- お役立ち記事
- For managers of equipment management departments! Practical method to prevent human error using pokayoke method
For managers of equipment management departments! Practical method to prevent human error using pokayoke method
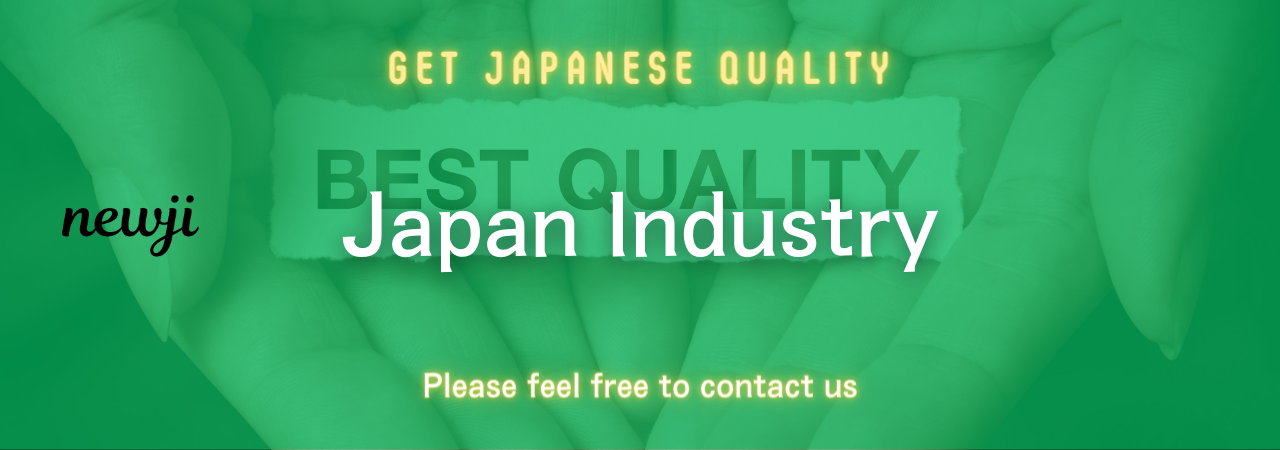
目次
What is the Pokayoke Method?
The Pokayoke method, also known as mistake-proofing, is a concept developed by Japanese engineer Shigeo Shingo in the 1960s.
It’s designed to prevent human errors in manufacturing processes.
The term “Pokayoke” translates to “mistake-proofing” or “avoid mistakes” in English.
This technique involves creating mechanisms or design changes that make it nearly impossible to commit a mistake.
Pokayoke can be implemented in various industries, helping to improve safety and efficiency.
Why Human Errors Occur in Equipment Management
In equipment management, human errors can lead to significant challenges, such as increased maintenance costs, production delays, and safety hazards.
Human errors often occur due to fatigue, lack of knowledge, stress, or miscommunication.
Equipment managers face the challenge of minimizing such errors to ensure smooth operations.
Understanding the root cause of human errors is crucial in implementing effective solutions.
By studying common errors and their origins, managers can take proactive measures to prevent them.
Practical Steps for Implementing Pokayoke
1. Identify Common Errors
The first step in using the Pokayoke method is to identify common errors that occur in equipment management.
This involves analyzing past incidents and understanding patterns.
For instance, frequent machine breakdowns may indicate a need for better maintenance procedures.
2. Analyze the Root Causes
Once errors are identified, it’s essential to analyze their root causes.
Use tools like the Fishbone diagram or 5 Whys analysis to delve deeper into the problem.
This will help identify underlying issues, such as training deficiencies or inadequate communication.
3. Design Error-Proof Solutions
After identifying the root causes, work on designing solutions to prevent these errors.
Consider factors such as user interface design, standardized procedures, and ergonomic improvements.
The goal is to make it difficult or impossible for operators to make mistakes.
For example, installing sensors that alert operators to machine malfunctions can reduce missteps.
Or, create checklists that guide workers through essential maintenance tasks step-by-step.
4. Test and Refine the Solutions
After designing error-proof solutions, test them in real-world conditions.
Collect feedback from operators and observe if the changes effectively reduce errors.
Be prepared to refine strategies based on this feedback to optimize the Pokayoke approach.
5. Train the Workforce
Implementation of any new system requires proper training.
Educate the workforce about the importance of the Pokayoke method and how to apply it in their daily tasks.
Ensure everyone understands the processes and knows how to report issues when they arise.
6. Maintain Continuous Improvement
Regular monitoring and review are essential for maintaining continuous improvement.
Conduct periodic assessments to ensure the Pokayoke solutions remain effective and adapt them as necessary.
Encourage team members to suggest improvements and stay involved.
Benefits of Using the Pokayoke Method
The Pokayoke method offers numerous benefits within equipment management departments.
By preventing errors, it enhances the quality of work and reduces wasted resources.
Managers can achieve more reliable production timelines and improved safety outcomes.
Additionally, integrating Pokayoke methods can lead to increased morale among workers.
Employees understand that their roles are supported by a system designed to make their tasks easier and safer.
Challenges in Implementing Pokayoke
Despite its advantages, implementing the Pokayoke method can present challenges.
Some common difficulties include initial resistance to change, the need for investment in technology, and time constraints.
Overcoming these barriers requires commitment and strategic planning.
Start small with pilot projects to demonstrate the benefits and garner support from stakeholders.
Conclusion
Incorporating the Pokayoke method into equipment management departments can significantly reduce human errors and enhance overall efficiency.
By identifying common errors, understanding their root causes, and developing error-proofing solutions, managers can create a more productive and safe working environment.
Adopting Pokayoke requires continuous improvement and collaboration among team members.
With dedication and strategic planning, this method can be a powerful tool in minimizing mistakes and ensuring successful equipment management.
資料ダウンロード
QCD調達購買管理クラウド「newji」は、調達購買部門で必要なQCD管理全てを備えた、現場特化型兼クラウド型の今世紀最高の購買管理システムとなります。
ユーザー登録
調達購買業務の効率化だけでなく、システムを導入することで、コスト削減や製品・資材のステータス可視化のほか、属人化していた購買情報の共有化による内部不正防止や統制にも役立ちます。
NEWJI DX
製造業に特化したデジタルトランスフォーメーション(DX)の実現を目指す請負開発型のコンサルティングサービスです。AI、iPaaS、および先端の技術を駆使して、製造プロセスの効率化、業務効率化、チームワーク強化、コスト削減、品質向上を実現します。このサービスは、製造業の課題を深く理解し、それに対する最適なデジタルソリューションを提供することで、企業が持続的な成長とイノベーションを達成できるようサポートします。
オンライン講座
製造業、主に購買・調達部門にお勤めの方々に向けた情報を配信しております。
新任の方やベテランの方、管理職を対象とした幅広いコンテンツをご用意しております。
お問い合わせ
コストダウンが利益に直結する術だと理解していても、なかなか前に進めることができない状況。そんな時は、newjiのコストダウン自動化機能で大きく利益貢献しよう!
(Β版非公開)