- お役立ち記事
- Practical Guide to Quality Improvement and Cost Reduction Using Six Sigma
Practical Guide to Quality Improvement and Cost Reduction Using Six Sigma
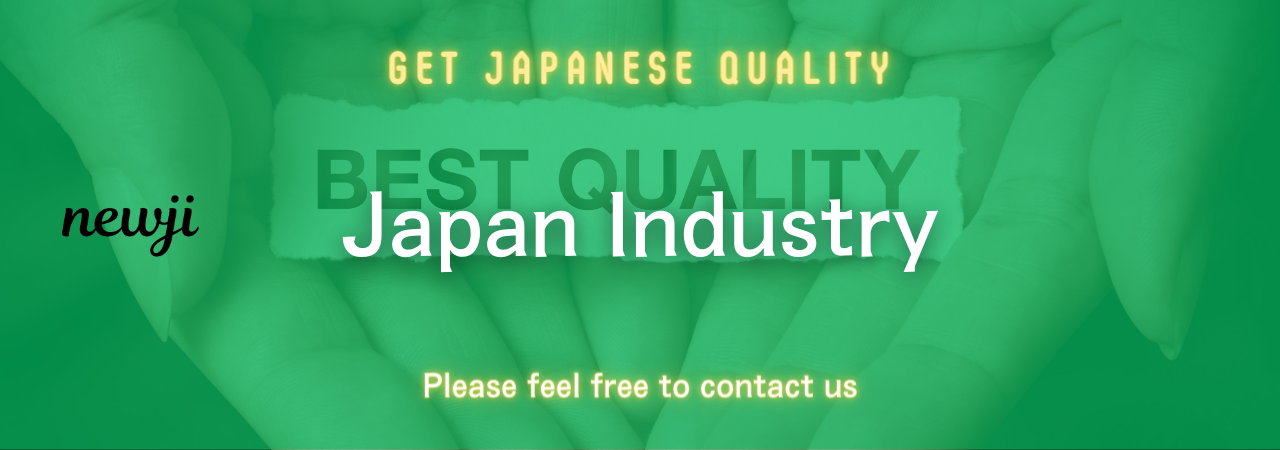
目次
Introduction to Six Sigma
Six Sigma is a powerful methodology widely adopted by businesses to improve quality and reduce costs.
Originating from manufacturing, it has expanded across various sectors, including healthcare, finance, and service industries.
The primary goal of Six Sigma is to reduce the occurrence of defects and variability in processes, thereby enhancing the overall quality of products and services.
At the core of Six Sigma is its statistical foundation, which relies on measurable data to drive process improvements.
By following a structured approach, businesses can identify inefficiencies, understand their root causes, and implement effective solutions.
This makes Six Sigma an essential tool for organizations aiming to achieve superior performance and customer satisfaction.
Key Principles of Six Sigma
Six Sigma is founded on several key principles that guide its implementation and success:
1. **Focus on Customer Needs**: Understanding and meeting customer requirements are vital. Six Sigma encourages businesses to prioritize customer satisfaction by delivering products and services that consistently meet their expectations.
2. **Data-Driven Decisions**: Decisions should be based on data analysis rather than assumptions. Six Sigma emphasizes the collection and analysis of relevant data to identify areas for improvement and track progress.
3. **Process-Centric Approach**: By analyzing and understanding processes, businesses can pinpoint areas needing enhancement. Well-defined processes reduce variability and lead to more predictable outcomes.
4. **Proactive Management**: Six Sigma stresses the importance of anticipating problems and implementing preventive measures. This proactive stance helps mitigate risks and seize opportunities for improvement.
5. **Collaborative Efforts**: Success in Six Sigma involves teamwork across all organizational levels. Employees are encouraged to work collaboratively, sharing knowledge and expertise to drive collective improvements.
The DMAIC Methodology
The DMAIC methodology is the backbone of Six Sigma projects.
It stands for Define, Measure, Analyze, Improve, and Control, and provides a structured framework for improving existing processes.
Define
The first phase involves defining the problem and identifying the project’s scope.
This includes clearly outlining the process to be improved, setting objectives, and determining the project goals.
It’s essential to define key deliverables and establish a timeline for completion.
Measure
In the Measure phase, data collection plays a crucial role.
Organizations gather data relating to the current process performance.
This helps in understanding baseline metrics and identifying areas of concern.
Tools such as process maps and flowcharts may be used to visualize data.
Analyze
During the Analyze phase, the collected data is thoroughly examined to identify the root causes of defects or inefficiencies.
Advanced statistical tools and techniques aid in this analysis.
The goal is to understand why problems occur and where changes are needed.
Improve
The Improve phase focuses on developing and implementing solutions to address the identified issues.
It involves brainstorming potential improvements, testing solutions, and making necessary adjustments.
Pilot tests or experiments may be conducted to gauge the effectiveness of proposed solutions.
Control
The Control phase ensures that improvements are sustained over time.
By establishing monitoring mechanisms and control plans, organizations can maintain the gains achieved.
Continuous monitoring helps detect potential deviations, allowing for quick corrective actions.
Benefits of Implementing Six Sigma
The adoption of Six Sigma brings numerous benefits to organizations:
– **Cost Reduction**: By eliminating defects and inefficiencies, businesses can significantly reduce operational costs. This can lead to enhanced profitability and competitive advantage.
– **Enhanced Quality**: Six Sigma helps produce higher-quality products and services, meeting and exceeding customer expectations. This strengthens customer loyalty and boosts brand reputation.
– **Increased Efficiency**: Streamlined processes lead to more efficient operations. Businesses can achieve faster turnaround times, optimize resource utilization, and improve overall productivity.
– **Data-Driven Culture**: Organizations develop a data-centric mindset, fostering informed decision-making. This cultural shift encourages continuous improvement and innovation.
– **Employee Engagement**: Involvement in Six Sigma projects empowers employees and fosters a sense of ownership. Team collaboration and skill development contribute to a motivated workforce.
Challenges in Six Sigma Implementation
While Six Sigma offers significant advantages, organizations may face challenges during implementation:
– **Resistance to Change**: Employees may resist changes to established processes. Overcoming this resistance requires effective communication and demonstrating the benefits of Six Sigma.
– **Training Requirements**: Successful implementation demands comprehensive training. Organizations need to invest time and resources in training employees, particularly in statistical tools and methodologies.
– **Sustaining Improvements**: Maintaining long-term improvements can be challenging. Businesses must have robust monitoring systems in place to ensure changes are preserved.
– **Cultural Shifts**: Developing a Six Sigma culture involves altering mindsets and behaviors. Cultivating this shift takes time, commitment, and leadership support.
Conclusion
Six Sigma is a proven methodology for quality improvement and cost reduction.
By embracing its techniques and principles, organizations can enhance their processes, deliver exceptional value to customers, and achieve sustained success.
Although challenges exist, overcoming them can lead to significant transformational benefits.
Companies that commit to the Six Sigma journey stand to gain a valuable edge in today’s competitive marketplace.
Through collaboration, data-driven decisions, and a relentless pursuit of excellence, Six Sigma guides organizations on the path to growth and prosperity.
資料ダウンロード
QCD調達購買管理クラウド「newji」は、調達購買部門で必要なQCD管理全てを備えた、現場特化型兼クラウド型の今世紀最高の購買管理システムとなります。
ユーザー登録
調達購買業務の効率化だけでなく、システムを導入することで、コスト削減や製品・資材のステータス可視化のほか、属人化していた購買情報の共有化による内部不正防止や統制にも役立ちます。
NEWJI DX
製造業に特化したデジタルトランスフォーメーション(DX)の実現を目指す請負開発型のコンサルティングサービスです。AI、iPaaS、および先端の技術を駆使して、製造プロセスの効率化、業務効率化、チームワーク強化、コスト削減、品質向上を実現します。このサービスは、製造業の課題を深く理解し、それに対する最適なデジタルソリューションを提供することで、企業が持続的な成長とイノベーションを達成できるようサポートします。
オンライン講座
製造業、主に購買・調達部門にお勤めの方々に向けた情報を配信しております。
新任の方やベテランの方、管理職を対象とした幅広いコンテンツをご用意しております。
お問い合わせ
コストダウンが利益に直結する術だと理解していても、なかなか前に進めることができない状況。そんな時は、newjiのコストダウン自動化機能で大きく利益貢献しよう!
(Β版非公開)