- お役立ち記事
- Basics of the Toyota Production System and on-site applications that new employees in the production technology department should know
Basics of the Toyota Production System and on-site applications that new employees in the production technology department should know
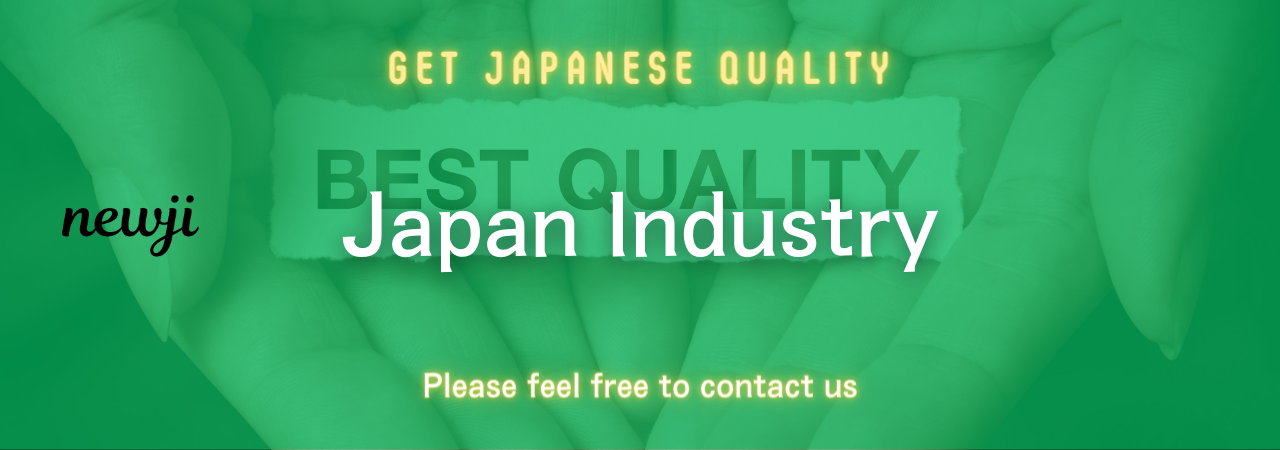
目次
Understanding the Toyota Production System
The Toyota Production System (TPS) is an integrated socio-technical system, developed by Toyota, that comprises its management philosophy and practices.
The system efficiently organizes manufacturing and logistics for the automobile manufacturer, including the interaction with suppliers and customers.
The main objective of TPS is to eliminate waste and improve productivity while maintaining value.
This approach is rooted in two key concepts: “Just-In-Time” (JIT) and “Jidoka.”
Just-In-Time (JIT)
Just-In-Time is primarily about producing only what is needed, when it is needed, and in the amount needed.
The goal here is to minimize the time products are sitting stagnant at any point in the production process.
JIT aims to improve a business’s return on investment by reducing in-process inventory and its associated carrying costs.
This approach not only helps in reducing waste but also in improving the flow of materials throughout the organization.
It enhances the company’s responsiveness to customer demands, making the system dynamic and flexible.
Jidoka
Jidoka is a practice that enables machines and operators to stop work immediately when a problem is found.
The principle is that quality should be built into the production process.
When a mistake is detected, production is halted and an investigation is started to find the root cause.
This approach ensures that defective products are not passed to the next stage in production.
The benefits of Jidoka include increased quality assurance and reduction in potential defective products reaching the customer.
On-Site Applications for New Employees
For new employees in the production technology department, it’s crucial to understand how TPS is applied on-site.
These applications are not only theoretical concepts but practical guidelines that must be implemented consistently.
Value Stream Mapping
Value Stream Mapping is a tool that allows the visualization of the flow of materials and information as a product or service makes its way through the value stream.
New employees should learn to map the current state and design a future state for the series of events that take a product from the beginning of the process to customer delivery.
This tool helps in identifying and eliminating waste, thus improving efficiency.
5S Methodology
5S is a workplace organization method that includes five phases: Sort, Set in order, Shine, Standardize, and Sustain.
The implementation of 5S helps in creating and maintaining an organized, clean, and efficient work environment.
It is an essential part of the TPS that contributes to waste reduction and maximizes efficiency.
Learning and applying 5S is crucial for new employees as it is a foundation for continuous improvement.
Kaizen
Kaizen, meaning “continuous improvement,” is the practice of constantly refining and improving processes.
For a new employee, engaging in kaizen means actively seeking small, incremental changes that lead to substantial improvements over time.
In practice, this involves participating in regular team meetings to identify improvement opportunities and propose solutions.
Kaizen fosters a culture where employees at all levels are contributing ideas and solutions to problems.
Practical Benefits of TPS
Understanding and implementing TPS has notable benefits for both new employees and the organization.
Waste Reduction
One of the most significant advantages of implementing TPS is the reduction of waste.
This waste includes excess inventory, unnecessary movements, and overproduction.
By adhering to principles like JIT and Jidoka, organizations minimize these inefficiencies, leading to reduced costs and improved resources utilization.
Improved Quality
TPS ensures that problems are identified and rectified at their source, thus improving the overall quality of the products.
This reduction in defects leads to higher customer satisfaction and fewer returns or recalls.
Increased Efficiency
The TPS framework leads to increased efficiency in operations.
Employees are well-versed in identifying waste, utilizing resources better, and streamlining processes, which contributes to higher productivity.
Teamwork and Employee Satisfaction
TPS promotes an environment of teamwork by involving employees at all levels in the process of improvement.
Employees feel valued as they are part of the decision-making process, which can lead to higher morale and job satisfaction.
Challenges and Considerations
While TPS is beneficial, there are challenges to consider, especially for new employees.
Change management and getting accustomed to the TPS culture can be daunting.
It requires dedication, willingness to learn, and adaptability.
It is essential for new employees to understand that TPS is a continuous process that requires ongoing commitment and effort.
Conclusion
The Toyota Production System is more than a collection of techniques and tools.
It is a comprehensive framework aimed at driving efficiency by eliminating waste and empowering operators to make quality contributions.
For new employees in production technology, understanding and implementing TPS principles is crucial.
It offers opportunities for personal development and contributes substantially to the organization’s success.
Embracing these principles sets a foundation for a successful career in manufacturing and production technology.
資料ダウンロード
QCD調達購買管理クラウド「newji」は、調達購買部門で必要なQCD管理全てを備えた、現場特化型兼クラウド型の今世紀最高の購買管理システムとなります。
ユーザー登録
調達購買業務の効率化だけでなく、システムを導入することで、コスト削減や製品・資材のステータス可視化のほか、属人化していた購買情報の共有化による内部不正防止や統制にも役立ちます。
NEWJI DX
製造業に特化したデジタルトランスフォーメーション(DX)の実現を目指す請負開発型のコンサルティングサービスです。AI、iPaaS、および先端の技術を駆使して、製造プロセスの効率化、業務効率化、チームワーク強化、コスト削減、品質向上を実現します。このサービスは、製造業の課題を深く理解し、それに対する最適なデジタルソリューションを提供することで、企業が持続的な成長とイノベーションを達成できるようサポートします。
オンライン講座
製造業、主に購買・調達部門にお勤めの方々に向けた情報を配信しております。
新任の方やベテランの方、管理職を対象とした幅広いコンテンツをご用意しております。
お問い合わせ
コストダウンが利益に直結する術だと理解していても、なかなか前に進めることができない状況。そんな時は、newjiのコストダウン自動化機能で大きく利益貢献しよう!
(Β版非公開)