- お役立ち記事
- Optimization Techniques for Quality Management Systems Using ISO 9001
Optimization Techniques for Quality Management Systems Using ISO 9001
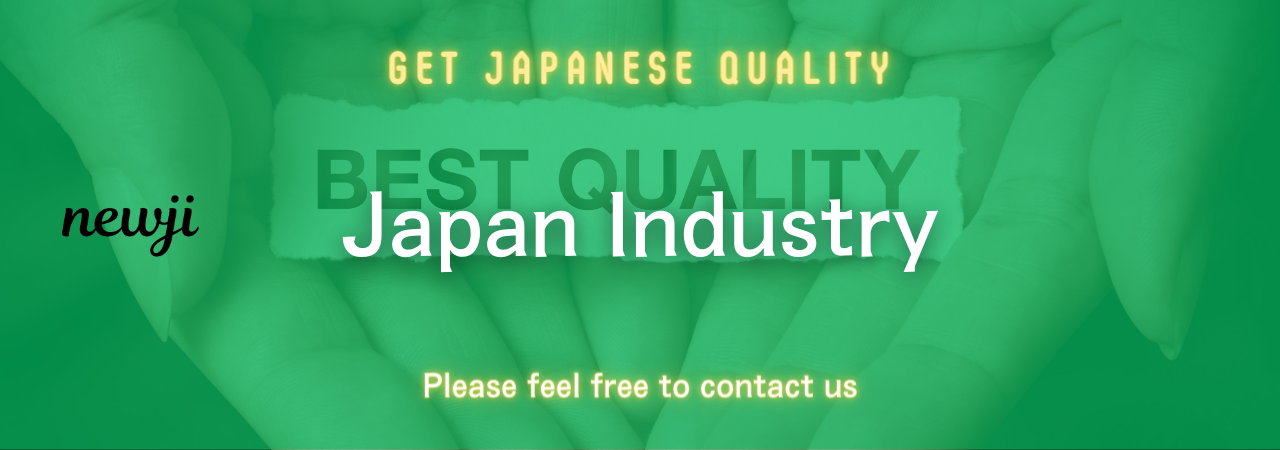
目次
Introduction to ISO 9001
ISO 9001 is a globally recognized standard for quality management systems (QMS) that aims to help organizations improve their processes and deliver better products or services to their customers.
This standard provides a framework that organizations can use to ensure that they meet the expectations of stakeholders while complying with regulatory requirements.
Implementing ISO 9001 can offer numerous benefits, including enhanced efficiency, increased customer satisfaction, and a competitive advantage in the market.
Understanding Quality Management Systems
A Quality Management System is a set of policies, processes, and procedures that an organization implements to ensure the consistent quality of its products or services.
The main objective of a QMS is to meet customer requirements and enhance customer satisfaction through continuous improvement.
ISO 9001 provides the criteria for a QMS that organizations can adapt, regardless of their size or industry.
By following these criteria, organizations can achieve a structured approach to managing quality, leading to consistent and reliable outputs.
The Role of Continuous Improvement
Continuous improvement is a core principle of ISO 9001, emphasizing the need for organizations to always look for ways to enhance their processes and systems.
This involves regularly analyzing performance data, identifying areas for improvement, and implementing changes that positively impact overall efficiency and effectiveness.
Continuous improvement helps organizations remain competitive, maintain customer satisfaction, and adapt to changing market conditions.
Customer Focus in Quality Management
ISO 9001 encourages organizations to prioritize customer requirements and strive to exceed customer expectations.
By maintaining a strong customer focus, organizations can build loyalty, ensure repeat business, and raise their reputation in the marketplace.
This is achieved by engaging customers and stakeholders, understanding their needs, and aligning organizational processes to meet these needs effectively.
Optimization Techniques for ISO 9001
Implementing and optimizing a QMS using ISO 9001 involves a series of techniques that organizations can apply to enhance their processes and outcomes.
Effective Process Mapping
Process mapping is an essential technique for visualizing workflows and identifying inefficiencies within an organization.
By creating detailed process maps, organizations can understand the interconnectivity of different processes, streamline operations, and eliminate waste.
Identifying bottlenecks or redundancies through process mapping allows for targeted improvements, ultimately contributing to a more efficient QMS.
Root Cause Analysis
Root cause analysis is a problem-solving method used to identify the underlying causes of defects, errors, or inefficiencies.
By conducting thorough investigations into issues, organizations can implement corrective actions that address the root of the problem, preventing recurrence.
This technique is critical for maintaining product or service quality and ensuring continual improvement.
Implementing Performance Metrics
Performance metrics allow organizations to quantitatively measure the success of their QMS and its impact on organizational goals.
By setting clear, measurable objectives, organizations can monitor progress and make data-driven decisions.
Key performance indicators (KPIs) provide insights into areas that require attention and help organizations prioritize resources for maximum impact.
Using SWOT Analysis
SWOT analysis (Strengths, Weaknesses, Opportunities, Threats) is a strategic planning tool that helps organizations assess their current position and identify areas for improvement.
Through SWOT analysis, organizations can build on their strengths, address weaknesses, take advantage of opportunities, and mitigate threats.
This comprehensive approach aids in aligning the QMS with the organization’s overall strategic objectives.
Challenges in Implementing ISO 9001
Despite the numerous benefits, implementing ISO 9001 can present certain challenges for organizations.
Resource Allocation
Implementing a QMS according to ISO 9001 can be resource-intensive, requiring time, financial investment, and personnel.
Organizations may struggle to allocate sufficient resources for effective implementation and maintenance of the system.
Addressing this challenge involves carefully planning and setting realistic expectations, ensuring resource use is efficient and effectively supports QMS objectives.
Change Management
Embedding a QMS may require significant changes in organizational culture and work practices.
Resistance to change can hinder the effective implementation of ISO 9001.
Organizations must engage employees, communicate changes clearly, and cultivate a culture of quality to facilitate smooth transitions.
Conclusion
ISO 9001 remains a critical tool for organizations seeking to enhance their quality management systems and achieve consistent, high-quality results.
By focusing on continuous improvement, customer satisfaction, and strategic optimization techniques, organizations can effectively implement and benefit from ISO 9001.
Although challenges may arise, engaging with these hurdles reminds us that the path to quality excellence is an ongoing journey.
Ultimately, by embracing the principles of ISO 9001, organizations position themselves to succeed in the competitive and ever-evolving marketplace.
資料ダウンロード
QCD調達購買管理クラウド「newji」は、調達購買部門で必要なQCD管理全てを備えた、現場特化型兼クラウド型の今世紀最高の購買管理システムとなります。
ユーザー登録
調達購買業務の効率化だけでなく、システムを導入することで、コスト削減や製品・資材のステータス可視化のほか、属人化していた購買情報の共有化による内部不正防止や統制にも役立ちます。
NEWJI DX
製造業に特化したデジタルトランスフォーメーション(DX)の実現を目指す請負開発型のコンサルティングサービスです。AI、iPaaS、および先端の技術を駆使して、製造プロセスの効率化、業務効率化、チームワーク強化、コスト削減、品質向上を実現します。このサービスは、製造業の課題を深く理解し、それに対する最適なデジタルソリューションを提供することで、企業が持続的な成長とイノベーションを達成できるようサポートします。
オンライン講座
製造業、主に購買・調達部門にお勤めの方々に向けた情報を配信しております。
新任の方やベテランの方、管理職を対象とした幅広いコンテンツをご用意しております。
お問い合わせ
コストダウンが利益に直結する術だと理解していても、なかなか前に進めることができない状況。そんな時は、newjiのコストダウン自動化機能で大きく利益貢献しよう!
(Β版非公開)