- お役立ち記事
- Basics of quality control using 7 QC tools that factory operations departments should know
Basics of quality control using 7 QC tools that factory operations departments should know
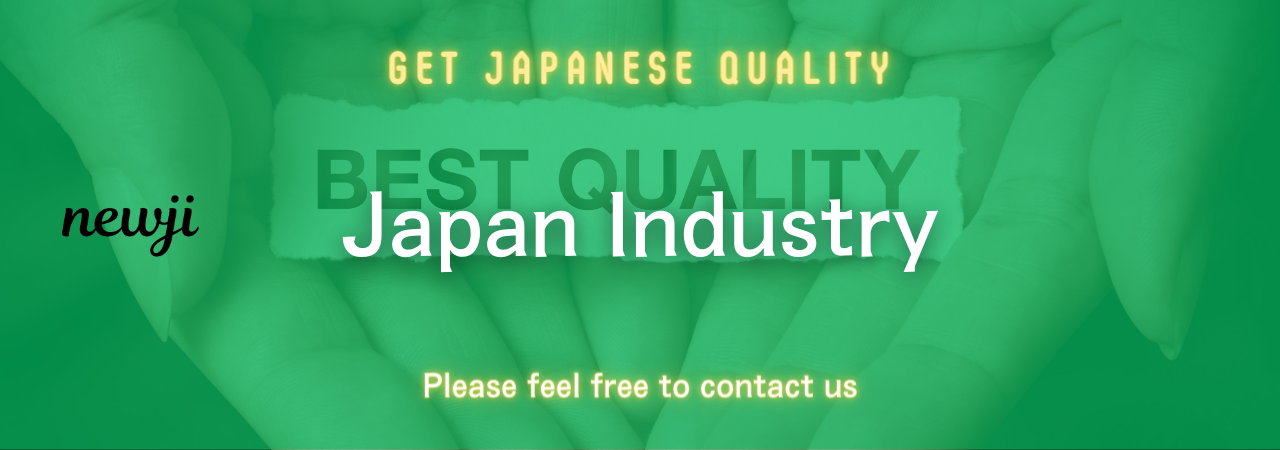
目次
Understanding the Importance of Quality Control
Quality control is a vital aspect of manufacturing and production processes.
It ensures that products meet the required specifications and standards before reaching customers.
This practice not only maintains customer satisfaction but also helps in minimizing production costs by reducing waste and rework.
In the world of manufacturing, upholding quality is imperative to maintaining a competitive edge.
For factory operations departments, mastering the basics of quality control can significantly improve production efficiency and product reliability.
An effective way to implement quality control is through the use of the 7 Quality Control (QC) tools.
These tools are simple yet powerful and can be utilized to diagnose and solve quality-related issues systematically.
The Seven QC Tools: A Closer Look
The 7 QC tools comprise seven fundamental tools that facilitate the quality improvement process.
These tools are versatile and can be adapted to various industries and applications.
Let’s delve into each tool to understand their application and benefits.
1. Cause-and-Effect Diagram (Fishbone Diagram)
The cause-and-effect diagram, also known as the fishbone diagram, helps identify the root causes of a problem.
By categorizing potential sources of variation in a structured form, it enables teams to pinpoint the exact cause of inefficiencies or defects.
The diagram resembles a fish’s skeleton, hence the name, and lists major causes of defects, such as materials, methods, machines, and manpower.
2. Check Sheet
A check sheet is a simple yet effective tool used for data collection.
It helps in gathering, organizing, and analyzing data efficiently, providing a clear picture of how often an event occurs.
Check sheets are customizable and can be adapted for various scenarios, making them a versatile tool in quality control efforts.
3. Control Chart
Control charts are essential for monitoring variability in processes.
They help track the performance of a process over time and identify any unusual variations.
By distinguishing between common cause variation and special cause variation, control charts enable proactive interventions, maintaining process stability and consistency.
4. Histogram
Histograms provide a visual representation of data distribution.
By plotting data as bars, they highlight the frequency of occurrences within different ranges.
This allows quality control teams to visualize data trends and patterns, helping to identify outliers or deviations from normal patterns that might require corrective actions.
5. Pareto Chart
The Pareto chart is based on the Pareto Principle, which states that roughly 80% of problems are caused by 20% of the causes.
This tool focuses on identifying and prioritizing the most significant factors contributing to a problem.
By focusing efforts on the major contributors, teams can achieve more efficient and effective solutions.
6. Scatter Diagram
Scatter diagrams, or scatter plots, help in identifying correlations and relationships between two variables.
By plotting data points on a graph, teams can observe trends and possibly infer causal relationships.
This tool is particularly helpful when trying to understand how changes in one variable might affect another.
7. Flowchart
Flowcharts are diagrams that depict the steps or sequences in a process.
They aid in visualizing and understanding complex processes, making it easier to identify bottlenecks, redundancies, and inefficiencies.
Flowcharts facilitate process optimization by allowing teams to streamline workflows and enhance productivity.
Integrating the 7 QC Tools in Factory Operations
For effective quality control, factory operations departments should embrace these 7 QC tools as part of their regular practices.
Implementing these tools requires a mix of technical knowledge and collaboration across teams.
To begin integrating these tools, the following steps are recommended:
1. **Training and Education**: Introduce the tools to the workforce through workshops and training sessions.
Educating team members on how to utilize these tools effectively will ensure a more comprehensive approach to quality control.
2. **Use Real Data**: Apply these tools to actual data from ongoing production processes.
Real-world data provides valid insights, helping in pinpointing the specific areas that need improvement.
3. **Continuous Improvement**: QC tools should become part of a culture of continuous improvement within the organization.
Regular reviews and updates based on QC tool findings will help in adapting to changing circumstances and maintaining high standards.
4. **Collaboration and Feedback**: Encourage collaboration among different departments and levels within the organization.
Feedback from different stakeholders can lead to more innovative solutions and improvements in quality control initiatives.
5. **Customize for Specific Needs**: While the tools are relatively universal, customizing them for the specific needs and context of your facility can yield better results.
Benefits of Mastering the 7 QC Tools
The advantage of mastering these 7 QC tools lies in their simplicity and effectiveness.
Proper implementation results in reduced defects, lower production costs, improved customer satisfaction, and increased competitiveness.
They help create a proactive quality culture that empowers employees to make informed decisions promoting consistent quality improvements.
Incorporating these QC tools into everyday operations also fosters a deeper understanding of production processes.
It enhances problem-solving capabilities among the workforce while promoting transparency and accountability at all levels.
In conclusion, understanding and applying these 7 QC tools empowers factory operations departments to better manage and improve process quality.
With a comprehensive grasp of these techniques, organizations can enjoy enhanced operational efficiency, leading to superior product quality and greater market success.
資料ダウンロード
QCD調達購買管理クラウド「newji」は、調達購買部門で必要なQCD管理全てを備えた、現場特化型兼クラウド型の今世紀最高の購買管理システムとなります。
ユーザー登録
調達購買業務の効率化だけでなく、システムを導入することで、コスト削減や製品・資材のステータス可視化のほか、属人化していた購買情報の共有化による内部不正防止や統制にも役立ちます。
NEWJI DX
製造業に特化したデジタルトランスフォーメーション(DX)の実現を目指す請負開発型のコンサルティングサービスです。AI、iPaaS、および先端の技術を駆使して、製造プロセスの効率化、業務効率化、チームワーク強化、コスト削減、品質向上を実現します。このサービスは、製造業の課題を深く理解し、それに対する最適なデジタルソリューションを提供することで、企業が持続的な成長とイノベーションを達成できるようサポートします。
オンライン講座
製造業、主に購買・調達部門にお勤めの方々に向けた情報を配信しております。
新任の方やベテランの方、管理職を対象とした幅広いコンテンツをご用意しております。
お問い合わせ
コストダウンが利益に直結する術だと理解していても、なかなか前に進めることができない状況。そんな時は、newjiのコストダウン自動化機能で大きく利益貢献しよう!
(Β版非公開)