- お役立ち記事
- Essential for Pharmaceutical Manufacturing! Best Practices for GMP Compliance
Essential for Pharmaceutical Manufacturing! Best Practices for GMP Compliance
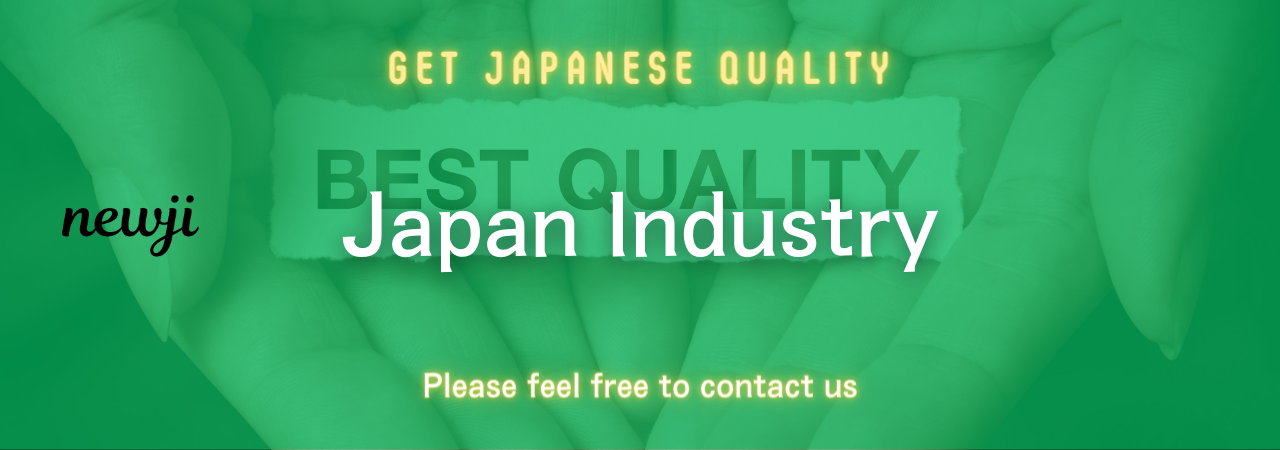
目次
Understanding GMP Compliance
Good Manufacturing Practice, commonly known as GMP, is a system that ensures products are consistently produced and controlled according to quality standards.
In the pharmaceutical industry, GMP compliance is of utmost importance because it directly impacts the safety and efficacy of medications.
Following GMP guidelines helps to prevent contamination, mix-ups, and errors that might compromise the health and safety of consumers.
GMP compliance is mandatory for pharmaceutical manufacturers across the globe.
Authorities like the U.S. Food and Drug Administration (FDA), the European Medicines Agency (EMA), and other regulatory agencies enforce these standards.
Adhering to GMP guidelines not only satisfies regulatory requirements but also enhances the credibility and brand reputation of pharmaceutical companies.
Key Elements of GMP Guidelines
When discussing GMP compliance in pharmaceutical manufacturing, several core elements are integral to the process.
Understanding these fundamentals is the first step towards building a comprehensive compliance strategy.
1. Quality Management
Quality management lies at the heart of GMP compliance.
It involves developing and implementing a quality assurance system that ensures products are manufactured consistently and meet predefined specifications.
This includes regular audits and reviews to identify areas of improvement and to maintain high-quality production processes.
2. Personnel and Training
Proper training and qualification of personnel are crucial components of GMP compliance.
Employees must be adequately trained in current GMP standards relevant to their specific duties.
Ongoing training programs and assessments help ensure that all staff are competent in their roles and understand the importance of adhering to GMP guidelines.
3. Premises and Equipment
The design, location, and maintenance of manufacturing facilities play a significant role in GMP compliance.
Facilities must be constructed to minimize contamination risks, and appropriate measures must be taken to manage temperatures, humidity, and cleanliness.
Equipment must be regularly maintained, calibrated, and validated to ensure optimal performance.
4. Documentation
Comprehensive documentation is a crucial aspect of GMP adherence.
All processes, procedures, and activities must be clearly documented to provide a traceable history of a product’s production lifecycle.
This documentation aids in tracking issues, streamlining audits, and ensuring that products meet quality standards.
5. Laboratory Controls
Laboratory control systems ensure that the testing of raw materials, in-process samples, and finished products are conducted with accuracy and precision.
Properly functioning laboratory controls prevent errors in the manufacturing processes and assure product quality.
Routine validation and testing are essential components of effective laboratory control systems.
Best Practices for GMP Compliance
Implementing GMP guidelines is a continuous process that requires commitment and adaptability from pharmaceutical manufacturers.
Here are some best practices to help maintain GMP compliance effectively:
1. Build a Culture of Compliance
Fostering a culture of compliance within an organization ensures that all employees understand and are committed to adhering to GMP standards.
Achieving this involves providing ongoing education, promoting accountability, and encouraging open communication about compliance matters.
2. Implement Risk Management Strategies
Risk management is critical for identifying and addressing potential hazards in the production environment.
By conducting regular risk assessments, manufacturers can prevent incidents that could compromise product safety and quality.
Implementing robust risk management strategies can also minimize disruptions in production.
3. Conduct Regular Audits and Inspections
Routine audits and inspections help identify any deviations from GMP compliance and provide opportunities for improvement.
Conduct internal audits regularly to assess adherence to all aspects of GMP standards, and address any non-conformities promptly.
4. Stay Updated with Regulatory Changes
Regulatory agencies frequently update GMP guidelines to reflect advancements in technology and changes in industry standards.
Stay informed of these updates and adjust practices accordingly to maintain compliance with current regulations.
5. Leverage Technology for Compliance
Technology can be an invaluable tool for maintaining GMP compliance.
Invest in reliable software solutions that efficiently manage documentation, track production processes, and streamline audits.
Automation can also enhance accuracy and efficiency in documentation and reporting.
Challenges in Achieving GMP Compliance
While aiming for consistent GMP compliance, pharmaceutical manufacturers face challenges that demand constant attention and proactive measures.
1. Global Regulatory Differences
Pharmaceutical manufacturers often encounter varying GMP standards across different countries.
The challenge lies in understanding these differences and complying with the specific regulations of each market.
A global approach to compliance management can help navigate these complexities.
2. Quality Control Over Supply Chain
Managing a complex supply chain involves challenges in maintaining the quality and authenticity of raw materials.
Implementing stringent supplier qualification processes and conducting regular audits are essential practices to ensure supply chain integrity and compliance.
3. Data Integrity
Maintaining data integrity is crucial for traceability and compliance verification.
Pharmaceutical companies must ensure that all records are accurate, accessible, and complete.
Data breaches and discrepancies can result in severe regulatory penalties.
4. Innovation and Compliance
The integration of new technologies and innovative practices can sometimes put pressure on maintaining compliance.
Balancing innovation with adherence to GMP guidelines requires careful consideration and strategic planning.
Conclusion
GMP compliance is non-negotiable for pharmaceutical manufacturing, as it upholds the safety, quality, and efficacy of products.
By understanding the core elements of GMP guidelines, implementing best practices, and addressing the associated challenges, companies position themselves for sustainable success and consumer trust.
A commitment to maintaining GMP compliance ultimately leads to the production of safer medications and better health outcomes for patients worldwide.
資料ダウンロード
QCD調達購買管理クラウド「newji」は、調達購買部門で必要なQCD管理全てを備えた、現場特化型兼クラウド型の今世紀最高の購買管理システムとなります。
ユーザー登録
調達購買業務の効率化だけでなく、システムを導入することで、コスト削減や製品・資材のステータス可視化のほか、属人化していた購買情報の共有化による内部不正防止や統制にも役立ちます。
NEWJI DX
製造業に特化したデジタルトランスフォーメーション(DX)の実現を目指す請負開発型のコンサルティングサービスです。AI、iPaaS、および先端の技術を駆使して、製造プロセスの効率化、業務効率化、チームワーク強化、コスト削減、品質向上を実現します。このサービスは、製造業の課題を深く理解し、それに対する最適なデジタルソリューションを提供することで、企業が持続的な成長とイノベーションを達成できるようサポートします。
オンライン講座
製造業、主に購買・調達部門にお勤めの方々に向けた情報を配信しております。
新任の方やベテランの方、管理職を対象とした幅広いコンテンツをご用意しております。
お問い合わせ
コストダウンが利益に直結する術だと理解していても、なかなか前に進めることができない状況。そんな時は、newjiのコストダウン自動化機能で大きく利益貢献しよう!
(Β版非公開)