- お役立ち記事
- A must-see for new employees in the quality control department! Basics and application examples of SQC (statistical quality control)
A must-see for new employees in the quality control department! Basics and application examples of SQC (statistical quality control)
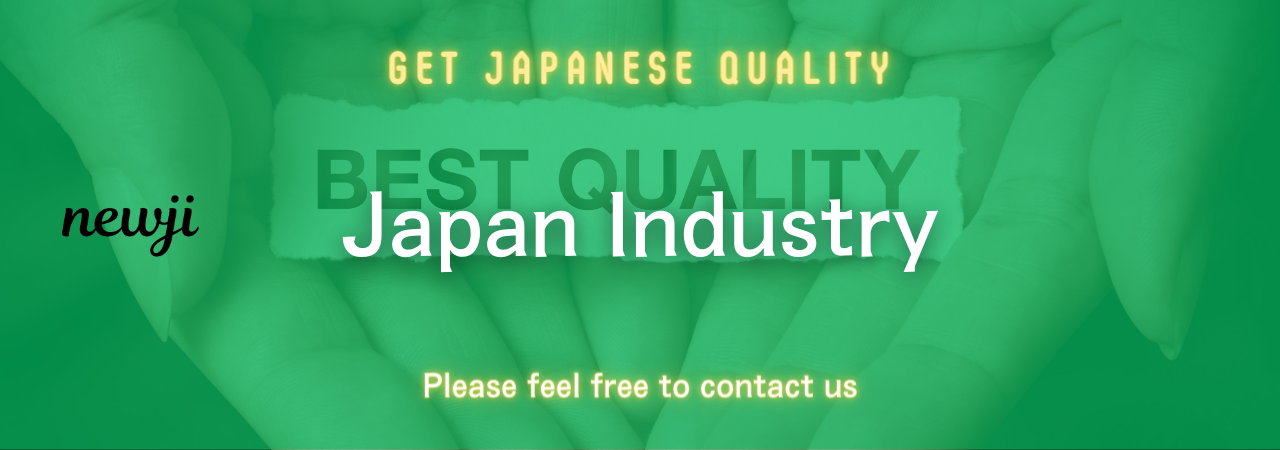
目次
Understanding SQC: A Foundation for New Quality Control Employees
As a new employee in the quality control department, you’re about to embark on an important journey in ensuring the quality and reliability of products.
Understanding Statistical Quality Control (SQC) is crucial for this role.
Let’s dive into the basics and see how SQC can be applied effectively in your work.
What is Statistical Quality Control (SQC)?
Statistical Quality Control is a method that uses statistical methods to monitor and control a process.
SQC helps ensure that the process operates at its full potential to produce conforming products.
When any element of the process varies beyond acceptable limits, SQC methods can help identify and correct these deviations.
The Importance of SQC in Quality Control
SQC is fundamental in maintaining product quality in manufacturing and service industries.
By employing data-driven techniques, it reduces variability, prevents defects, and improves the overall operational efficiency.
For new employees, mastering SQC is critical to delivering high-quality products that meet customer expectations and industry standards.
Key Concepts of SQC
Here are a few key concepts you’ll need to understand as you start utilizing SQC in your work:
Basic Statistical Tools
1. **Control Charts**: These are used to plot data over time to look for trends or variations in the process.
2. **Histograms**: Histograms depict the frequency distribution of data points.
They provide insights into the variability and distribution of process output.
3. **Pareto Analysis**: This tool helps prioritize problems to determine which have the greatest impact on quality.
Types of Variation
Understanding variation is essential to SQC.
There are two types:
– **Common Cause Variation**: This type of variation is inherent to the process itself.
It is predictable and consistent over time.
– **Special Cause Variation**: This variation arises from external factors and is often unpredictable.
Identifying and eliminating special cause variations is a crucial step in process improvement.
Process Capability
This concept helps you evaluate how well a process can produce output within specified limits.
Process capability analysis bridges the gap between user demands and production limitations.
It shows whether a process is capable of meeting customer requirements consistently.
Practical Applications of SQC
Now that you have an understanding of SQC fundamentals, let’s explore how these techniques can be applied in your quality control responsibilities.
Control Chart Applications
Control charts are vital for real-time monitoring of production processes.
For instance, if you are manufacturing auto parts, a control chart can help track the diameter of a specific part.
By plotting sample results over time, you can quickly identify deviations from the standard and make necessary adjustments before producing defective pieces.
Using Histograms for Process Analysis
Histograms can help you analyze the distribution of product dimensions or weight.
Suppose you are responsible for packaging products of a specific weight.
Using histograms, you can assess whether the weights are consistently falling within the acceptable range, making it easier to spot any anomalies and prevent packaging errors.
Pareto Analysis for Problem Solving
Implementing Pareto analysis allows you to focus your efforts on the most significant issues.
For example, if your department faces frequent customer complaints, a Pareto analysis can pinpoint the most common reasons.
By addressing these primary causes, you can significantly improve customer satisfaction and reduce complaints.
Incorporating SQC into Daily Quality Control Activities
To maximize the benefits of SQC, integrate it into your daily routine.
This integration involves collaboration across teams and a commitment to continual improvement.
Regular Training and Skill Development
Embrace opportunities for training and workshops related to SQC.
Participating in these activities will enhance your understanding and application of statistical tools, keeping you updated with the latest practices.
Data-Driven Decision Making
Make it a habit to base decisions on data rather than intuitions.
By relying on SQC tools, you can make informed decisions that lead to better processes and product quality.
Collaboration with Cross-Functional Teams
Quality control is not an isolated task.
Effective SQC involves working with engineering, production, and other departments to resolve issues and implement solutions.
Conclusion: Your Role in SQC
As a new employee in the quality control department, you play a crucial role in maintaining and improving product quality.
By mastering the basics of SQC, understanding its key concepts, and applying them effectively in your work, you can make significant contributions to your team’s success.
Remember, continual learning and a commitment to data-driven solutions will make you a valuable asset to your organization.
Welcome to the dynamic and essential world of quality control!
資料ダウンロード
QCD調達購買管理クラウド「newji」は、調達購買部門で必要なQCD管理全てを備えた、現場特化型兼クラウド型の今世紀最高の購買管理システムとなります。
ユーザー登録
調達購買業務の効率化だけでなく、システムを導入することで、コスト削減や製品・資材のステータス可視化のほか、属人化していた購買情報の共有化による内部不正防止や統制にも役立ちます。
NEWJI DX
製造業に特化したデジタルトランスフォーメーション(DX)の実現を目指す請負開発型のコンサルティングサービスです。AI、iPaaS、および先端の技術を駆使して、製造プロセスの効率化、業務効率化、チームワーク強化、コスト削減、品質向上を実現します。このサービスは、製造業の課題を深く理解し、それに対する最適なデジタルソリューションを提供することで、企業が持続的な成長とイノベーションを達成できるようサポートします。
オンライン講座
製造業、主に購買・調達部門にお勤めの方々に向けた情報を配信しております。
新任の方やベテランの方、管理職を対象とした幅広いコンテンツをご用意しております。
お問い合わせ
コストダウンが利益に直結する術だと理解していても、なかなか前に進めることができない状況。そんな時は、newjiのコストダウン自動化機能で大きく利益貢献しよう!
(Β版非公開)