- お役立ち記事
- For mid-level employees in the design department! Introduction of PLM (Product Lifecycle Management) considering the product lifecycle
For mid-level employees in the design department! Introduction of PLM (Product Lifecycle Management) considering the product lifecycle
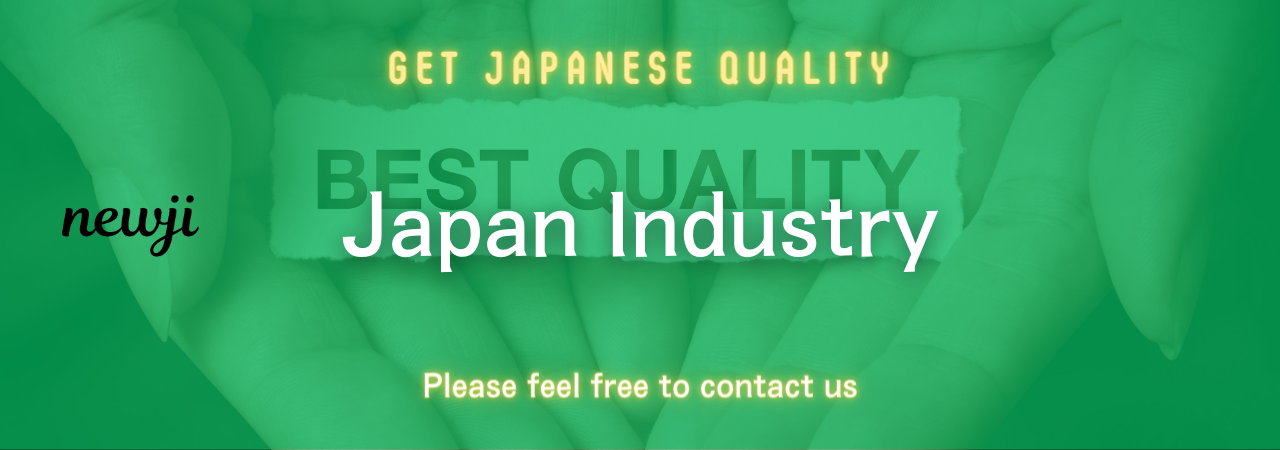
目次
Understanding Product Lifecycle Management (PLM)
Product Lifecycle Management, or PLM, is a strategic process employed by companies, especially in the design and manufacturing sectors.
It involves managing the complete lifecycle of a product from inception, through engineering design and manufacturing, to service and disposal.
PLM integrates people, data, processes, and business systems and provides a digital thread for managing information across the lifecycle of a product.
For mid-level employees in the design department, understanding PLM is crucial as it enhances collaboration, innovation, and efficiency in the product development processes.
It serves as a crucial tool for ensuring that all stakeholders have access to accurate and up-to-date product information, improving decision-making and reducing time to market.
The Importance of Considering Product Lifecycle
Before diving into how PLM can aid in managing the product lifecycle, it is essential to understand why considering the product lifecycle is important.
The lifecycle of a product typically involves several stages: development, growth, maturity, and decline.
Each of these stages presents unique challenges and opportunities, and managing them effectively can make a significant difference in the overall success of a product.
Considering the product lifecycle allows companies to anticipate these challenges and capitalize on opportunities, optimizing resources and enhancing return on investment.
For example, during the growth phase, a company can focus on scaling production and optimizing supply chains.
In the maturity phase, the focus might shift to improving product features and customer satisfaction to maintain market share.
Integrating PLM into these stages ensures that the process is streamlined and coherent, fostering a more dynamic response to market and internal changes.
Key Benefits of PLM for the Design Department
For mid-level employees in the design department, PLM offers several tangible benefits that enhance productivity and product quality.
1. Enhanced Collaboration
PLM facilitates better collaboration among cross-functional teams by providing a centralized platform for accessing product data.
This centralized access ensures that designers, engineers, and other stakeholders are working with the same information, reducing the risk of errors and miscommunication.
By ensuring everyone is on the same page, PLM can significantly streamline the design process and bring products to market more quickly.
2. Improved Quality and Compliance
PLM systems often come with integrated tools for managing quality standards and regulatory compliance.
For the design department, this means that any product design undergoes thorough checks to ensure it meets necessary industry standards before it reaches production.
Ensuring compliance early in the design process can save resources and prevent costly revisions later.
3. Efficient Change Management
The design phase is often subject to numerous changes based on feedback from testing, marketing, and other departments.
PLM systems provide robust change management capabilities that help track these design changes, maintain version control, and document the reasons for each change.
This feature allows designers to make necessary adjustments without losing track of prior versions or the rationale behind decisions.
Implementing PLM: A Step-by-Step Guide
Implementing PLM in the design department is a strategic decision that requires careful planning and execution.
Here’s a step-by-step guide for staff to effectively integrate PLM into their workflow:
1. Assess Needs and Objectives
Start by understanding the specific needs of your design department and how PLM can meet those needs.
Are there particular pain points in your current processes, such as delays or quality issues, that you hope PLM will address?
Define clear objectives that PLM implementation can achieve.
2. Select the Right PLM Software
Not all PLM systems are created equal; thus, selecting the right one is crucial.
Consider factors such as ease of use, integration with existing systems, scalability, customization options, and cost.
Engage with vendors, request demos, and solicit feedback from potential users within the department to make an informed choice.
3. Plan the Implementation
Create a detailed implementation plan that outlines timelines, responsibilities, and key milestones.
Ensure that all team members understand the process and their roles in carrying it out.
This plan should also include a training schedule to ensure that everyone is comfortable using the new system.
4. Train Your Team
Invest in thorough training for all users of the PLM system.
This training should cover both the technical aspects of using the system and the cultural impact of PLM within the organization.
Encouraging open communication and feedback during the training phase can help identify potential issues early on.
5. Monitor and Refine
After implementation, continuously monitor the system’s performance against the objectives defined earlier.
Solicit feedback from users to identify areas for improvement and refine processes accordingly.
PLM is not a static tool but a dynamic system that should evolve to meet the changing needs of the organization.
Conclusion
For mid-level employees in the design department, the introduction of PLM considering the product lifecycle can significantly transform how products are designed, developed, and brought to market.
By enhancing collaboration, improving quality, and enabling efficient change management, PLM serves as a powerful tool in navigating the complexities of modern product development.
With careful planning and execution, the integration of PLM can provide a competitive advantage that drives innovation and efficiency across the organization.
資料ダウンロード
QCD調達購買管理クラウド「newji」は、調達購買部門で必要なQCD管理全てを備えた、現場特化型兼クラウド型の今世紀最高の購買管理システムとなります。
ユーザー登録
調達購買業務の効率化だけでなく、システムを導入することで、コスト削減や製品・資材のステータス可視化のほか、属人化していた購買情報の共有化による内部不正防止や統制にも役立ちます。
NEWJI DX
製造業に特化したデジタルトランスフォーメーション(DX)の実現を目指す請負開発型のコンサルティングサービスです。AI、iPaaS、および先端の技術を駆使して、製造プロセスの効率化、業務効率化、チームワーク強化、コスト削減、品質向上を実現します。このサービスは、製造業の課題を深く理解し、それに対する最適なデジタルソリューションを提供することで、企業が持続的な成長とイノベーションを達成できるようサポートします。
オンライン講座
製造業、主に購買・調達部門にお勤めの方々に向けた情報を配信しております。
新任の方やベテランの方、管理職を対象とした幅広いコンテンツをご用意しております。
お問い合わせ
コストダウンが利益に直結する術だと理解していても、なかなか前に進めることができない状況。そんな時は、newjiのコストダウン自動化機能で大きく利益貢献しよう!
(Β版非公開)