- お役立ち記事
- Unlocking the Future: How Japanese Manufacturing Revolutionizes Industry with Frequency Division Multiplexing (FDM)
Unlocking the Future: How Japanese Manufacturing Revolutionizes Industry with Frequency Division Multiplexing (FDM)
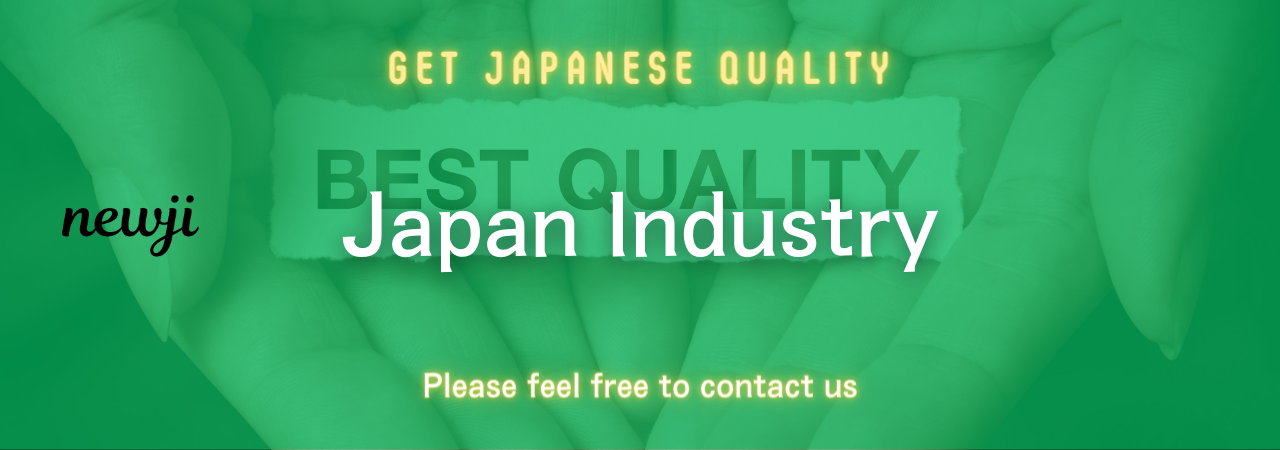
目次
Introduction to Frequency Division Multiplexing (FDM) in Manufacturing
Frequency Division Multiplexing, commonly known as FDM, is a technology traditionally associated with telecommunications. In recent years, Japanese manufacturing industries have begun to integrate FDM into their production processes, leading to significant advancements in efficiency and productivity. This article explores how Japanese manufacturers are revolutionizing the industry with FDM, highlighting its practical applications, advantages and disadvantages, supplier negotiation techniques, market conditions, and best practices.
Understanding Frequency Division Multiplexing (FDM)
FDM is a method of transmitting multiple signals simultaneously over a single communication medium by allocating different frequency bands to each signal. In manufacturing, this technology can be adapted to enhance various aspects of production, from machine communication to data management.
FDM in Machine Communication
Japanese manufacturers are utilizing FDM to improve communication between machines on the production floor. By assigning specific frequency bands to different machines, data can be transmitted more efficiently, reducing downtime and increasing overall productivity.
Data Management and FDM
FDM allows for the simultaneous transmission of multiple data streams, enabling real-time monitoring and data analysis in manufacturing processes. This real-time data handling supports better decision-making and proactive maintenance, ensuring smooth operations.
Advantages of Implementing FDM in Manufacturing
Adopting FDM in manufacturing offers several benefits that contribute to the overall efficiency and effectiveness of production processes.
Enhanced Efficiency
By enabling simultaneous data transmission, FDM reduces the time required for communication between different parts of the production process. This enhancement leads to faster decision-making and quicker responses to potential issues.
Improved Accuracy
FDM minimizes interference between different data streams, ensuring more accurate data transmission. This accuracy is crucial for maintaining high-quality standards in manufacturing.
Scalability
FDM systems can be easily scaled to accommodate growing production needs. As manufacturing demands increase, additional frequency bands can be allocated without significant redesigns of the existing system.
Cost-Effectiveness
Implementing FDM can lead to cost savings by reducing the need for multiple communication channels and minimizing downtime. These savings can be reinvested into other areas of the manufacturing process.
Disadvantages of FDM in Manufacturing
While FDM offers numerous benefits, there are also challenges associated with its implementation in manufacturing environments.
Initial Investment
Setting up an FDM system requires an initial investment in technology and infrastructure. For some manufacturers, the upfront costs can be a barrier to adoption.
Complexity of Integration
Integrating FDM into existing manufacturing processes can be complex. It requires careful planning and expertise to ensure seamless integration without disrupting current operations.
Maintenance Requirements
FDM systems require regular maintenance to function optimally. This maintenance involves ongoing costs and the need for skilled personnel to manage the system.
Supplier Negotiation Techniques for FDM Components
Effective supplier negotiation is crucial for manufacturers looking to implement FDM. Japanese suppliers are known for their high-quality components and reliable service, making them valuable partners in the adoption of FDM technology.
Building Strong Relationships
Japanese business culture emphasizes long-term relationships and mutual trust. Building strong relationships with suppliers can lead to better negotiation outcomes and more favorable terms.
Understanding Supplier Capabilities
Before entering negotiations, it is essential to understand the supplier’s capabilities and limitations. This knowledge enables manufacturers to negotiate terms that are realistic and beneficial for both parties.
Leveraging Total Cost of Ownership
Negotiations should consider the total cost of ownership, including initial costs, maintenance, and potential savings. This comprehensive approach ensures that decisions are made based on long-term benefits rather than short-term gains.
Utilizing Negotiation Strategies
Employing effective negotiation strategies, such as bundling purchases or committing to long-term contracts, can provide manufacturers with leverage to secure better prices and terms.
Current Market Conditions for FDM in Manufacturing
The market for FDM in manufacturing is influenced by various factors, including technological advancements, global supply chains, and economic conditions.
Technological Advancements
Continuous advancements in FDM technology are expanding its applications in manufacturing. Innovations such as increased bandwidth and improved signal processing are making FDM more attractive to manufacturers.
Global Supply Chain Dynamics
The global supply chain plays a significant role in the adoption of FDM. Japanese suppliers, renowned for their reliability and quality, are key players in providing the necessary components for FDM systems.
Economic Factors
Economic conditions, such as fluctuations in currency values and trade policies, impact the cost and availability of FDM components. Manufacturers must stay informed about these factors to make strategic purchasing decisions.
Best Practices for Implementing FDM in Manufacturing
To successfully integrate FDM into manufacturing processes, companies should follow best practices that ensure smooth adoption and optimal performance.
Comprehensive Planning
Thorough planning is essential for the successful implementation of FDM. This includes assessing current processes, identifying areas for improvement, and developing a detailed implementation roadmap.
Investing in Training
Training staff on the use and maintenance of FDM systems is crucial. Skilled personnel are necessary to manage the technology effectively and troubleshoot any issues that arise.
Collaborating with Experts
Working with experts, including technology providers and consultants, can help manufacturers navigate the complexities of FDM implementation. These collaborations can provide valuable insights and support throughout the process.
Continuous Monitoring and Improvement
Implementing FDM is not a one-time effort. Continuous monitoring and regular assessments are necessary to ensure the system remains efficient and effective. Manufacturers should also seek opportunities for ongoing improvements.
The Role of Japanese Suppliers in FDM Adoption
Japanese suppliers play a pivotal role in the adoption of FDM technology within manufacturing. Their commitment to quality and innovation supports manufacturers in achieving their operational goals.
Quality Assurance
Japanese suppliers are known for their stringent quality control measures. This reliability ensures that manufacturers receive high-quality FDM components, reducing the risk of system failures.
Innovation and R&D
Japanese manufacturers often lead in research and development, continuously improving FDM technology. Partnering with these suppliers allows manufacturers to access the latest advancements and maintain a competitive edge.
Responsive Support
Japanese suppliers typically offer excellent customer support, providing timely assistance and solutions to any issues that arise during the implementation and operation of FDM systems.
Case Studies: Successful FDM Implementation in Japanese Manufacturing
Examining real-world examples of FDM implementation can provide valuable insights into best practices and potential challenges.
Automotive Industry
A leading Japanese automotive manufacturer integrated FDM into their assembly line communication systems. This integration resulted in a 20% increase in production efficiency and a significant reduction in communication-related downtimes.
Electronics Manufacturing
A prominent electronics manufacturer in Japan adopted FDM for real-time monitoring of their production processes. The implementation led to improved data accuracy and enhanced quality control, resulting in higher product reliability.
Future Trends in FDM and Japanese Manufacturing
The future of FDM in Japanese manufacturing looks promising, with several trends shaping its development and adoption.
Integration with IoT
The Internet of Things (IoT) is expected to enhance FDM applications in manufacturing. By connecting machines and devices through IoT, FDM can facilitate more sophisticated data management and automation.
Artificial Intelligence and FDM
Artificial intelligence (AI) can complement FDM by analyzing the vast amounts of data transmitted through the system. AI-driven insights can lead to more informed decision-making and predictive maintenance strategies.
Sustainability and FDM
Sustainable manufacturing practices are becoming increasingly important. FDM can contribute to sustainability by optimizing resource usage and reducing waste through more efficient data management and machine operation.
Conclusion
Japanese manufacturing continues to lead the way in integrating advanced technologies like Frequency Division Multiplexing to revolutionize the industry. By leveraging FDM, manufacturers can achieve enhanced efficiency, improved accuracy, and scalable operations. Despite some challenges, the benefits of FDM make it a valuable investment for forward-thinking companies. Effective supplier negotiation, adherence to best practices, and a focus on continuous improvement are crucial for successful implementation. As technology evolves, the synergy between FDM, IoT, AI, and sustainability will further solidify Japan’s position at the forefront of manufacturing innovation.
資料ダウンロード
QCD調達購買管理クラウド「newji」は、調達購買部門で必要なQCD管理全てを備えた、現場特化型兼クラウド型の今世紀最高の購買管理システムとなります。
ユーザー登録
調達購買業務の効率化だけでなく、システムを導入することで、コスト削減や製品・資材のステータス可視化のほか、属人化していた購買情報の共有化による内部不正防止や統制にも役立ちます。
NEWJI DX
製造業に特化したデジタルトランスフォーメーション(DX)の実現を目指す請負開発型のコンサルティングサービスです。AI、iPaaS、および先端の技術を駆使して、製造プロセスの効率化、業務効率化、チームワーク強化、コスト削減、品質向上を実現します。このサービスは、製造業の課題を深く理解し、それに対する最適なデジタルソリューションを提供することで、企業が持続的な成長とイノベーションを達成できるようサポートします。
オンライン講座
製造業、主に購買・調達部門にお勤めの方々に向けた情報を配信しております。
新任の方やベテランの方、管理職を対象とした幅広いコンテンツをご用意しております。
お問い合わせ
コストダウンが利益に直結する術だと理解していても、なかなか前に進めることができない状況。そんな時は、newjiのコストダウン自動化機能で大きく利益貢献しよう!
(Β版非公開)