- お役立ち記事
- Digital factory construction and operation guide that should be promoted by the production technology department
Digital factory construction and operation guide that should be promoted by the production technology department
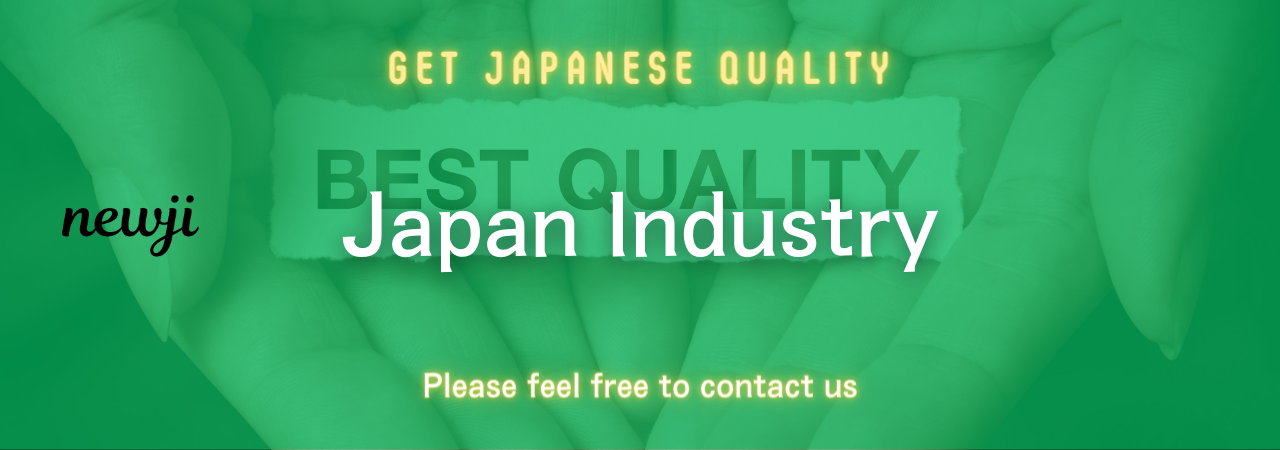
目次
Introduction to Digital Factories
The digital age has brought about transformative changes in various industries, including manufacturing.
One of the most significant advancements is the concept of a digital factory.
A digital factory integrates cutting-edge technologies such as the Internet of Things (IoT), artificial intelligence (AI), robotics, and advanced data analytics to revamp traditional manufacturing processes.
This comprehensive guide will walk you through the construction and operation of a digital factory, emphasizing the crucial role of the production technology department in driving this innovation.
Understanding the Digital Factory
A digital factory is not merely a factory with digital gadgets; it is a fully integrated, technology-driven entity that optimizes every aspect of manufacturing.
Unlike conventional factories that rely heavily on manual processes, digital factories utilize real-time data and advanced computing to enhance efficiency, quality, and flexibility.
Key Components of a Digital Factory
To successfully build and operate a digital factory, it’s essential to understand its key components:
1. **Connected Devices and IoT**: At the heart of a digital factory are interconnected devices and IoT systems that collect and transfer data in real-time.
2. **Advanced Data Analytics**: Data analytics tools analyze this data to provide insights that help in decision-making and process optimization.
3. **Automation and Robotics**: Automated systems and robots perform repetitive tasks with high precision and speed, reducing human error.
4. **AI and Machine Learning**: AI algorithms help predict maintenance needs, optimize production schedules, and improve product quality.
5. **Digital Twin Technology**: This involves creating a virtual model of the factory to simulate operations and identify potential improvements without disrupting actual processes.
The Role of the Production Technology Department
The production technology department is pivotal in the transition to and operation of a digital factory.
Here’s how they can lead the charge:
1. Designing the Digital Infrastructure
This department is responsible for designing the digital architecture of the factory.
They determine which technologies to implement, how they will be integrated, and ensure that all systems communicate effectively.
2. Overseeing Implementation
During the construction phase, the production technology team supervises the installation and integration of digital tools and platforms.
They work closely with IT teams and external vendors to ensure seamless execution.
3. Workforce Training and Development
A major part of digital transformation is upskilling the workforce.
The production technology department should spearhead training programs to ensure employees can effectively interact with digital tools and understand new workflows.
4. Continuous Improvement and Innovation
This department must continually monitor the factory’s digital environment, using data analytics to identify areas for improvement and innovation.
By staying ahead of technological trends, they can maintain competitive advantage.
Steps to Build a Digital Factory
Building a digital factory is a complex but manageable process if approached strategically.
Here are the steps to follow:
1. Conduct a Needs Assessment
Begin by assessing current manufacturing processes to identify areas where digital solutions can add value.
Engage with stakeholders to understand their pain points and aspirations for the digital factory.
2. Develop a Robust Strategy
Based on the assessment, develop a comprehensive strategy.
This should outline the objectives, key technologies, budget, timeline, and metrics for success.
3. Design and Plan
With a strategy in place, design the digital infrastructure.
Plan for the infrastructure that supports digital technologies, taking into account potential future expansions and upgrades.
4. Select the Right Technologies
Choosing the right mix of technologies is crucial.
Consider factors such as cost, compatibility, scalability, and user-friendliness.
5. Implement and Integrate
Execute the plan by implementing the selected technologies and integrating them into existing systems.
Ensure robust cybersecurity measures are in place to protect data and operations.
6. Test and Optimize
Before fully launching the digital factory, conduct thorough testing to ensure all systems function as expected.
Use the feedback to make necessary adjustments.
Operating a Digital Factory
Once the digital factory is operational, the focus shifts to continuous optimization and efficiency.
Here are some key operational strategies:
1. Real-time Monitoring
Utilize real-time data monitoring for instant insights into production status, allowing for rapid response to issues.
2. Predictive Maintenance
Leverage AI and data analytics to predict equipment failures before they occur, minimizing downtime and extending machine life.
3. Supply Chain Integration
Integrate supply chain management with digital factory processes to enhance transparency and reduce lead times.
4. Quality Assurance
Implement digital quality control systems that ensure product specifications are met consistently, reducing defects and waste.
5. Foster Collaboration
Encourage collaboration between departments by utilizing digital communication platforms.
This ensures everyone is aligned and informed.
Conclusion
Embracing digital factory concepts can transform manufacturing operations, making them more efficient, agile, and competitive.
By taking a proactive approach, the production technology department can lead the charge in this digital revolution, ensuring a smooth transition and continuous improvement.
The steps and strategies outlined above provide a comprehensive guide to navigating the journey of constructing and operating a state-of-the-art digital factory.
資料ダウンロード
QCD調達購買管理クラウド「newji」は、調達購買部門で必要なQCD管理全てを備えた、現場特化型兼クラウド型の今世紀最高の購買管理システムとなります。
ユーザー登録
調達購買業務の効率化だけでなく、システムを導入することで、コスト削減や製品・資材のステータス可視化のほか、属人化していた購買情報の共有化による内部不正防止や統制にも役立ちます。
NEWJI DX
製造業に特化したデジタルトランスフォーメーション(DX)の実現を目指す請負開発型のコンサルティングサービスです。AI、iPaaS、および先端の技術を駆使して、製造プロセスの効率化、業務効率化、チームワーク強化、コスト削減、品質向上を実現します。このサービスは、製造業の課題を深く理解し、それに対する最適なデジタルソリューションを提供することで、企業が持続的な成長とイノベーションを達成できるようサポートします。
オンライン講座
製造業、主に購買・調達部門にお勤めの方々に向けた情報を配信しております。
新任の方やベテランの方、管理職を対象とした幅広いコンテンツをご用意しております。
お問い合わせ
コストダウンが利益に直結する術だと理解していても、なかなか前に進めることができない状況。そんな時は、newjiのコストダウン自動化機能で大きく利益貢献しよう!
(Β版非公開)