- お役立ち記事
- Basics and practices of TPM activities that new leaders of equipment maintenance departments should learn
Basics and practices of TPM activities that new leaders of equipment maintenance departments should learn
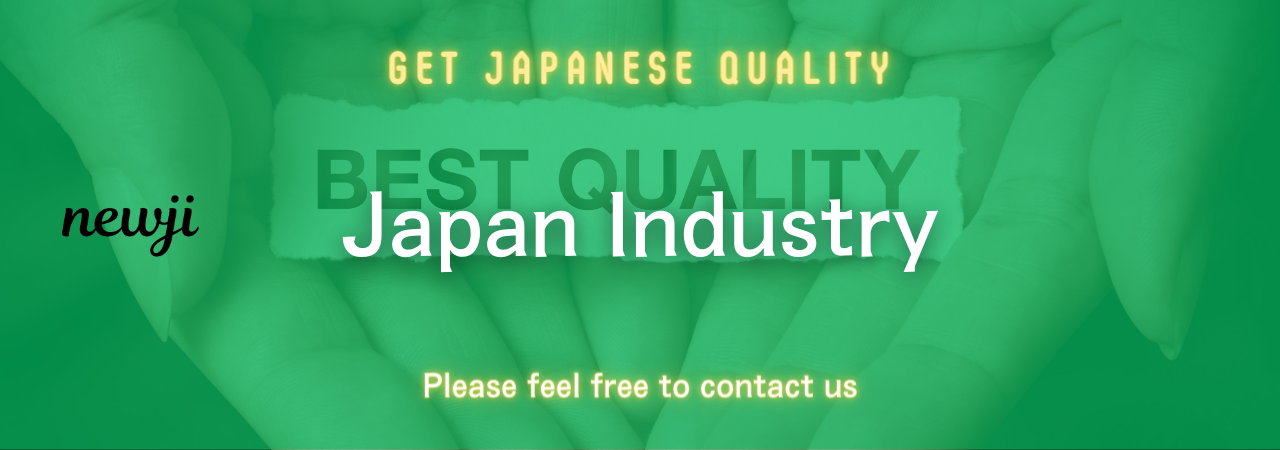
目次
What is Total Productive Maintenance (TPM)?
Total Productive Maintenance (TPM) is a comprehensive approach aimed at improving the productivity of a manufacturing enterprise by maximizing the efficiency and lifespan of equipment.
Unlike traditional maintenance practices that often focus solely on repairing machinery after a breakdown occurs, TPM emphasizes proactive and preventive strategies.
This approach fosters a collaborative environment where operators, maintenance personnel, and management work together to achieve optimal machine performance.
By involving employees from all levels, TPM not only enhances machine reliability but also boosts employee morale and engagement.
The Eight Pillars of TPM
TPM is structured around eight distinct pillars, each of which plays a vital role in optimizing equipment effectiveness.
Understanding these pillars is essential for any leader in the equipment maintenance department.
1. Autonomous Maintenance
Autonomous Maintenance encourages operators to take ownership of their equipment.
They are trained in routine maintenance tasks such as cleaning, lubricating, and inspection.
This empowers operators to identify and address minor issues before they escalate into more significant problems, reducing downtime and enhancing equipment reliability.
2. Planned Maintenance
Planned Maintenance focuses on scheduling and performing regular maintenance activities to prevent unexpected failures.
This ensures that machinery is serviced at regular intervals, reducing the risk of breakdowns and extending machine lifespan.
A well-planned schedule considers factors like operational hours, machine criticality, and historical data on machine performance.
3. Quality Maintenance
This pillar is dedicated to maintaining quality standards by identifying and rectifying equipment issues that could lead to defects in the products.
By continuously monitoring equipment performance and making necessary adjustments, companies can produce high-quality products consistently.
4. Focused Improvement
Focused Improvement seeks to identify and eliminate waste, thereby increasing efficiency.
Teams are encouraged to collaborate in pinpointing inefficiencies across production processes and to develop targeted solutions.
This pillar relies heavily on data analysis, brainstorming sessions, and problem-solving techniques.
5. Early Equipment Management
Early Equipment Management involves incorporating maintenance perspectives into the design and development stages of new equipment.
By considering ease of maintenance, equipment reliability, and overall operational efficiency early on, companies can reduce future maintenance challenges and costs.
6. Training and Education
This pillar emphasizes the importance of continuous learning for all employees involved in maintenance.
Training programs are designed to equip staff with the skills and knowledge needed to perform maintenance tasks effectively.
An educated workforce contributes to the overall success of TPM initiatives.
7. Safety, Health, and Environment
Ensuring a safe and healthy working environment is a cornerstone of TPM.
This pillar involves identifying potential hazards associated with machinery and implementing measures to mitigate these risks.
It also encourages practices that minimize environmental impact.
8. TPM in Office
Although TPM is traditionally associated with the shop floor, its principles can be applied to office environments as well.
By streamlining office processes and reducing administrative waste, organizations can improve overall efficiency and productivity.
Steps to Implement TPM Successfully
Implementing TPM effectively requires strategic planning, dedicated leadership, and active collaboration among all stakeholders.
Step 1: Assess Current Maintenance Practices
Begin by evaluating existing maintenance practices to identify areas for improvement.
Conducting a thorough audit of current processes will highlight strengths and weaknesses in the system.
This assessment serves as the foundation for developing a tailored TPM strategy.
Step 2: Develop a TPM Vision and Goals
Define a clear vision of what TPM success looks like for your organization.
Set specific, measurable, achievable, relevant, and time-bound (SMART) goals that align with this vision.
These goals will guide the implementation process and provide benchmarks for monitoring progress.
Step 3: Secure Management Commitment
The support and commitment of upper management are crucial for the successful implementation of TPM.
Leaders must allocate adequate resources, communicate the importance of TPM to the workforce, and demonstrate ongoing support for the initiative.
Step 4: Create a Cross-Functional TPM Team
Assemble a cross-functional team comprising individuals from various departments, including operations, maintenance, quality, and safety.
This team will be responsible for driving the TPM activities, fostering collaboration, and ensuring alignment across the organization.
Step 5: Conduct Training and Build Competencies
Invest in training programs to build competencies across the workforce.
Equip employees with the necessary skills and knowledge to perform their roles effectively within the TPM framework.
Ongoing education and skill enhancement are key components of sustaining successful TPM practices.
Step 6: Start Small and Scale Gradually
Implement TPM on a small scale initially, focusing on specific equipment or departments.
This allows for the refinement of processes and provides valuable insights into what works well and what needs adjustment.
Once successful, expand TPM practices incrementally to other areas of the organization.
Step 7: Monitor, Evaluate, and Improve
Regularly monitor the progress of TPM activities to assess their effectiveness.
Utilize metrics and key performance indicators (KPIs) to evaluate various aspects such as equipment uptime, defect rates, and maintenance costs.
Use this data to make data-driven decisions and improvements to the TPM process.
Conclusion
Mastering the basics and practices of Total Productive Maintenance (TPM) is crucial for new leaders of equipment maintenance departments.
By focusing on proactive maintenance strategies, organizations can maximize equipment effectiveness, reduce downtime, and improve overall productivity.
Through the implementation of TPM’s eight pillars and a structured approach, maintenance leaders can drive significant improvements in equipment performance and organizational success.
As with any initiative, persistence, and committed involvement at all levels are essential for achieving lasting results.
資料ダウンロード
QCD調達購買管理クラウド「newji」は、調達購買部門で必要なQCD管理全てを備えた、現場特化型兼クラウド型の今世紀最高の購買管理システムとなります。
ユーザー登録
調達購買業務の効率化だけでなく、システムを導入することで、コスト削減や製品・資材のステータス可視化のほか、属人化していた購買情報の共有化による内部不正防止や統制にも役立ちます。
NEWJI DX
製造業に特化したデジタルトランスフォーメーション(DX)の実現を目指す請負開発型のコンサルティングサービスです。AI、iPaaS、および先端の技術を駆使して、製造プロセスの効率化、業務効率化、チームワーク強化、コスト削減、品質向上を実現します。このサービスは、製造業の課題を深く理解し、それに対する最適なデジタルソリューションを提供することで、企業が持続的な成長とイノベーションを達成できるようサポートします。
オンライン講座
製造業、主に購買・調達部門にお勤めの方々に向けた情報を配信しております。
新任の方やベテランの方、管理職を対象とした幅広いコンテンツをご用意しております。
お問い合わせ
コストダウンが利益に直結する術だと理解していても、なかなか前に進めることができない状況。そんな時は、newjiのコストダウン自動化機能で大きく利益貢献しよう!
(Β版非公開)