- お役立ち記事
- Equipment reliability testing and maintenance optimization that should be practiced by equipment maintenance departments
Equipment reliability testing and maintenance optimization that should be practiced by equipment maintenance departments
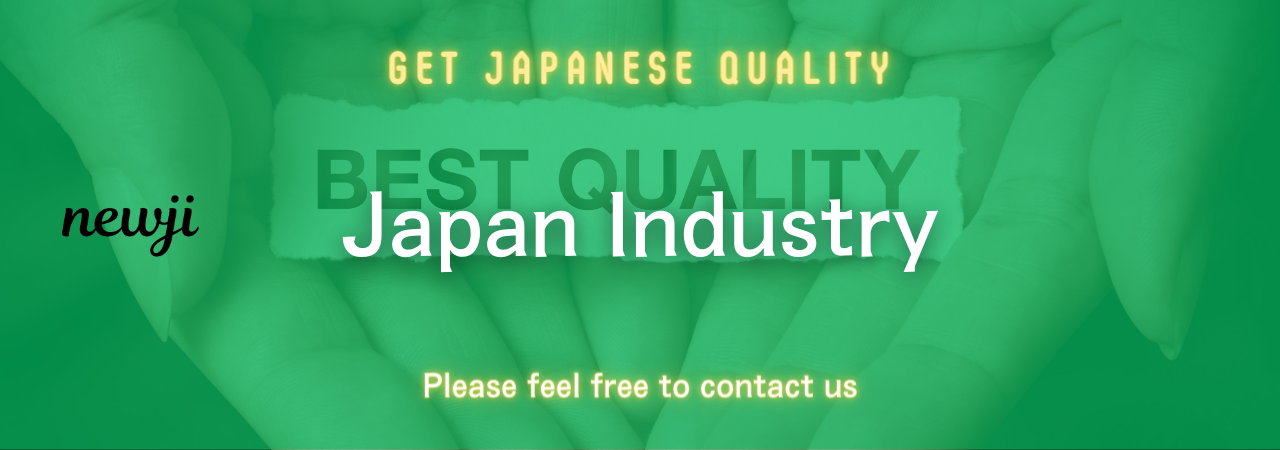
目次
Understanding Equipment Reliability Testing
Equipment reliability testing is a crucial process in ensuring that machinery and equipment perform their intended functions consistently over their lifespan.
This testing involves evaluating equipment under various conditions to assess its durability, performance, and reliability.
Maintenance departments benefit greatly from incorporating reliability testing into their regular routines, as it helps prevent unexpected breakdowns and enhances overall operational efficiency.
Reliability testing typically includes stress tests, life testing, and performance assessments.
Each type of test provides invaluable data, helping maintenance teams predict potential failures before they occur.
By understanding how and why equipment might fail, departments can develop strategic maintenance plans to address issues proactively.
Key Components of Equipment Reliability Testing
When implementing equipment reliability testing, it’s essential to focus on a few key components.
These include:
1. Performance Testing
This involves assessing the equipment’s ability to perform under normal operating conditions.
Performance tests determine if the equipment meets the manufacturer’s specifications and if it can sustain optimal operation for extended periods.
2. Stress Testing
Stress testing evaluates how equipment behaves under extreme conditions, often beyond its standard operational limits.
This helps identify weaknesses or vulnerabilities that may not be apparent during normal use.
3. Lifecycle Testing
Lifecycle testing examines the equipment’s durability over a prolonged period.
It helps predict the lifespan and the potential maintenance needs of machinery, enabling departments to plan and budget accordingly.
Benefits of Equipment Reliability Testing
The ultimate goal of reliability testing is to ensure that equipment operates without hitch.
This can yield several essential benefits:
1. Reduced Downtime
By identifying potential issues before they result in failure, teams can prevent unexpected breakdowns, thus reducing downtime and ensuring continuous productivity.
2. Enhanced Safety
Reliable equipment decreases the likelihood of malfunctions that could lead to unsafe conditions for operators and workers.
This leads to a safer work environment overall.
3. Cost Savings
Proactive maintenance, informed by reliability testing, can significantly cut costs associated with emergency repairs and replacements.
Predicting and mitigating failures before they happen often proves more economical than abrupt fixes post-failure.
4. Improved Equipment Performance
Regular testing ensures that equipment continues to function at peak efficiency.
This leads to better product quality and increased satisfaction for customers and stakeholders alike.
Optimizing Maintenance Through Data
Once reliability testing is conducted, data gathered must be meticulously analyzed to optimize maintenance processes.
Advanced data analytics techniques can uncover patterns and trends that may not be visible otherwise.
By leveraging this information, maintenance teams can make informed decisions about servicing, repairs, and replacements, thus optimizing the maintenance schedule.
1. Predictive Maintenance
Predictive maintenance involves using data from equipment sensors and historical performance to predict when a piece of equipment is likely to require maintenance.
This method minimizes the risk of equipment failure by addressing potential issues before they occur.
2. Condition-Based Maintenance
This approach monitors the actual condition of equipment through assessments and diagnostic tests to determine the appropriate maintenance task.
This ensures that maintenance is only performed when necessary, avoiding both over-maintenance and under-maintenance.
Developing a Comprehensive Maintenance Plan
A successful maintenance department should implement a comprehensive maintenance plan, integrating insights gained from reliability testing.
1. Regular Inspections
Schedule regular equipment inspections and ensure that all team members are trained in identifying signs of wear or potential issues.
This not only helps maintain safety but also ensures that equipment operates at its best.
2. Detailed Documentation
Keep meticulous records of all maintenance activities, repairs, and part replacements.
This information is invaluable for future reference and can help streamline processes in the long run.
3. Training and Development
Continuously invest in staff training and development to keep them updated on the latest maintenance techniques and technologies.
Well-trained staff will be better equipped to conduct tests and interpret data, leading to improved reliability testing and maintenance optimization outcomes.
Embracing Technology in Maintenance
Technology plays a crucial role in enhancing equipment reliability and optimizing maintenance.
From the use of IoT devices to AI-driven predictive analytics, modern solutions provide maintenance departments with advanced tools to manage their equipment effectively.
Adopting technologies like computerized maintenance management systems (CMMS) can streamline operations, automate routine tasks, and provide significant insights into equipment performance.
This allows maintenance teams to focus more on strategic decision-making rather than mundane administrative tasks.
Conclusion
Equipment reliability testing and maintenance optimization are indispensable processes for any maintenance department aiming to ensure operational excellence.
By understanding the components of reliability testing, leveraging the data for predictive and condition-based maintenance, and embracing technology, these departments can improve equipment performance, reduce costs, and ensure a safe working environment.
Ultimately, a comprehensive and well-informed approach not only prolongs equipment lifespan but also drives organizational success.
資料ダウンロード
QCD調達購買管理クラウド「newji」は、調達購買部門で必要なQCD管理全てを備えた、現場特化型兼クラウド型の今世紀最高の購買管理システムとなります。
ユーザー登録
調達購買業務の効率化だけでなく、システムを導入することで、コスト削減や製品・資材のステータス可視化のほか、属人化していた購買情報の共有化による内部不正防止や統制にも役立ちます。
NEWJI DX
製造業に特化したデジタルトランスフォーメーション(DX)の実現を目指す請負開発型のコンサルティングサービスです。AI、iPaaS、および先端の技術を駆使して、製造プロセスの効率化、業務効率化、チームワーク強化、コスト削減、品質向上を実現します。このサービスは、製造業の課題を深く理解し、それに対する最適なデジタルソリューションを提供することで、企業が持続的な成長とイノベーションを達成できるようサポートします。
オンライン講座
製造業、主に購買・調達部門にお勤めの方々に向けた情報を配信しております。
新任の方やベテランの方、管理職を対象とした幅広いコンテンツをご用意しております。
お問い合わせ
コストダウンが利益に直結する術だと理解していても、なかなか前に進めることができない状況。そんな時は、newjiのコストダウン自動化機能で大きく利益貢献しよう!
(Β版非公開)