- お役立ち記事
- Optimizing Manufacturing Processes through Benchmarking Methods
Optimizing Manufacturing Processes through Benchmarking Methods
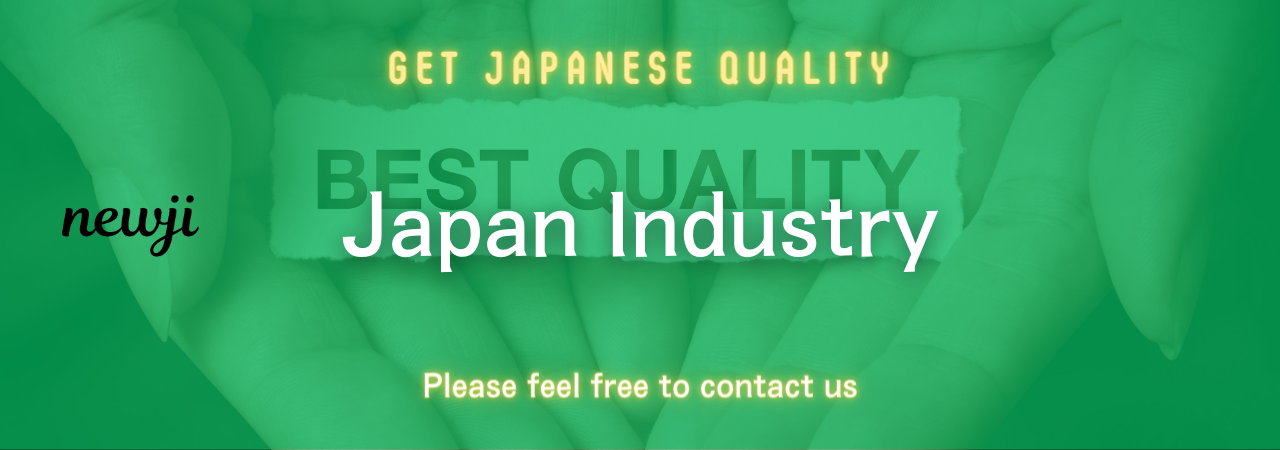
目次
Understanding Benchmarking in Manufacturing
Benchmarking is an essential tool used by manufacturing companies to evaluate and improve their processes.
It involves comparing one’s business processes and performance metrics to industry bests or best practices from other companies.
Such comparisons are crucial for companies that aim to stay competitive and continue delivering high-quality products.
In manufacturing, benchmarking allows organizations to pinpoint inefficiencies and areas of waste.
By analyzing how others in the industry operate, companies can adopt those strategies that enhance productivity and reduce costs.
Consequently, adopting benchmarking methods can lead to significant improvements in output, quality, and overall operational efficiency.
Types of Benchmarking Methods
There are several types of benchmarking methods that manufacturers can employ:
1. Internal Benchmarking
Internal benchmarking involves comparing processes within the same organization.
This can be between different departments, teams, or locations.
It’s a valuable approach when an organization is large and diverse because it helps identify internal best practices that can be scaled across the company.
2. Competitive Benchmarking
With competitive benchmarking, a company compares its processes and performance metrics with those of its direct competitors.
This type of benchmarking is crucial in understanding the competitive landscape and identifying areas where a company might be lagging behind.
3. Functional Benchmarking
Functional benchmarking involves looking at practices in organizations that may not be competitors but operate in similar functions.
For example, a manufacturing company might compare its logistics processes with those of a leading logistics company.
This approach can uncover innovative practices not typically found within the manufacturing sector.
4. Generic Benchmarking
Generic benchmarking looks at the practices of companies in entirely different industries.
The focus here is on finding creative solutions that can be applied to the manufacturing process.
This type of benchmarking requires thinking outside the box, and it can lead to groundbreaking changes.
The Importance of Data in Benchmarking
Data is the cornerstone of effective benchmarking.
Without accurate and relevant data, comparisons are meaningless.
Manufacturers need to collect data on various performance metrics, such as production speed, defect rates, and resource utilization.
Data should be collected consistently over time to observe trends and changes.
Additionally, it is important to ensure the data is comparable – companies should strive to compare like with like, meaning that metrics should be adjusted to reflect differences in scale or market.
Steps to Implement Benchmarking in Manufacturing
To realize the benefits of benchmarking, manufacturers need a structured approach:
1. Identify Areas for Improvement
Before starting, it is crucial to identify which areas of the manufacturing process require improvements.
This can be done through SWOT analysis (Strengths, Weaknesses, Opportunities, Threats) or direct feedback from employees and customers.
2. Choose the Right Benchmark
Depending on the goal, select the most appropriate type of benchmarking.
If aiming to outperform competitors, competitive benchmarking may be the best choice.
For innovation, generic benchmarking could be more suitable.
3. Data Collection and Analysis
Collect relevant data from both the company and the chosen benchmark partners.
This could involve visiting other facilities or consulting research reports.
Once collected, analyze the data to identify gaps and opportunities for improvement.
4. Develop an Action Plan
Create a strategic plan outlining the steps necessary to implement changes.
This includes assigning responsibilities, setting timelines, and defining the resources needed.
The plan should be clear and actionable to ensure successful implementation.
5. Implement Changes
Put the action plan into action.
This involves training employees, changing processes, and possibly investing in new technology or equipment.
Implementation should be monitored closely to ensure changes are made effectively.
6. Monitor and Review
Finally, monitor the results of the changes to assess their impact.
Review the outcomes against initial goals and benchmarks to measure success.
Regular review sessions can help maintain continuous improvement and ensure a company remains agile in its operations.
Overcoming Challenges in Benchmarking
Benchmarking can present several challenges.
These include resistance to change within an organization, issues with data confidentiality, and variations in processes across different companies.
Overcoming these requires strong leadership, a transparent culture open to change, and ensuring data protection agreements when partnering with other entities for benchmarking purposes.
The Role of Technology in Benchmarking
Technology plays a pivotal role in modern benchmarking.
Advanced data analytics tools and software can rapidly process and analyze large sets of data.
Moreover, technology can facilitate virtual benchmarking, where companies use digital twinning and simulations to benchmark processes without physical visits.
Ultimately, embracing technology in benchmarking allows faster and more accurate assessments, leading to quicker implementation of improvements.
Conclusion
Benchmarking in manufacturing is a powerful method for optimizing processes.
By learning from both competitors and non-competitors, manufacturers can adopt the best processes and practices available, driving both efficiency and innovation.
With careful planning, data collection, and action, benchmarking can lead to substantial gains in production capability and market position.
資料ダウンロード
QCD調達購買管理クラウド「newji」は、調達購買部門で必要なQCD管理全てを備えた、現場特化型兼クラウド型の今世紀最高の購買管理システムとなります。
ユーザー登録
調達購買業務の効率化だけでなく、システムを導入することで、コスト削減や製品・資材のステータス可視化のほか、属人化していた購買情報の共有化による内部不正防止や統制にも役立ちます。
NEWJI DX
製造業に特化したデジタルトランスフォーメーション(DX)の実現を目指す請負開発型のコンサルティングサービスです。AI、iPaaS、および先端の技術を駆使して、製造プロセスの効率化、業務効率化、チームワーク強化、コスト削減、品質向上を実現します。このサービスは、製造業の課題を深く理解し、それに対する最適なデジタルソリューションを提供することで、企業が持続的な成長とイノベーションを達成できるようサポートします。
オンライン講座
製造業、主に購買・調達部門にお勤めの方々に向けた情報を配信しております。
新任の方やベテランの方、管理職を対象とした幅広いコンテンツをご用意しております。
お問い合わせ
コストダウンが利益に直結する術だと理解していても、なかなか前に進めることができない状況。そんな時は、newjiのコストダウン自動化機能で大きく利益貢献しよう!
(Β版非公開)