- お役立ち記事
- Basics and success stories of the Toyota Production System that new employees in the production technology department should know
Basics and success stories of the Toyota Production System that new employees in the production technology department should know
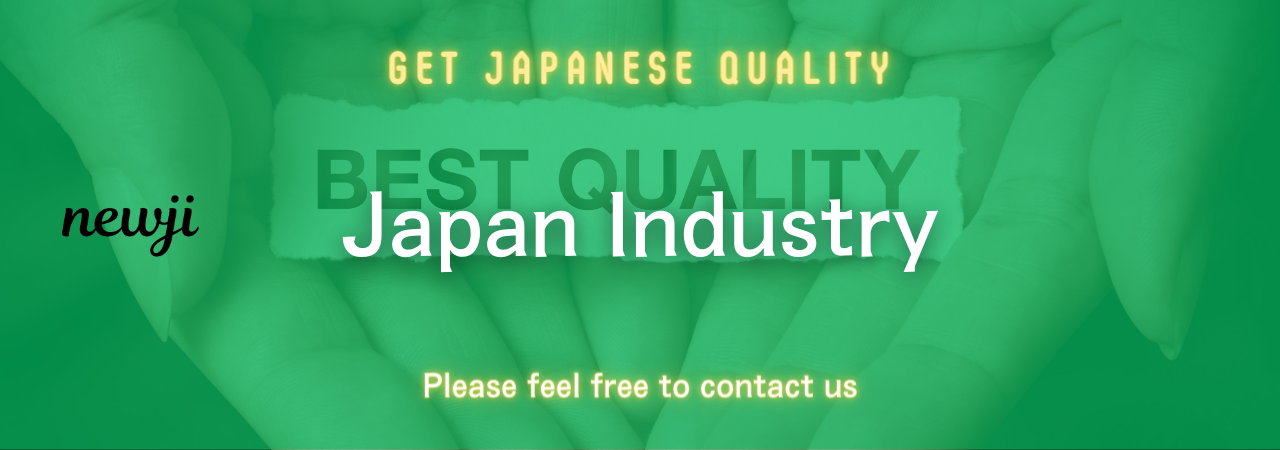
目次
Introduction to the Toyota Production System (TPS)
The Toyota Production System, commonly referred to as TPS, is a manufacturing methodology developed by Toyota that focuses on maximizing efficiency and eliminating waste.
This system has revolutionized the manufacturing industry, setting benchmarks for lean manufacturing across the globe.
For new employees in the production technology department, understanding TPS is crucial as it not only enhances production efficiency but also contributes to overall company success.
Understanding the Core Principles of TPS
TPS is built on two main pillars: Just-In-Time (JIT) and Jidoka.
Together, these principles form a framework for reducing waste and improving product quality.
Just-In-Time (JIT)
JIT is a strategy that aims to improve a business’s return on investment by reducing in-process inventory and associated carrying costs.
Within this system, materials are delivered and products are manufactured at the time they are needed, minimizing excess inventory.
This helps in reducing costs and increasing efficiency.
JIT requires precise coordination and communication along all points of the supply chain, which can be achieved through continuous improvement and employee empowerment.
Jidoka
The principle of Jidoka, often translated as “automation with a human touch,” emphasizes quality at every stage.
In the TPS, this means that when an abnormality is detected in a process, that process stops immediately to prevent defective products from moving down the line.
This immediate attention to issues helps in maintaining high-quality standards and prevents larger problems later in the production process.
The Role of Kaizen in TPS
‘Kaizen’, meaning “continuous improvement,” is an integral part of TPS.
It encourages every employee, from management to the factory floor, to suggest and implement incremental changes regularly to improve productivity, streamline processes, and enhance quality.
Kaizen fosters a culture where workers at all levels are invested in the organization’s success and are empowered to seek out improvements in their daily tasks.
The Tools and Techniques of Kaizen
Several methodologies support Kaizen, including the 5S system, PDCA cycles, and value stream mapping.
These tools help identify waste, bring order to the workplace, and streamline operations.
By systematically applying these techniques, organizations can continuously drive process improvements and uphold the values of TPS.
Success Stories: The Impact of TPS on Global Manufacturing
Numerous success stories around the world showcase the effectiveness of the Toyota Production System.
By implementing TPS, many companies have achieved remarkable improvements in productivity and efficiency.
Here are a few notable examples:
Toyota Motor Corporation
Toyota itself is the best example, demonstrating how the TPS principle turned it into the leading automobile manufacturer.
By reducing production times and efficiently utilizing resources, Toyota remained agile in a competitive market, maintaining a high level of product quality.
A Nestlé Facility
Nestlé, the global food and beverage leader, applied TPS principles to its manufacturing processes.
By focusing on productivity improvements, Nestlé reduced factory waste significantly and saw a substantial increase in production efficiency.
The company harnessed the potential of its workforce by empowering them to identify inefficiencies, leading to long-term cost savings.
Kaiser Permanente
Even outside traditional manufacturing, industries have seen success with TPS.
Kaiser Permanente, a leading healthcare provider, applied TPS principles to streamline its operations, reducing patient wait times and enhancing service quality.
This example highlights the adaptability of TPS across various sectors, emphasizing its role in improving processes and outcomes.
Implementing TPS: Challenges and Considerations
While TPS offers numerous benefits, implementing it can pose challenges.
Organizations may face resistance to change from employees accustomed to traditional methods, or struggle with the initial cost of restructuring existing systems.
Moreover, TPS requires ongoing commitment to training, as all employees should continuously develop skills and knowledge about lean manufacturing principles.
Overcoming Challenges
To successfully implement TPS, companies should focus on change management strategies.
This involves educating employees on the benefits of TPS and actively engaging them in the transformation process.
Providing regular training sessions ensures that staff are equipped with the necessary knowledge and skills, fostering an environment of openness and adaptability.
Conclusion
Understanding and adopting the Toyota Production System can significantly transform production technology departments.
By streamlining processes, reducing waste, and investing in employee engagement and empowerment, organizations can achieve improved efficiency and higher quality outcomes.
Success stories from around the world showcase TPS’s adaptability across different industries, reflecting its relevance beyond automobile manufacturing alone.
For new employees entering the production technology field, embracing these principles could pave the way for a successful career in a rapidly evolving industry.
By consistently practicing continuous improvement and upholding the values central to the Toyota Production System, firms can ensure long-term sustainability and competitive advantage.
資料ダウンロード
QCD調達購買管理クラウド「newji」は、調達購買部門で必要なQCD管理全てを備えた、現場特化型兼クラウド型の今世紀最高の購買管理システムとなります。
ユーザー登録
調達購買業務の効率化だけでなく、システムを導入することで、コスト削減や製品・資材のステータス可視化のほか、属人化していた購買情報の共有化による内部不正防止や統制にも役立ちます。
NEWJI DX
製造業に特化したデジタルトランスフォーメーション(DX)の実現を目指す請負開発型のコンサルティングサービスです。AI、iPaaS、および先端の技術を駆使して、製造プロセスの効率化、業務効率化、チームワーク強化、コスト削減、品質向上を実現します。このサービスは、製造業の課題を深く理解し、それに対する最適なデジタルソリューションを提供することで、企業が持続的な成長とイノベーションを達成できるようサポートします。
オンライン講座
製造業、主に購買・調達部門にお勤めの方々に向けた情報を配信しております。
新任の方やベテランの方、管理職を対象とした幅広いコンテンツをご用意しております。
お問い合わせ
コストダウンが利益に直結する術だと理解していても、なかなか前に進めることができない状況。そんな時は、newjiのコストダウン自動化機能で大きく利益貢献しよう!
(Β版非公開)