- お役立ち記事
- A must-see for equipment maintenance department managers! How to reduce equipment downtime using reliability testing
A must-see for equipment maintenance department managers! How to reduce equipment downtime using reliability testing
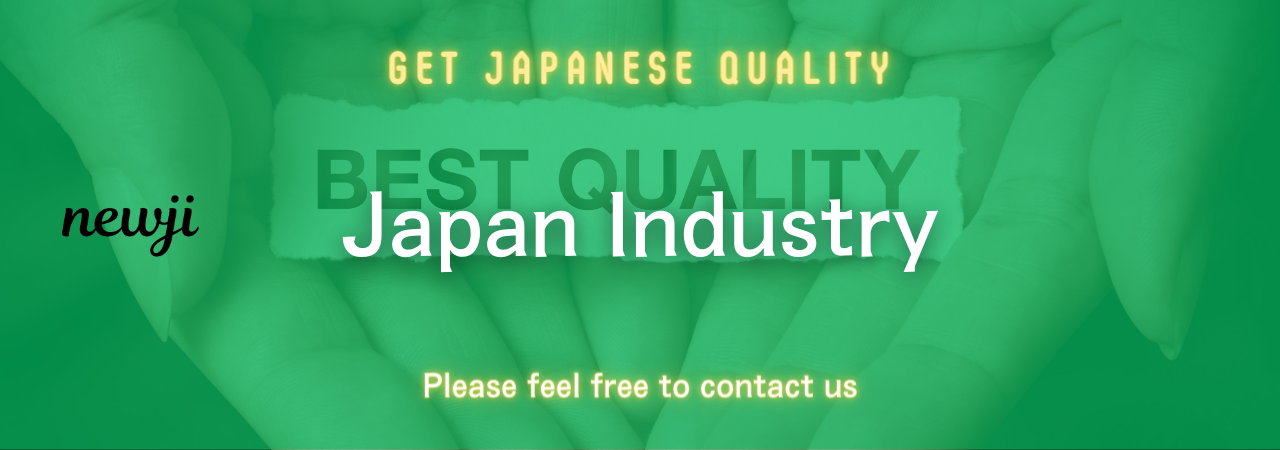
目次
Understanding Equipment Downtime
Equipment downtime is a critical concern in any industry that relies heavily on machinery and equipment for production and operations.
Simply put, downtime refers to periods when equipment is not operational.
This can be due to various reasons such as technical failures, maintenance, or lack of parts.
The impact of equipment downtime can be significant, leading to delays in production, increased costs, and reduced profitability.
For maintenance department managers, minimizing downtime is a crucial aspect of ensuring smooth operations and achieving targets.
Understanding the factors that contribute to downtime is the first step in tackling this problem.
The Role of Reliability Testing
Reliability testing plays a vital role in reducing equipment downtime.
At its core, reliability testing aims to determine the probability of a machine performing its intended function without failure over a specified period.
By understanding how and why equipment fails, maintenance teams can take proactive measures to prevent breakdowns before they occur.
Reliability testing typically involves several techniques and methodologies, each designed to assess different aspects of equipment performance.
These may include accelerated life testing, failure mode effects analysis, and environmental testing, among others.
Benefits of Reliability Testing
Implementing reliability testing can offer numerous benefits to companies looking to reduce downtime.
Some of these benefits include:
– **Improved Predictive Maintenance**: By identifying potential failure points, maintenance teams can plan and execute timely maintenance activities, reducing the likelihood of unexpected breakdowns.
– **Cost Savings**: Reducing the occurrence of unforeseen equipment failures can lead to significant cost savings.
Avoiding emergency repairs and minimizing production stoppages contribute to improved financial performance.
– **Extended Equipment Life**: By ensuring that equipment is maintained in optimum condition, reliability testing can help extend the usable life of machinery, delaying the need for costly replacements.
– **Enhanced Safety**: Reliability testing helps identify potential safety hazards that may arise from equipment malfunction, ensuring a safer work environment.
Implementing Reliability Testing in Your Maintenance Strategy
For maintenance department managers looking to leverage reliability testing, implementing a structured approach is essential.
Here’s how you can incorporate reliability testing into your maintenance strategy:
1. Identify Critical Equipment
Begin by identifying the critical equipment and machinery in your operations.
These are the pieces of equipment whose failure would cause the most significant impact on production.
Prioritize these for reliability testing efforts.
2. Develop a Testing Plan
Create a comprehensive reliability testing plan that outlines the methodologies to be used, the frequency of testing, and the key performance metrics to track.
The plan should be specific to each piece of equipment, considering its unique operating conditions and potential failure modes.
3. Conduct Regular Testing
Implement a schedule for regular reliability testing on identified equipment.
Consistent testing allows for the early detection of potential issues and helps track the health and performance of machinery over time.
4. Analyze and Interpret Results
Once testing is conducted, analyze the results to identify trends, patterns, and potential areas for improvement.
Work with your team to interpret the data and develop actionable insights.
5. Implement Proactive Measures
Based on the results of reliability testing, take proactive measures to address identified issues.
This might involve adjusting maintenance schedules, performing corrective maintenance, or investing in training for your team.
Building a Culture of Reliability
Beyond the technical aspects of reliability testing, fostering a culture of reliability within your maintenance department is critical for long-term success.
This involves not only implementing best practices but also engaging with your team and other stakeholders in promoting the importance of reliability.
1. Encourage Collaboration
Promote collaboration between maintenance, operations, and engineering teams.
By working together, each department can contribute valuable insights and expertise to the reliability testing process.
2. Invest in Training
Provide training opportunities for your maintenance team to deepen their understanding of reliability concepts and techniques.
This not only enhances their skills but also empowers them to take ownership of equipment reliability initiatives.
3. Reward and Recognize
Celebrate success and recognize individuals and teams who contribute to reducing downtime and promoting reliability.
Acknowledgment and rewards can motivate staff and reinforce a culture of continuous improvement.
Conclusion
Reducing equipment downtime is a priority for any effective maintenance department manager.
By leveraging reliability testing, managers can improve the reliability and performance of their equipment, leading to increased productivity, cost savings, and enhanced safety.
Combining technical strategies with a culture of accountability and continuous learning can make a significant difference in achieving long-term operational excellence.
By implementing the steps outlined above, you can foster a proactive maintenance environment that keeps equipment running at peak performance and contributes to your organization’s success.
資料ダウンロード
QCD調達購買管理クラウド「newji」は、調達購買部門で必要なQCD管理全てを備えた、現場特化型兼クラウド型の今世紀最高の購買管理システムとなります。
ユーザー登録
調達購買業務の効率化だけでなく、システムを導入することで、コスト削減や製品・資材のステータス可視化のほか、属人化していた購買情報の共有化による内部不正防止や統制にも役立ちます。
NEWJI DX
製造業に特化したデジタルトランスフォーメーション(DX)の実現を目指す請負開発型のコンサルティングサービスです。AI、iPaaS、および先端の技術を駆使して、製造プロセスの効率化、業務効率化、チームワーク強化、コスト削減、品質向上を実現します。このサービスは、製造業の課題を深く理解し、それに対する最適なデジタルソリューションを提供することで、企業が持続的な成長とイノベーションを達成できるようサポートします。
オンライン講座
製造業、主に購買・調達部門にお勤めの方々に向けた情報を配信しております。
新任の方やベテランの方、管理職を対象とした幅広いコンテンツをご用意しております。
お問い合わせ
コストダウンが利益に直結する術だと理解していても、なかなか前に進めることができない状況。そんな時は、newjiのコストダウン自動化機能で大きく利益貢献しよう!
(Β版非公開)