- お役立ち記事
- The forefront of cost management using economical engineering that finance departments should keep in mind
The forefront of cost management using economical engineering that finance departments should keep in mind
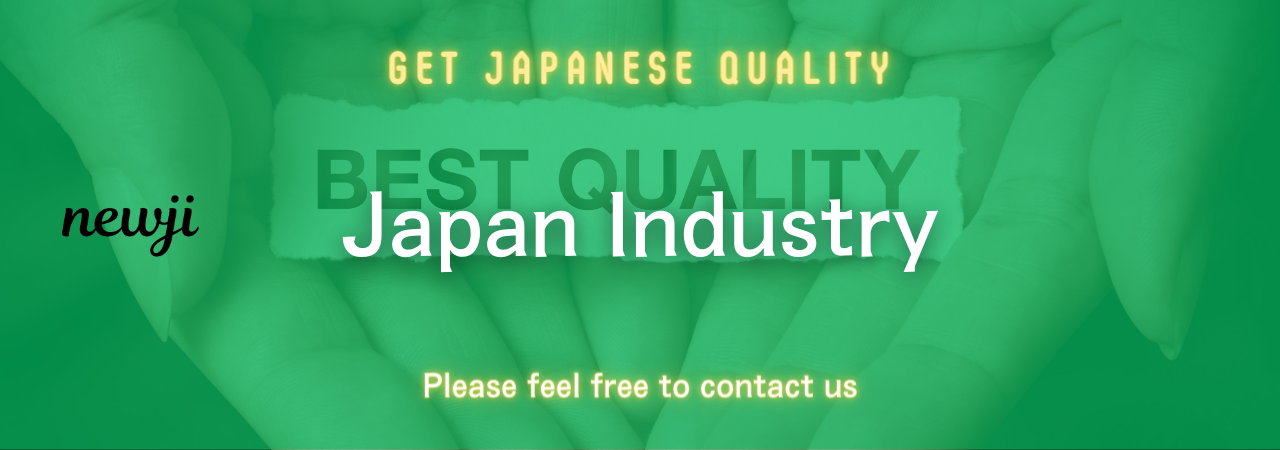
目次
Understanding Economical Engineering
Economical engineering, often referred to as value engineering, is a systematic approach to improving the value of goods or products by utilizing an examination of function.
The goal is to reduce costs without sacrificing quality, reliability, performance, or even aesthetics.
This approach is particularly important for finance departments as it helps in maintaining budget efficiency and ensuring that resources are utilized in the most effective manner possible.
By integrating economical engineering principles, companies can achieve substantial cost savings and develop more cost-effective solutions.
For finance departments, incorporating these strategies can seem daunting, but understanding the basic principles is a good starting point.
Simply put, economical engineering focuses on understanding the essential functions of a product or service and eliminating unnecessary costs while achieving the desired performance and quality.
The Importance of Cost Management
Cost management is a critical function of any finance department.
It involves planning, controlling, and monitoring the cost associated with any process, which allows businesses to improve profitability and make informed financial decisions.
Economical engineering plays a vital role in this, as it enables finance departments to identify and implement cost-saving measures.
Effective cost management through economical engineering not only helps organizations stay competitive but also enhances their ability to cope with fluctuating market conditions and unforeseen expenses.
By keeping constant track of costs, finance departments can ensure that financial resources are allocated optimally, and potential savings are not overlooked.
How Economical Engineering Can Benefit Finance Departments
1. Enhanced Budget Control
Economical engineering provides a systematic approach to analyze each component of a project or product to determine its cost-effectiveness.
This allows finance departments to better manage budgets by identifying areas where overspending can be curbed.
By focusing on the functions necessary for performance and discarding unnecessary features, teams can avoid budget overruns and optimize resource allocation.
2. Improved Decision Making
With a focus on function-based costing, finance departments can make more informed decisions about resource allocation.
Economical engineering encourages critical analysis and evaluation of various components, ensuring that only the most viable and cost-effective options are chosen.
This leads to better decision-making and ultimately supports the organization’s financial health and strategic goals.
3. Greater Cost Transparency
By understanding every component’s function and its associated costs, economical engineering provides greater transparency into where money is being spent.
This detail allows finance departments to track expenses accurately and justify expenditures, ensuring accountability within the organization.
By clarifying costs associated with different functions, management can implement adjustments promptly.
4. Fostering Innovation
One of the side benefits of employing economical engineering is fostering a culture of innovation.
When finance departments focus on optimizing costs and functions, they are naturally drawn towards finding new, efficient ways to achieve goals.
This leads to innovation, which can further drive down costs and improve performance, giving the company a competitive edge.
Key Steps in Economical Engineering
Step 1: Analyze Costs
The first step in economical engineering is a thorough analysis of costs.
Finance departments must identify all the associated costs of a product, process, or service and determine their importance.
Separating necessary costs from those that are not essential will highlight potential savings.
Step 2: Identify Functions
Understand the primary functions of the item or process in question.
Determine which functions must remain uninterrupted and which can be modified or eliminated without impacting the overall performance or quality.
This helps in identifying areas where costs can be reduced.
Step 3: Evaluate Alternatives
Once functions have been analyzed, teams should brainstorm alternative approaches to achieving the same results at a lower cost.
This step may involve creative thinking and collaboration with engineering, production, and other relevant departments within the organization.
Step 4: Implement Cost-Saving Measures
After evaluating alternatives and selecting the most cost-effective options, implement the changes.
These could involve rethinking designs, altering materials, improving processes, or negotiating cost-effective supplier relationships.
Step 5: Monitor and Review
Finally, it is crucial to continually monitor the results of the newly implemented changes and review their impacts on cost and performance.
Regular reviews ensure that the improvements are sustained and further adjustments are made if necessary.
The Role of Technology in Economical Engineering
Technology plays a significant role in economical engineering by providing tools and systems that make cost analysis and optimization more efficient.
Software solutions can assist finance departments with detailed cost analysis, function identification, and alternative evaluation.
Automation and data analytics enable more comprehensive monitoring of expenses and help in identifying potential areas for cost savings.
By leveraging technological advancements, finance departments can enhance the efficiency and reliability of their cost management procedures significantly.
Conclusion
For finance departments, mastering the art of cost management through economical engineering is indispensable in today’s competitive business environment.
By applying these principles, organizations can achieve significant savings, improve efficiency, and foster innovation while maintaining high-quality standards.
Understanding and implementing economical engineering ensures that finance departments remain strategic partners in driving organizational success.
By focusing on optimizing functions and costs, businesses can stay ahead of market changes and improve their bottom line effectively.
資料ダウンロード
QCD調達購買管理クラウド「newji」は、調達購買部門で必要なQCD管理全てを備えた、現場特化型兼クラウド型の今世紀最高の購買管理システムとなります。
ユーザー登録
調達購買業務の効率化だけでなく、システムを導入することで、コスト削減や製品・資材のステータス可視化のほか、属人化していた購買情報の共有化による内部不正防止や統制にも役立ちます。
NEWJI DX
製造業に特化したデジタルトランスフォーメーション(DX)の実現を目指す請負開発型のコンサルティングサービスです。AI、iPaaS、および先端の技術を駆使して、製造プロセスの効率化、業務効率化、チームワーク強化、コスト削減、品質向上を実現します。このサービスは、製造業の課題を深く理解し、それに対する最適なデジタルソリューションを提供することで、企業が持続的な成長とイノベーションを達成できるようサポートします。
オンライン講座
製造業、主に購買・調達部門にお勤めの方々に向けた情報を配信しております。
新任の方やベテランの方、管理職を対象とした幅広いコンテンツをご用意しております。
お問い合わせ
コストダウンが利益に直結する術だと理解していても、なかなか前に進めることができない状況。そんな時は、newjiのコストダウン自動化機能で大きく利益貢献しよう!
(Β版非公開)