- お役立ち記事
- “Japanese Manufacturing: Innovations and Trends Shaping the Industry in 2023”
“Japanese Manufacturing: Innovations and Trends Shaping the Industry in 2023”
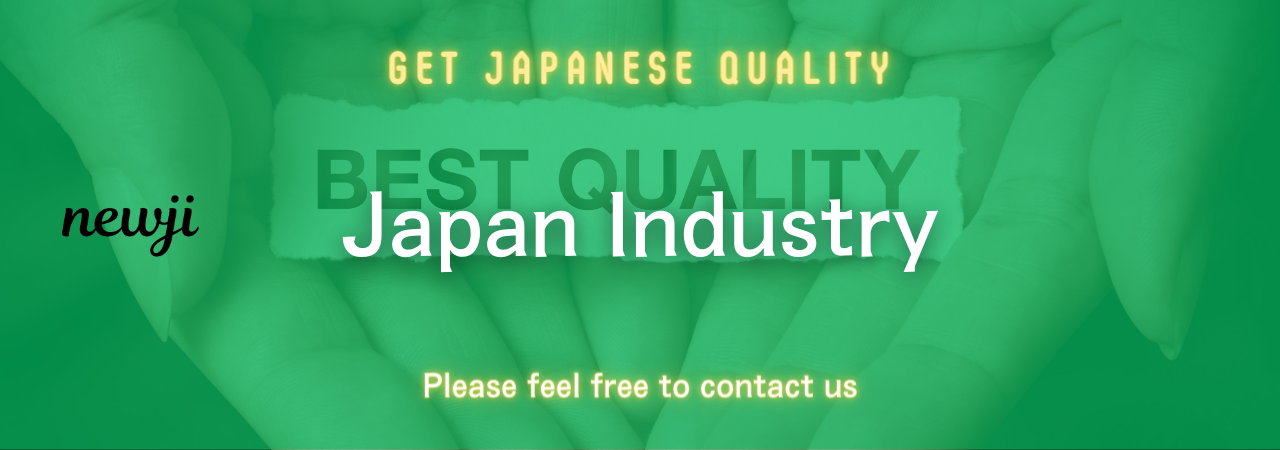
目次
Introduction to Japanese Manufacturing in 2023
Japanese manufacturing has long been synonymous with quality, precision, and innovation. In 2023, the industry continues to evolve, embracing cutting-edge technologies and adapting to global market dynamics. This article explores the latest innovations and trends shaping Japanese manufacturing, with a particular focus on procurement and purchasing perspectives. We will delve into the advantages and disadvantages of sourcing from Japanese suppliers, effective negotiation techniques, current market conditions, and best practices for maximizing the benefits of Japanese procurement.
Key Innovations in Japanese Manufacturing
Advanced Robotics and Automation
Japanese manufacturers are at the forefront of robotics and automation technology. In 2023, the integration of collaborative robots, or cobots, has increased, allowing for more flexible and efficient production lines. These robots work alongside human workers, enhancing productivity and reducing the risk of errors.
Artificial Intelligence and Machine Learning
Artificial Intelligence (AI) and Machine Learning (ML) are revolutionizing manufacturing processes. Japanese companies are leveraging AI for predictive maintenance, quality control, and supply chain optimization. These technologies enable manufacturers to anticipate equipment failures, maintain high product quality, and streamline logistics.
Sustainable Manufacturing Practices
Sustainability remains a critical focus in Japanese manufacturing. Companies are adopting eco-friendly materials, reducing waste, and optimizing energy consumption. Innovations such as circular economy models and green manufacturing technologies are gaining traction, aligning with global environmental standards and consumer preferences.
Internet of Things (IoT) Integration
The Internet of Things is transforming manufacturing by connecting machines, devices, and systems. Japanese manufacturers are implementing IoT solutions to monitor real-time data, enhance operational efficiency, and enable smart factory environments. This connectivity facilitates better decision-making and more responsive manufacturing processes.
Additive Manufacturing and 3D Printing
Additive manufacturing, or 3D printing, continues to grow in Japan, particularly in sectors requiring customized and complex components. This technology allows for rapid prototyping, reducing time-to-market, and enabling mass customization. Japanese manufacturers are utilizing 3D printing to innovate product designs and improve manufacturing flexibility.
Trends Shaping the Japanese Manufacturing Industry
Reshoring and Local Production
In response to global supply chain disruptions, many Japanese companies are reshoring production to domestic facilities. This trend enhances supply chain resilience, reduces dependency on international suppliers, and supports local economies. Reshoring also allows for better control over production quality and timelines.
Digital Transformation
Digital transformation is a critical trend in Japanese manufacturing. Companies are investing in digital tools and platforms to enhance operational efficiency, improve data analytics, and facilitate communication across global operations. Digital transformation supports the implementation of Industry 4.0 practices, driving innovation and competitiveness.
Focus on Workforce Development
As manufacturing becomes more technologically advanced, there is a growing emphasis on workforce development. Japanese manufacturers are investing in training programs to equip employees with the skills needed to operate advanced machinery, manage digital systems, and engage in continuous improvement initiatives.
Collaborative Supply Chains
Collaboration across the supply chain is becoming increasingly important. Japanese manufacturers are fostering closer relationships with suppliers and partners to enhance coordination, reduce lead times, and ensure quality. Collaborative supply chains contribute to greater flexibility and responsiveness in meeting customer demands.
Emphasis on Quality and Reliability
Quality and reliability remain paramount in Japanese manufacturing. Companies continue to implement rigorous quality control measures, adhere to strict standards, and pursue certifications such as ISO to ensure product excellence. This emphasis on quality helps maintain Japan’s reputation for producing superior goods.
Advantages of Sourcing from Japanese Suppliers
High-Quality Standards
Japanese suppliers are renowned for their commitment to quality. Rigorous quality control processes and continuous improvement practices ensure that products meet or exceed specifications. This high standard minimizes defects and enhances the reliability of sourced components.
Technological Expertise
Japanese manufacturers possess advanced technological expertise. Their ability to innovate and integrate new technologies into production processes results in superior products and efficient manufacturing practices. Partnering with technologically adept suppliers can provide access to cutting-edge solutions.
Strong Supply Chain Management
Japanese companies excel in supply chain management, ensuring timely delivery and consistent supply. Their efficient logistics, inventory management, and ability to handle complex supply chains reduce the risk of delays and disruptions, contributing to smoother procurement processes.
Long-Term Relationships
Building long-term relationships with suppliers is a cornerstone of Japanese business culture. This approach fosters trust, reliability, and mutual benefit, leading to stable partnerships and improved collaboration over time.
Innovation and R&D Capabilities
Japanese suppliers invest heavily in research and development, driving continuous innovation. Partnering with such suppliers provides access to the latest advancements and fosters collaborative innovation, enhancing the competitiveness of your products.
Disadvantages of Sourcing from Japanese Suppliers
Higher Costs
Sourcing from Japan can be more expensive compared to suppliers from regions with lower labor and production costs. The higher cost is often reflective of the superior quality and advanced technologies offered by Japanese manufacturers.
Cultural and Language Barriers
Cultural differences and language barriers can pose challenges in communication and negotiation. Navigating these differences requires understanding Japanese business etiquette and potentially investing in language translation services or local expertise.
Longer Lead Times
Shipping products from Japan may involve longer lead times compared to domestic or closer international suppliers. Delays in shipping and customs can impact the overall procurement timeline, necessitating careful planning and inventory management.
Strict Quality Requirements
While high-quality standards are an advantage, they can also be a disadvantage if your organization is not prepared to meet these stringent requirements. Ensuring compliance with Japanese quality standards may require additional resources and adjustments to your own processes.
Limited Flexibility
Japanese manufacturers may have specific processes and systems that limit flexibility in production. Customizing orders or making rapid changes to specifications can be more challenging, requiring careful coordination and clear communication.
Supplier Negotiation Techniques
Building Trust and Relationships
Establishing trust is crucial in Japanese business culture. Spend time building relationships through regular communication, site visits, and mutual respect. Demonstrating reliability and commitment can lead to more favorable negotiation outcomes.
Understanding Cultural Norms
Familiarize yourself with Japanese cultural norms and business etiquette. Showing respect, patience, and humility can facilitate smoother negotiations. Understanding the importance of consensus and harmony will help in navigating discussions effectively.
Focusing on Mutual Benefits
Approach negotiations with a focus on creating mutually beneficial outcomes. Highlight how the partnership can add value for both parties, ensuring that agreements are sustainable and advantageous in the long term.
Being Patient and Persistent
Japanese negotiations may take longer as decisions often involve multiple stakeholders and thorough deliberation. Exercise patience and persistence, allowing time for processes to unfold without pressuring for immediate decisions.
Emphasizing Quality and Reliability
Align your negotiation strategy with the emphasis on quality and reliability. Demonstrate your commitment to maintaining high standards and how your partnership can enhance product excellence and operational efficiency.
Clear and Detailed Communication
Ensure that all terms, expectations, and specifications are clearly communicated and documented. Providing detailed information reduces misunderstandings and helps in reaching clear and enforceable agreements.
Current Market Conditions
Global Supply Chain Challenges
The global supply chain continues to face challenges such as disruptions from geopolitical tensions, natural disasters, and pandemics. Japanese manufacturers, known for their resilience, are adapting by diversifying their supply chains and enhancing flexibility to mitigate these disruptions.
Economic Factors
Japan’s economy remains robust, supported by its advanced manufacturing sector. However, factors such as fluctuating currency exchange rates, inflation, and changes in consumer demand can impact the cost and availability of manufacturing inputs.
Technological Advancements
Rapid technological advancements are driving changes in manufacturing processes. Companies that fail to keep pace with innovations risk losing their competitive edge. Japanese manufacturers are investing heavily in research and development to stay ahead.
Environmental Regulations
Increasingly stringent environmental regulations are shaping manufacturing practices. Japanese companies are leading the way in adopting sustainable practices to comply with regulations and meet the growing demand for eco-friendly products.
Labor Market Dynamics
Japan faces challenges related to an aging workforce and labor shortages. Manufacturers are responding by investing in automation, enhancing training programs, and implementing measures to retain skilled workers.
Best Practices for Procurement and Purchasing from Japan
Comprehensive Supplier Evaluation
Conduct thorough evaluations of potential Japanese suppliers. Assess their financial stability, quality certifications, production capabilities, and past performance. Site visits and third-party audits can provide valuable insights into supplier operations.
Establishing Clear Specifications
Define clear and detailed product specifications to ensure that Japanese suppliers understand your requirements. Detailed specifications help in minimizing misunderstandings and ensuring that the final products meet your standards.
Developing Long-Term Partnerships
Focus on building long-term relationships rather than seeking short-term gains. Long-term partnerships foster trust, encourage collaboration, and can lead to better pricing, priority service, and mutual growth opportunities.
Implementing Effective Communication Channels
Establish robust communication channels to facilitate regular and transparent interactions with Japanese suppliers. Utilize digital communication tools, schedule regular meetings, and ensure that language barriers are addressed through translation or local support.
Leveraging Technology for Collaboration
Use collaborative technologies such as project management software, shared digital platforms, and real-time data sharing to enhance collaboration. Technology can streamline processes, improve transparency, and enable faster decision-making.
Negotiating Fair and Transparent Terms
Aim for fairness and transparency in all negotiations. Clearly outline terms related to pricing, delivery schedules, quality standards, and payment conditions. Transparent agreements reduce the risk of conflicts and foster a positive working relationship.
Continuous Monitoring and Improvement
Regularly monitor supplier performance through key performance indicators (KPIs) such as on-time delivery, quality metrics, and responsiveness. Use this data to identify areas for improvement and work collaboratively with suppliers to address any issues.
Risk Management and Contingency Planning
Identify potential risks in your procurement process and develop contingency plans. This includes having alternative suppliers, maintaining safety stock, and diversifying supply sources to mitigate the impact of unforeseen disruptions.
Compliance with Regulations and Standards
Ensure that both your organization and your Japanese suppliers comply with relevant regulations and industry standards. Staying compliant helps in avoiding legal issues and maintains the integrity of your supply chain.
Embracing Sustainability
Incorporate sustainability into your procurement strategy by selecting suppliers who prioritize eco-friendly practices. This not only aligns with global environmental goals but also meets the growing consumer demand for sustainable products.
Conclusion
Japanese manufacturing in 2023 showcases a blend of traditional excellence and modern innovation. The industry’s focus on advanced technologies, sustainability, and quality continues to set benchmarks globally. For procurement and purchasing professionals, sourcing from Japanese suppliers offers significant advantages, including high-quality standards, technological expertise, and strong supply chain management. However, it also presents challenges such as higher costs and cultural barriers.
By adopting best practices in supplier evaluation, communication, and relationship building, companies can effectively navigate these challenges and harness the benefits of Japanese manufacturing. Emphasizing mutual trust, clear specifications, and continuous improvement will foster productive partnerships, driving success in an increasingly competitive global market. As Japanese manufacturers continue to innovate and adapt to evolving trends, they remain invaluable partners for businesses seeking quality, reliability, and cutting-edge solutions in their procurement strategies.
資料ダウンロード
QCD調達購買管理クラウド「newji」は、調達購買部門で必要なQCD管理全てを備えた、現場特化型兼クラウド型の今世紀最高の購買管理システムとなります。
ユーザー登録
調達購買業務の効率化だけでなく、システムを導入することで、コスト削減や製品・資材のステータス可視化のほか、属人化していた購買情報の共有化による内部不正防止や統制にも役立ちます。
NEWJI DX
製造業に特化したデジタルトランスフォーメーション(DX)の実現を目指す請負開発型のコンサルティングサービスです。AI、iPaaS、および先端の技術を駆使して、製造プロセスの効率化、業務効率化、チームワーク強化、コスト削減、品質向上を実現します。このサービスは、製造業の課題を深く理解し、それに対する最適なデジタルソリューションを提供することで、企業が持続的な成長とイノベーションを達成できるようサポートします。
オンライン講座
製造業、主に購買・調達部門にお勤めの方々に向けた情報を配信しております。
新任の方やベテランの方、管理職を対象とした幅広いコンテンツをご用意しております。
お問い合わせ
コストダウンが利益に直結する術だと理解していても、なかなか前に進めることができない状況。そんな時は、newjiのコストダウン自動化機能で大きく利益貢献しよう!
(Β版非公開)