- お役立ち記事
- Mastering Precision: The Role of Inner Diameter Measuring Machines in Revolutionizing Japanese Manufacturing
Mastering Precision: The Role of Inner Diameter Measuring Machines in Revolutionizing Japanese Manufacturing
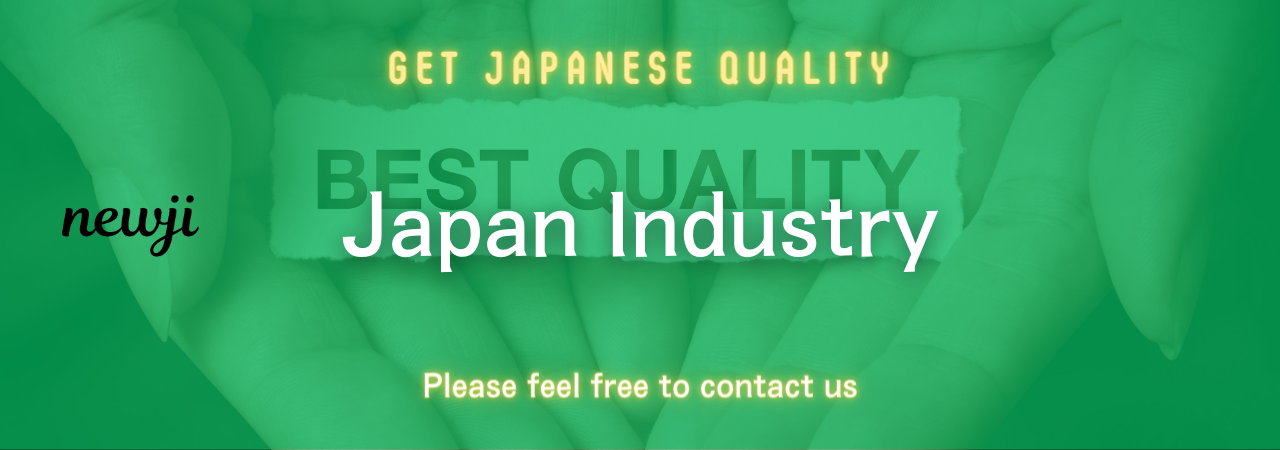
目次
Introduction to Inner Diameter Measuring Machines in Japanese Manufacturing
Japanese manufacturing has long been synonymous with precision, quality, and innovation. Central to maintaining these high standards is the use of advanced measuring technologies, particularly inner diameter measuring machines. These instruments play a critical role in ensuring that components meet stringent specifications, thereby enhancing overall product reliability and performance. This article delves into the significance of inner diameter measuring machines in revolutionizing Japanese manufacturing, exploring their advantages, challenges, and best practices from a procurement and purchasing perspective.
The Importance of Precision in Manufacturing
Precision is a cornerstone of Japanese manufacturing excellence. From automotive parts to electronics, the demand for components that fit perfectly and function seamlessly is paramount. Inner diameter measuring machines are essential tools that help manufacturers achieve this level of precision. By accurately measuring the internal dimensions of components, these machines ensure that parts are produced within tight tolerances, minimizing defects and enhancing product quality.
Enhancing Product Quality
High-precision measurements allow for the consistent production of components that meet exact specifications. This consistency is crucial in industries where even minor deviations can lead to significant performance issues or product failures. Inner diameter measuring machines contribute to maintaining these standards by providing reliable and repeatable measurements, thereby reducing the likelihood of defects and enhancing overall product quality.
Reducing Waste and Costs
Accurate measurements help in minimizing material waste by ensuring that only components within specified tolerances are approved for use. This reduces the need for rework and scrap, leading to significant cost savings. Additionally, minimizing waste contributes to more sustainable manufacturing practices, aligning with the global emphasis on environmental responsibility.
Advantages of Inner Diameter Measuring Machines
Investing in inner diameter measuring machines offers numerous benefits to Japanese manufacturers. These advantages span across quality assurance, production efficiency, and supplier relationships.
Precision and Accuracy
One of the primary advantages of inner diameter measuring machines is their ability to deliver precise and accurate measurements. Advanced technologies, such as laser measurement and automated data processing, enhance the reliability of these instruments. This precision ensures that components meet strict specifications, which is critical for maintaining the high-quality standards associated with Japanese manufacturing.
Improved Production Efficiency
Inner diameter measuring machines streamline the quality control process by providing rapid and accurate measurements. This efficiency allows for faster production cycles and reduces downtime associated with manual measuring methods. Automated systems can integrate seamlessly with production lines, facilitating real-time quality monitoring and prompt corrective actions when deviations are detected.
Enhanced Data Management
Modern inner diameter measuring machines are equipped with sophisticated data management capabilities. They can store and analyze measurement data, providing valuable insights into production trends and quality issues. This data-driven approach enables manufacturers to implement continuous improvement strategies, optimizing processes and enhancing overall manufacturing performance.
Supplier Negotiation and Quality Assurance
For procurement and purchasing departments, having reliable measuring equipment like inner diameter measuring machines strengthens negotiations with suppliers. Demonstrating a commitment to quality through precise measurements can lead to better terms, improved supplier performance, and stronger partnerships.
Challenges in Implementing Inner Diameter Measuring Machines
While the benefits are substantial, integrating inner diameter measuring machines into manufacturing processes presents several challenges. Addressing these hurdles is essential for maximizing the advantages of these technologies.
High Initial Investment
Advanced inner diameter measuring machines often require significant capital investment. The cost of high-precision equipment can be a barrier, especially for small to medium-sized enterprises. However, the long-term benefits, including reduced waste and improved quality, can offset the initial expenditure.
Technical Expertise
Operating and maintaining inner diameter measuring machines requires specialized technical knowledge. Manufacturers must invest in training their workforce to ensure proper usage and upkeep of the equipment. Without adequate expertise, the potential of these machines may not be fully realized, leading to inefficiencies and measurement inaccuracies.
Integration with Existing Systems
Seamlessly integrating inner diameter measuring machines with existing manufacturing systems can be challenging. Compatibility issues with software and hardware, as well as the need for data synchronization, must be addressed to ensure smooth operations. Effective integration is crucial for maximizing the efficiency and effectiveness of these measuring tools.
Supplier Negotiation Techniques for Procuring Measuring Machines
Effective negotiation with suppliers is vital for securing the best possible deals on inner diameter measuring machines. Here are some strategies to enhance negotiation outcomes.
Research and Preparation
Thoroughly researching potential suppliers and understanding their offerings is the first step in successful negotiations. Evaluate the technical specifications, reliability, and support services of different machines to determine the best fit for your manufacturing needs. Familiarity with the market conditions and pricing trends will provide a solid foundation for discussions.
Building Strong Relationships
Cultivating strong relationships with suppliers can lead to more favorable terms and better support. Engage with suppliers who demonstrate a commitment to quality and innovation. Long-term partnerships often result in trust and collaboration, facilitating smoother negotiations and enhanced mutual benefits.
Leveraging Bulk Purchases
If your company requires multiple measuring machines or plans to scale its operations, negotiating bulk purchase discounts can be advantageous. Suppliers are often willing to offer price reductions for larger orders, resulting in significant cost savings.
Considering Total Cost of Ownership
When negotiating, consider the total cost of ownership rather than just the upfront price. Factors such as maintenance costs, training expenses, and the lifespan of the equipment should be taken into account. A slightly higher initial investment may be justified by lower long-term costs and greater reliability.
Market Conditions and Trends
Understanding the current market conditions and emerging trends is crucial for making informed procurement decisions regarding inner diameter measuring machines.
Technological Advancements
The field of precision measurement is continually evolving, with advancements in laser technology, automation, and data analytics driving improvements in inner diameter measuring machines. Staying abreast of these developments can help manufacturers select the most advanced and efficient equipment available.
Global Supply Chain Dynamics
Global supply chain fluctuations can impact the availability and pricing of measuring machines. Factors such as geopolitical tensions, trade policies, and supply chain disruptions must be considered when planning procurement strategies. Building flexibility into purchasing plans can mitigate the risks associated with these uncertainties.
Demand for Customization
As manufacturers increasingly seek customized solutions to meet specific production requirements, the demand for versatile and adaptable measuring machines grows. Suppliers offering customizable features and scalable options are better positioned to meet the evolving needs of the manufacturing sector.
Best Practices in Procuring Inner Diameter Measuring Machines
Adopting best practices in procurement ensures that manufacturers select the right inner diameter measuring machines that align with their quality and efficiency goals.
Define Clear Requirements
Clearly outline your measurement needs, including the range of diameters, required accuracy, and integration capabilities. Detailed specifications help in selecting machines that precisely meet your manufacturing demands, avoiding costly mismatches and ensuring seamless operational integration.
Evaluate Supplier Reputation
Choose suppliers with a proven track record of reliability and quality. Assess their reputation through customer reviews, case studies, and industry certifications. A reputable supplier is more likely to provide high-quality equipment and reliable after-sales support.
Assess After-Sales Support
The availability of comprehensive after-sales support, including training, maintenance, and technical assistance, is crucial. Effective support services ensure that your measuring machines operate efficiently and that any issues are promptly addressed, minimizing downtime and maintaining production continuity.
Conduct Trials and Demonstrations
Before finalizing a purchase, conduct trials or request demonstrations of the measuring machines. Hands-on evaluation allows you to assess the functionality, ease of use, and compatibility with your existing systems. This practical assessment helps in making an informed decision based on real-world performance.
Implement Continuous Training Programs
Ongoing training for staff ensures that they are proficient in operating and maintaining inner diameter measuring machines. Continuous education initiatives help in keeping the workforce updated with the latest technologies and best practices, enhancing overall operational efficiency.
Case Studies: Success Stories in Japanese Manufacturing
Examining real-world examples of Japanese manufacturers successfully implementing inner diameter measuring machines provides valuable insights into best practices and achievable benefits.
Automotive Industry Excellence
A leading Japanese automotive manufacturer integrated advanced inner diameter measuring machines into their production line. The implementation resulted in a 15% reduction in component defects and a 10% increase in production efficiency. The accurate measurements facilitated better quality control, contributing to the company’s reputation for reliability and excellence.
Electronics Manufacturing Innovation
A prominent electronics manufacturer adopted inner diameter measuring machines to enhance the precision of component assemblies. The initiative led to improved product performance and a significant decrease in warranty claims. The data collected from the measuring machines also enabled the company to optimize their manufacturing processes, fostering continuous improvement.
The Future of Inner Diameter Measuring Machines in Manufacturing
The future of inner diameter measuring machines in Japanese manufacturing looks promising, with ongoing advancements set to further revolutionize the industry.
Integration with Industry 4.0
As manufacturing embraces Industry 4.0, the integration of inner diameter measuring machines with smart manufacturing systems will become increasingly important. Connectivity with Internet of Things (IoT) devices and advanced data analytics will enable real-time monitoring and predictive maintenance, enhancing operational efficiency and reducing downtime.
Advancements in Automation and AI
Automation and artificial intelligence (AI) are poised to play significant roles in the evolution of inner diameter measuring machines. Automated measurement processes combined with AI-driven data analysis will lead to more accurate and efficient quality control, allowing manufacturers to achieve higher levels of precision and productivity.
Sustainability and Green Manufacturing
Sustainable manufacturing practices are gaining traction globally, including in Japan. Inner diameter measuring machines contribute to sustainability by reducing material waste and optimizing resource usage. Future advancements may focus on enhancing energy efficiency and incorporating eco-friendly materials, aligning with the broader goals of green manufacturing.
Conclusion
Inner diameter measuring machines are indispensable tools in the landscape of Japanese manufacturing, underpinning the industry’s commitment to precision, quality, and innovation. By investing in these advanced measuring technologies, manufacturers can achieve higher levels of product quality, reduce wastage, and enhance production efficiency. Despite the challenges associated with initial investments and technical expertise, the long-term benefits make inner diameter measuring machines a valuable asset. Through effective procurement strategies, strong supplier relationships, and adherence to best practices, Japanese manufacturers can continue to lead the global market, setting benchmarks for excellence and reliability. As technology advances and the industry evolves, inner diameter measuring machines will remain at the forefront of manufacturing innovation, driving continuous improvement and sustaining Japan’s reputation for manufacturing prowess.
資料ダウンロード
QCD調達購買管理クラウド「newji」は、調達購買部門で必要なQCD管理全てを備えた、現場特化型兼クラウド型の今世紀最高の購買管理システムとなります。
ユーザー登録
調達購買業務の効率化だけでなく、システムを導入することで、コスト削減や製品・資材のステータス可視化のほか、属人化していた購買情報の共有化による内部不正防止や統制にも役立ちます。
NEWJI DX
製造業に特化したデジタルトランスフォーメーション(DX)の実現を目指す請負開発型のコンサルティングサービスです。AI、iPaaS、および先端の技術を駆使して、製造プロセスの効率化、業務効率化、チームワーク強化、コスト削減、品質向上を実現します。このサービスは、製造業の課題を深く理解し、それに対する最適なデジタルソリューションを提供することで、企業が持続的な成長とイノベーションを達成できるようサポートします。
オンライン講座
製造業、主に購買・調達部門にお勤めの方々に向けた情報を配信しております。
新任の方やベテランの方、管理職を対象とした幅広いコンテンツをご用意しております。
お問い合わせ
コストダウンが利益に直結する術だと理解していても、なかなか前に進めることができない状況。そんな時は、newjiのコストダウン自動化機能で大きく利益貢献しよう!
(Β版非公開)