- お役立ち記事
- For SMEs: A Guide to Implementing Precision Injection Molding and Managing Costs
For SMEs: A Guide to Implementing Precision Injection Molding and Managing Costs
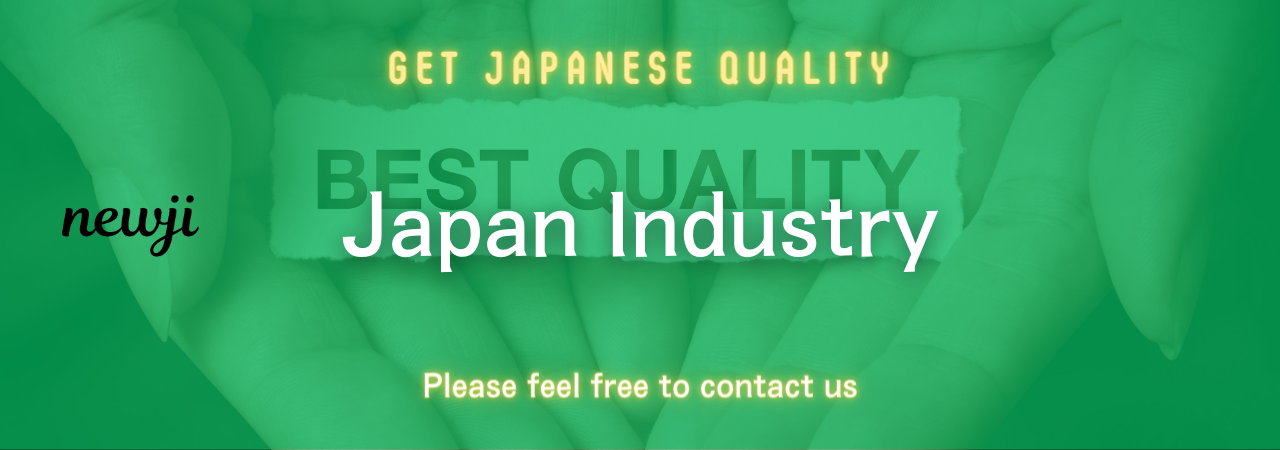
目次
Understanding Precision Injection Molding
Precision injection molding is a manufacturing process that involves creating intricate plastic parts by injecting molten material into a precisely designed mold.
This method ensures high accuracy, consistency, and efficiency in producing components that meet stringent specifications.
The process is particularly beneficial for industries requiring detailed parts with tight tolerances, such as automotive, electronics, and medical devices.
For small to medium-sized enterprises (SMEs), adopting precision injection molding can lead to significant competitive advantages.
The Benefits of Precision Injection Molding for SMEs
Precision injection molding offers several benefits that can enhance the operational capabilities of SMEs.
Firstly, it delivers high repeatability, which is crucial for maintaining consistency in product quality over large production runs.
This consistency helps SMEs uphold brand reputation and meet customer expectations, which is vital in competitive markets.
Secondly, the process allows for complex design capabilities that are not feasible with other manufacturing methods.
This flexibility enables SMEs to produce unique products that differentiate them from competitors.
Moreover, precision injection molding is a cost-effective solution when producing large volumes due to lower material wastage and efficient cycle times.
Additionally, this technology supports sustainable practices by minimizing scrap and energy consumption.
By using precision injection molding, SMEs can align their operations with modern environmental standards, appealing to environmentally conscious consumers.
Implementing Precision Injection Molding in SMEs
For SMEs looking to implement precision injection molding, the initial step is to understand the specific requirements of your products.
It’s essential to assess the complexity, material needs, and volume of production.
Collaborating with mold makers and design engineers experienced in precision injection molding can provide valuable insights into feasibility and design optimization.
Selecting the right materials is critical, as they influence the durability and functionality of the final product.
Consultation with material specialists can aid in choosing plastics or composites that meet performance criteria and industry standards.
Investing in high-quality equipment is also vital, as this ensures operational efficiency and precision.
While the upfront cost might be significant, investing in reliable machinery can reduce maintenance costs and downtime in the long run.
Furthermore, training staff on equipment operation and maintenance is imperative to maximize productivity and ensure safety standards are met.
Regular training sessions and workshops can keep your workforce updated with the latest industry practices.
Choosing the Right Precision Molding Partner
Partnering with a reputable precision injection molding service provider can ease the implementation process for SMEs.
When selecting a partner, consider their experience, capabilities, and track record in delivering quality products.
A good partner can offer guidance on mold design, material selection, and process optimization.
Evaluate potential partners based on their response time and willingness to collaborate on projects.
Effective communication and a mutual understanding of goals are crucial for a successful partnership.
Additionally, review case studies and client testimonials to gauge their ability to handle projects similar to yours.
This can provide insights into their problem-solving skills and reliability in meeting deadlines.
Cost Management in Precision Injection Molding
Managing costs is a primary concern for SMEs venturing into precision injection molding.
Understanding cost components and finding areas for optimization can help maintain financial health while benefiting from high-precision manufacturing.
The most significant cost factors include mold creation, material selection, production volume, and labor.
Custom molds are typically the largest expense, and SMEs should aim for designs that maximize efficiency and longevity.
Using standardized components for mold design can reduce customization needs and cost.
Material costs are another key consideration.
While selecting high-performance materials may incur higher costs initially, they often result in longer-lasting products and lower long-term expenses.
Opt for suppliers who can provide competitive pricing and consistent quality.
Volume is also crucial; higher production runs generally lower the per-unit cost.
When feasible, plan production schedules to reach economies of scale.
To manage labor costs, consider automating certain steps of the injection molding process if possible.
Automation can enhance precision, reduce human error, and increase production speed, offsetting initial investments in technology.
Finally, consider exploring alternative financing options or governmental incentives tailored for SMEs looking to adopt innovative manufacturing technologies.
These can provide the necessary capital while easing the transition into precision molding.
Ongoing Maintenance and Upgrades
After implementing precision injection molding, continual maintenance and upgrades are essential for sustained success.
Scheduled maintenance prevents unexpected breakdowns and prolongs the life of your equipment.
Stay informed about the latest developments in injection molding technology.
Upgrades to machinery can improve efficiency, reduce waste, and enhance product quality.
Moreover, maintaining a relationship with your precision molding partner can facilitate knowledge exchange and keep you abreast of industry trends.
Their expertise can serve as an invaluable resource for solving challenges and capitalizing on new opportunities.
By combining strategic planning with disciplined execution, SMEs can effectively adopt precision injection molding, manage costs, and thrive in competitive industries.
資料ダウンロード
QCD調達購買管理クラウド「newji」は、調達購買部門で必要なQCD管理全てを備えた、現場特化型兼クラウド型の今世紀最高の購買管理システムとなります。
ユーザー登録
調達購買業務の効率化だけでなく、システムを導入することで、コスト削減や製品・資材のステータス可視化のほか、属人化していた購買情報の共有化による内部不正防止や統制にも役立ちます。
NEWJI DX
製造業に特化したデジタルトランスフォーメーション(DX)の実現を目指す請負開発型のコンサルティングサービスです。AI、iPaaS、および先端の技術を駆使して、製造プロセスの効率化、業務効率化、チームワーク強化、コスト削減、品質向上を実現します。このサービスは、製造業の課題を深く理解し、それに対する最適なデジタルソリューションを提供することで、企業が持続的な成長とイノベーションを達成できるようサポートします。
オンライン講座
製造業、主に購買・調達部門にお勤めの方々に向けた情報を配信しております。
新任の方やベテランの方、管理職を対象とした幅広いコンテンツをご用意しております。
お問い合わせ
コストダウンが利益に直結する術だと理解していても、なかなか前に進めることができない状況。そんな時は、newjiのコストダウン自動化機能で大きく利益貢献しよう!
(Β版非公開)