- お役立ち記事
- Effective Burr Prevention Methods and Their Relationship to Cost Reduction
Effective Burr Prevention Methods and Their Relationship to Cost Reduction
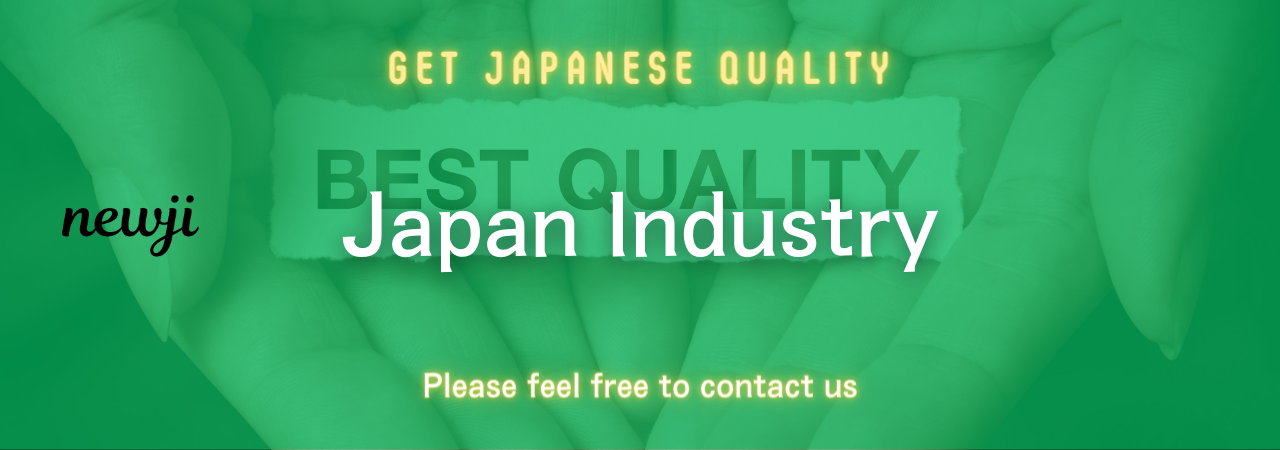
In the manufacturing industry, ensuring product quality while managing costs is a critical balance to strike.
One often overlooked aspect of this is dealing with burrs, the unwanted rough edges or pieces left on metal or other materials by cutting or machining processes.
Effective burr prevention not only enhances the quality and safety of the final product but also plays a significant role in cost reduction.
目次
Understanding Burrs and Their Impact
Burrs occur every time metal or similar materials are machined, cut, or stamped.
They may appear as small, raised particles or jagged edges that can affect the functionality of a product.
If burrs are not addressed, they can lead to several issues: compromising the assembly of parts, creating safety hazards, and adversely impacting product performance.
This means that addressing burrs is not just a matter of finishing aesthetics; it is essential to maintaining rigorous standards of functionality and safety.
The Cost Implications of Improper Burr Management
When burrs are not efficiently managed, they can incur significant costs.
These costs manifest in various ways, including increased time and resources for manual deburring, reduced efficiency in automated systems, and potential recalls of defective products.
Moreover, the presence of burrs can lead to damage during assembly, resulting in additional waste and requiring repair or replacement parts, which further drives up production costs.
Investing in effective burr prevention and control measures can thus yield considerable cost savings by minimizing these unnecessary expenses.
This investment not only enhances production efficiency but also supports a company’s reputation for quality and reliability.
Effective Burr Prevention Methods
To prevent burrs effectively, several methods can be employed in the manufacturing process.
Here’s a look at some of the most effective strategies:
1. Optimizing Tool Selection and Maintenance
Using the right tools and maintaining them properly is foundational to minimizing burr formation.
Selecting high-quality tools that are appropriate for the specific material and cutting task can significantly reduce the occurrence of burrs.
Regular maintenance of cutting tools, including sharpening and replacing worn components, ensures they function optimally, thereby reducing burr creation.
2. Advanced Machining Techniques
Incorporating advanced machining techniques can significantly reduce or even eliminate burrs.
For example, using precision laser cutting, water jet cutting, or electrical discharge machining (EDM) methods can enhance accuracy and cleanliness of cuts, minimizing burrs.
These techniques, while sometimes more expensive initially, reduce the need for secondary deburring processes, thereby saving on labor and time costs in the long run.
3. Deburring Technologies and Equipment
When burrs inevitably do occur, employing effective deburring technologies is crucial.
Automated deburring machines, such as vibratory finishers or tumblers, can handle large volumes efficiently.
Also, implementing robotic deburring for high-precision tasks can improve consistency and reduce the time required for manual inspection and rework.
4. Implementing Software Solutions
Modern manufacturing often leverages advanced CAD/CAM software solutions that help in designing for manufacturability, including burr prevention.
These programs can simulate machining processes in a digital environment and suggest adjustments to reduce cutting forces and optimize the feed rate, which assists in minimizing burr formation.
5. Employee Training and Best Practices
Investing in employee training ensures that the workforce is skilled in operating machinery according to best practices that minimize burrs.
Educating workers about the importance of proper tool alignment, correct feed rates, and regular machine maintenance can lead to significant reductions in burr formation.
The Relationship Between Burr Prevention and Cost Reduction
By incorporating these burr prevention strategies, companies can fundamentally change their cost structures.
Reduced burr-related defects mean fewer returns and warranty claims, and enhanced product quality increases customer satisfaction and loyalty.
Further, when less time and fewer resources are spent on post-processing tasks like deburring, production lines can operate more efficiently, reducing operational costs.
In essence, while the upfront investment in advanced tools, technologies, and training might seem high, these costs are often offset by the savings garnered through increased product quality, reduced wastage, and enhanced production speed.
The cumulative effect can be a considerable reduction in overall production costs, allowing companies to remain competitive in price-sensitive markets.
Conclusion
Effective burr prevention is a clear pathway to achieving substantial cost reductions in manufacturing.
By adopting a proactive approach to managing burr formation through optimized tool use, advanced technologies, appropriate equipment, and staff training, manufacturers not only ensure the superior quality of their products but also create significant efficiencies within their operations.
This balance of quality and cost-effectiveness makes burr prevention an essential focus for companies looking to maintain a competitive edge in today’s market.
資料ダウンロード
QCD調達購買管理クラウド「newji」は、調達購買部門で必要なQCD管理全てを備えた、現場特化型兼クラウド型の今世紀最高の購買管理システムとなります。
ユーザー登録
調達購買業務の効率化だけでなく、システムを導入することで、コスト削減や製品・資材のステータス可視化のほか、属人化していた購買情報の共有化による内部不正防止や統制にも役立ちます。
NEWJI DX
製造業に特化したデジタルトランスフォーメーション(DX)の実現を目指す請負開発型のコンサルティングサービスです。AI、iPaaS、および先端の技術を駆使して、製造プロセスの効率化、業務効率化、チームワーク強化、コスト削減、品質向上を実現します。このサービスは、製造業の課題を深く理解し、それに対する最適なデジタルソリューションを提供することで、企業が持続的な成長とイノベーションを達成できるようサポートします。
オンライン講座
製造業、主に購買・調達部門にお勤めの方々に向けた情報を配信しております。
新任の方やベテランの方、管理職を対象とした幅広いコンテンツをご用意しております。
お問い合わせ
コストダウンが利益に直結する術だと理解していても、なかなか前に進めることができない状況。そんな時は、newjiのコストダウン自動化機能で大きく利益貢献しよう!
(Β版非公開)