- お役立ち記事
- Successful Case Studies of JIT Strategy Integrating Logistics and Production Planning
Successful Case Studies of JIT Strategy Integrating Logistics and Production Planning
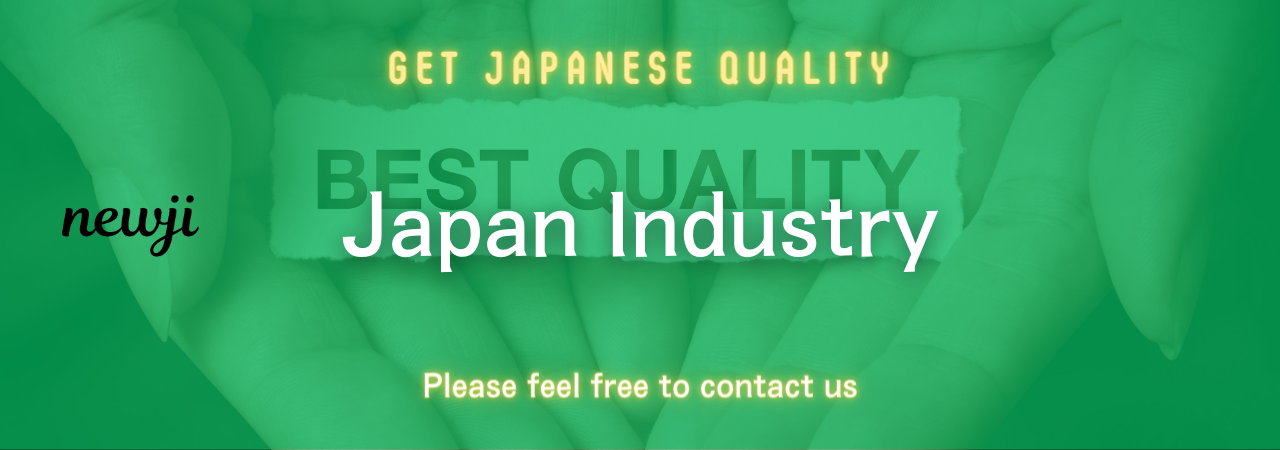
目次
Understanding the JIT Strategy
The Just-In-Time (JIT) strategy is a management philosophy aimed at improving efficiency by receiving goods only as they are needed in the production process, thereby reducing inventory costs.
This strategy requires producers to accurately forecast demand and involves close cooperation between suppliers and logistics teams.
The JIT approach was popularized by Toyota in the automotive manufacturing sector, where it significantly optimized their assembly line production.
The strategy focuses on synchronization between the various elements of production and logistics to ensure a seamless operation.
Key Elements of JIT
To understand JIT’s success in integrating logistics and production planning, it’s crucial to recognize its foundational elements.
One key aspect is demand forecasting, which involves predicting production requirements with high accuracy to ensure raw materials and components are available just when needed.
Another element is supplier collaboration, which is essential for timely delivery of inputs.
Effective communication channels and technology infrastructure, such as digital tracking and automated ordering systems, are also critical in implementing JIT successfully.
Successful Case Studies
JIT has proven successful across various industries by optimizing production processes and reducing waste.
Here are some exemplary case studies that showcase the successful integration of logistics and production planning through JIT.
Toyota: Pioneer of JIT
Toyota Motor Corporation is the textbook example of JIT, often referred to as the Toyota Production System (TPS).
The integration was so successful that it reduced the company’s inventory costs and led to the development of lean manufacturing.
Toyota’s approach involves close partnerships with suppliers, adopting a pull system where production is based on customer demand rather than forecasts.
Whenever an order is made, it triggers a cascade of events where each component required is delivered just in time for assembly.
This system reduces waste, minimizes storage costs, and improves the production process, making it a benchmark for other industries.
Harley-Davidson
Harley-Davidson, the iconic motorcycle manufacturer, is another success story.
In the early 1980s, the company faced severe financial challenges, which triggered a transformation process including the adoption of JIT.
By implementing JIT, Harley-Davidson improved production efficiency and product quality.
The company forged solid relationships with its suppliers and adopted a modular assembly process which, in conjunction with real-time data analytics, streamlined operations dramatically.
As a result, they saw an increase in customer satisfaction, quicker response times to market changes, and significant cost savings.
Apple Inc.
Apple Inc., known for its innovative products and efficient supply chain, uses JIT principles to maintain its competitive edge.
Apple’s strategy includes strategic partnerships with suppliers and logistics providers, which ensures the company can meet customer demands promptly without holding excessive stock.
By leveraging JIT, Apple minimizes inventory costs and avoids surplus production, which is crucial for electronics that rapidly become obsolete.
The company’s robust logistics framework, with precise demand forecasting and strategic supplier location near assembly plants, is a testament to JIT’s effective integration.
Benefits of Integrating Logistics with JIT
The integration of logistics into the JIT strategy offers myriad benefits to companies seeking lean operations and cost savings.
Reduced Inventory Costs
With JIT, companies only stock what is necessary at any given time, which reduces the costs associated with overproduction and excess inventory.
This efficiency leads to significant savings, which can be channeled into other business areas.
Improved Efficiency
JIT helps streamline operations across the supply chain from production to logistics.
This system reduces the need for unnecessary movement and handling of goods, which translates to lower operational costs and faster turnaround times.
Enhanced Supplier Relationships
The close collaboration required between firms and their suppliers fosters trust and reliability.
This partnership ensures that logistics are aligned with production needs seamlessly, leading to more predictable and reliable supply chains.
Challenges in Implementing JIT
While JIT has substantial merits, it is not without challenges in its implementation.
Dependency on Suppliers
A significant risk in JIT is over-dependence on suppliers.
Any disruption from a supplier, such as delays or quality issues, can halt the entire production process.
Demand Forecasting
JIT relies heavily on accurate demand forecasting.
Any errors can lead to either shortages or surpluses, both of which are undesirable.
Efficient systems must be in place to ensure data accuracy and forecast reliability.
Infrastructure Requirements
JIT requires robust technology, communication systems, and infrastructure.
Investing in these systems can be costly and complex but is necessary for JIT’s success.
Conclusion
The JIT strategy’s integration with logistics and production planning has proven to be an effective tool for enhancing efficiency and reducing costs in various industries.
Companies like Toyota, Harley-Davidson, and Apple demonstrate how JIT can lead to improved processes, greater efficiency, and strengthened supplier relationships.
While challenges exist, the benefits of a successful JIT implementation can significantly outweigh the potential drawbacks.
Businesses considering JIT must weigh the costs and benefits carefully and ensure they are prepared to meet the demands of this strategic approach.
資料ダウンロード
QCD調達購買管理クラウド「newji」は、調達購買部門で必要なQCD管理全てを備えた、現場特化型兼クラウド型の今世紀最高の購買管理システムとなります。
ユーザー登録
調達購買業務の効率化だけでなく、システムを導入することで、コスト削減や製品・資材のステータス可視化のほか、属人化していた購買情報の共有化による内部不正防止や統制にも役立ちます。
NEWJI DX
製造業に特化したデジタルトランスフォーメーション(DX)の実現を目指す請負開発型のコンサルティングサービスです。AI、iPaaS、および先端の技術を駆使して、製造プロセスの効率化、業務効率化、チームワーク強化、コスト削減、品質向上を実現します。このサービスは、製造業の課題を深く理解し、それに対する最適なデジタルソリューションを提供することで、企業が持続的な成長とイノベーションを達成できるようサポートします。
オンライン講座
製造業、主に購買・調達部門にお勤めの方々に向けた情報を配信しております。
新任の方やベテランの方、管理職を対象とした幅広いコンテンツをご用意しております。
お問い合わせ
コストダウンが利益に直結する術だと理解していても、なかなか前に進めることができない状況。そんな時は、newjiのコストダウン自動化機能で大きく利益貢献しよう!
(Β版非公開)