- お役立ち記事
- Cost Reduction Examples in New Product Development Using VE Methodologies
Cost Reduction Examples in New Product Development Using VE Methodologies
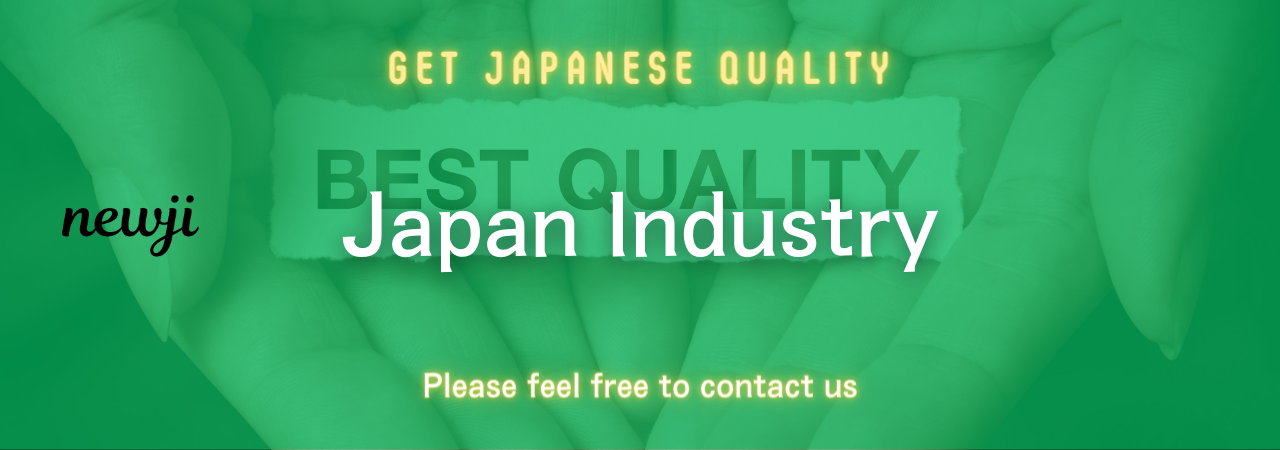
目次
Understanding the VE Methodology
The Value Engineering (VE) methodology is a systematic approach aimed at enhancing the value of a product by using an organized method for analyzing functions of the product.
This technique encourages creativity and innovation, helping industries minimize costs while maintaining or improving their product functions.
The goal is to maximize value by identifying and eliminating unnecessary costs during the development phase of a new product.
By adopting VE methodologies, companies can produce cost-efficient products without compromising on quality or performance.
Importance of Cost Reduction in New Product Development
In today’s competitive market, reducing costs during the new product development process is crucial for companies aiming to achieve sustainable growth.
Effective cost management leads to better pricing strategies, increased market share, and improved profit margins.
Reducing costs not only aids in delivering competitive products but also prepares businesses to adapt to market fluctuations and changing customer expectations.
The VE approach fits seamlessly into this requirement, providing a structured framework to assess and minimize product costs.
Steps Involved in Implementing the VE Methodology
1. Information Gathering
The first step is to gather detailed information about the product, including its components, functions, costs, and production processes.
Understanding the customer’s needs and expectations is also crucial during this stage to ensure the product aligns with user requirements.
Gathering comprehensive data provides a solid foundation for identifying areas where cost-savings can be made without affecting product functionality.
2. Function Analysis
In this step, products are broken down into their core functions to analyze their necessity and explore cost-saving possibilities.
Function analysis helps to determine the essential functions and those that can be modified or eliminated to reduce costs.
This stage is pivotal in identifying redundant elements that do not add value to the final product.
3. Creative Exploration
Creativity is key in this phase, where teams brainstorm various alternative methods and designs to achieve the essential functions of the product.
Diverse groups are encouraged to explore different perspectives and generate innovative solutions, enabling the company to optimize designs for cost-effectiveness.
This brainstorming session is critical for developing multiple solutions that could potentially reduce product costs.
4. Evaluation Process
Once creative ideas have been presented, each alternative is rigorously evaluated based on feasibility, cost implications, and alignment with customer needs.
This process involves a detailed comparison of different proposals against the current design and production methods.
The most viable options are selected for further development and testing.
5. Development and Implementation
The chosen alternative solutions undergo detailed development involving prototyping, testing, and refinement.
The objective is to ensure the new approach meets performance standards and customer expectations while achieving cost savings.
Successful implementations are integrated into the production process, finalizing the VE process.
6. Continuous Monitoring and Improvement
After implementing the VE solutions, companies should continuously monitor product performance and cost savings.
This ongoing evaluation helps to identify further areas for improvement and ensure that cost efficiencies are sustained over the product’s lifecycle.
Continuous improvement is essential for maintaining competitiveness in the ever-evolving market landscape.
Examples of VE Methodologies in Action
Example 1: Automotive Industry
In the automotive sector, manufacturers frequently use VE methodologies for cost-effective design and production of vehicles.
By analyzing the materials and functionalities of car components, companies have transitioned from using heavy metal parts to lighter composite materials.
This strategic change reduces both production costs and vehicle weight, leading to improved fuel efficiency and reduced emissions, enhancing overall vehicle appeal.
Example 2: Electronics Industry
In the electronics industry, value engineering has been instrumental in the development of products like smartphones, laptops, and other devices.
Manufacturers have adopted innovative designs and alternative materials that deliver similar levels of performance at a lower cost.
For instance, the integration of multi-functional chips that combine several features in one unit reduces the cost of production and assembly without compromising on the user experience.
Example 3: Construction Industry
In construction, VE methodologies are applied to project planning and execution to minimize costs while maintaining safety and quality standards.
By opting for prefabricated sections and modern construction techniques, companies reduce both material and labor costs.
These methods not only lower overall expenses but also shorten project timelines, delivering enhanced value to stakeholders.
Challenges and Considerations in VE Implementation
While VE offers significant benefits, implementing it effectively poses several challenges.
One critical issue is resistance to change, as employees may be hesitant to adopt new processes due to familiarity with existing methods.
Another challenge is ensuring a balance between cost reduction and maintaining product quality—overzealous cost-cutting measures can compromise key functionalities.
It is essential to foster a culture of innovation and encourage collaboration across departments to mitigate these challenges.
Proper training and clear communication can help in overcoming resistance and achieving successful VE implementation.
Conclusion
Value Engineering methodologies offer a practical blueprint for achieving cost reduction in new product development.
By systematically analyzing product functions, inspiring creativity, evaluating alternatives, and implementing innovative solutions, companies can effectively design cost-efficient products.
This approach not only enhances a product’s value but also empowers businesses to thrive in competitive marketplaces for the long term.
As industries continue to evolve, adopting VE methodologies can provide the necessary edge to meet growing demands and customer expectations while ensuring profitability.
資料ダウンロード
QCD調達購買管理クラウド「newji」は、調達購買部門で必要なQCD管理全てを備えた、現場特化型兼クラウド型の今世紀最高の購買管理システムとなります。
ユーザー登録
調達購買業務の効率化だけでなく、システムを導入することで、コスト削減や製品・資材のステータス可視化のほか、属人化していた購買情報の共有化による内部不正防止や統制にも役立ちます。
NEWJI DX
製造業に特化したデジタルトランスフォーメーション(DX)の実現を目指す請負開発型のコンサルティングサービスです。AI、iPaaS、および先端の技術を駆使して、製造プロセスの効率化、業務効率化、チームワーク強化、コスト削減、品質向上を実現します。このサービスは、製造業の課題を深く理解し、それに対する最適なデジタルソリューションを提供することで、企業が持続的な成長とイノベーションを達成できるようサポートします。
オンライン講座
製造業、主に購買・調達部門にお勤めの方々に向けた情報を配信しております。
新任の方やベテランの方、管理職を対象とした幅広いコンテンツをご用意しております。
お問い合わせ
コストダウンが利益に直結する術だと理解していても、なかなか前に進めることができない状況。そんな時は、newjiのコストダウン自動化機能で大きく利益貢献しよう!
(Β版非公開)