- お役立ち記事
- Guide to Setting Injection Pressure and Optimizing Molding Cycles
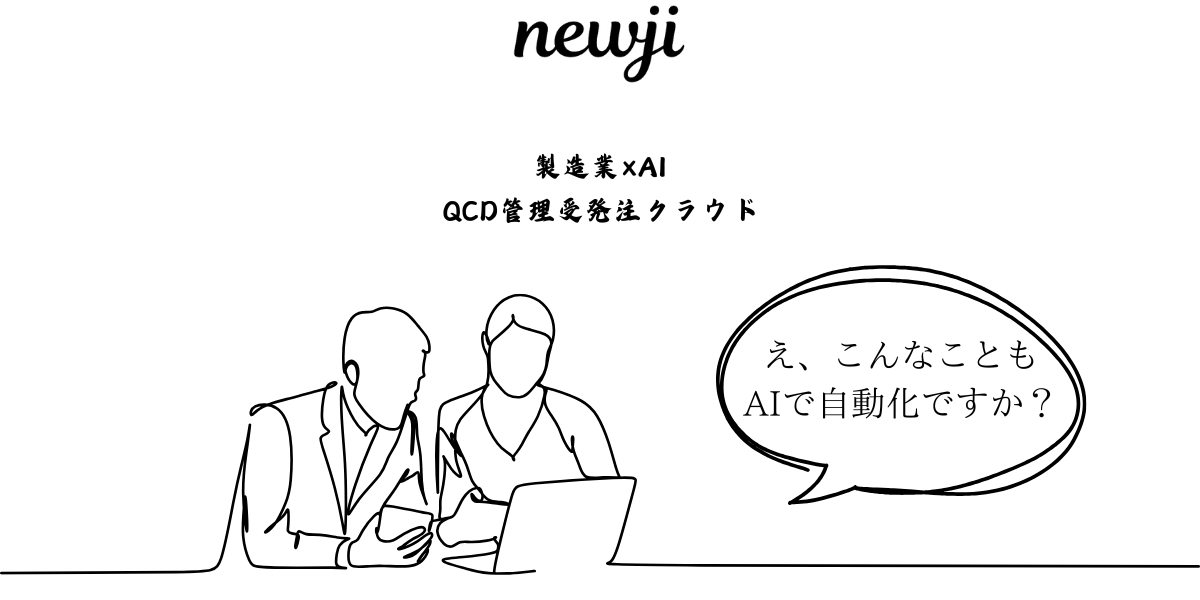
Guide to Setting Injection Pressure and Optimizing Molding Cycles
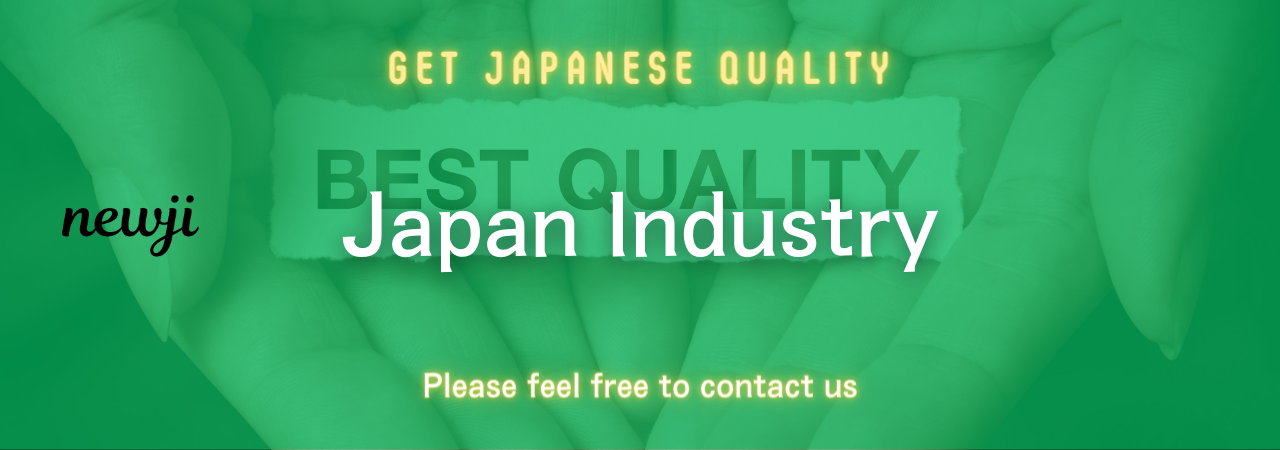
目次
Understanding Injection Pressure
Injection pressure is a crucial parameter in the injection molding process.
It refers to the force that is applied to push molten material into a mold cavity.
This pressure must be optimized to ensure high-quality molds, reduce defects, and improve the efficiency of the production cycle.
A well-set injection pressure helps in filling the mold completely, achieving the desired shape, and ensuring the durability of the final product.
There are two primary types of injection pressures that operators deal with: first-stage (or primary) injection pressure and second-stage (or packing) pressure.
First-stage injection pressure is responsible for filling the mold, while the second-stage pressure packs the material and compensates for material shrinkage.
Factors Affecting Injection Pressure
Several factors determine the appropriate injection pressure in a molding cycle:
– **Material Type**: Different materials have different viscosity and flow characteristics, requiring varied pressures for optimal filling.
– **Part Geometry**: Complex shapes with thin walls or intricate details may require higher pressures to ensure complete fill.
– **Mold Design**: The design, gate size, and venting can affect the pressure needs for a successful cycle.
– **Machine Capabilities**: The molding machine’s maximum pressure output capability is a limiting factor.
– **Temperature Settings**: Both mold and barrel temperatures influence the viscosity of the molten material, impacting the needed injection pressure.
Setting Injection Pressure
Setting the correct injection pressure is essential for minimizing defects such as sink marks, flash, and short shots.
Here’s how you can set the injection pressure for optimal results:
1. Initial Setup
Begin by consulting the material data sheet for the recommended processing parameters of your chosen material.
This will provide a baseline for initial pressure and temperature settings.
2. Start with Low Pressure
Initiate molding with a low first-stage pressure to observe the flow pattern.
Gradually increase it until the mold is fully filled without visible defects.
Keep in mind that each increase will affect the cycle time.
3. Monitor for Defects
Once the mold fills completely, inspect the parts for common defects.
Adjust the injection pressure based on these observations.
If short shots occur, increase the pressure.
If flash appears, reduce the pressure slightly.
4. Optimize Pack and Hold Pressure
After the first-stage pressure fills the mold, set a second-stage pack and hold pressure.
This compensates for shrinkage during solidification.
Monitor the part’s weight and shrinkage until minimal changes occur, indicating optimum pressure settings.
Optimizing Molding Cycles
Optimizing molding cycles is not only about setting the correct injection pressure.
It involves a holistic approach toward time, quality, and cost efficiency.
1. Cycle Time Reduction
Reducing the cycle time increases productivity and lowers production costs.
However, balance is key; reducing time should not compromise quality.
– Analyze each phase of the cycle, such as fill time, cooling time, and ejection time, for potential reductions.
– Ensure mold cooling systems are efficient, possibly through the use of water chillers or advanced cooling channels.
2. Quality Control Measures
Implement consistent quality checks to identify defects early in the production cycle.
Utilize automated inspection tools like cameras or sensors to detect surface and structural anomalies quickly.
Keeping rigorous quality standards helps in minimizing waste and rework.
3. Machine Maintenance
Regular maintenance of molding machines prevents unexpected downtimes and ensures consistent pressure and performance.
Inspect hydraulic systems, mold-clamping systems, and barrels regularly.
Calibration of sensors and controllers must also be done routinely.
4. Training and Skill Development
Invest in continuous training for machine operators and technicians to recognize pressure settings and optimal cycle conditions.
Knowledgeable staff can often preemptively adjust settings to accommodate minor variations in materials or environments.
Conclusion
Setting the correct injection pressure and optimizing molding cycles are fundamental to the efficiency and quality of injection molding processes.
By understanding material characteristics, and mold design, and monitoring production closely, operators can achieve high-quality outcomes with minimal waste.
Regular maintenance and training further enhance these efforts, ensuring that the production process is as efficient and effective as possible.
資料ダウンロード
QCD調達購買管理クラウド「newji」は、調達購買部門で必要なQCD管理全てを備えた、現場特化型兼クラウド型の今世紀最高の購買管理システムとなります。
ユーザー登録
調達購買業務の効率化だけでなく、システムを導入することで、コスト削減や製品・資材のステータス可視化のほか、属人化していた購買情報の共有化による内部不正防止や統制にも役立ちます。
NEWJI DX
製造業に特化したデジタルトランスフォーメーション(DX)の実現を目指す請負開発型のコンサルティングサービスです。AI、iPaaS、および先端の技術を駆使して、製造プロセスの効率化、業務効率化、チームワーク強化、コスト削減、品質向上を実現します。このサービスは、製造業の課題を深く理解し、それに対する最適なデジタルソリューションを提供することで、企業が持続的な成長とイノベーションを達成できるようサポートします。
オンライン講座
製造業、主に購買・調達部門にお勤めの方々に向けた情報を配信しております。
新任の方やベテランの方、管理職を対象とした幅広いコンテンツをご用意しております。
お問い合わせ
コストダウンが利益に直結する術だと理解していても、なかなか前に進めることができない状況。そんな時は、newjiのコストダウン自動化機能で大きく利益貢献しよう!
(Β版非公開)