- お役立ち記事
- Revolutionizing Efficiency: The Art of the Production Line in Japanese Manufacturing
Revolutionizing Efficiency: The Art of the Production Line in Japanese Manufacturing
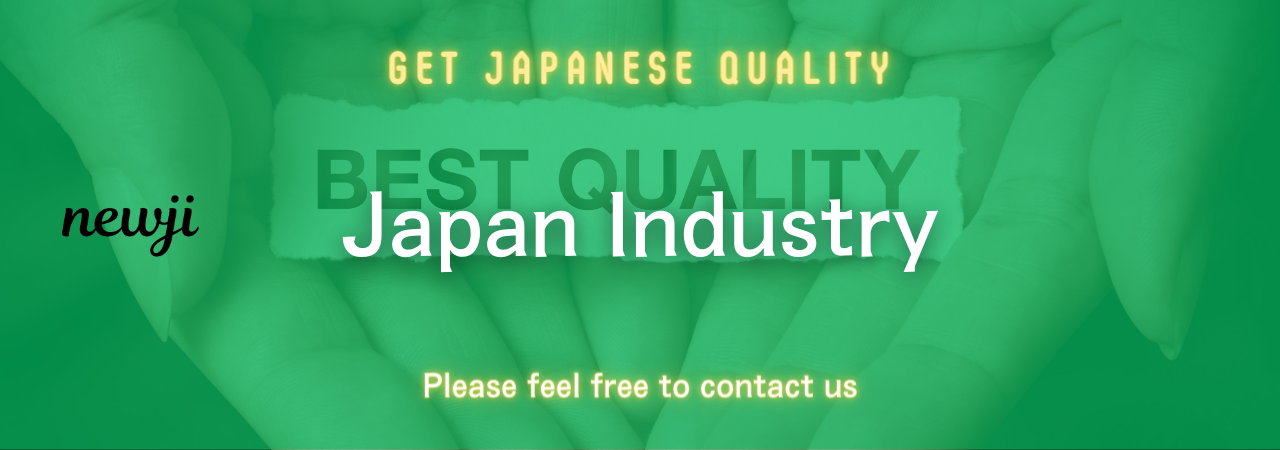
目次
Introduction to Japanese Manufacturing Efficiency
Japanese manufacturing is renowned worldwide for its exceptional efficiency and quality.
This reputation is not accidental but the result of meticulous practices and philosophies.
Understanding the art of the production line in Japanese manufacturing offers valuable insights into achieving operational excellence.
This article explores the intricacies of Japanese procurement and purchasing, supplier negotiation techniques, market conditions, and best practices that contribute to their manufacturing prowess.
By delving into these aspects, international companies can harness the benefits of Japanese manufacturing to revolutionize their own production processes.
The Foundation of Japanese Manufacturing Efficiency
Japanese manufacturing efficiency is built upon principles that prioritize continuous improvement and waste elimination.
The Just-In-Time (JIT) system is a cornerstone of this approach, ensuring that materials arrive exactly when needed, reducing inventory costs.
Kanban, a scheduling system, complements JIT by managing workflow and production processes efficiently.
These systems collectively minimize waste and enhance productivity, laying the groundwork for a highly efficient production line.
Lean Manufacturing Principles
Lean manufacturing focuses on value creation with minimal waste.
By streamlining processes and eliminating non-essential activities, Japanese manufacturers achieve higher efficiency and quality.
This approach not only reduces costs but also fosters a culture of continuous improvement among employees.
Implementing lean principles can lead to significant advancements in production line efficiency and product excellence.
Kaizen: The Continuous Improvement Culture
Kaizen, meaning “change for better,” is a fundamental philosophy in Japanese manufacturing.
It encourages all employees to contribute ideas for improvement, fostering an environment of collective responsibility.
Regularly evaluating and refining processes ensures that the production line remains adaptable and efficient.
The Kaizen mindset leads to incremental advancements that accumulate, resulting in substantial overall improvements.
Procurement and Purchasing in Japanese Manufacturing
Effective procurement and purchasing are essential for maintaining the efficiency and quality of Japanese production lines.
Japanese companies adopt strategic approaches to sourcing materials and managing supplier relationships, which are critical to their manufacturing success.
Strategic Sourcing and Supplier Selection
Japanese manufacturers prioritize strategic sourcing, selecting suppliers based on reliability, quality, and long-term partnerships.
This careful selection process ensures a consistent supply of high-quality materials essential for maintaining production standards.
By fostering strong relationships with trusted suppliers, Japanese companies can mitigate risks and enhance supply chain resilience.
Supplier Relationship Management
Building and maintaining strong supplier relationships is a hallmark of Japanese procurement practices.
Regular communication, mutual respect, and shared goals underpin these relationships, creating a collaborative environment.
This partnership approach facilitates problem-solving and innovation, enabling suppliers to align closely with the manufacturer’s needs and expectations.
Cost Management and Value Optimization
Japanese manufacturers focus on cost management without compromising quality.
Through bulk purchasing, long-term contracts, and negotiation strategies, they achieve cost efficiencies.
Moreover, by working closely with suppliers to optimize value, they ensure that costs are controlled while maintaining the highest standards of quality and performance.
Advantages of Japanese Production Line Techniques
Japanese production line techniques offer numerous advantages that contribute to their renowned manufacturing efficiency and quality.
High-Quality Standards
Japanese manufacturers uphold stringent quality standards at every stage of production.
This commitment ensures that the final products meet or exceed customer expectations, fostering brand loyalty and market competitiveness.
Operational Flexibility
The ability to adapt to changing market demands and production requirements is a significant advantage of Japanese manufacturing.
Flexible production lines can quickly adjust to variations in product specifications and volume, enhancing responsiveness and customer satisfaction.
Cost Efficiency
Through waste minimization, efficient resource utilization, and strategic procurement, Japanese manufacturers achieve cost efficiency.
Lower operational costs translate into competitive pricing, increasing market share and profitability.
Innovation and Technology Integration
Japanese production lines integrate advanced technologies and innovative processes to enhance efficiency and product quality.
Automation, robotics, and data analytics are employed to optimize operations, reduce errors, and drive continuous improvement.
Challenges and Disadvantages
While Japanese production line techniques offer significant advantages, they also present certain challenges and disadvantages.
Cultural Barriers
The cultural emphasis on group harmony and consensus can sometimes impede rapid decision-making and adaptation.
This can be a challenge in dynamic markets where swift actions are necessary to stay competitive.
High Initial Investment
Implementing advanced production technologies and lean systems requires substantial initial investment.
Small and medium-sized enterprises may find it challenging to allocate the necessary resources, potentially limiting their ability to adopt these practices fully.
Dependency on Supplier Relationships
The strong reliance on long-term supplier relationships may reduce flexibility in sourcing alternatives.
In the event of supplier issues, disruptions can significantly impact the production line’s efficiency and continuity.
Supplier Negotiation Techniques
Effective supplier negotiation is crucial for maintaining cost efficiency and ensuring high-quality inputs in Japanese manufacturing.
Win-Win Negotiation Strategy
Japanese negotiations often focus on achieving mutually beneficial outcomes.
By fostering partnerships where both parties gain value, long-term relationships are strengthened, and collaboration is enhanced.
Preparation and Information Gathering
Thorough preparation and comprehensive understanding of the supplier’s business, capabilities, and market conditions are essential.
This knowledge empowers negotiators to make informed decisions and present compelling arguments during negotiations.
Building Trust and Transparency
Establishing trust through open communication and transparency is key to successful negotiations.
Trust facilitates smoother negotiations, reduces conflicts, and promotes long-term partnerships based on reliability and mutual respect.
Flexibility and Adaptability
Being flexible and adaptable during negotiations allows for creative solutions that address both parties’ needs.
This approach enables negotiators to overcome obstacles and reach agreements that support ongoing collaboration.
Market Conditions and Their Impact
Market conditions significantly influence Japanese procurement and manufacturing strategies.
Global Supply Chain Dynamics
Global supply chain fluctuations, such as geopolitical tensions and trade policies, affect sourcing strategies.
Japanese manufacturers must navigate these dynamics to maintain supply chain stability and ensure uninterrupted production.
Technological Advancements
Rapid technological changes drive the need for continuous adaptation in production processes.
Staying abreast of technological advancements allows Japanese manufacturers to integrate new tools and methods that enhance efficiency and competitiveness.
Economic Factors
Economic conditions, including currency exchange rates and economic growth, influence procurement costs and pricing strategies.
Japanese manufacturers must adapt to these factors to maintain profitability and market position.
Environmental and Regulatory Pressures
Increasing environmental regulations and sustainability expectations impact manufacturing practices.
Japanese companies are at the forefront of adopting sustainable practices, integrating eco-friendly materials and processes to comply with regulations and meet market expectations.
Best Practices in Japanese Production Lines
Adopting best practices from Japanese manufacturing can significantly enhance a company’s production efficiency and quality.
Standardization and Documentation
Standardizing processes and maintaining comprehensive documentation ensure consistency and facilitate training.
This approach minimizes errors and variability, promoting reliable and predictable production outcomes.
Employee Empowerment and Training
Investing in employee training and empowerment fosters a skilled and motivated workforce.
Encouraging employees to take initiative and contribute ideas for improvement cultivates a culture of excellence and continuous betterment.
Visual Management
Implementing visual management tools, such as dashboards and Kanban boards, enhances transparency and coordination.
These tools provide real-time insights into production status, facilitating prompt decision-making and issue resolution.
Total Quality Management (TQM)
Adopting TQM principles ensures that quality is integrated into every aspect of the production process.
Continuous monitoring, evaluation, and improvement of quality metrics lead to superior products and customer satisfaction.
Implementing Japanese Practices Internationally
Global companies can benefit from integrating Japanese production line practices into their operations.
Adaptation to Local Contexts
While adopting Japanese practices, it is essential to adapt them to fit local cultural and operational contexts.
Customization ensures that the practices are effective and resonate with the workforce, maximizing their impact.
Investment in Training and Development
Providing comprehensive training and development programs equips employees with the skills and knowledge necessary to implement Japanese practices successfully.
Continuous learning and skill enhancement are critical for sustaining long-term improvements.
Collaborative Partnerships
Establishing partnerships with Japanese suppliers and consultants can facilitate knowledge transfer and effective implementation.
Collaborative efforts ensure that best practices are integrated seamlessly into existing operations.
Monitoring and Continuous Improvement
Regularly monitoring performance and seeking opportunities for improvement ensures that the adopted practices remain effective and relevant.
Embracing a mindset of continuous improvement sustains the benefits derived from Japanese manufacturing techniques.
Case Studies of Successful Implementation
Several global companies have successfully adopted Japanese manufacturing practices to enhance their production efficiency and quality.
Toyota’s Global Expansion
Toyota has effectively implemented its Toyota Production System (TPS) across its global operations.
By maintaining consistency in lean manufacturing principles and fostering a culture of continuous improvement, Toyota has achieved remarkable efficiency and quality standards worldwide.
Honda’s Supplier Integration
Honda’s strategic integration with suppliers has led to improved supply chain efficiency and product quality.
Through strong supplier partnerships and collaborative development, Honda ensures that its production lines are supported by reliable and innovative supply sources.
Siemens’ Lean Transformation
Siemens adopted lean manufacturing principles inspired by Japanese practices to streamline its production processes.
This transformation resulted in reduced waste, enhanced productivity, and improved product quality, demonstrating the effectiveness of Japanese manufacturing techniques in diverse industries.
Conclusion
Japanese manufacturing’s art of the production line exemplifies unmatched efficiency and quality.
By embracing strategic procurement and purchasing, fostering strong supplier relationships, and implementing best practices like lean manufacturing and continuous improvement, Japanese companies set a benchmark for manufacturing excellence.
International companies can draw valuable lessons from these practices, adapting and integrating them to revolutionize their own production lines.
The synergy of proven Japanese techniques with local innovations holds the key to achieving operational excellence and sustained competitive advantage in the global marketplace.
資料ダウンロード
QCD調達購買管理クラウド「newji」は、調達購買部門で必要なQCD管理全てを備えた、現場特化型兼クラウド型の今世紀最高の購買管理システムとなります。
ユーザー登録
調達購買業務の効率化だけでなく、システムを導入することで、コスト削減や製品・資材のステータス可視化のほか、属人化していた購買情報の共有化による内部不正防止や統制にも役立ちます。
NEWJI DX
製造業に特化したデジタルトランスフォーメーション(DX)の実現を目指す請負開発型のコンサルティングサービスです。AI、iPaaS、および先端の技術を駆使して、製造プロセスの効率化、業務効率化、チームワーク強化、コスト削減、品質向上を実現します。このサービスは、製造業の課題を深く理解し、それに対する最適なデジタルソリューションを提供することで、企業が持続的な成長とイノベーションを達成できるようサポートします。
オンライン講座
製造業、主に購買・調達部門にお勤めの方々に向けた情報を配信しております。
新任の方やベテランの方、管理職を対象とした幅広いコンテンツをご用意しております。
お問い合わせ
コストダウンが利益に直結する術だと理解していても、なかなか前に進めることができない状況。そんな時は、newjiのコストダウン自動化機能で大きく利益貢献しよう!
(Β版非公開)