- お役立ち記事
- How to Improve Product Quality Using the Latest Burr Prevention Technologies
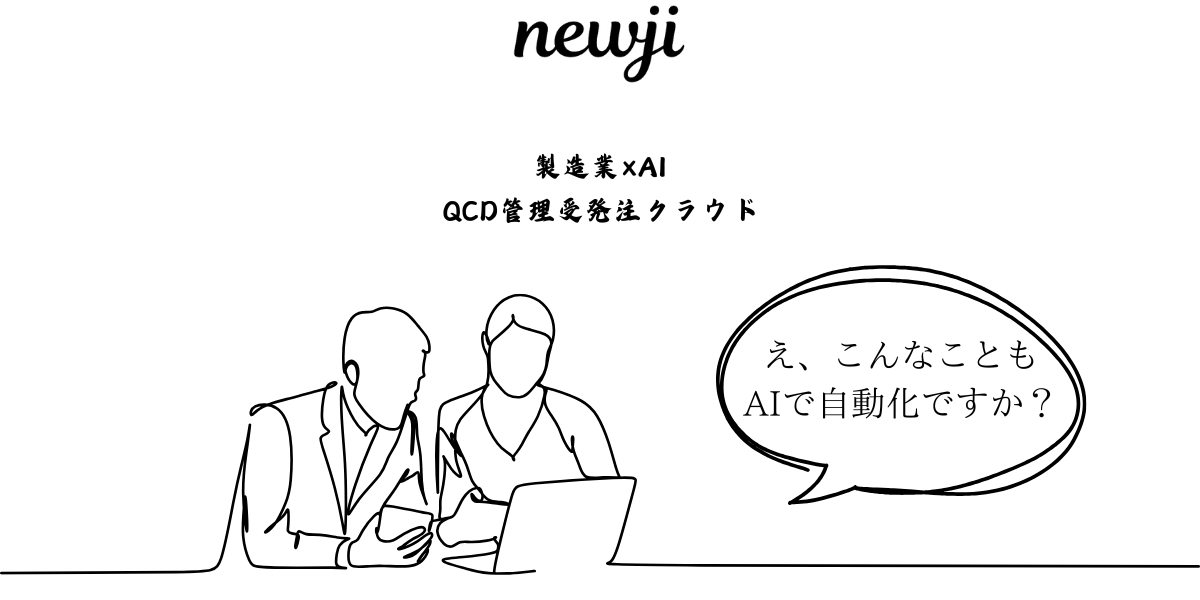
How to Improve Product Quality Using the Latest Burr Prevention Technologies
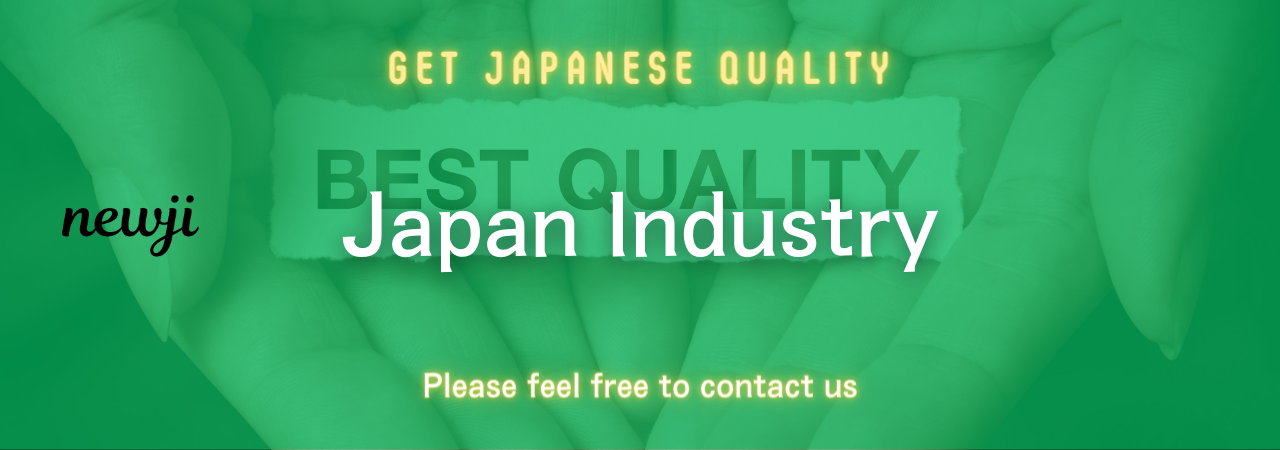
目次
Understanding Burrs and Their Impact on Product Quality
Burrs are unwanted pieces of material that remain attached to a product after the manufacturing process.
They usually result from machining operations like drilling, milling, or grinding.
These tiny edges or protrusions may appear insignificant, but they can significantly affect the product’s overall quality, functionality, and aesthetics.
Burrs can cause assembly problems, lead to increased wear and tear, and even pose safety hazards in some applications.
The presence of burrs often means additional time and costs for manufacturers to remove them and ensure a smooth finish.
With the ever-increasing demand for high-quality products, it becomes crucial for manufacturers to adopt advanced technologies to prevent and handle burr issues effectively.
This not only enhances product quality but also boosts customer satisfaction.
Latest Technologies in Burr Prevention
As industries evolve, so do the technologies used to improve manufacturing processes.
Several innovative techniques and equipment have emerged to prevent burr formation and enhance product quality.
1. High-Precision Machining
High-precision machining is a state-of-the-art approach that involves using advanced machinery to produce parts with tight tolerances and smooth surface finishes.
Modern CNC machines with precision controls can minimize the amount of material being cut, thereby reducing the risk of burr formation.
These machines can be programmed to adjust speeds, feeds, and cutting paths, ensuring optimal conditions to prevent burrs.
2. Laser Cutting
Laser cutting technology has gained popularity for its ability to produce clean and precise cuts.
Unlike traditional mechanical cutting methods, laser cutting involves using a focused beam of light to melt or vaporize material, leading to minimal burr formation.
This technology is particularly advantageous for complex designs or delicate materials where mechanical methods may fall short.
3. Water Jet Cutting
Water jet cutting uses a high-pressure stream of water, often mixed with abrasive particles, to cut through materials.
This method is highly effective at preventing burrs since it does not generate heat that can alter material properties or create imperfections.
Water jet cutting is versatile and can be used on various materials, including metals, plastics, and composites.
4. Cryogenic Treatment
Cryogenic treatment involves cooling materials to extremely low temperatures using liquid nitrogen.
This process alters the microstructure of materials, making them more resistant to stress and wear.
By improving material stability, cryogenic treatment can reduce the likelihood of burrs forming during machining operations.
It is especially useful for materials that are prone to thermal distortion.
5. Vibration-Assisted Machining
Vibration-assisted machining (VAM) integrates ultrasonic vibrations into the cutting process, enhancing precision and reducing cutting forces.
This technique helps to minimize burrs by controlling material deformation and ensuring smoother cuts.
VAM is applicable to multiple machining operations, including turning, milling, and drilling.
Implementing Burr Prevention Strategies in Manufacturing
While advanced technologies play a crucial role in burr prevention, effective implementation of these strategies requires careful planning and execution.
1. Material Selection
The choice of material greatly influences burr formation.
Selecting materials with favorable machining characteristics can reduce the risk of burrs.
Manufacturers should consider factors such as material hardness, ductility, and thermal properties during the design phase.
2. Tool Selection and Maintenance
Using the right tools and maintaining them properly is essential for preventing burrs.
Sharp, high-quality cutting tools reduce friction and improve cutting performance.
Routine maintenance, including the sharpening and replacement of tools, is necessary to ensure consistent results.
3. Process Parameter Optimization
Optimizing machining parameters like feed rate, spindle speed, and depth of cut can significantly impact burr formation.
Manufacturers should experiment with different settings to identify optimal conditions for specific materials and operations.
This may involve using simulation software to predict outcomes and adjust processes accordingly.
4. Quality Control and Inspection
Regular quality control and inspection measures are necessary to detect and address burrs before products reach the market.
Incorporating automated inspection systems with image recognition capabilities can efficiently identify burrs and other defects.
Such systems provide real-time feedback, enabling manufacturers to make necessary adjustments swiftly.
Benefits of Advanced Burr Prevention
Adopting the latest burr prevention technologies offers numerous benefits to manufacturers, including:
– Improved product quality: Enhanced finishes and precision reduce defects and rework.
– Cost savings: Reduced need for manual deburring and associated labor costs.
– Faster production times: Efficient processes lead to shorter lead times and increased throughput.
– Competitive advantage: Higher-quality products strengthen market position and brand reputation.
As industries continue to advance, the emphasis on product quality and efficiency remains paramount.
By leveraging the latest burr prevention technologies, manufacturers can meet customer expectations and stand out in an increasingly competitive market.
資料ダウンロード
QCD調達購買管理クラウド「newji」は、調達購買部門で必要なQCD管理全てを備えた、現場特化型兼クラウド型の今世紀最高の購買管理システムとなります。
ユーザー登録
調達購買業務の効率化だけでなく、システムを導入することで、コスト削減や製品・資材のステータス可視化のほか、属人化していた購買情報の共有化による内部不正防止や統制にも役立ちます。
NEWJI DX
製造業に特化したデジタルトランスフォーメーション(DX)の実現を目指す請負開発型のコンサルティングサービスです。AI、iPaaS、および先端の技術を駆使して、製造プロセスの効率化、業務効率化、チームワーク強化、コスト削減、品質向上を実現します。このサービスは、製造業の課題を深く理解し、それに対する最適なデジタルソリューションを提供することで、企業が持続的な成長とイノベーションを達成できるようサポートします。
オンライン講座
製造業、主に購買・調達部門にお勤めの方々に向けた情報を配信しております。
新任の方やベテランの方、管理職を対象とした幅広いコンテンツをご用意しております。
お問い合わせ
コストダウンが利益に直結する術だと理解していても、なかなか前に進めることができない状況。そんな時は、newjiのコストダウン自動化機能で大きく利益貢献しよう!
(Β版非公開)