- お役立ち記事
- Effective use of quality function deployment (QFD) that quality assurance department leaders should know
Effective use of quality function deployment (QFD) that quality assurance department leaders should know
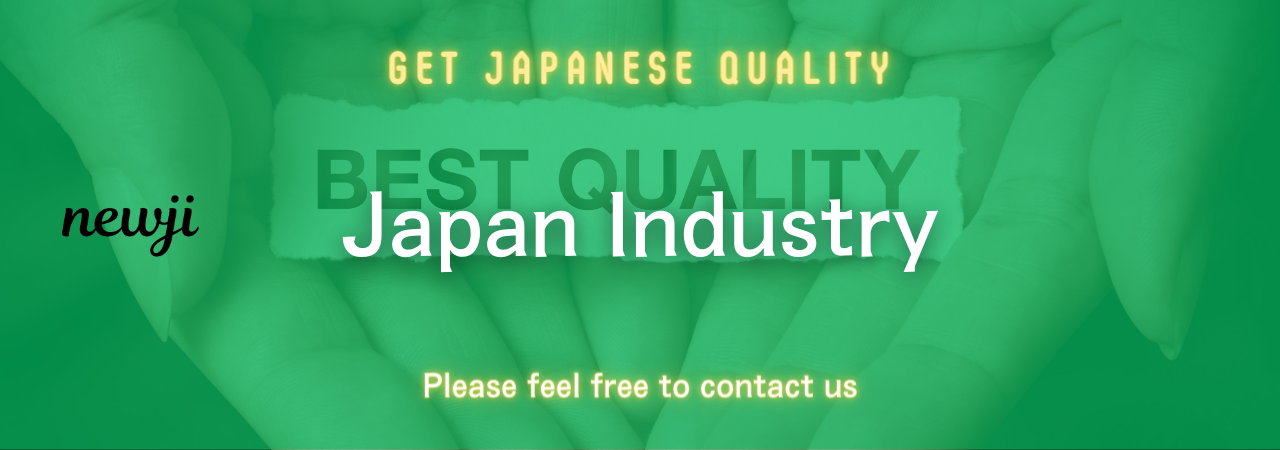
目次
Understanding Quality Function Deployment (QFD)
Quality Function Deployment (QFD) is a powerful methodology used by organizations to ensure that the needs and desires of customers are incorporated into the design and manufacturing of products.
Originating in Japan in the 1960s, it has grown in popularity across the globe due to its effectiveness in bridging the gap between customer expectations and final product quality.
As a quality assurance department leader, understanding and applying QFD can significantly enhance the quality of products and services your company offers.
The Basics of QFD
QFD is sometimes referred to as the “Voice of the Customer” (VOC) process because it centers on capturing and systematically addressing customer requirements.
The method uses a set of matrices to translate customer needs into specific, actionable plans for production and design teams.
This process ensures that every stage of product development aligns with customer expectations, leading to higher satisfaction and fewer costly redesigns.
The primary tool used in QFD is the House of Quality, a matrix that looks somewhat like a house due to its roof-like structure.
This tool helps teams identify the relationships between customer demands and the company’s ability to meet them, providing a clear roadmap for product development.
Implementing QFD in Your Organization
Step 1: Identifying Customer Needs
The first step in implementing QFD is collecting and analyzing the VOC.
This involves engaging with customers through surveys, interviews, focus groups, and other methods to understand what they truly value in your product.
The information gathered should be detailed and precise, providing a clear picture of customer expectations.
Step 2: Developing the House of Quality
Once you have a comprehensive list of customer requirements, these needs are prioritized and organized in the House of Quality matrix.
The matrix links these needs to technical descriptors that specify how the company can meet these demands.
For example, if customers prioritize durability in a product, the company might focus on using strong materials or implementing rigorous testing protocols.
Step 3: Relating Customer Needs to Product Characteristics
The next step is to establish the interrelationships between customer needs and the product’s technical requirements.
This involves assigning weights or ratings to these relationships to identify which product features are most critical in fulfilling customer demands.
This part of the process helps prioritize efforts and resources efficiently.
Step 4: Competitive Analysis
A significant part of QFD is analyzing how your products compare with competitors’.
This involves benchmarking your technical responses against those of competitors to identify strengths and areas for improvement.
This comparative analysis can guide strategic decisions, such as deciding where to differentiate your product in the market.
Benefits of Using QFD
Improved Customer Satisfaction
By systematically incorporating customer feedback into product development, QFD ensures that the final product closely aligns with customer desires.
This leads to increased customer satisfaction, loyalty, and ultimately, a better market position for your company.
Reduction in Development Time and Costs
QFD helps to identify potential issues early in the product development process, reducing the need for costly modifications and redesigns.
By resolving potential mismatches at the planning stage, development teams can streamline their processes, shortening time-to-market and saving on costs.
Enhanced Team Collaboration
The use of QFD promotes a cross-functional approach, bringing together various departments such as design, marketing, engineering, and quality assurance.
This collaboration fosters better communication, alignment, and a shared vision towards fulfilling customer needs.
Challenges in Implementing QFD
Complexity and Resource Intensity
Implementing QFD can be resource-intensive, requiring significant time and effort to accurately gather and analyze customer data.
The process involves multiple stakeholders and can become complex, demanding effective project management skills.
Resistance to Change
Introducing a new methodology like QFD may encounter resistance from employees accustomed to traditional processes.
It requires a shift in mindset towards a more customer-centered approach, which can be challenging for some organizations.
Best Practices for Effective QFD Use
Training and Education
Ensure that all team members are trained in QFD techniques and understand the importance of customer-focused design.
Workshops and seminars can be valuable for building the skills necessary to leverage QFD effectively.
Use of Technology
Utilize modern tools and software to facilitate data collection and analysis.
These technologies can simplify the complex processes involved in QFD, making it easier to implement and manage within your organization.
Regular Updates and Iterations
QFD should not be a one-time effort.
Regular updates based on ongoing customer feedback ensure that the processes remain relevant and continue to address current market demands.
Management Support
Having strong support from upper management is crucial in effectively implementing QFD.
They can provide the necessary resources, align organizational goals, and drive the cultural change needed for successful implementation.
In conclusion, QFD is a transformative tool for quality assurance leaders aiming to deliver superior products that resonate with customer needs.
By systematically capturing and addressing customer requirements, QFD enhances product quality, streamlines development processes, and boosts customer satisfaction.
Despite the challenges involved, with the right strategies and commitment, organizations can reap the many benefits of QFD, positioning themselves for sustained success in competitive markets.
資料ダウンロード
QCD調達購買管理クラウド「newji」は、調達購買部門で必要なQCD管理全てを備えた、現場特化型兼クラウド型の今世紀最高の購買管理システムとなります。
ユーザー登録
調達購買業務の効率化だけでなく、システムを導入することで、コスト削減や製品・資材のステータス可視化のほか、属人化していた購買情報の共有化による内部不正防止や統制にも役立ちます。
NEWJI DX
製造業に特化したデジタルトランスフォーメーション(DX)の実現を目指す請負開発型のコンサルティングサービスです。AI、iPaaS、および先端の技術を駆使して、製造プロセスの効率化、業務効率化、チームワーク強化、コスト削減、品質向上を実現します。このサービスは、製造業の課題を深く理解し、それに対する最適なデジタルソリューションを提供することで、企業が持続的な成長とイノベーションを達成できるようサポートします。
オンライン講座
製造業、主に購買・調達部門にお勤めの方々に向けた情報を配信しております。
新任の方やベテランの方、管理職を対象とした幅広いコンテンツをご用意しております。
お問い合わせ
コストダウンが利益に直結する術だと理解していても、なかなか前に進めることができない状況。そんな時は、newjiのコストダウン自動化機能で大きく利益貢献しよう!
(Β版非公開)