such as hardness, flexibility, and thermal resistance.
The design should account for the right flow balance during the molding process to ensure seamless integration of materials.
2. Mold Design and Fabrication
The next step is designing and fabricating the mold.
A high-quality mold is central to achieving precise and repeatable outcomes in multi-injection molding.
Tools like CAD software are typically used to design molds that accommodate the product’s complexity.
A well-designed mold will ensure the correct placement and bonding of materials during the injection process.
3. Process Setup and Optimization
Setting up the injection molding machine with precise control over temperature, pressure, and injection timing is crucial for successful multi-material integration.
Optimization may involve trial runs and adjustments to eliminate flaws such as warping or improper bonding.
Advanced technologies like 3D simulation can be used to predict and correct potential production issues.
4. Quality Control and Testing
Quality control procedures should be put in place to ensure product consistency and reliability.
Testing might include mechanical stress tests or color-matching assessments, depending on the end-use application of the product.
Ensuring that each product meets quality standards will help maintain brand reputation and consumer trust.
Applications of Multi-Injection Molding
Multi-injection molding is employed in diverse industries for producing a range of products.
– **Automotive Industry**: This technology is used to create durable and aesthetically pleasing interior components, handles, and weather seals.
The ability to combine materials enhances comfort and functionality in automotive products.
– **Consumer Electronics**: Manufacturers use multi-injection molding to craft lightweight yet robust casings and components that require varying material properties, such as flexibility and rigidity.
– **Medical Devices**: Precision and reliability are critical in medical device manufacturing.
Multi-injection molding allows for the creation of products with finely tuned properties, important for product safety and efficacy.
– **Household Goods**: From kitchen utensils to ergonomic tools, multi-injection molding enables the combination of textures and colors to enhance both function and consumer appeal.
In conclusion, multi-injection molding technology offers a myriad of advantages for creating high-value, multifaceted products.
With the right approach to design, materials, and process optimization, businesses can leverage this technology to enhance product quality, improve cost efficiency, and reduce environmental impact.
資料ダウンロード
QCD調達購買管理クラウド「newji」は、調達購買部門で必要なQCD管理全てを備えた、現場特化型兼クラウド型の今世紀最高の購買管理システムとなります。
ユーザー登録
調達購買業務の効率化だけでなく、システムを導入することで、コスト削減や製品・資材のステータス可視化のほか、属人化していた購買情報の共有化による内部不正防止や統制にも役立ちます。
NEWJI DX
製造業に特化したデジタルトランスフォーメーション(DX)の実現を目指す請負開発型のコンサルティングサービスです。AI、iPaaS、および先端の技術を駆使して、製造プロセスの効率化、業務効率化、チームワーク強化、コスト削減、品質向上を実現します。このサービスは、製造業の課題を深く理解し、それに対する最適なデジタルソリューションを提供することで、企業が持続的な成長とイノベーションを達成できるようサポートします。
オンライン講座
製造業、主に購買・調達部門にお勤めの方々に向けた情報を配信しております。
新任の方やベテランの方、管理職を対象とした幅広いコンテンツをご用意しております。
お問い合わせ
コストダウンが利益に直結する術だと理解していても、なかなか前に進めることができない状況。そんな時は、newjiのコストダウン自動化機能で大きく利益貢献しよう!
(Β版非公開)