- お役立ち記事
- A new approach to improving work efficiency using SLP (facility layout planning) for production engineering departments
A new approach to improving work efficiency using SLP (facility layout planning) for production engineering departments
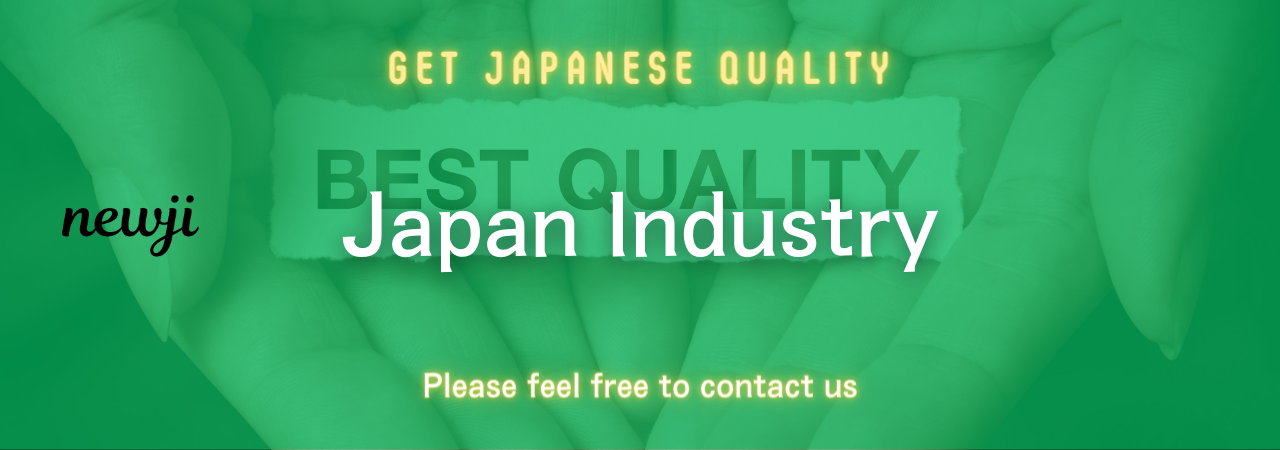
目次
Understanding Facility Layout Planning (SLP)
Facility Layout Planning (SLP) is a systematic approach used to design and organize the physical arrangements of a manufacturing setting.
These arrangements include workstations, equipment, and workflow paths to ensure a productive work environment.
SLP aims to streamline operations and enhance efficiency within production engineering departments.
By implementing SLP, businesses can reduce operational costs, improve safety, and increase overall productivity.
SLP involves a thorough analysis of space requirements, workflow processes, and interdepartmental relationships within a production facility.
This planning is crucial because a poorly designed layout can lead to bottlenecks, inefficiencies, and wasted resources.
On the contrary, an optimized layout enhances interactions, minimizes material movement, and improves the overall function of the production process.
The Principles of SLP
For effective layout planning, you must understand the core principles of SLP.
These principles guide production engineers and facility planners in creating an efficient workspace:
1. Systematic Approach
SLP follows a systematic approach that involves analyzing existing conditions, identifying objectives, and implementing changes.
It requires detailed observation and data collection to establish a practical layout that meets operational needs.
2. Space Utilization
One of the main goals of SLP is to make optimum use of available space.
The layout should allocate space for machines, materials, and personnel effectively, reducing wasted space and enhancing productivity.
3. Smooth Workflow
An essential SLP principle is ensuring a smooth and uninterrupted workflow.
This involves organizing equipment and workstations in a sequence that minimizes distance and travel time during production processes.
4. Flexibility
Flexible layouts allow production systems to adapt to changes in demand and technology without requiring major overhauls.
SLP should consider future scalability and modifications to maintain efficiency over time.
5. Safety and Ergonomics
Safety is paramount in any production environment.
The layout must take into account worker safety, equipment placement, and ergonomic considerations to prevent accidents and promote a healthy workspace.
Implementing SLP in Production Engineering
To apply SLP effectively in a production environment, production engineering departments should follow these steps:
1. Conduct a Comprehensive Analysis
Start with a detailed analysis of the current layout, identifying inefficiencies, material flow, and workspace usage.
Gather data on production processes, equipment capabilities, and space constraints to understand existing conditions.
2. Identify Objectives
Set clear objectives for the layout improvement.
These could include increasing production output, reducing costs, improving safety, or enhancing flexibility.
Clear goals help guide the planning process and measure success post-implementation.
3. Develop Layout Alternatives
Create multiple layout alternatives based on collected data and objectives.
Consider various configurations, such as process layouts, product layouts, or a combination of both.
Each alternative should be evaluated for its advantages and drawbacks.
4. Evaluate and Select the Best Layout
Evaluate each layout alternative against the set objectives, using tools like computer simulations, workflow analysis, and cost-benefit assessments.
Select the layout that best fits the needs and goals of the production facility.
5. Implement and Monitor
Once a layout is selected, plan and implement the changes systematically to minimize disruption to production.
Monitoring the new layout’s effectiveness over time is crucial, allowing for adjustments and improvements as needed.
Benefits of Using SLP for Work Efficiency
Applying SLP in production engineering can significantly enhance work efficiency.
Here are some of the key benefits:
1. Improved Productivity
An optimized layout reduces the time and effort needed for material handling and processing, resulting in faster production cycles and increased output.
2. Cost Reduction
By minimizing waste, reducing transportation costs, and utilizing space efficiently, businesses can realize significant cost savings in their production processes.
3. Enhanced Safety
SLP prioritizes safety and ergonomic considerations, reducing the risk of workplace injuries and accidents.
A well-planned layout ensures that equipment and materials are accessible without compromising worker safety.
4. Better Workflow
By aligning the layout with production processes, SLP ensures a smooth flow of materials and information, reducing bottlenecks and delays in the production line.
5. Increased Flexibility
An SLP-designed layout can adapt to changes in production needs, such as new product lines or technologies, without requiring significant alterations or downtime.
Conclusion
Facility Layout Planning (SLP) is a vital tool for enhancing work efficiency in production engineering departments.
By systematically analyzing and optimizing layouts, businesses can improve productivity, reduce costs, and create a safer working environment.
Implementing SLP requires clear objectives, thorough analysis, and continuous evaluation to ensure success.
In today’s competitive manufacturing landscape, leveraging SLP can provide a significant edge, aligning production processes with business goals effectively and sustainably.
資料ダウンロード
QCD調達購買管理クラウド「newji」は、調達購買部門で必要なQCD管理全てを備えた、現場特化型兼クラウド型の今世紀最高の購買管理システムとなります。
ユーザー登録
調達購買業務の効率化だけでなく、システムを導入することで、コスト削減や製品・資材のステータス可視化のほか、属人化していた購買情報の共有化による内部不正防止や統制にも役立ちます。
NEWJI DX
製造業に特化したデジタルトランスフォーメーション(DX)の実現を目指す請負開発型のコンサルティングサービスです。AI、iPaaS、および先端の技術を駆使して、製造プロセスの効率化、業務効率化、チームワーク強化、コスト削減、品質向上を実現します。このサービスは、製造業の課題を深く理解し、それに対する最適なデジタルソリューションを提供することで、企業が持続的な成長とイノベーションを達成できるようサポートします。
オンライン講座
製造業、主に購買・調達部門にお勤めの方々に向けた情報を配信しております。
新任の方やベテランの方、管理職を対象とした幅広いコンテンツをご用意しております。
お問い合わせ
コストダウンが利益に直結する術だと理解していても、なかなか前に進めることができない状況。そんな時は、newjiのコストダウン自動化機能で大きく利益貢献しよう!
(Β版非公開)