- お役立ち記事
- For new employees in the quality assurance department! QMS (Quality Management System) Basics and Introduction Guide
For new employees in the quality assurance department! QMS (Quality Management System) Basics and Introduction Guide
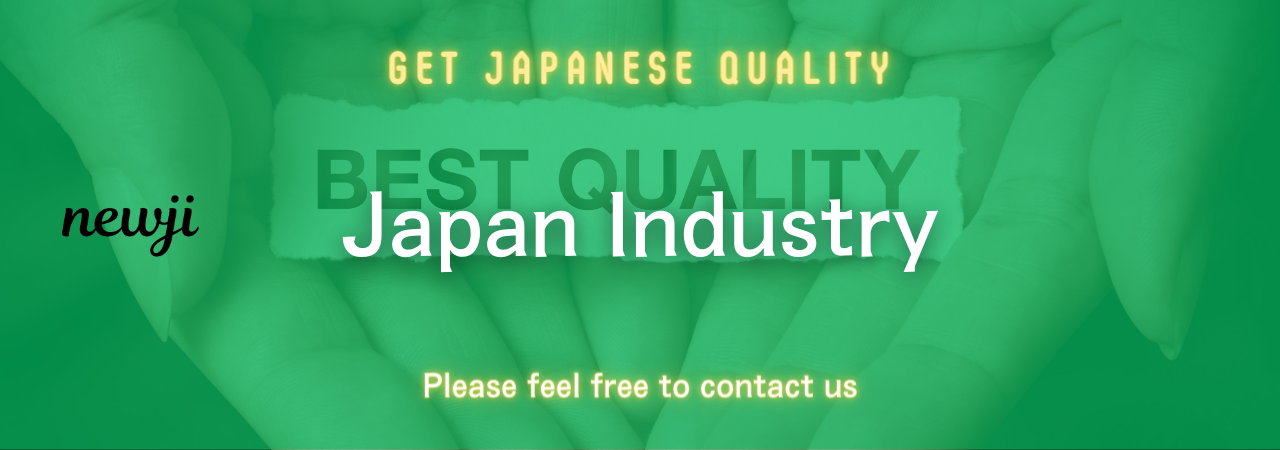
目次
Understanding the Basics of Quality Management Systems (QMS)
When you join the quality assurance department as a new employee, one of the most important things you’ll need to understand is the Quality Management System, or QMS for short.
A QMS is a formalized system that documents processes, procedures, and responsibilities for achieving quality policies and objectives.
Essentially, it helps an organization direct and control the quality aspects of its operations.
QMS is crucial for delivering consistent product or service quality, meeting regulatory requirements, and fostering customer satisfaction.
Not only does a QMS help identify areas for improvement, but it also ensures that all team members understand their roles in maintaining quality standards.
Key Components of a Quality Management System
There are several key components that make up an effective QMS.
Understanding these components will help you grasp the full scope of your responsibilities in quality assurance.
1. **Quality Policy and Objectives**: These set the direction for the company’s efforts to meet quality standards.
A quality policy outlines the commitment to quality, while quality objectives provide measurable goals.
2. **Documented Information**: This includes all documented procedures, records, and instructions that guide quality management processes.
Proper documentation ensures consistency and provides a reference for continuous improvement.
3. **Process Management**: QMS relies heavily on clearly defined and managed processes.
Process management ensures that activities are planned and controlled in alignment with quality objectives.
4. **Resource Management**: An effective QMS requires the allocation of adequate resources, including human resources, infrastructure, and work environment, to achieve quality objectives.
5. **Measurement and Analysis**: Monitoring, measuring, and analyzing various aspects of the QMS are essential for identifying areas for improvement and ensuring conformance to quality standards.
6. **Improvement**: A strong focus on continual improvement ensures that the QMS evolves and adapts to changes in the business environment.
The Role of Standards in QMS
International standards, such as ISO 9001, play a significant role in the development and implementation of QMS.
These standards provide a framework for companies to design a QMS that meets globally recognized quality requirements.
Adhering to these standards helps organizations improve efficiency, reduce waste, and enhance customer satisfaction.
For a newly appointed quality assurance employee, understanding these standards will provide key insights into how your organization aligns its processes with regulatory and industry expectations.
Steps to Implementing a Quality Management System
If your organization is in the process of developing or revamping its QMS, here are some essential steps to consider:
1. Define Key Processes
Start by identifying and defining the core processes critical to maintaining quality.
This may include production, design, customer service, and procurement processes.
Clearly outline the objectives, inputs, outputs, and interactions of each process.
2. Develop Documentation
Create documentation detailing procedures, work instructions, and quality policies.
Ensure that all documentation is accessible, easily understandable, and regularly updated to reflect process changes.
3. Assign Responsibilities
Define roles and responsibilities for all team members involved in quality management.
Ensure everyone understands their contribution to the company’s quality objectives.
4. Train Employees
Provide comprehensive training on the QMS framework, including the use of tools, techniques, and documentation processes.
Training ensures that employees are well-equipped to fulfill their roles and continuously uphold quality standards.
5. Monitor Performance
Regularly monitor and measure the effectiveness of the QMS using established metrics and audits.
Performance evaluation helps identify areas for improvement and reinforces commitment to quality.
6. Foster Continuous Improvement
Encourage a culture of continuous improvement by promoting open feedback and innovation.
Implement corrective actions when needed and celebrate achievements in quality outcomes.
Challenges and Tips for Success in QMS
Implementing and managing a QMS can be challenging, especially for new employees.
However, with the right approach, these hurdles can be overcome, leading to successful quality outcomes.
Here are some common challenges and tips for overcoming them:
Resistance to Change
Teams may resist changes in processes introduced by QMS.
To mitigate this, clearly communicate the benefits of QMS and involve employees in the development process.
Lack of Engagement
Involving team members at every stage of the QMS implementation fosters engagement and ownership.
Regularly seek input from staff and address their concerns to maintain involvement.
Data Management
Handling large volumes of quality-related data can be cumbersome.
Use centralized digital databases and automation tools to streamline data management tasks.
Maintaining Consistency
Consistent application of QMS principles is key.
Facilitate regular training and update sessions to keep employees informed about changes and best practices.
Conclusion: Your Role in the Quality Assurance Journey
As a new member of the quality assurance department, understanding the principles and components of a quality management system will empower you to contribute effectively to your organization’s quality goals.
Your role is pivotal in ensuring that quality processes are not only implemented but also continuously improved upon.
By embracing the QMS framework and taking proactive steps to foster quality, you are setting your organization up for sustained success and customer satisfaction in the long run.
資料ダウンロード
QCD調達購買管理クラウド「newji」は、調達購買部門で必要なQCD管理全てを備えた、現場特化型兼クラウド型の今世紀最高の購買管理システムとなります。
ユーザー登録
調達購買業務の効率化だけでなく、システムを導入することで、コスト削減や製品・資材のステータス可視化のほか、属人化していた購買情報の共有化による内部不正防止や統制にも役立ちます。
NEWJI DX
製造業に特化したデジタルトランスフォーメーション(DX)の実現を目指す請負開発型のコンサルティングサービスです。AI、iPaaS、および先端の技術を駆使して、製造プロセスの効率化、業務効率化、チームワーク強化、コスト削減、品質向上を実現します。このサービスは、製造業の課題を深く理解し、それに対する最適なデジタルソリューションを提供することで、企業が持続的な成長とイノベーションを達成できるようサポートします。
オンライン講座
製造業、主に購買・調達部門にお勤めの方々に向けた情報を配信しております。
新任の方やベテランの方、管理職を対象とした幅広いコンテンツをご用意しております。
お問い合わせ
コストダウンが利益に直結する術だと理解していても、なかなか前に進めることができない状況。そんな時は、newjiのコストダウン自動化機能で大きく利益貢献しよう!
(Β版非公開)