- お役立ち記事
- APQP (Advanced Quality Planning) implementation guide for production control departments aiming to improve quality
APQP (Advanced Quality Planning) implementation guide for production control departments aiming to improve quality
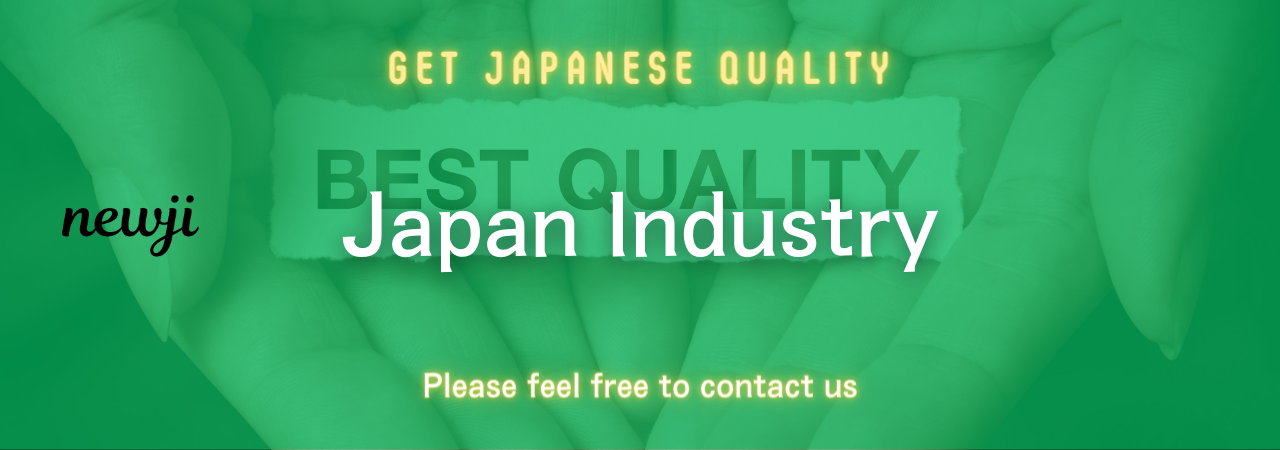
目次
Understanding APQP and Its Importance
Advanced Product Quality Planning (APQP) is a structured framework designed to guide the processes of designing and developing products with consistent quality.
Primarily used in the automotive industry, APQP aims to ensure that the product meets customer requirements in a cost-efficient and timely manner.
It involves cross-functional teams working together to identify potential issues upfront, therefore minimizing risks further down the production line.
For production control departments, embracing APQP serves as a crucial strategy to streamline operations and enhance product quality.
With its proactive approach, APQP not only helps companies in achieving customer satisfaction but also aids in reducing waste and avoiding costly last-minute changes.
Key Elements of APQP
When implementing APQP in production control, it’s essential to understand its key components, which cover various phases of product development.
These elements guide teams through planning, decision-making, and implementation processes.
1. Planning and Definition
During the planning and definition stage, the focus is on understanding the customer needs and expectations.
This phase involves identifying objectives, defining scopes, and setting timelines.
Collecting feedback from stakeholders and ensuring that their requirements are well understood is vital for a successful APQP operation.
2. Product Design and Development
The second phase is where the actual product design takes shape, accommodating the features and specifications identified earlier.
Engineering teams work closely to create a detailed design, ensuring all requirements are thoroughly integrated.
Prototyping may occur in this stage to evaluate design efficacy in real-world scenarios.
3. Process Design and Development
Once the product design is finalized, the next focus is on developing the processes necessary for production.
This includes selecting appropriate technologies, machinery, and crafting process flows that will ensure efficient and quality-focused production.
Considerations like equipment capabilities and capacity planning play critical roles.
4. Product and Process Validation
Validation is a critical step where product designs and processes are tested against customer-requirements and performance expectations.
This involves extensive testing and quality checks to ensure that everything operates smoothly and efficiently before mass production begins.
Any flaws identified at this stage are addressed before the product reaches the consumer market.
5. Production Launch, Assessment, and Continuous Improvement
The final stage involves the initial production run termed as ‘pilot production’.
Here, feedback and performance assessments are made to validate the full production process.
Additionally, APQP emphasizes continuous improvement, encouraging constant evaluation and enhancement of both product and process efficiency over time.
Benefits of APQP for Production Control Departments
Implementing APQP processes come with several significant benefits tailored to production control departments.
Consistent Product Quality
APQP’s structured approach ensures that quality is built into each phase of product development, leading to consistently high-quality products.
This consistency is vital for manufacturers seeking to maintain customer satisfaction and brand reputation.
Reduced Risks and Costs
By identifying potential issues early in the product development stage, APQP helps in reducing risks, leading to fewer costly errors and changes during production.
Moreover, streamlined processes mean less wastage, contributing to significant cost savings.
Enhanced Collaboration and Communication
One of the cornerstones of APQP is its emphasis on teamwork and communication across different departments.
This collaborative approach ensures that all stakeholders are on the same page, resulting in fewer misunderstandings or gaps in the production process.
Predictable Timelines and Delivery
Through meticulous planning and validation processes, APQP contributes to more predictable production timelines.
This helps the production control department in managing resources better and ensuring timely product delivery to customers.
Implementing APQP in Your Production Control Department
For successful implementation of APQP in your department, several strategies can be adopted.
Get Leadership Buy-In
Senior management’s commitment is crucial for successful APQP implementation.
Leadership must understand the benefits and provide the necessary resources and support for effective execution.
Training and Education
Training staff and providing them with the right tools and knowledge for executing APQP processes is vital.
Invest in workshops and courses that delve into methodologies and practical application of APQP principles.
Utilize Technology
Leverage technological advancements like simulation tools and project management software that can assist in APQP processes.
These tools can help streamline tasks and enhance accuracy in planning and validation stages.
Cross-Functional Teams
Encourage the formation of cross-functional teams to foster collaboration.
Drawing skills and expertise from various departments ensures a comprehensive approach to problem-solving across the APQP lifecycle.
Conclusion
APQP serves as an indispensable tool for production control departments striving to improve product quality while optimizing efficiency.
With its detailed framework, APQP equips teams with the means to plan, execute, and evaluate their processes strategically.
By embracing this systematic approach, production control departments can ensure their products meet high-quality standards, satisfy customer expectations, and maintain a strong presence in competitive markets.
Ultimately, implementing APQP is not just about maintaining quality; it’s about driving innovation and sustainable growth in manufacturing operations.
資料ダウンロード
QCD調達購買管理クラウド「newji」は、調達購買部門で必要なQCD管理全てを備えた、現場特化型兼クラウド型の今世紀最高の購買管理システムとなります。
ユーザー登録
調達購買業務の効率化だけでなく、システムを導入することで、コスト削減や製品・資材のステータス可視化のほか、属人化していた購買情報の共有化による内部不正防止や統制にも役立ちます。
NEWJI DX
製造業に特化したデジタルトランスフォーメーション(DX)の実現を目指す請負開発型のコンサルティングサービスです。AI、iPaaS、および先端の技術を駆使して、製造プロセスの効率化、業務効率化、チームワーク強化、コスト削減、品質向上を実現します。このサービスは、製造業の課題を深く理解し、それに対する最適なデジタルソリューションを提供することで、企業が持続的な成長とイノベーションを達成できるようサポートします。
オンライン講座
製造業、主に購買・調達部門にお勤めの方々に向けた情報を配信しております。
新任の方やベテランの方、管理職を対象とした幅広いコンテンツをご用意しております。
お問い合わせ
コストダウンが利益に直結する術だと理解していても、なかなか前に進めることができない状況。そんな時は、newjiのコストダウン自動化機能で大きく利益貢献しよう!
(Β版非公開)