- お役立ち記事
- The basics of 5S activities and how to proceed with improvements that new employees in the production operations department should learn
The basics of 5S activities and how to proceed with improvements that new employees in the production operations department should learn
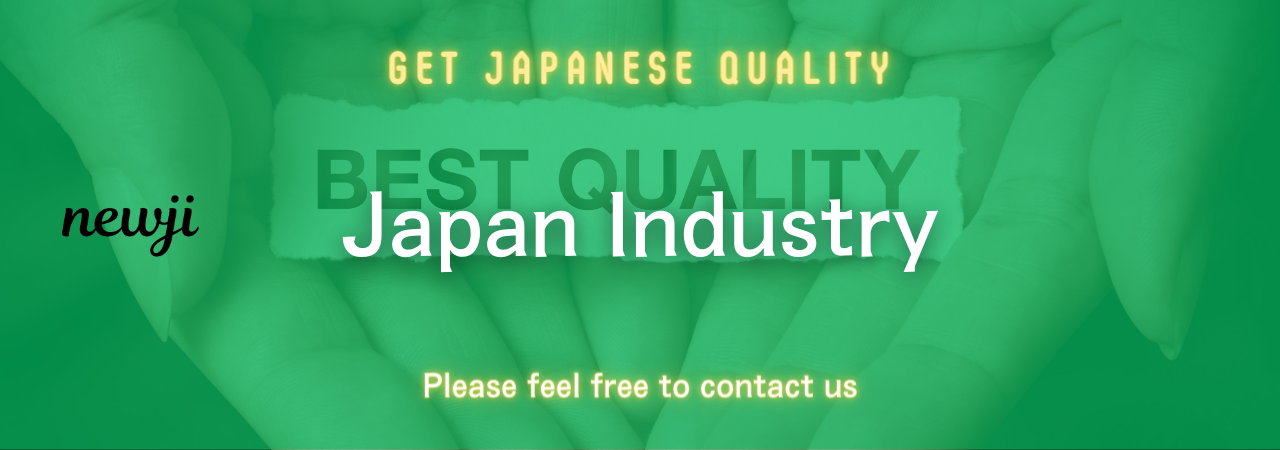
目次
Understanding 5S Activities
5S is a workplace organization method that originated from Japan, aiming to enhance efficiency and productivity while ensuring a safe and tidy environment.
These activities are vital in production operations and can significantly benefit new employees who are eager to learn and implement effective processes.
5S stands for Sort, Set in order, Shine, Standardize, and Sustain, which together create a framework for organizing and managing the workspace.
Sort: Streamlining Workspaces
Sort is the first step of the 5S process.
The purpose of this step is to eliminate unnecessary items from the workspace, so only essential items remain.
For new employees, this means identifying tools, equipment, and materials that are regularly used and removing anything that does not contribute to daily tasks.
It is about decluttering the area and ensuring that only what is necessary for performing tasks efficiently is available.
This step often involves sorting through cluttered areas, matching items to their purpose, and discarding what is obsolete or duplicated.
Set in Order: Organize with Precision
Once unnecessary items have been removed, the next step is Set in Order.
This process involves organizing the necessary items so that they are easy to find and use.
For instance, tools and materials should be arranged in a manner where they are easily accessible to reduce time wasted searching for them.
Labeling areas, color-coding, and using well-defined storage solutions are common strategies used to arrange items logically.
For new employees, getting acquainted with these systems can lead to more effective and streamlined work processes.
Shine: Maintain a Clean Environment
Shine focuses on cleaning the workspace and ensuring it remains tidy.
This step involves regular cleaning and maintenance that helps prevent deterioration of equipment and work areas.
By keeping a clean workspace, production areas are safer and more appealing, which can improve morale and productivity.
New employees should develop a routine that includes daily cleaning and periodic inspections to identify potential areas that require deeper cleaning efforts.
The Shine step is crucial for preventing workplace hazards and instilling a culture of responsibility and pride in the workspace.
Standardize: Create Consistent Practices
Standardize is about developing uniform procedures and guidelines that keep the previous three steps consistent and sustained over time.
This means creating clear, written guidelines on how tasks should be performed and how work areas should be maintained.
New employees should familiarize themselves with these standards to understand the expectations and requirements of their roles.
Standardization allows new team members to quickly adapt without confusion, and it helps maintain quality and efficiency across shifts and department transitions.
Sustain: Cultivate a Culture of Continuous Improvement
The Sustain step refers to the ongoing effort to maintain these practices over time.
It is about fostering a culture where employees take ownership of their workspaces and continuously seek ways to improve them.
New employees should be encouraged to consistently apply the previous steps and actively contribute ideas for further improvement.
This might involve regular check-ins, training sessions, and encouragement from management to ensure these practices are integrated into daily routines.
How New Employees Can Implement 5S
For new employees, understanding and implementing 5S might seem overwhelming at first.
However, breaking it down into manageable steps can make the process more approachable.
Start by observing your workspace and identifying areas that need immediate attention, then follow the steps methodically.
Participate in 5S Training
One of the most effective ways for new employees to get involved in 5S activities is by participating in training sessions.
These sessions provide a comprehensive overview of each step and demonstrate practical applications in various scenarios.
Training helps new employees understand the “why” behind each step and how it contributes to their work overall.
Become an Active Team Member
5S activities are best implemented as a team effort.
New employees should engage with their team and participate in activities and discussions regarding 5S improvements.
Being proactive about seeking help and offering suggestions can foster a sense of community and shared purpose, enhancing the workplace environment.
Monitor and Reflect on Progress
Regularly monitoring and reflecting on the progress of 5S implementation can motivate new employees to stay committed to these principles.
Keeping track of improvements, acknowledging successes, and learning from failures can refine approaches and optimize workspace organization over time.
This involves maintaining a keen eye on how the implementation is affecting productivity and workflow.
Benefits of 5S for New Employees
For new employees in the production operations department, embracing 5S activities can offer numerous benefits.
It fosters a sense of responsibility and accountability for one’s own environment, promotes safety, reduces waste, and enhances efficiency.
Additionally, 5S principles align with personal development by encouraging habits that promote organization and time management.
Implementing 5S not only contributes to personal growth but also supports the overall goals of the workplace.
It creates a harmonious environment where new employees can thrive and grow alongside their colleagues.
In conclusion, understanding and implementing 5S activities can significantly impact the productivity and efficiency of new employees in the production operations department.
By learning to sort, set in order, shine, standardize, and sustain, new team members can integrate these practices into their daily routine and contribute to a well-organized and efficient workplace.
資料ダウンロード
QCD調達購買管理クラウド「newji」は、調達購買部門で必要なQCD管理全てを備えた、現場特化型兼クラウド型の今世紀最高の購買管理システムとなります。
ユーザー登録
調達購買業務の効率化だけでなく、システムを導入することで、コスト削減や製品・資材のステータス可視化のほか、属人化していた購買情報の共有化による内部不正防止や統制にも役立ちます。
NEWJI DX
製造業に特化したデジタルトランスフォーメーション(DX)の実現を目指す請負開発型のコンサルティングサービスです。AI、iPaaS、および先端の技術を駆使して、製造プロセスの効率化、業務効率化、チームワーク強化、コスト削減、品質向上を実現します。このサービスは、製造業の課題を深く理解し、それに対する最適なデジタルソリューションを提供することで、企業が持続的な成長とイノベーションを達成できるようサポートします。
オンライン講座
製造業、主に購買・調達部門にお勤めの方々に向けた情報を配信しております。
新任の方やベテランの方、管理職を対象とした幅広いコンテンツをご用意しております。
お問い合わせ
コストダウンが利益に直結する術だと理解していても、なかなか前に進めることができない状況。そんな時は、newjiのコストダウン自動化機能で大きく利益貢献しよう!
(Β版非公開)