- お役立ち記事
- A must-see for quality assurance department managers! A data-driven quality improvement approach using seven new QC tools
月間76,176名の
製造業ご担当者様が閲覧しています*
*2025年3月31日現在のGoogle Analyticsのデータより
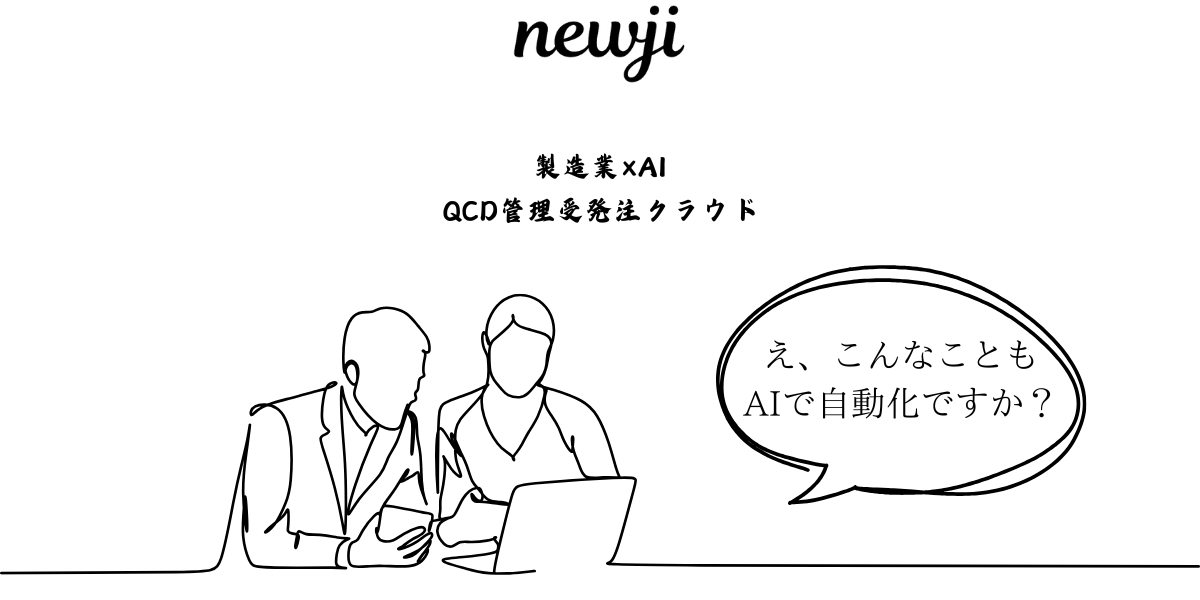
A must-see for quality assurance department managers! A data-driven quality improvement approach using seven new QC tools
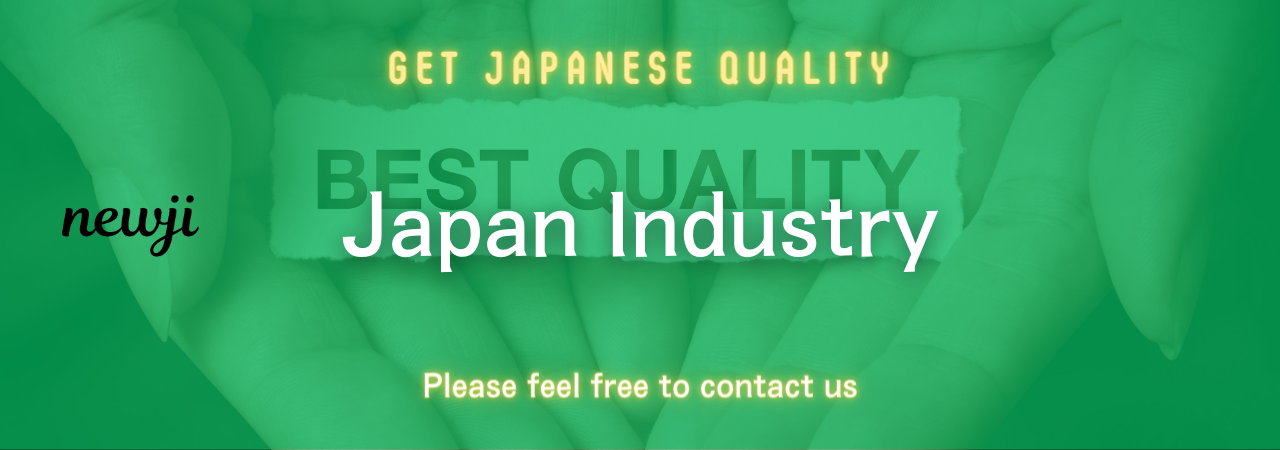
目次
Introduction to Quality Improvement
The world of manufacturing and production is ever-evolving, and the demand for high-quality products has never been more prominent.
Companies aim to provide products that not only meet but exceed customer expectations.
This constant pursuit of perfection has led to the development of various quality control methodologies.
Among these, the seven new QC tools play a crucial role in ensuring quality improvements in a data-driven way.
These tools are invaluable for quality assurance department managers who are keen on adopting innovative strategies to enhance their processes.
What Are the Seven New QC Tools?
Before diving deeper into how these tools can aid in quality improvement, let’s first understand what these tools are.
Unlike the traditional QC tools such as the histogram or cause-and-effect diagram, the seven new QC tools focus on managing and processing complex data and information.
These tools include:
1. Affinity Diagrams
2. Interrelationship Diagrams
3. Tree Diagrams
4. Prioritization Matrices
5. Matrix Diagrams
6. Process Decision Program Charts (PDPC)
7. Activity Network Diagrams
These tools are designed to help managers approach quality tasks methodically, thus ensuring a thorough evaluation of processes and systems.
Affinity Diagrams: Organizing Ideas
The Affinity Diagram is used to organize a large amount of data or ideas into grouped themes.
This tool is particularly useful in brainstorming sessions for quality improvement projects.
It allows team members to sort scattered thoughts into natural clusters, leading to clearer insights.
For a quality assurance manager, using an Affinity Diagram can reveal the root causes of quality issues and guide necessary actions.
Interrelationship Diagrams: Understanding Connections
Interrelationship Diagrams help in identifying cause-and-effect relationships within a set of factors.
This is essential for understanding how different variables impact the quality of a product.
By using this diagram, quality managers can visualize complex relationships and pinpoint key issues that require attention.
This tool aids in developing strategies that can effectively address multiple issues simultaneously.
Tree Diagrams: Breaking Down the Details
Tree Diagrams are excellent for breaking down broad goals into detailed, actionable steps.
For quality improvement purposes, they allow managers to map out a comprehensive view of the steps required to achieve a certain quality standard.
This clarity in planning ensures that efforts are focused and coordinated, leading to more efficient quality enhancement processes.
Prioritization Matrices: Focusing on the Essential
To make the most of limited resources, quality managers need to prioritize tasks.
The Prioritization Matrix facilitates this by comparing various quality-related activities and determining their significance based on several criteria.
This systematic approach ensures that the most impactful tasks receive immediate attention, thereby driving substantial improvements in product quality.
Matrix Diagrams: Comparing Data
Matrix Diagrams are used to analyze relationships between different data sets.
By laying out data in a matrix format, quality managers can identify correlations that might not be immediately obvious.
This aids in comprehensive decision-making by providing insights into how different factors influence each other, enabling managers to optimize quality control processes effectively.
Process Decision Program Charts (PDPC): Planning for Contingencies
PDPCs are important for planning out potential problems and solutions in advance.
This tool encourages quality managers to think ahead and prepare for uncertainties that might arise during a project.
Having a well-thought-out contingency plan ensures that quality processes remain uninterrupted even when unexpected challenges occur.
Activity Network Diagrams: Managing Timelines
The Activity Network Diagram is a scheduling tool that helps manage project timelines effectively.
For quality assurance tasks, it ensures that activities are carried out in the correct sequence, helping to avoid delays.
Completing tasks on time is crucial for maintaining the quality standards a company strives for.
Implementing the New QC Tools for Quality Improvement
Now that we understand what each tool offers, the next step is implementation.
Integrating these tools into daily operations might require a cultural shift within a company, emphasizing data-driven decision-making and continuous improvement.
Training and Development: Quality managers should invest in training their teams to use these tools efficiently.
Understanding the nuances of each tool and knowing when and how to apply them can significantly enhance their effectiveness.
Continuous Monitoring: Regularly using these QC tools will ensure constant monitoring of quality processes.
This helps in timely identification and resolution of issues, allowing companies to maintain high quality standards.
Data-Driven Culture: Encouraging a data-driven approach in quality assurance promotes transparency and accuracy in decision-making.
This cultural shift will foster an environment of learning and growth, where data guides all major improvements.
Feedback and Adjustment: Implementing these tools is not a one-time task but rather an ongoing process.
Gather feedback from team members and adjust the use of these tools to suit the evolving needs of the company.
Conclusion
For quality assurance department managers eager to drive significant quality improvements, the seven new QC tools offer a robust framework.
These tools allow managers to harness the power of data in a structured manner, enabling more effective and strategic quality control.
By adopting these tools, companies can stay ahead in the competitive market, consistently delivering products that meet the high standards of their customers.
It’s time for quality assurance teams to embrace these innovative tools and lead their organizations toward operational excellence.
資料ダウンロード
QCD管理受発注クラウド「newji」は、受発注部門で必要なQCD管理全てを備えた、現場特化型兼クラウド型の今世紀最高の受発注管理システムとなります。
ユーザー登録
受発注業務の効率化だけでなく、システムを導入することで、コスト削減や製品・資材のステータス可視化のほか、属人化していた受発注情報の共有化による内部不正防止や統制にも役立ちます。
NEWJI DX
製造業に特化したデジタルトランスフォーメーション(DX)の実現を目指す請負開発型のコンサルティングサービスです。AI、iPaaS、および先端の技術を駆使して、製造プロセスの効率化、業務効率化、チームワーク強化、コスト削減、品質向上を実現します。このサービスは、製造業の課題を深く理解し、それに対する最適なデジタルソリューションを提供することで、企業が持続的な成長とイノベーションを達成できるようサポートします。
製造業ニュース解説
製造業、主に購買・調達部門にお勤めの方々に向けた情報を配信しております。
新任の方やベテランの方、管理職を対象とした幅広いコンテンツをご用意しております。
お問い合わせ
コストダウンが利益に直結する術だと理解していても、なかなか前に進めることができない状況。そんな時は、newjiのコストダウン自動化機能で大きく利益貢献しよう!
(β版非公開)