- お役立ち記事
- For new managers in the manufacturing department! Approach to embedding 5S activities into company culture
For new managers in the manufacturing department! Approach to embedding 5S activities into company culture
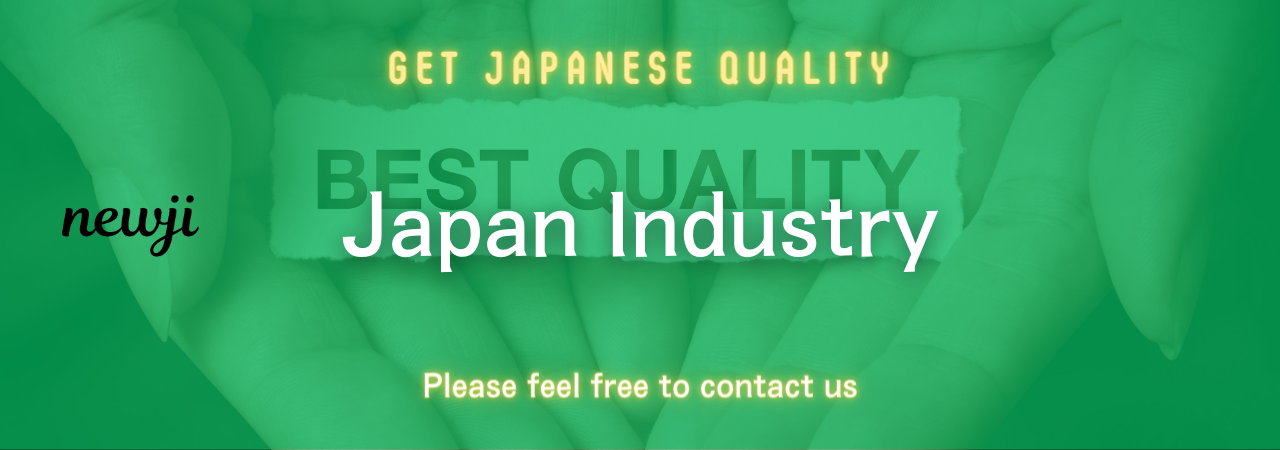
目次
Understanding 5S Activities
The concept of 5S activities is pivotal in establishing a productive and efficient working environment, especially within the manufacturing department.
Originating from Japan, 5S stands for five Japanese words: Seiri (Sort), Seiton (Set in order), Seiso (Shine), Seiketsu (Standardize), and Shitsuke (Sustain).
These principles are aimed at organizing workplaces to increase efficiency, reduce waste, and enhance work quality.
For new managers in manufacturing, embedding these practices into the company culture is a crucial step towards operational excellence.
5S activities not only streamline operations but also improve safety and boost employee morale.
By adopting these strategies, businesses can experience smoother workflows, higher productivity levels, and a more engaged workforce.
Benefits of 5S in Manufacturing
Implementing 5S activities within a manufacturing setting offers a multitude of benefits.
Firstly, it aids in reducing clutter, making it easier for employees to find tools and materials.
This reduction in time waste directly translates into increased productivity.
Moreover, a clean and organized environment minimizes the risks of accidents, thus enhancing the overall safety of the workplace.
Having a standardized system in place ensures that each employee knows exactly where everything belongs, promoting a sense of ownership and responsibility.
Additionally, integrating 5S into your company culture fosters an atmosphere of continuous improvement.
When employees see tangible results from their efforts in organizing and maintaining their workspace, they are more likely to engage proactively in identifying and implementing further improvements.
Steps to Embed 5S in Company Culture
1. Start with Education and Training
For 5S to take root, employees need to understand its significance and the impact it can have on their daily work.
Organize training sessions to educate your team about the principles of 5S and its benefits.
Include real-life examples and engage them in discussions to ensure that they grasp the necessity of these activities in maintaining an efficient workspace.
2. Lead by Example
Managers who embody 5S principles lead their teams more effectively.
Set an example by maintaining an organized work area and consistently following the 5S practices.
When employees see leadership taking these principles seriously, they are more inclined to mimic those behaviors.
3. Customize Strategies
Every manufacturing setup is unique, so tailor the 5S activities to fit your company’s specific needs.
Engage with your team to understand their challenges and perceptions, and collaborate on finding solutions that align with 5S goals.
This collaborative approach helps in gaining buy-in from the team, making them feel valued and involved in the change process.
4. Communicate and Celebrate Achievements
Clear communication about ongoing 5S efforts and their outcomes is essential.
Regularly update the team on progress and recognize areas of improvement.
Celebrate achievements, however small, to motivate employees and keep the enthusiasm alive for maintaining the 5S activities.
5. Establish a Monitoring System
To ensure the successful embedding of 5S into your company culture, set up a monitoring system.
This could include regular audits, feedback from employees, and performance metrics related to efficiency and safety.
Monitoring allows you to track adherence to 5S principles and identify areas for further enhancement.
Overcoming Challenges
Like any other change initiative, introducing 5S into a company culture may encounter resistance.
Employees may perceive it as additional work or be skeptical about its benefits.
Address these concerns by maintaining open lines of communication and providing evidence of the positive impacts 5S has had in other settings.
Another challenge could be sustaining the momentum over time.
Regular reinforcement through training, recognition, and integration of 5S into everyday routines can help maintain it as a critical component of your workplace culture.
Continuous emphasis from leadership on the importance of 5S will also play a significant role in overcoming these challenges.
The Role of Leadership
Leadership plays a crucial role in the successful implementation of 5S activities.
As a manager, it is vital to communicate the strategic importance of 5S principles and how they align with the company’s broader goals.
Displaying a commitment to these values reassures employees of their significance and encourages them to participate actively.
Furthermore, leaders are instrumental in breaking down barriers and driving a culture of change.
By creating an environment where feedback is valued and improvements are welcome, managers can foster a culture where 5S becomes second nature to all employees.
Conclusion
For new managers in the manufacturing department, embedding 5S activities into the company culture is more than just organizing tools and cleaning workspaces.
It is about instilling a mindset that values efficiency, safety, and continuous improvement.
Through education, leading by example, and consistent communication, these practices can become an integral part of your workplace culture.
Overcoming resistance, monitoring progress, and celebrating successes are critical steps in ensuring long-term adoption and success of 5S activities.
By integrating these principles, managers can create a productive environment that not only boosts morale but also elevates the overall performance of the manufacturing department.
資料ダウンロード
QCD調達購買管理クラウド「newji」は、調達購買部門で必要なQCD管理全てを備えた、現場特化型兼クラウド型の今世紀最高の購買管理システムとなります。
ユーザー登録
調達購買業務の効率化だけでなく、システムを導入することで、コスト削減や製品・資材のステータス可視化のほか、属人化していた購買情報の共有化による内部不正防止や統制にも役立ちます。
NEWJI DX
製造業に特化したデジタルトランスフォーメーション(DX)の実現を目指す請負開発型のコンサルティングサービスです。AI、iPaaS、および先端の技術を駆使して、製造プロセスの効率化、業務効率化、チームワーク強化、コスト削減、品質向上を実現します。このサービスは、製造業の課題を深く理解し、それに対する最適なデジタルソリューションを提供することで、企業が持続的な成長とイノベーションを達成できるようサポートします。
オンライン講座
製造業、主に購買・調達部門にお勤めの方々に向けた情報を配信しております。
新任の方やベテランの方、管理職を対象とした幅広いコンテンツをご用意しております。
お問い合わせ
コストダウンが利益に直結する術だと理解していても、なかなか前に進めることができない状況。そんな時は、newjiのコストダウン自動化機能で大きく利益貢献しよう!
(Β版非公開)