- お役立ち記事
- Key Considerations for Selecting and Implementing Print Inspection Systems for SMEs
Key Considerations for Selecting and Implementing Print Inspection Systems for SMEs
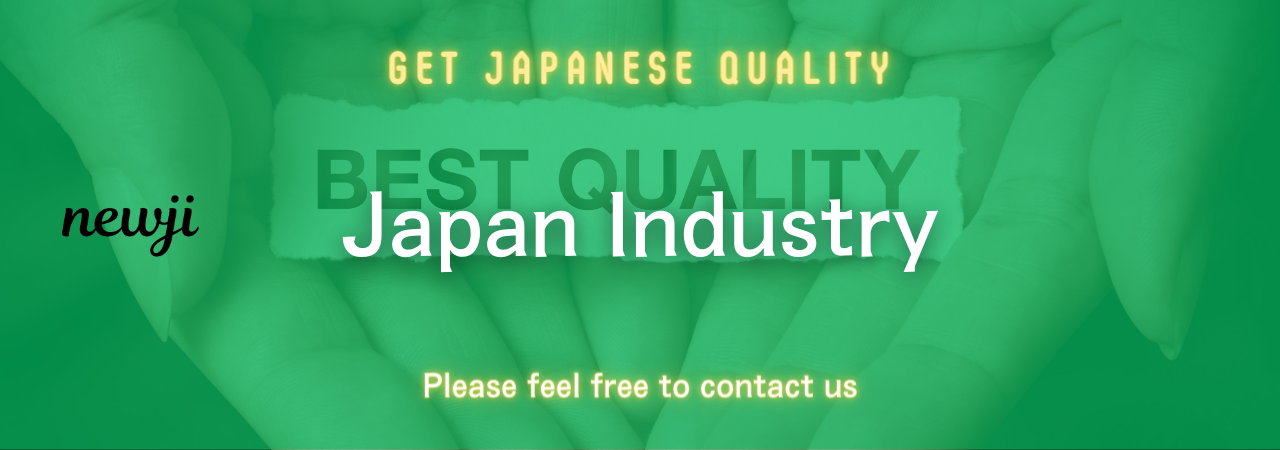
目次
Introduction
In the fast-paced world of manufacturing, quality is of the utmost importance.
Small to medium-sized enterprises (SMEs) often face challenges when it comes to maintaining high-quality standards due to limited resources.
This is where print inspection systems come into play, offering an effective solution to ensure product quality without sacrificing efficiency.
Selecting and implementing a suitable print inspection system is crucial for SMEs to remain competitive.
This article will explore key considerations that SMEs should keep in mind when choosing a print inspection system.
Understanding Print Inspection Systems
Print inspection systems are designed to detect and rectify errors in the production process.
These systems help ensure that printed materials meet specified quality standards, thus reducing waste and improving product consistency.
By using advanced technologies like optical sensors and cameras, they can identify defects, such as color variations, misprints, and alignment issues.
For SMEs, implementing these systems can lead to increased productivity and improved quality assurance.
Key Considerations for Selecting a Print Inspection System
1. Budget Constraints
One of the most important factors for SMEs is the budget for purchasing a print inspection system.
It’s crucial to balance cost with the capabilities offered by the system.
Ensure that the system provides essential functions without overspending on unnecessary features.
Evaluate the long-term financial benefits, such as reduced returns and waste, against the initial investment.
2. System Compatibility
Compatibility with existing equipment is another critical consideration.
The new system should integrate seamlessly with current production lines to avoid disruptions.
Check if the inspection system supports the types of materials and printing methods used by your company.
If the system requires extensive modifications to integrate, it might not be the best option for your business.
3. Ease of Use
An ideal print inspection system should be user-friendly, with intuitive interfaces that require minimal training.
Complex systems can drain resources due to time spent on lengthy training sessions.
Look for systems that offer straightforward setup procedures and easy maintenance to keep your operation running smoothly.
4. Scalability
As your business grows, your needs will evolve.
It’s wise to select an inspection system that can scale in response to increased production demands.
Opt for systems that offer modular upgrades or flexible configurations to ensure that your investment remains viable in the long term.
5. Accuracy and Precision
The precision of a print inspection system is vital for ensuring quality.
Inaccurate systems can lead to overlooked defects and compromised products.
Research various systems to find one that offers high-resolution imaging and reliable defect detection.
The ability to adjust tolerance levels for different products can provide additional flexibility.
6. After-Sales Support and Training
Reliable customer support and comprehensive training should be a top priority when selecting a print inspection system.
Strong after-sales support ensures that any issues that arise are resolved quickly, minimizing downtime.
Look for manufacturers that offer extensive training resources and responsive technical assistance to support your team.
Implementation Tips
1. Conduct a Needs Assessment
Before purchasing a print inspection system, conducting a thorough needs assessment is crucial.
Identify areas in your production process that would benefit most from improved quality control.
Understanding your specific requirements will guide you in choosing the right system.
2. Involve Key Stakeholders
Involving key stakeholders in the decision-making process can lead to better results.
Engage team members from various departments to gather insights and ensure the chosen system meets everyone’s needs.
This collaborative approach will also facilitate smoother implementation.
3. Test the System
Request a demonstration or trial period with the system to evaluate its true capabilities.
Testing the system under real production conditions can provide a clearer picture of its strengths and limitations.
It also allows your team to become familiar with the system before full implementation.
4. Plan for Continuous Improvement
Finally, implementing a print inspection system should be viewed as an ongoing process, not a one-time fix.
Regularly review the system’s performance and make adjustments as needed.
Encourage feedback from your team to identify areas for improvement and potential system updates.
Conclusion
Choosing and implementing print inspection systems in SMEs is a strategic decision that can greatly enhance product quality and operational efficiency.
By carefully considering budget constraints, system compatibility, ease of use, and other key factors, SMEs can select a system that aligns with their specific needs.
Integrating the right print inspection system will not only ensure superior product quality but also provide a competitive edge in the market.
As your business evolves, the right print inspection system will support your growth and ensure continued success.
資料ダウンロード
QCD調達購買管理クラウド「newji」は、調達購買部門で必要なQCD管理全てを備えた、現場特化型兼クラウド型の今世紀最高の購買管理システムとなります。
ユーザー登録
調達購買業務の効率化だけでなく、システムを導入することで、コスト削減や製品・資材のステータス可視化のほか、属人化していた購買情報の共有化による内部不正防止や統制にも役立ちます。
NEWJI DX
製造業に特化したデジタルトランスフォーメーション(DX)の実現を目指す請負開発型のコンサルティングサービスです。AI、iPaaS、および先端の技術を駆使して、製造プロセスの効率化、業務効率化、チームワーク強化、コスト削減、品質向上を実現します。このサービスは、製造業の課題を深く理解し、それに対する最適なデジタルソリューションを提供することで、企業が持続的な成長とイノベーションを達成できるようサポートします。
オンライン講座
製造業、主に購買・調達部門にお勤めの方々に向けた情報を配信しております。
新任の方やベテランの方、管理職を対象とした幅広いコンテンツをご用意しております。
お問い合わせ
コストダウンが利益に直結する術だと理解していても、なかなか前に進めることができない状況。そんな時は、newjiのコストダウン自動化機能で大きく利益貢献しよう!
(Β版非公開)