- お役立ち記事
- Enhancing Occupational Health and Safety in Japanese Manufacturing: A Comprehensive Guide
Enhancing Occupational Health and Safety in Japanese Manufacturing: A Comprehensive Guide
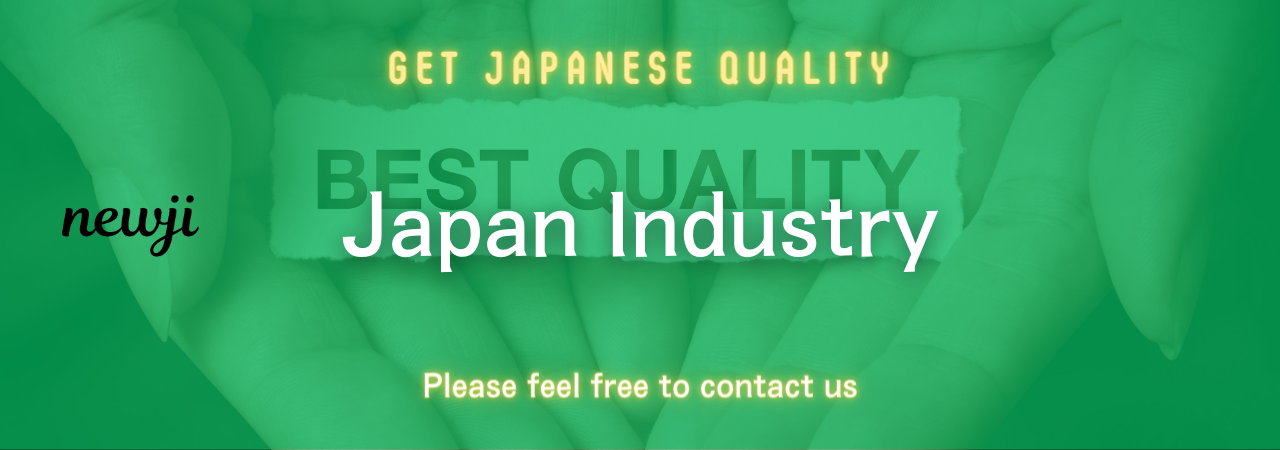
目次
Introduction to Occupational Health and Safety in Japanese Manufacturing
Ensuring occupational health and safety (OHS) is paramount in the manufacturing sector.
Japanese manufacturing companies have long been recognized for their commitment to high standards of workplace safety.
This comprehensive guide explores the strategies and practices that enhance OHS in Japanese manufacturing settings.
By understanding these methods, international procurement and purchasing professionals can better collaborate with Japanese suppliers to achieve mutual safety and efficiency goals.
The Importance of Occupational Health and Safety in Manufacturing
Occupational health and safety play a critical role in the manufacturing industry.
A safe workplace reduces accidents, minimizes downtime, and increases overall productivity.
Moreover, it fosters a positive work environment, which can lead to higher employee satisfaction and retention.
In the context of Japanese manufacturing, OHS is deeply ingrained in the corporate culture, reflecting the country’s emphasis on meticulousness and continuous improvement.
The Impact of OHS on Productivity and Quality
A focus on OHS directly correlates with enhanced productivity.
When employees feel safe, they are more likely to perform efficiently and with greater attention to detail.
This attentiveness leads to higher quality products, reducing defects and waste.
Japanese manufacturers leverage OHS practices not only to protect their workforce but also to streamline production processes.
Regulatory Compliance and Corporate Responsibility
Compliance with national and international OHS regulations is non-negotiable.
Japanese manufacturers adhere to stringent safety standards set by the Ministry of Health, Labour and Welfare.
Beyond compliance, there is a strong sense of corporate responsibility to ensure the well-being of all employees.
This dual focus on regulation and ethics underscores the comprehensive approach Japanese companies take toward OHS.
Key Components of Effective OHS Programs in Japanese Manufacturing
Japanese manufacturing firms implement multifaceted OHS programs that address various aspects of workplace safety.
These programs are designed to be proactive, continuously evolving to meet emerging challenges and incorporate best practices.
Risk Assessment and Management
A cornerstone of OHS is the identification and mitigation of workplace hazards.
Japanese companies conduct regular risk assessments to identify potential safety issues.
This proactive approach allows for timely interventions, preventing accidents before they occur.
Risk management strategies include machine safety protocols, ergonomic assessments, and environmental controls.
Employee Training and Education
Continuous training is essential for maintaining high safety standards.
Japanese manufacturers invest in comprehensive training programs that educate employees about safety procedures and best practices.
These programs often include hands-on training, simulations, and regular refresher courses to ensure that safety knowledge remains current.
Safety Culture and Leadership
A strong safety culture is cultivated through leadership commitment and employee involvement.
In Japanese companies, leadership actively promotes OHS by setting clear expectations and leading by example.
Employees are encouraged to take ownership of their safety and that of their colleagues, fostering a collective responsibility for maintaining a safe workplace.
Advantages of Implementing Robust OHS Practices in Japanese Manufacturing
Adopting comprehensive OHS practices yields numerous benefits for Japanese manufacturers and their international partners.
Enhanced Reputation and Competitive Advantage
Companies known for their commitment to OHS gain a competitive edge in the global market.
A strong safety record enhances a company’s reputation, making it a preferred partner for international buyers concerned with ethical sourcing and corporate responsibility.
Cost Savings and Operational Efficiency
Effective OHS programs can lead to significant cost savings by reducing workplace injuries and associated expenses.
Lower accident rates decrease medical costs, workers’ compensation claims, and legal fees.
Additionally, minimized downtime from accidents ensures smoother operations and higher productivity.
Employee Morale and Retention
A safe work environment positively impacts employee morale.
When workers feel valued and protected, job satisfaction increases, leading to higher retention rates.
This stability reduces turnover costs and fosters a more experienced and skilled workforce.
Challenges and Considerations in Enhancing OHS
While the benefits of robust OHS practices are clear, implementing them in Japanese manufacturing requires addressing several challenges.
Cultural Considerations
Japanese workplace culture emphasizes harmony and group cohesion, which can both aid and complicate OHS initiatives.
Encouraging individual accountability without disrupting the collective spirit requires a delicate balance.
Cultural sensitivity is essential when introducing new safety protocols to ensure they are accepted and embraced by all employees.
Integration with Global Standards
International procurement often involves aligning OHS practices with diverse global standards.
Japanese manufacturers must harmonize their existing practices with those of their international partners, which may have different regulatory requirements and safety expectations.
Technological Integration
Incorporating advanced technologies to enhance OHS can be challenging.
Japanese manufacturers must invest in modern safety equipment, automation, and data analytics while ensuring that these technologies integrate seamlessly with existing production processes.
Best Practices for Enhancing OHS in Japanese Manufacturing
To overcome challenges and maximize the benefits of OHS, Japanese manufacturers can adopt several best practices.
Continuous Improvement and Kaizen
Embracing the Kaizen philosophy of continuous improvement ensures that OHS practices evolve over time.
Regularly reviewing and refining safety procedures helps address new risks and incorporate the latest safety innovations.
Employee Engagement and Empowerment
Involving employees in safety decision-making fosters a sense of ownership and accountability.
Japanese manufacturers encourage worker participation through safety committees, suggestion programs, and regular feedback sessions, ensuring that safety initiatives are well-informed and widely supported.
Leveraging Technology for Safety Enhancements
Adopting cutting-edge technologies can significantly improve workplace safety.
Examples include automation to handle hazardous tasks, wearable devices for monitoring employee health, and data analytics to predict and prevent potential safety incidents.
Establishing Clear Communication Channels
Effective communication is vital for OHS success.
Japanese companies establish clear communication channels for reporting hazards, sharing safety information, and coordinating emergency responses.
Regular safety meetings and updates ensure that all employees are informed and aware of current safety practices.
Supplier Negotiation Techniques for OHS Compliance
When collaborating with Japanese suppliers, ensuring OHS compliance is essential.
Effective negotiation techniques can help achieve mutual safety standards and expectations.
Setting Clear OHS Expectations
Begin negotiations by clearly outlining your OHS requirements and expectations.
Specify the safety standards and certifications that suppliers must adhere to, ensuring alignment from the outset.
Evaluating Supplier OHS Performance
Assess the supplier’s OHS performance through audits, inspections, and review of safety records.
Use this information to make informed decisions about partnerships and to identify areas for improvement.
Incorporating OHS Clauses in Contracts
Include specific OHS clauses in contracts to formalize safety commitments.
These clauses should detail the responsibilities of each party, reporting requirements, and consequences for non-compliance.
Collaborative Safety Initiatives
Foster a collaborative approach to OHS by working together on safety initiatives.
Share best practices, provide joint training sessions, and develop shared safety goals to enhance overall safety performance.
Market Conditions Affecting OHS in Japanese Manufacturing
Understanding the market conditions that impact OHS is crucial for effective procurement and purchasing strategies.
Economic Factors
Economic fluctuations can influence the prioritization of OHS investments.
During economic downturns, companies may face budget constraints, potentially impacting their ability to invest in safety enhancements.
Conversely, economic growth can provide opportunities for expanding and upgrading OHS programs.
Technological Advancements
Rapid technological advancements present both opportunities and challenges for OHS.
While new technologies can improve safety, they also require ongoing training and adaptation to ensure they are used effectively and safely.
Globalization and Supply Chain Complexity
Globalization increases supply chain complexity, introducing diverse OHS standards and practices.
Navigating these differences requires a deep understanding of international safety norms and the ability to harmonize practices across borders.
Labor Market Dynamics
The availability of skilled labor affects OHS implementation.
A shortage of trained workers may necessitate increased investment in training programs to maintain high safety standards.
Conclusion: The Future of Occupational Health and Safety in Japanese Manufacturing
Occupational health and safety will continue to be a critical focus in Japanese manufacturing.
As the industry evolves, so too will the strategies and practices that ensure safe and healthy workplaces.
By embracing continuous improvement, leveraging technology, and fostering collaborative partnerships, Japanese manufacturers can maintain their reputation for excellence in OHS.
For international procurement and purchasing professionals, understanding and aligning with these OHS practices is essential for successful and sustainable collaborations.
資料ダウンロード
QCD調達購買管理クラウド「newji」は、調達購買部門で必要なQCD管理全てを備えた、現場特化型兼クラウド型の今世紀最高の購買管理システムとなります。
ユーザー登録
調達購買業務の効率化だけでなく、システムを導入することで、コスト削減や製品・資材のステータス可視化のほか、属人化していた購買情報の共有化による内部不正防止や統制にも役立ちます。
NEWJI DX
製造業に特化したデジタルトランスフォーメーション(DX)の実現を目指す請負開発型のコンサルティングサービスです。AI、iPaaS、および先端の技術を駆使して、製造プロセスの効率化、業務効率化、チームワーク強化、コスト削減、品質向上を実現します。このサービスは、製造業の課題を深く理解し、それに対する最適なデジタルソリューションを提供することで、企業が持続的な成長とイノベーションを達成できるようサポートします。
オンライン講座
製造業、主に購買・調達部門にお勤めの方々に向けた情報を配信しております。
新任の方やベテランの方、管理職を対象とした幅広いコンテンツをご用意しております。
お問い合わせ
コストダウンが利益に直結する術だと理解していても、なかなか前に進めることができない状況。そんな時は、newjiのコストダウン自動化機能で大きく利益貢献しよう!
(Β版非公開)