- お役立ち記事
- Revolutionizing Japanese Manufacturing: Unleashing Potential with Sol-Gel Processing OEM Solutions
Revolutionizing Japanese Manufacturing: Unleashing Potential with Sol-Gel Processing OEM Solutions
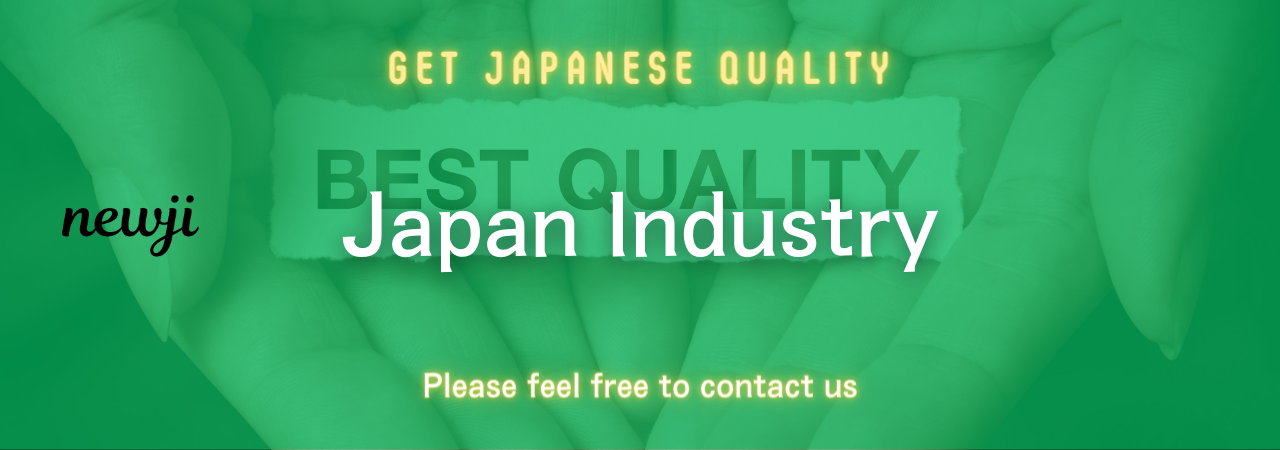
目次
Introduction to Sol-Gel Processing in Japanese Manufacturing
Japanese manufacturing has long been synonymous with precision, innovation, and quality. Among the various technological advancements contributing to this reputation, sol-gel processing stands out as a transformative technique. Sol-gel processing involves the transition of a system from a liquid “sol” into a solid “gel” phase, enabling the creation of materials with unique properties tailored for specific applications. This method is pivotal in industries ranging from electronics to aerospace, offering flexibility and high-performance outcomes. Leveraging Original Equipment Manufacturer (OEM) solutions in sol-gel processing allows businesses to harness the expertise of Japanese suppliers, driving efficiency and fostering innovation in manufacturing processes.
The Role of OEM Solutions in Japanese Manufacturing
OEM solutions play a crucial role in the landscape of Japanese manufacturing. By partnering with OEM providers, companies can access specialized technologies and manufacturing capabilities without the need for extensive in-house development. In the context of sol-gel processing, OEM solutions offer several advantages:
Access to Expertise
Japanese OEMs are renowned for their deep technical knowledge and expertise in sol-gel technology. Collaborating with these suppliers ensures that manufacturers benefit from cutting-edge advancements and best practices developed through years of research and development.
Cost Efficiency
Outsourcing sol-gel processing to OEMs can lead to significant cost savings. Manufacturers can reduce capital expenditures on equipment and facilities while leveraging the OEM’s established production capabilities and economies of scale.
Focus on Core Competencies
By utilizing OEM solutions, companies can concentrate on their core competencies, such as product design and marketing, leaving the complexities of sol-gel processing to specialized manufacturers. This division of labor enhances overall business efficiency and competitiveness.
Procurement and Purchasing Strategies for Sol-Gel Processing
Effective procurement and purchasing strategies are essential for maximizing the benefits of sol-gel processing OEM solutions. These strategies encompass supplier selection, negotiation, contract management, and ongoing supplier relationship management.
Supplier Selection
Selecting the right OEM partner is critical. Key considerations include the supplier’s technical capabilities, production capacity, quality standards, and track record in sol-gel processing. Conducting thorough due diligence, including site visits and reference checks, can help identify reliable partners aligned with your manufacturing goals.
Negotiation Techniques
Negotiating with Japanese suppliers requires an understanding of cultural nuances and effective communication strategies. Building trust and demonstrating respect are fundamental. Techniques such as focusing on long-term partnerships, being transparent about expectations, and engaging in collaborative problem-solving can lead to favorable negotiation outcomes.
Contract Management
Establishing clear and comprehensive contracts is vital to ensure mutual understanding and adherence to agreed terms. Contracts should detail specifications, delivery schedules, quality standards, pricing, and mechanisms for resolving disputes. Regular reviews and updates to contracts can accommodate changes in market conditions and business needs.
Advantages and Disadvantages of Sol-Gel Processing OEM Solutions
While sol-gel processing OEM solutions offer numerous benefits, they also present certain challenges. Understanding these advantages and disadvantages is essential for informed decision-making.
Advantages
- High-Quality Output: Japanese OEMs are committed to maintaining stringent quality standards, ensuring that the sol-gel processed materials meet or exceed industry requirements.
- Innovation and R&D: OEM partners often invest heavily in research and development, providing access to the latest technological advancements and innovative solutions.
- Scalability: OEMs can scale production to meet varying demand levels, offering flexibility to manufacturers as their business grows.
- Reduced Time-to-Market: Leveraging OEM capabilities can accelerate the production process, enabling faster product development and market entry.
Disadvantages
- Dependence on Suppliers: Relying heavily on OEM partners may lead to dependency, potentially impacting supply chain resilience.
- Communication Barriers: Language and cultural differences can pose challenges in communication, affecting collaboration and project management.
- Intellectual Property Risks: Sharing sensitive information with OEMs requires robust safeguards to protect intellectual property and prevent misuse.
- Cost Considerations: While OEM solutions can be cost-effective, hidden costs such as logistics, quality control, and potential delays must be accounted for.
Market Conditions and Trends in Sol-Gel Processing
The sol-gel processing market is influenced by various factors, including technological advancements, industry demand, and economic conditions. Understanding these market conditions and trends is crucial for strategic procurement and purchasing decisions.
Technological Advancements
Continuous innovation in sol-gel processing techniques enhances material properties and broadens application possibilities. Trends such as nanotechnology integration, multi-layer coatings, and eco-friendly processing methods are shaping the future of sol-gel applications.
Industry Demand
Sectors like electronics, aerospace, automotive, and pharmaceuticals drive the demand for sol-gel processed materials. The increasing need for lightweight, durable, and high-performance materials fuels the growth of the sol-gel market.
Economic Factors
Global economic conditions impact manufacturing investments and consumer demand. Fluctuations in raw material prices, trade policies, and economic stability of key markets can influence the sol-gel processing industry dynamics.
Sustainability and Environmental Regulations
Growing emphasis on sustainability and stringent environmental regulations are encouraging the adoption of eco-friendly sol-gel processing methods. Manufacturers are increasingly seeking OEM partners that prioritize green technologies and sustainable practices.
Best Practices in Managing Japanese Suppliers
Effective management of Japanese suppliers is essential for successful procurement and purchasing operations. Adhering to best practices fosters strong partnerships, ensures quality, and drives mutual growth.
Building Strong Relationships
Cultivating trust and mutual respect lays the foundation for successful collaborations with Japanese OEMs. Regular communication, collaborative problem-solving, and cultural sensitivity are key to building enduring relationships.
Ensuring Quality Control
Implementing robust quality control measures is critical to maintaining the integrity of sol-gel processed materials. Establishing clear quality standards, conducting regular audits, and utilizing joint quality management systems can enhance product reliability and consistency.
Effective Communication
Clear and consistent communication minimizes misunderstandings and aligns expectations. Utilizing bilingual teams, leveraging translation services, and adopting standardized communication protocols can bridge language gaps and facilitate smooth interactions.
Joint Continuous Improvement
Collaborating on continuous improvement initiatives, such as Lean Manufacturing and Six Sigma, can drive operational excellence. Joint efforts to optimize processes, reduce waste, and enhance efficiency benefit both manufacturers and OEM partners.
Enhancing Factory Efficiency with Sol-Gel Processing
Integrating sol-gel processing into manufacturing operations can significantly enhance factory efficiency. This integration involves optimizing production workflows, implementing automation, and leveraging data analytics to streamline operations.
Optimizing Production Workflows
Designing efficient production workflows minimizes bottlenecks and reduces cycle times. Sol-gel processing can be seamlessly integrated into existing manufacturing processes through careful planning and process mapping, ensuring smooth transitions and minimal disruptions.
Implementing Automation
Automation in sol-gel processing enhances precision, consistency, and scalability. Automated systems for mixing, coating, drying, and curing can reduce manual intervention, lower error rates, and increase production throughput.
Leveraging Data Analytics
Utilizing data analytics in sol-gel processing enables real-time monitoring and data-driven decision-making. Analyzing process data helps identify trends, predict maintenance needs, and optimize parameters for improved performance and reduced downtime.
Future Outlook and Potential of Sol-Gel Processing OEM Solutions
The future of sol-gel processing OEM solutions in Japanese manufacturing is promising, driven by continuous innovation and evolving market demands. Anticipated developments include advancements in material science, increased adoption of sustainable practices, and the integration of smart technologies.
Advancements in Material Science
Ongoing research in material science is expected to yield new sol-gel formulations with enhanced properties, such as increased durability, flexibility, and multifunctionality. These advancements will open up new application areas and improve existing products.
Sustainable Sol-Gel Processing
Sustainability will continue to be a significant focus, with OEM partners developing eco-friendly sol-gel processes that minimize environmental impact. This includes the use of non-toxic precursors, energy-efficient methods, and recycling of waste materials.
Integration of Smart Technologies
The incorporation of smart technologies, such as the Internet of Things (IoT) and artificial intelligence (AI), into sol-gel processing will drive further efficiency and innovation. Smart systems can optimize processing parameters, predict maintenance needs, and enhance product quality.
Global Collaboration and Expansion
Japanese OEMs are likely to expand their global presence, fostering international collaborations and partnerships. This global expansion will provide manufacturers worldwide with greater access to advanced sol-gel processing solutions and expertise.
Conclusion
Revolutionizing Japanese manufacturing through sol-gel processing OEM solutions presents a significant opportunity for businesses seeking to enhance their manufacturing capabilities. By leveraging the expertise, quality, and innovation of Japanese OEM partners, manufacturers can achieve superior product outcomes, increase operational efficiency, and stay competitive in a dynamic market. Effective procurement and purchasing strategies, coupled with best practices in supplier management, are essential for maximizing the benefits of sol-gel processing. As the industry continues to evolve, embracing these OEM solutions will unlock new potentials and drive the future of manufacturing excellence.
資料ダウンロード
QCD調達購買管理クラウド「newji」は、調達購買部門で必要なQCD管理全てを備えた、現場特化型兼クラウド型の今世紀最高の購買管理システムとなります。
ユーザー登録
調達購買業務の効率化だけでなく、システムを導入することで、コスト削減や製品・資材のステータス可視化のほか、属人化していた購買情報の共有化による内部不正防止や統制にも役立ちます。
NEWJI DX
製造業に特化したデジタルトランスフォーメーション(DX)の実現を目指す請負開発型のコンサルティングサービスです。AI、iPaaS、および先端の技術を駆使して、製造プロセスの効率化、業務効率化、チームワーク強化、コスト削減、品質向上を実現します。このサービスは、製造業の課題を深く理解し、それに対する最適なデジタルソリューションを提供することで、企業が持続的な成長とイノベーションを達成できるようサポートします。
オンライン講座
製造業、主に購買・調達部門にお勤めの方々に向けた情報を配信しております。
新任の方やベテランの方、管理職を対象とした幅広いコンテンツをご用意しております。
お問い合わせ
コストダウンが利益に直結する術だと理解していても、なかなか前に進めることができない状況。そんな時は、newjiのコストダウン自動化機能で大きく利益貢献しよう!
(Β版非公開)