- お役立ち記事
- Fundamentals of reliability engineering and practical usage that mid-level employees in equipment management departments should know
Fundamentals of reliability engineering and practical usage that mid-level employees in equipment management departments should know
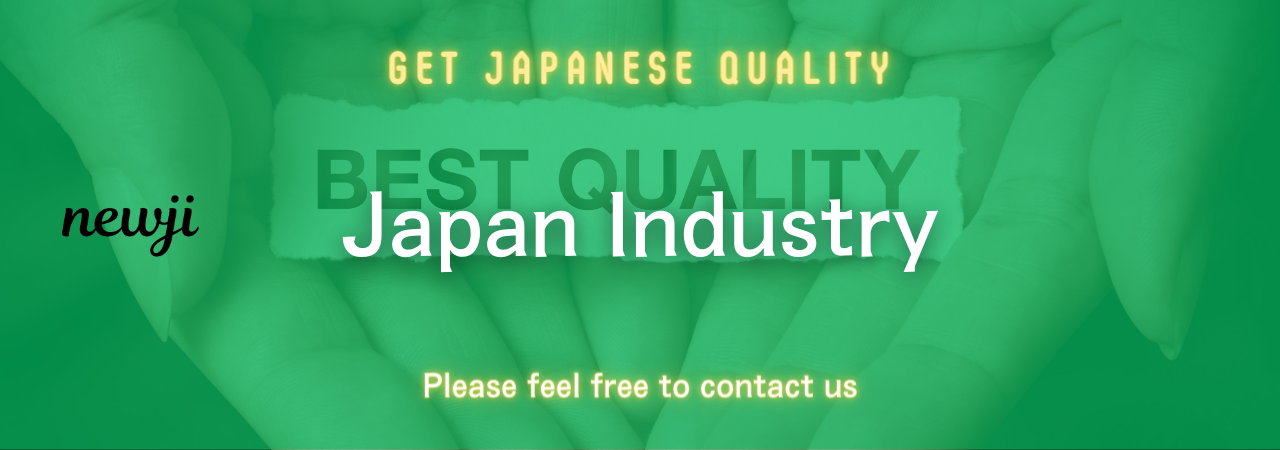
目次
Understanding Reliability Engineering
Reliability engineering is a core concept within the equipment management sector, focusing on prolonging the life and performance of machinery.
Essential for those in mid-level positions, it involves ensuring that systems and components perform their intended functions without failure over a specified period.
This discipline combines principles from engineering, statistics, and quality control, offering a comprehensive approach to maintaining the integrity and efficiency of equipment.
Reliability engineering reduces failures and contributes to cost management by minimizing unexpected breakdowns.
By applying these principles, mid-level employees can help their organizations maintain a competitive edge by ensuring equipment is operational and efficient.
A profound understanding of reliability engineering helps manage risk, improve safety, and enhance overall productivity.
Key Concepts in Reliability Engineering
MTBF and MTTR
Two fundamental concepts in reliability engineering are Mean Time Between Failures (MTBF) and Mean Time to Repair (MTTR).
MTBF measures the average time a system operates before failing, providing insights into the expected performance range of equipment.
A higher MTBF indicates a more reliable system, which helps in planning maintenance schedules and ensuring longevity.
MTTR, on the other hand, refers to the average time required to repair a system or component once a failure occurs.
Understanding MTTR assists in estimating downtime and planning for resource allocation.
Together, MTBF and MTTR help in analyzing the reliability and maintainability of equipment, enabling effective maintenance strategies.
Failure Mode and Effects Analysis (FMEA)
Failure Mode and Effects Analysis (FMEA) is a structured approach used to identify potential failure modes within a system and evaluate their impact on performance.
This technique prioritizes failures based on their severity, likelihood, and detectability, thus guiding the focus towards areas that need immediate attention.
Mid-level employees can use FMEA to systematically assess the reliability of various components and implement corrective actions to mitigate risks.
Conducting regular FMEAs leads to improvements in processes and systems, reducing the occurrence of failures and enhancing organizational reliability.
Reliability Centered Maintenance (RCM)
Reliability Centered Maintenance (RCM) is a process used to determine the most effective maintenance strategies.
RCM focuses on preserving system functions, identifying potential failure causes, and selecting appropriate maintenance tasks to mitigate those risks.
The aim is to ensure that equipment continues to do what users require in its present operating context.
By implementing RCM, mid-level employees can optimize maintenance efforts, improve safety, and extend the life of equipment.
This proactive approach ensures operational effectiveness and efficiency, reducing costs related to unscheduled repairs and downtime.
Practical Application of Reliability Engineering
Implementing Predictive Maintenance
Predictive maintenance is a critical application of reliability engineering that uses condition monitoring tools and techniques to predict equipment failures.
It involves analyzing data from sensors and diagnostic tools to forecast when a machine or component is likely to fail.
By effectively implementing predictive maintenance, mid-level employees can anticipate equipment issues and address them before they lead to significant failures.
This approach not only enhances equipment reliability but also optimizes maintenance resources, leading to cost savings and improved operational productivity.
Data-Driven Decision Making
The reliance on data analytics in reliability engineering cannot be overstated.
Employing data-driven methods allows mid-level employees to make informed decisions about equipment maintenance and management.
By utilizing statistical analysis and failure data, they can identify trends, anomalies, and recurrent issues that may affect system reliability.
Data analysis helps in developing more efficient maintenance schedules and strategies, ensuring that all decisions are based on concrete evidence rather than assumptions.
Implementing data-driven decision-making processes maximizes the efficacy of reliability engineering tasks and outcomes.
Continuous Improvement Processes
An essential aspect of reliability engineering is the focus on continuous improvement.
Mid-level employees must perpetually seek ways to enhance equipment reliability and efficiency by learning from past failures and successes.
This involves conducting regular training sessions, benchmarking best practices, and investing in new technologies.
Continuous improvement not only boosts equipment performance but also drives innovation across the organization.
By consistently implementing reliability improvements, employees can build a culture of reliability that permeates all aspects of their operations.
Benefits of Reliability Engineering
Increased Equipment Availability
One of the primary benefits of reliability engineering is increased equipment availability.
By minimizing failures and reducing downtime, equipment is available for production more often, ensuring that organizational objectives are met.
This results in higher productivity and output, directly impacting the bottom line.
Reduced Maintenance Costs
Implementing reliability engineering principles effectively leads to a reduction in maintenance costs.
With strategies such as predictive and preventive maintenance, mid-level employees can reduce the frequency and severity of unexpected repairs, saving time and resources.
Lower maintenance costs also mean that more budget can be allocated towards innovation and other development initiatives, fostering growth and expansion within the organization.
Improved Safety and Compliance
Reliability engineering also plays a critical role in enhancing workplace safety and compliance.
By prioritizing equipment reliability, employees help ensure that all machinery operates within safe parameters, reducing the risk of accidents and injuries.
Additionally, reliable equipment aids in compliance with industry regulations and standards, protecting the organization from potential legal liabilities and reputational damage.
Conclusion
For mid-level employees in equipment management departments, mastering the fundamentals of reliability engineering is vital.
By understanding and applying concepts such as MTBF, MTTR, FMEA, and RCM, they can enhance equipment reliability, reduce costs, and improve safety.
The practical application of predictive maintenance, data-driven decision-making, and a focus on continuous improvement will not only boost operational efficiency but also drive organizational success.
Reliability engineering is essential for maintaining a competitive advantage and ensuring sustained growth and development in today’s dynamic industrial landscape.
資料ダウンロード
QCD調達購買管理クラウド「newji」は、調達購買部門で必要なQCD管理全てを備えた、現場特化型兼クラウド型の今世紀最高の購買管理システムとなります。
ユーザー登録
調達購買業務の効率化だけでなく、システムを導入することで、コスト削減や製品・資材のステータス可視化のほか、属人化していた購買情報の共有化による内部不正防止や統制にも役立ちます。
NEWJI DX
製造業に特化したデジタルトランスフォーメーション(DX)の実現を目指す請負開発型のコンサルティングサービスです。AI、iPaaS、および先端の技術を駆使して、製造プロセスの効率化、業務効率化、チームワーク強化、コスト削減、品質向上を実現します。このサービスは、製造業の課題を深く理解し、それに対する最適なデジタルソリューションを提供することで、企業が持続的な成長とイノベーションを達成できるようサポートします。
オンライン講座
製造業、主に購買・調達部門にお勤めの方々に向けた情報を配信しております。
新任の方やベテランの方、管理職を対象とした幅広いコンテンツをご用意しております。
お問い合わせ
コストダウンが利益に直結する術だと理解していても、なかなか前に進めることができない状況。そんな時は、newjiのコストダウン自動化機能で大きく利益貢献しよう!
(Β版非公開)