- お役立ち記事
- Revolutionizing Manufacturing: The Future of Moldless Casting in Japan
Revolutionizing Manufacturing: The Future of Moldless Casting in Japan
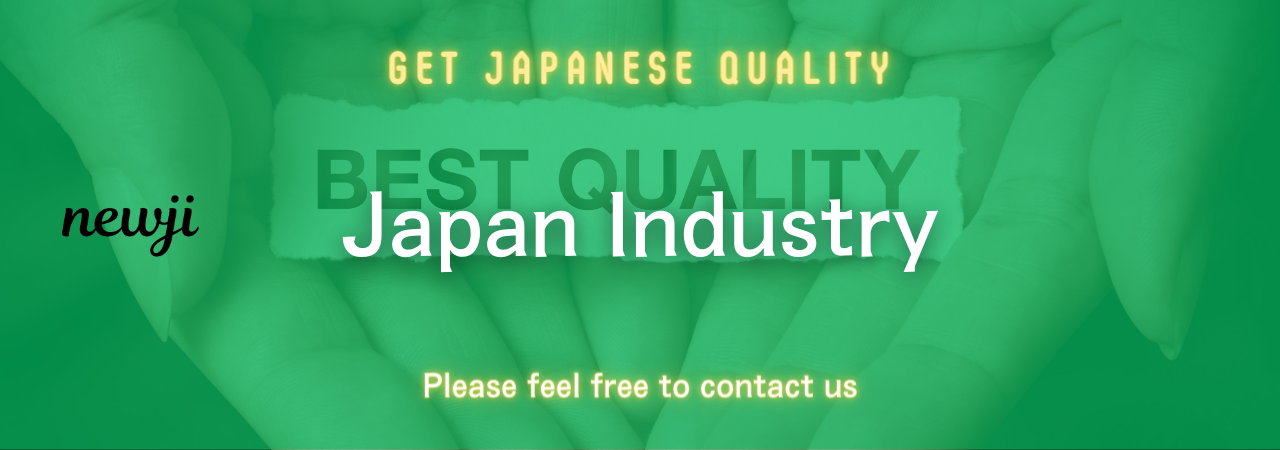
目次
Introduction to Moldless Casting
Moldless casting is an innovative manufacturing technique that eliminates the need for traditional molds. This method offers significant advantages in terms of flexibility and cost-efficiency. In Japan, moldless casting is gaining traction, revolutionizing the manufacturing landscape.
The Evolution of Moldless Casting in Japan
Japan has long been a leader in manufacturing technology. The adoption of moldless casting represents the latest advancement in this tradition. This section explores the historical context and the factors driving the shift towards moldless techniques.
Historical Context
Japan’s manufacturing sector has consistently prioritized precision and efficiency. The transition from mold-based to moldless casting aligns with these core values. This evolution reflects the industry’s commitment to innovation.
Driving Factors
Several factors contribute to the rise of moldless casting in Japan. These include the need for rapid prototyping, the demand for customized products, and advancements in materials science. Additionally, economic considerations such as reducing production costs play a crucial role.
Advantages of Moldless Casting
Moldless casting offers numerous benefits over traditional methods. This section delves into the key advantages, highlighting why Japanese manufacturers are embracing this technology.
Flexibility in Design
One of the primary benefits of moldless casting is the enhanced flexibility it provides in product design. Manufacturers can easily modify designs without the constraints of fixed molds. This adaptability is essential for industries that require frequent design iterations.
Cost Efficiency
Eliminating the need for molds significantly reduces initial setup costs. Additionally, moldless casting minimizes material waste, leading to further cost savings. These financial benefits make it an attractive option for businesses aiming to optimize their budgets.
Speed of Production
Moldless casting accelerates the production process. Without the time-consuming steps of mold creation and maintenance, manufacturers can achieve faster turnaround times. This speed is crucial in competitive markets where time-to-market is a key differentiator.
Material Versatility
This technique supports a wide range of materials, including metals, plastics, and composites. The ability to work with diverse materials expands the scope of applications for moldless casting, making it suitable for various industries.
Challenges and Disadvantages
Despite its advantages, moldless casting presents certain challenges. Understanding these drawbacks is essential for manufacturers considering this technology.
Initial Investment in Technology
Implementing moldless casting requires investment in advanced machinery and technology. While the long-term savings are significant, the upfront costs can be a barrier for some businesses.
Skill Requirements
Operating moldless casting equipment demands specialized skills. Manufacturers need to train their workforce or hire experts to effectively utilize this technology. This requirement can impact the overall implementation timeline.
Quality Control
Maintaining consistent quality can be more challenging without traditional molds. Manufacturers must establish robust quality control measures to ensure that products meet the required standards.
Supplier Negotiation Techniques
Effective negotiation with suppliers is crucial for successful procurement of moldless casting technology. This section outlines strategies to optimize supplier relationships and secure favorable terms.
Building Strong Relationships
Developing long-term relationships with suppliers fosters trust and collaboration. This partnership approach can lead to better pricing, priority in supply chains, and access to the latest technologies.
Leveraging Market Knowledge
Understanding market conditions and supplier capabilities empowers buyers during negotiations. Staying informed about industry trends and competitor offerings provides leverage in discussions.
Negotiating Flexible Contracts
Flexibility in contracts allows for adjustments based on changing needs. Negotiating terms that accommodate scaling production or integrating new technologies can enhance overall procurement effectiveness.
Market Conditions and Trends
Analyzing current market conditions and future trends helps manufacturers make informed decisions about adopting moldless casting.
Demand for Customization
The market’s increasing demand for customized products drives the adoption of moldless casting. This trend is particularly prominent in sectors such as automotive, electronics, and consumer goods.
Technological Advancements
Continuous advancements in manufacturing technology support the evolution of moldless casting. Innovations in 3D printing, additive manufacturing, and materials science are key contributors.
Global Competition
Japanese manufacturers face intense global competition. Adopting moldless casting can provide a competitive edge by enhancing product quality, reducing costs, and accelerating production timelines.
Best Practices in Implementing Moldless Casting
Successful implementation of moldless casting requires adherence to best practices. This section outlines key strategies to maximize the benefits of this technology.
Comprehensive Training Programs
Investing in training ensures that the workforce is proficient in operating moldless casting equipment. Comprehensive training programs enhance efficiency and reduce the likelihood of errors.
Integration with Existing Systems
Seamlessly integrating moldless casting with current manufacturing processes minimizes disruption. This integration facilitates smoother transitions and optimizes overall production workflows.
Continuous Improvement
Adopting a mindset of continuous improvement promotes ongoing optimization of moldless casting operations. Regularly assessing performance and incorporating feedback drives sustained success.
Case Studies: Success Stories in Japan
Examining real-world examples of moldless casting implementation in Japan provides valuable insights into its practical applications and benefits.
Automotive Industry
Japanese automotive manufacturers have leveraged moldless casting to produce lightweight and complex components. This approach has led to improvements in vehicle performance and fuel efficiency.
Electronics Sector
In the electronics industry, moldless casting has enabled the creation of intricate parts for devices such as smartphones and laptops. The flexibility of this method supports rapid innovation and design changes.
Consumer Goods
Consumer goods companies in Japan have adopted moldless casting to offer customized products tailored to individual preferences. This capability enhances customer satisfaction and drives brand loyalty.
The Future Outlook
The future of moldless casting in Japan looks promising, with continued advancements and increasing adoption across various industries. This section explores potential developments and the long-term impact on the manufacturing sector.
Integration with Industry 4.0
Moldless casting is poised to integrate seamlessly with Industry 4.0 initiatives. The combination of advanced manufacturing techniques and smart technologies will further enhance efficiency and innovation.
Sustainability Considerations
Sustainability is becoming a critical focus in manufacturing. Moldless casting contributes to more sustainable practices by reducing material waste and optimizing energy usage.
Global Expansion
As Japanese expertise in moldless casting grows, there is potential for global expansion. Collaborations and exports can position Japan as a leader in this advanced manufacturing technology worldwide.
Conclusion
Moldless casting is transforming the manufacturing landscape in Japan, offering enhanced flexibility, cost efficiency, and speed. While challenges exist, the benefits and ongoing advancements make it a pivotal technology for the future. By adopting best practices and leveraging strategic supplier relationships, Japanese manufacturers can continue to lead in innovation and competitiveness.
資料ダウンロード
QCD調達購買管理クラウド「newji」は、調達購買部門で必要なQCD管理全てを備えた、現場特化型兼クラウド型の今世紀最高の購買管理システムとなります。
ユーザー登録
調達購買業務の効率化だけでなく、システムを導入することで、コスト削減や製品・資材のステータス可視化のほか、属人化していた購買情報の共有化による内部不正防止や統制にも役立ちます。
NEWJI DX
製造業に特化したデジタルトランスフォーメーション(DX)の実現を目指す請負開発型のコンサルティングサービスです。AI、iPaaS、および先端の技術を駆使して、製造プロセスの効率化、業務効率化、チームワーク強化、コスト削減、品質向上を実現します。このサービスは、製造業の課題を深く理解し、それに対する最適なデジタルソリューションを提供することで、企業が持続的な成長とイノベーションを達成できるようサポートします。
オンライン講座
製造業、主に購買・調達部門にお勤めの方々に向けた情報を配信しております。
新任の方やベテランの方、管理職を対象とした幅広いコンテンツをご用意しております。
お問い合わせ
コストダウンが利益に直結する術だと理解していても、なかなか前に進めることができない状況。そんな時は、newjiのコストダウン自動化機能で大きく利益貢献しよう!
(Β版非公開)