- お役立ち記事
- Best Practices for Sustainable Factory Operations through Environmental Impact Reduction Technologies
Best Practices for Sustainable Factory Operations through Environmental Impact Reduction Technologies
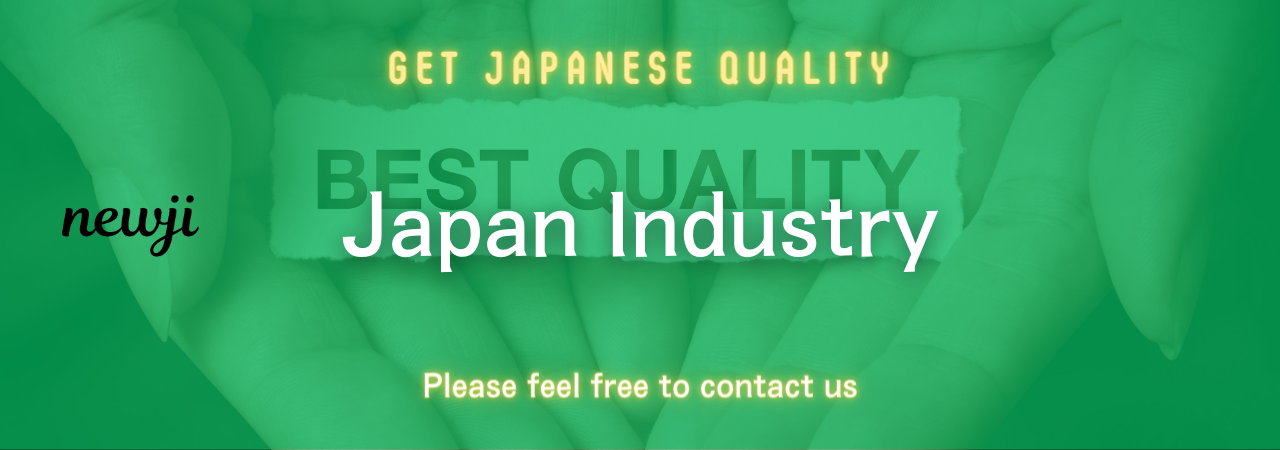
目次
Understanding Sustainable Factory Operations
Sustainable factory operations are more crucial than ever in our rapidly evolving world.
Manufacturers are increasingly recognizing the importance of minimizing their environmental impact to ensure resource efficiency and reduce ecological footprints.
This shift is driven by growing consumer awareness, stringent regulations, and a genuine interest in preserving our planet for future generations.
At its core, sustainable manufacturing seeks to optimize the use of resources while minimizing waste and pollution.
This can be achieved through innovative technologies and practices that focus on efficiency and conservation.
Key Elements of Sustainable Manufacturing
To build a sustainable factory, manufacturers must consider several key elements.
These include energy efficiency, waste reduction, water conservation, and sustainable sourcing of materials.
Each of these elements plays a pivotal role in reducing the overall environmental impact of factory operations.
Energy Efficiency
One of the primary areas to tackle is energy efficiency.
Factories are significant consumers of energy, so finding ways to reduce usage can have a huge impact.
This might involve investing in energy-efficient machinery, using renewable energy sources, or optimizing production schedules to reduce peak energy demand.
Implementing energy management systems can also provide significant benefits by tracking usage patterns and identifying areas for improvement.
Additionally, employees can be trained to follow best practices in energy conservation, such as turning off machines when not in use or scheduling maintenance to keep equipment running efficiently.
Waste Reduction
Another critical component of sustainable operations is waste reduction.
Factories often produce significant waste, from manufacturing byproducts to packaging materials.
To address this, companies can adopt a circular economy approach, focusing on recycling and reusing materials wherever possible.
This starts with a waste audit to understand what waste is being produced and where.
Once identified, manufacturers can explore recycling programs, waste-to-energy solutions, or redesigning products and processes to minimize waste generation.
Moreover, engaging employees and stakeholders in waste reduction initiatives can foster a culture of sustainability within the company.
Incentives for ideas that reduce waste or increase recycling can also drive innovation.
Water Conservation
Water is another vital resource for manufacturing.
Reducing water consumption not only benefits the environment but also reduces operational costs.
To achieve this, factories can implement water-saving devices, upgrade to more efficient fixtures, and monitor water usage closely.
Recycling water within the production process can also lead to significant conservation.
For instance, water used for cooling or cleaning can often be treated and reused instead of being discarded.
Training staff on efficient water use and establishing regular maintenance schedules can prevent leaks or extravagant use of water.
Sustainable Sourcing
Sustainable sourcing of materials is essential for reducing environmental impact.
Factories should prioritize materials that are renewable, recyclable, or have a lower environmental footprint.
Sourcing from suppliers who adhere to sustainable practices can also ensure that the supply chain supports environmental goals.
By evaluating the life cycle of products, manufacturers can make informed decisions about materials that offer the least environmental impact.
Collaborating with suppliers for transparency in their processes can lead to more sustainable choices and foster long-lasting partnerships.
Adopting Environmental Impact Reduction Technologies
Embracing cutting-edge technologies can make a significant difference in achieving sustainable factory operations.
Environmental impact reduction technologies provide innovative solutions targeting specific sustainability challenges.
Smart manufacturing technologies, such as the Internet of Things (IoT), can monitor factory processes in real-time, offering insights into energy, water, and material usage.
This level of detail ensures quick identification of inefficiencies and the possibility to make real-time adjustments.
Advanced analytics, powered by machine learning, can help predict maintenance needs, thus reducing unplanned downtime and unnecessary resource use.
Automated systems can streamline operations, reducing waste and improving product quality.
Renewable energy technologies, such as solar panels and wind turbines, can offset factory energy demands.
Battery storage solutions allow for storing excess energy, providing power even when natural conditions aren’t ideal.
Biodegradable materials and eco-friendly chemical substitutes can replace more harmful substances.
These technologies not only reduce waste but also produce safer products that align with consumer demands for sustainable options.
Building a Sustainable Future
As factories transition towards sustainability, it’s essential to understand that these changes don’t happen overnight.
Developing a detailed sustainability strategy, setting achievable goals, and keeping a keen eye on performance metrics are key steps.
Investing in research and development to pilot new technologies and methods can bolster sustainability efforts.
Educational programs can also enhance employees’ understanding and engagement with sustainable practices.
Collaboration across industries and with governmental bodies can foster innovation and turn challenges into opportunities for growth.
Sharing knowledge and successes can inspire other manufacturers, promoting industry-wide sustainability.
Conclusion
By implementing best practices and embracing environmental impact reduction technologies, factories can work towards sustainable operations that benefit both the environment and their bottom line.
The journey towards sustainability is ongoing, requiring continuous efforts, innovation, and commitment.
Ultimately, these practices not only ensure compliance with regulations but also meet consumer demands, paving the way for a resilient, sustainable future in manufacturing.
資料ダウンロード
QCD調達購買管理クラウド「newji」は、調達購買部門で必要なQCD管理全てを備えた、現場特化型兼クラウド型の今世紀最高の購買管理システムとなります。
ユーザー登録
調達購買業務の効率化だけでなく、システムを導入することで、コスト削減や製品・資材のステータス可視化のほか、属人化していた購買情報の共有化による内部不正防止や統制にも役立ちます。
NEWJI DX
製造業に特化したデジタルトランスフォーメーション(DX)の実現を目指す請負開発型のコンサルティングサービスです。AI、iPaaS、および先端の技術を駆使して、製造プロセスの効率化、業務効率化、チームワーク強化、コスト削減、品質向上を実現します。このサービスは、製造業の課題を深く理解し、それに対する最適なデジタルソリューションを提供することで、企業が持続的な成長とイノベーションを達成できるようサポートします。
オンライン講座
製造業、主に購買・調達部門にお勤めの方々に向けた情報を配信しております。
新任の方やベテランの方、管理職を対象とした幅広いコンテンツをご用意しております。
お問い合わせ
コストダウンが利益に直結する術だと理解していても、なかなか前に進めることができない状況。そんな時は、newjiのコストダウン自動化機能で大きく利益貢献しよう!
(Β版非公開)